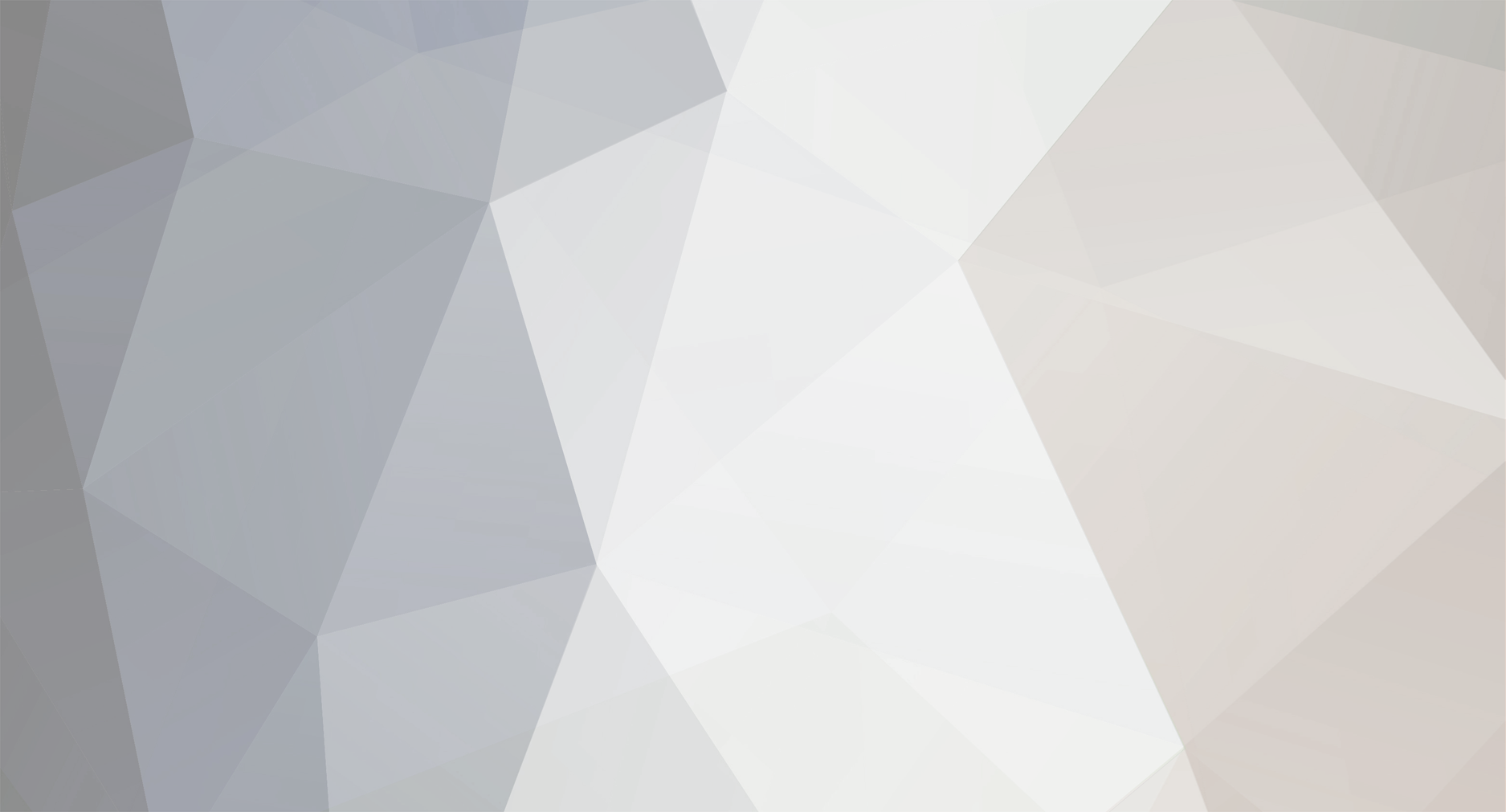
tube80z
Super Moderators-
Posts
1399 -
Joined
-
Last visited
-
Days Won
30
Content Type
Profiles
Forums
Blogs
Events
Gallery
Downloads
Store
Everything posted by tube80z
-
Okay, Jon you need to send me money for the coke I just spewed on my PC Sold by JC Whiteney no less. That's so cool. Cary
-
John, you must have more patience then me. I started to look and came across this site http://www.nissanperformancemag.com/june04/240sx/ and looked at the CUSCO roll cage, starting laughing and well, gave up. I have no clue what a floor bar is or would do but I'm sorta curious. I do think the Z can stand to have some triangulation under the engine compartment and hooked it to the TC boxes. We'll see if it makes any difference as that's what I'm doing this weekend. Cary
-
a little more progress on the Z
tube80z replied to stony's topic in Brakes, Wheels, Suspension and Chassis
Stony, I think you got a good deal but that's also why you probably don't have your car running at this point. Generally any shop that does a "sponsor" type deal ends up taking a lot longer as they get other paying jobs in. I'd wait it out if you can. If it is any consolation my project has been going on for about four years so I understand the frustration. In may case I have no one to blame but me. So I envy you a little in that respect. Cary -
Billet Ali Rear Subframe
tube80z replied to BlackBeaut's topic in Brakes, Wheels, Suspension and Chassis
-
On my race car I use the lightweight diamonds. Fronts are 13x10 and rears are 13x12. The fronts are around ten pounds and the rears around 15. You wouldn't want to run these on the street as potholes would probably bend them. They are designed to fold up easily to help from bending other bits. I think these are referred to as their mini stock wheels. That said a good quality aluminum wheel will probably be stiffer for the same or less weight. Whether or not you can tell any difference will depend a lot on what your car is and how you use it. Cary
-
An answer to an old thread. I modified the stock pedal box in a manner similar to what Don does. The dual brake masters are in the engine compartment, not in the car. You need to cut out an area of the firewall to accomodate this and you need to replumb the brakes. I'll try and dig up some pictures from my archives. Cary
-
280ZX Rear Suspension - fixes??
tube80z replied to ecp48's topic in Brakes, Wheels, Suspension and Chassis
-
Crossmember modded to raise steering rack?
tube80z replied to ezzzzzzz's topic in Brakes, Wheels, Suspension and Chassis
I don't see why the motor mounts need to be reworked when cut out the center. The only problem with your plan is there isn't that much room to the oil pan. If you're going to do this it would be far easier to make the entire thing from scratch. Then you'd probably make a k-member that bolts into the TC boxes and servers to reinforce the bottom of the engine compartment, then you could lengthen the lower control arms, change the ackerman ... No, never thought about it Cary -
If you're looking to get into racing on the cheap there is no better way than buying a car that is already built. You will save 100 to 200 percent over doing it yourself. What your describing above is an EMOD car for SCCA SOLO II. It's a wide open class that's really fast. Not a good place for a beginner to start. Prepared cars are really fast, MOD cars take that to another level. I'd really recommend using your daily driver for a year to get some seat time and experience. The real trick in building a race car is to figure out what you're going to do with it and build to those rules. You won't save any money buying things over as you change your mind. There's lots of advice on this thread and many of the responses are biased to the individuals program. You need to figure out yours and go with that. For what it's worth I have what you'd call a low budget autox car. I bought it wrecked for the parts for my EMOD project and ending up fixing it. The plan was to get seat time in the slow version before getting really crazy. That said I should tell you that my initial purchase of $2500 has grown into about $8000 mostly in suspension, brakes, wheels. The car routinely sets TTOD but has been specialized to autox and hillclimb competition and would make a horrible track day car. Cary
-
280ZX Rear Suspension - fixes??
tube80z replied to ecp48's topic in Brakes, Wheels, Suspension and Chassis
The one I remember required you to send in your crossmember as a core. They raised the pivots and added eccentric adjusters. I seem to recall later there was a bolt-in option like you mentioned. You might try looking at dimequarterly.com for Kelvin Dietz's EP 510. I built a crossmember for the back of it that raised the pivots and changed the trailing arm angle to fix squat and lessen the rear camber and toe gains. Cary -
Bumpsteer spacers................
tube80z replied to Vintage-TechZ's topic in Brakes, Wheels, Suspension and Chassis
I had to move the outside too. It may have been because I run a lot of caster why I needed to move both. I'm trying to find my notes, argh!!! -
Bumpsteer spacers................
tube80z replied to Vintage-TechZ's topic in Brakes, Wheels, Suspension and Chassis
I have an easier solution for you (well maybe). If you're using heims on the inner ends of your control arms you can turn them to be up/down orientation instead of front/back. The bolt can come down from the top. You'll need to make the top flat and create a tab on the bottom of the crossmember to make this double shear. You get an additional bonus in that this is a lower friction way to mount the heim (also do the TC the same way). Just mind the total travel so you don't hit the bearing race. This would allow you to adjust the up and down a small amount for different RCs. I think if you move the inner pivot too muh you may need to move the inner tie-rod up or down as well. When you measure bumpsteer it will tell you what end needs to go up or down from the curve. Cary -
Bumpsteer spacers................
tube80z replied to Vintage-TechZ's topic in Brakes, Wheels, Suspension and Chassis
When I did mine I made a piece that went on the rack end (inner tie-rod removed) and then I dropped a transfer punch through a hole in this piece to mark the crossmember. Seemed to work for me but you need to make some bits. For Jon's setup it sounds like a u-bracket that you could slide shims under would be the ticket. This would allow for precise adjustement and it would be mechanically solid. I've not had much luck with the slotted adjustments I've played with in the past. And to get really carried away with this topic why not make a new crossmember that allows the inner pivot points and steering to be moved as a unit. This would let you play with RC positions and camber change without messing up bumpsteer. Then you'd need to have the TC points adjustable and you could adjust anti-dive. Cary -
best rear suspension setup for...
tube80z replied to TomsCoupe's topic in Brakes, Wheels, Suspension and Chassis
I have some friends that run a GT4/5 cars (nasport champions, many track records, etc.) They use live axles and have tried all the types of linkage you can find info about. They settled on a 4-link with panhard. They thought it was the simplest that responded the best to adjustment. My personal choice would be a 4-link with a mumford linkage. About the only thing I can offer from personal experience is that a car that must corner will not put the power down with anti-squat in any great amount. It would be far better to use springs to control the body mass then geometry in this case. The gentleman on corner-carvers is in for a rude awakening when he gets his car running with 100 percent anti-squat in the back. Cary -
Ground control camber plates
tube80z replied to gfc's topic in Brakes, Wheels, Suspension and Chassis
The car in the pictures is Dave Kipperman's. I race with Dave and the plate is reinforced underneath. He thought it looked better on top and I'd agree. His 510 is done the same way. This is a really nice car built for to show off at track days and autoxs. Dave built the car in about 6 months. There are a lot of cool features hidden on the car. It features a lot of bracing in the bottom of the engine compartment, rocker panels, etc. Cary Cary -
Jon's 2 year roll cage saga...
tube80z replied to JMortensen's topic in Brakes, Wheels, Suspension and Chassis
If you measure the car you'll find it will generally be stiffer if you spread the load out on the strut tower. It is easier to go to the tube but you can't spread the load out as much and this seems to make the structure less stiff. But then again, you have the rules to deal with. On a couple of my cars I haven't worried about the rules I welded a plate across the ribs top pf the tower and brough the down tube into this. Then the side tubes I brought into the front face of the rear tower. And then had a strut bar that was welded across the towers. I did something similar on my mod car after playing around with whether it was better to run the tubes together or spread the load out. Those simple experiements indicated that it would be better to spread the load. Hope this makes sense, Cary Cary -
Jon's 2 year roll cage saga...
tube80z replied to JMortensen's topic in Brakes, Wheels, Suspension and Chassis
Some of us are burried at work and can't find the time to play as much as we might like. Another goup are probably headed to Shasta Is this going to be weld in or bolt in? I'm guessing bolt in. Does it need to be SCCA legal? I seem to recall you could only have a max of 180 gegrees of bend in the main hoop. It may not work to put holes in the floor and drop the bar down to weld the top. In this case I think You'll need to build up a base from the rocker to the raised section in the rear floor that fits under the bar. I think the SCCA has a rule regarding how much angle the rear stays can have from the car centerline. I don't have a rulebook handy to say for sure. So I would check that. If they don't I think you're fine connecting to the crossbar you have welded in the back. There are a host of solutions from here. I think you'll need a diagonal from the drivers side top of hoop down to the lower passenger side at minum. To make is stiffer you can put in a upper and lower X to the opposing struts. I'd also look at attaching to the roof section if this is weld in. This not only makes the structure stiffer but will help to keep the car together in a side impace. The lower X requires some creativity to get around the seat depending on how far back yours is. If you intend a bolt in solution that I have another idea for you. Sorry, work calls -- Cary -
Billet Ali Rear Subframe
tube80z replied to BlackBeaut's topic in Brakes, Wheels, Suspension and Chassis
A local shop used to think 0.25 inch plate was the end all solution for everything. Somewhere I have a set of lower control arms with two quarter inch thick tabs for the sway bar mount. Never mind the arm is no where near that thick. They built a lot of dirt cars. Cary -
Billet Ali Rear Subframe
tube80z replied to BlackBeaut's topic in Brakes, Wheels, Suspension and Chassis
-
Subframe installation idea
tube80z replied to 78zlt1's topic in Brakes, Wheels, Suspension and Chassis
I don't know if this will help or not. But when you make a tubeframe you don't preload it. I think a lot of the issue with subframe connectors is when you have the car up on a lift to install them. In that case the chassis may have some loading that isn't the same as if it were supported by the wheels. So if you just have a bare chassis I think you're fine. That's generally been how I've done this in the past. Cary -
Quick questions about bleeding the brakes...
tube80z replied to a topic in Brakes, Wheels, Suspension and Chassis
-
Billet Ali Rear Subframe
tube80z replied to BlackBeaut's topic in Brakes, Wheels, Suspension and Chassis
-
I need springs what can you reccomend for rate?
tube80z replied to cyrus's topic in Brakes, Wheels, Suspension and Chassis
Looking at the photo you can definitely see a lot of extension on the inside, which is pretty common. If you limit this you'll find that the car won't roll out of its geometry window as easily. I currently use 0 mm rebound on the front and 15 mm in the rear. If you run on rough courses you may need a little more but generally not more than 5 mm front and 25 mm rear. You don't really need a lot of rebound. What you'll find is the car rolls less, turns in quicker, and puts the power down better. When I started doing this I started getting comments about how flat my car cornered. I found it was generally about 0.15 seconds faster on my standard referrence course. I also found the car more consistent and easier to drive. Easy to do with cables and turnbuckles. Worst case you throw it all away and call it a waste of time. This is a common setup crutch that's not too well documented. Cary -