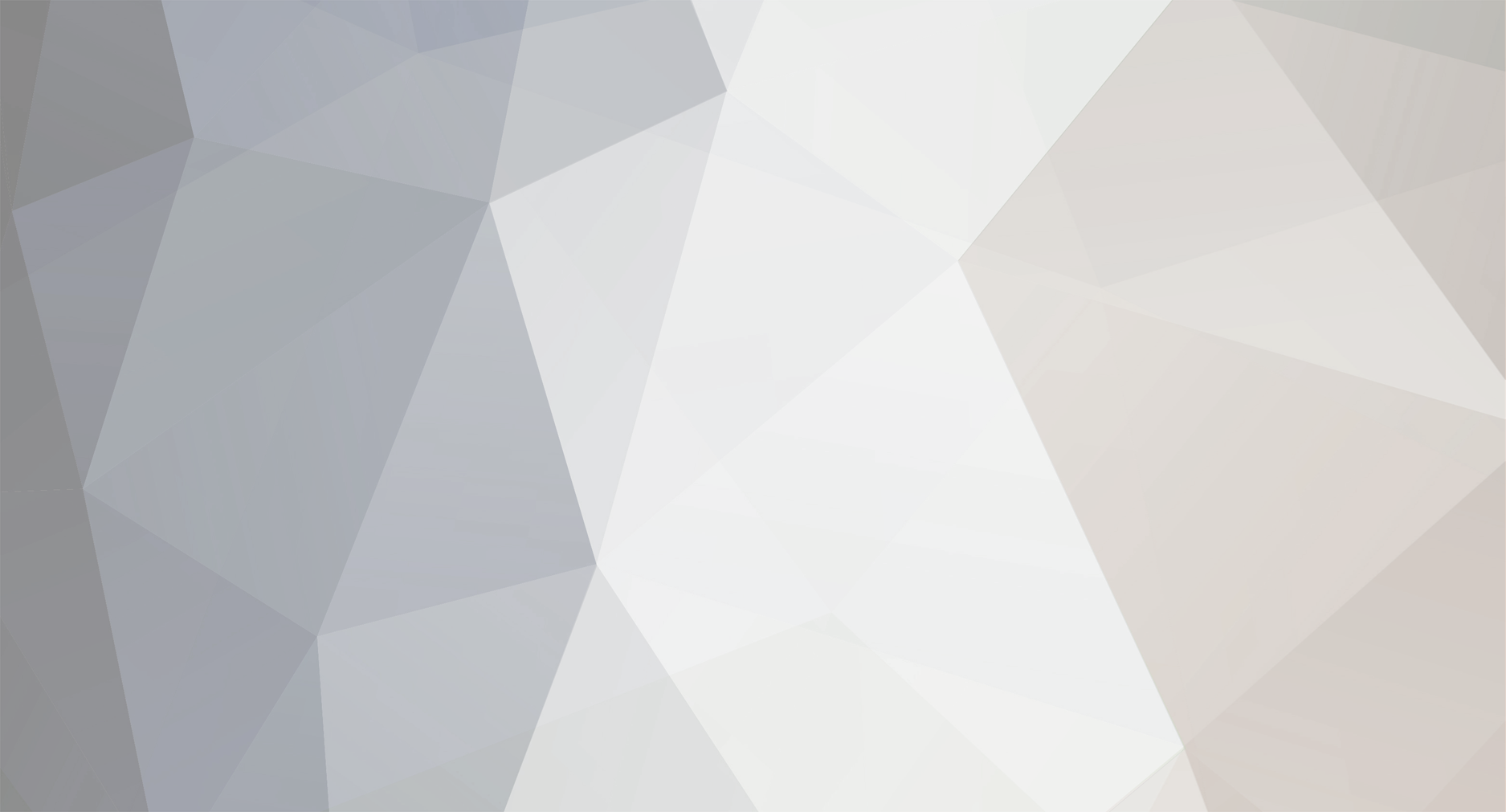
WizardBlack
Donating Members-
Posts
1444 -
Joined
-
Last visited
-
Days Won
2
Content Type
Profiles
Forums
Blogs
Events
Gallery
Downloads
Store
Everything posted by WizardBlack
-
how do you know what year skyline rb motor do you have?
WizardBlack replied to cinpatico's topic in Nissan RB Forum
Use the search button, dude. In before the lock. How did you buy a powerplant as expensive as an RB without even knowing the year differences? -
ORLY? Hmmmm. Do you know what model it was, etc? I was going to buy the solid mount from AZC, but they were out. I suspected I might have to do the same to get everything to line up, but I guess I did not.
-
Just as a quick reply (on my way to work), I figured I would detail a few things with the new McKinney trans mount for 280Z's. First on the structure of it; there's a few tweaks I would recommend to McKinney, but I believe I have a prototype, so I am sure that will get worked out. Otherwise, it fit as well as any might be expected. The 280Z's just don't permit an easy solution. On fitment. All along I was concerned about pinion angle being correct (which most people check), but pinion offset angle is also very critical. This angle is measured from the centerline of the trans output to the direct line towards the differential flange center. Your pinion may be perfect, but if the differential is vertically offset from the trans a lot, this will cause a problem. Anyways, I took RIPS' statement of 10 degrees engine deck slant (thank you!) with the statement and photos of spacers for the McKinney mounts (thanks gmac708!) and standard limits for the two angles (from an SAE tech buddy of mine) and set it in the car. I came up with 3 degree pinion angle (which is what is recommended) and 0.68 degrees pinion offset angle (with 7 degrees being the limit). As you apply power, the nose of the differential will rise with the resistance to torque and cause the pinion angle to lessen and the pinion offset angle to zero or perhaps go negative. I think I have right at 10.25 degrees deck slant using stuff I had lying around for spacers. I believe this mount provides a great solution to get the proper geometry for the RB engine in a 280Z. I also measured the length for the propshaft using my 280Z propshaft's rear u-joint centerline and the RB's front u-joint centerline. I came up with 21.0" length between the centerline of the two u-joints bearings; while providing about 3/8"~1/2" of slack in the trans output to avoid bottoming out. I also noticed that I will need to notch both holes in the engine subframe a tad to get the mounts to drop straight on and have the engine mount bolts not angled to hit the hole. (I am using the poly mounts)
-
??? This is a swap forum. I am not sure how you can say they 'butchered' a chassis to put a hi-po turbo setup with good power/weight and reliability into an empty shell. 4G63 DSM engines had crankwalk issues due to poor maintenance combined with oil squirter design and sitting on the clutch all the time. I can't really say anything about 3S as it was not one of my specialties, but I know my main tech had one and never got very far with it. I don't know why they don't seem to take well to a basic rebuild.
-
I put on my Lonewolf intake, and 90mm TB
WizardBlack replied to big-phil's topic in Turbo / Supercharger
QFT. I thought we already had stated we thought the WG must be functional since it worked without a BC on it. I'd try a manual controller before you go to all that trouble, if I were you. -
Gotcha. Of course you also know that the L motor slants to the other side, compared to the RB, too. So neither one really helps on that front. :-/ When I get my new mounts in, I will drop it in, tweak the exhaust mount up to 10 degrees slant (with none on the other side) and see what pinion is like and post it up. Then I will know what I gotta do to get offset/pinion decent. I still fear I will need a front diff mount to tweak/shim everything the way it should be.
-
I put on my Lonewolf intake, and 90mm TB
WizardBlack replied to big-phil's topic in Turbo / Supercharger
Yup, that's what I mean. If you had a JUN style manifold like 1 or 2, it is not as important. With the style posted here, you'd have a choice between 3 and 4. Note that the VH45DE also has a throttle flange pretty close to the plenum, so they do that as well. Of course, the entire intake tract is fat on that thing. Then again, as BRAAP and a few others mentioned, there are lots of things on the engine you are bolting the stupid thing to that will toss all your calcs out the door. -
Well, who is we? You have no signature.
-
Well, the whole intake manifold thing and valve placement thing threw us off. What you are referring to has been done by Colt cams. Take a look at 'em.
-
Well, bugger, I did not check that when the factory system was in the car. That presumes that the new powertrain has the same effective propshaft length. If it's shorter, which the RB seems to be by maybe 4" or so, the pinion angle has to be smaller, as I understand it.
-
I think Adam's biggest point is more the staggered valve placement than dual cross-flow. What do you guys think of that situation? I bet 5 valve head design might offer a little bit of insight into what kind of nature a staggered 4 would have.
-
I thought that of fellow students who had not even collected a paycheck yet when I was an ME major. So that's scratched, then.
-
If you are breaking bits, you are using too much pressure or stepping the bit sizes too fast. Most likely the second one. For a high tolerance hole, I usually go fast and very very light pressure. Use some WD40 on that puppy.
-
Where are you located? "101, Broadway" doesn't tell the whole tale. EDIT: NVM, it's Chennai, India. You may want to change your contact info on your website. People outside of India surf the web, too.
-
Honestly, I think to get an appropriate pinion and offset, you'd need to tweak the diff a bit. If you get the offset decent, either the front of the engine is too high or the pinion is not right. I don't have my trans mount just yet, though, so I am just messing about with jacks and shims. AFAIK, the bottom of the oilpan is flat with the road; even though it is angled when looking at it compared to it's mounting flange. The deck of the engine is slanted when installed, yes. According to RIPS, 10 degrees. With the McKinney engine mounts, it sits at 13 with no adjustment shims. You definitely don't set it flat. Dizzle, you need an inclinometer to determine what you actually have. It sounds like your pinion angle is wrong. That is the difference in inclination between the output of the trans (which can be measured by the face of the block when you have the water pump and whatnot off of it) and the input flange of the differential. As I understand, at or around 2.5 degrees difference is good. Some cars can get away with more, but I suspect the relatively short propshaft leaves us with a tighter tolerance. What I notice is that the diff is angled up a hair (at least how I have the chassis sitting) and as I jack the rear of the trans up so the trans output and diff input are at the same level (reducing the offset or elevation difference), the engine/trans noses down and I lose too much angle compared to the diff. (If this makes sense) I can get the angle back by shimming the engine mounts up more, but that's a slow process and I suspect I would end up getting it too high; perhaps hitting the valve covers on the hood, etc. Anyone that installed an RB in an S30 actually measure their pinion?
-
Have you guys seen Colt Cams' staggered lobe profiles for the 'swirl effect'? Swirl effect for fuel mixture is nice with DI. Why not figure a way to use direct air injection as well? Operate a compressor off of the relatively underutilized alternator electrical supply and inject air as well as fuel. Skip the inlet plumbing altogether. You'd want a high flow, low pressure compressor.
-
(Misfire) Before and after side gapping the plugs - VIDEOS
WizardBlack replied to cygnusx1's topic in Ignition and Electrical
Bigger gap. -
I saw this on TV years ago. It works. They demo'd a little 4 banger sounding like an F1 car. Hondaaazzzz rejoice!
-
Holset reliability? Yeah, I guess some of them fail after only 100,000 miles at 25 psi. Psht. Pieces of junk! How do they fail? The HX35 or HX35/40 would suit your needs. Rebuild kits cost a massive $60 and you can do it yourself. I have been told these modern versions (versus H1C, etc perhaps?) feature the turbine wheel (and integrated shaft) balanced separately from the compressor wheel (which is also individually balanced) so you don't even have to worry about indexing things during the rebuild. Those other turbos, although Holsets cost about the same new as the Garretts, cannot be rebuilt but by a few shops. Big bucks.
-
Sure, DIY parts made in China. If you have the fab skills, a few extra grand will get you proper turbos and you can fab it just the same. A couple of HX40's would actually make a decent economical TT setup.
-
RIPS RB30 FED 2nd in Northern Nationals and claims NZ record
WizardBlack replied to RIPSNZ's topic in Nissan RB Forum
LOL, that's ridiculous. Keep up the great work and be safe! Mark -
I have a shaved manifold listed further back. Still on my shelf. Just been too busy to keep it bumped. Take a peek if interested.
-
I put on my Lonewolf intake, and 90mm TB
WizardBlack replied to big-phil's topic in Turbo / Supercharger
I'm still on the air velocity thing. The air has to be slow enough as it enters the plenum (and of the right direction) to easily make the turn to cylinder 1. This is done by design of the plenum size, runner size/taper/design, intended engine performance (rpm, displacement, rod/stroke, valves, cam timing/lift), intercooler piping size and direction, etc.). It also has to evenly distribute to all 6 as well. The only way to know for sure is to do a fluid analysis on the whole shebang. The more air you are flowing through a throttle, the higher it's velocity will be. This is going to change how it distributes to the cylinders. Keeping the velocity down when massively raising power levels (for the given engine parameters; including plenum) should help keep it more even, but it's not a perfect solution. The whole point of it is to keep flow even. When it isn't, your A/F ratio is varied amongst cylinders. Some will be hotter than others. Some will be too rich while others are close to detonation. It basically makes your engine demonstrate a lower output before being limited by detonation or heat, etc. There are very few manifolds that are going to be perfect. That's why high end standalones allow for cylinder-to-cylinder fuel correction. I guarantee you that any top level racing engine has already had it's flow balance tested and adjusted for (note that I didn't say corrected). Likewise with high end sports car engines. They do as much design as they can and then they tune for what's left. I know, Tony, that you are stuck like a dog with a bone on that puppy ( and just to be clear, I mean that in a friendly tone ) and that's fine. No one has fluid flow analysis to answer you and you know they don't, so you won't get the level of tech data you want to be satisfied, methinks. The bottom line, IMHO, is that it is better to be too big than too small and aggravate the balance issues. I have personally owned a car (Evo 8) with a massive throttle on an even smaller engine. The throttle spring was so soft you could practically breathe on it and it would open. Add to that an HKS twin plate that left the clutch pedal feeling like a normal throttle pedal does. It took a bit to adjust to, but was not an issue after adapting. Who ever said big turbo cars had linear throttle response anyways? I base my power control off of boost pressure and sound (which is the same thing, really). Big turbos have too much transient response at low rpm and throttle levels to do otherwise. To directly answer Phil (after first apologizing for co-hijacking the thread), you would need per-cylinder EGT readouts or somehow gaining cylinder pressure numbers or A/F ratio numbers on a real world car. I've seen per-cylinder EGT readout on some street cars before. The next best thing would be to do dyno testing with one EGT gauge and doing back to back pulls with the probe in each runner, but everything else has to be amazingly equal. You'd be best off with a Dynapack style dyno to do that. I used to own a 4WD dynapack and it was precise enough that it could demonstrate repeatable power differences with A/C on vs. off. -
I put on my Lonewolf intake, and 90mm TB
WizardBlack replied to big-phil's topic in Turbo / Supercharger
Maybe so, maybe not. Perhaps they looked back at another car that used a 60mm throttle, etc. and thought the same thing. I cannot give you a direct before/after comparison and I don't think digging out a fluid dynamics book would be useful; just that it's done all the time as a part of a collection of modifications. Personally, the WOT thing is what convinces me. I look at the car on boost and consider the air flowing through the system like a liquid. You want a nice smooth flow and even tapers in diameter from the compressor outward. WRC cars make a lot with a restrictor, but they'd probably make a lot more without it, obviously. Otherwise, the rules would not dictate one. Ultimately, if you're stuck on that one car, that's fine. I'd say there are plenty more cars making big power with one. So anyways, any updates? -
I put on my Lonewolf intake, and 90mm TB
WizardBlack replied to big-phil's topic in Turbo / Supercharger
The ~280 hp VH45DE uses a big throttle. It is a heavily engineered engine with little in the way of "let's just throw it in there" mentality and virtually no bling stuff since it's in a big boat of a car, but they selected a good sized throttle, so there must be something to matching up the throttle to plenum size. If you used something smaller, it would have an even smaller cross section to expand out from as soon as it passed the TB and entered the plenum. Likewise, having a smaller TB would raise velocity; making it even harder for air to make the turns necessary to even flow to all cylinders. I suspect for ideal delivery, you'd want air to enter the plenum at a pretty slow velocity. Gaining more and more power puts the inlet air velocity higher than the plenum is probably designed for. Look at big shot intake manifolds on 2JZ's and RB's. They're typically made for big throttles and they have angle TB flanges and tapered plenums to even things out. Why 3"? Well, cause I can, for one. Cause I continually build more power and don't want to have to redo it, for two. 2.5" may get the job done, but 3" might make a little less restriction; even at a measly 400~500 whp. It is indeed diminishing returns, but it is still returns at a moderate whp stage. Some of us aren't aiming for 'just enough', either. I personally aim for as much as I can and then I'll dial it down with the throttle. I use TPS-dependent boost targets on standalone-controlled EBC's, too; which is nice.