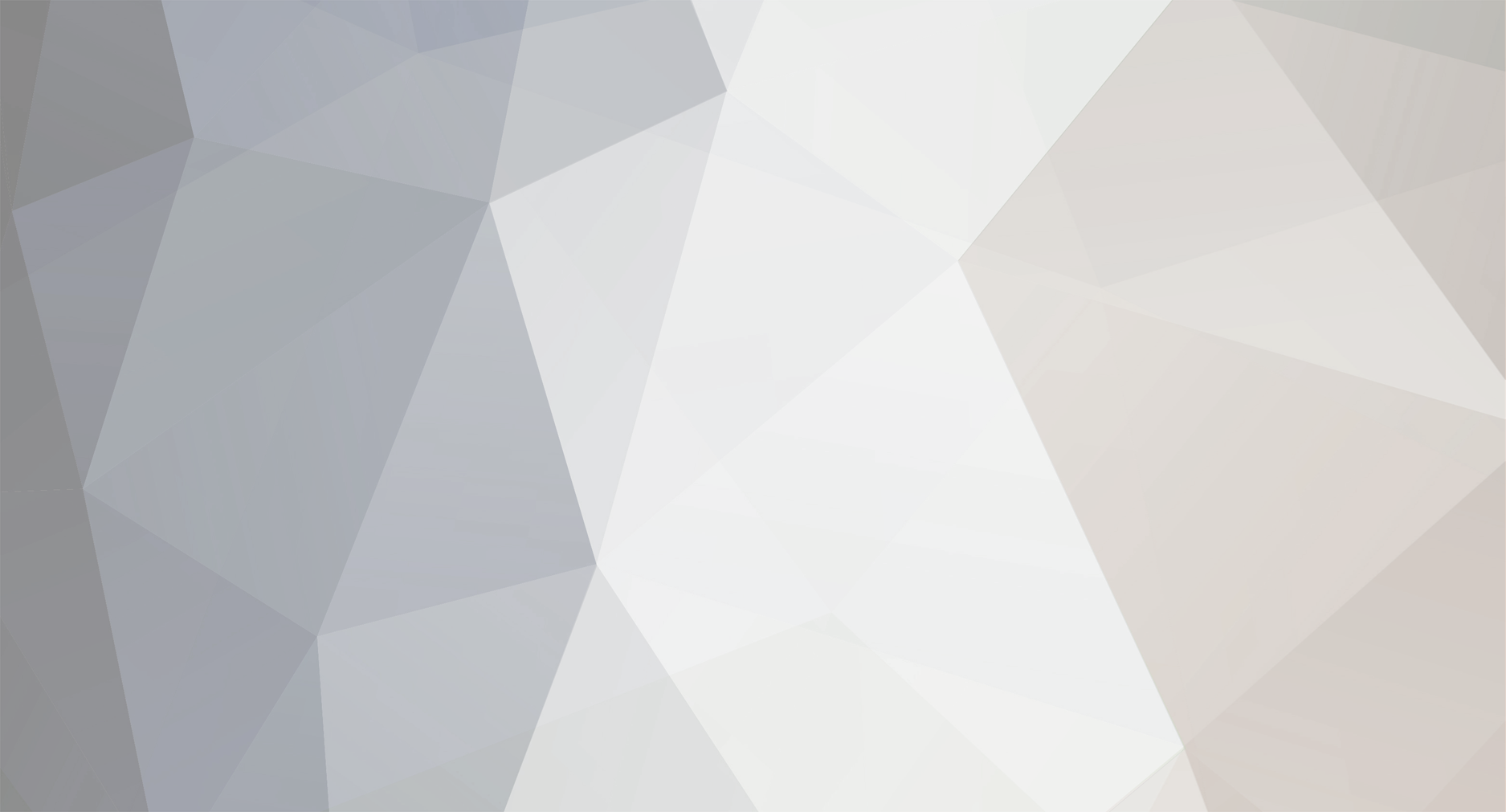
AydinZ71
Members-
Posts
1073 -
Joined
-
Last visited
-
Days Won
27
Content Type
Profiles
Forums
Blogs
Events
Gallery
Downloads
Store
Everything posted by AydinZ71
-
240z SCCA vintage race car, restoration
AydinZ71 replied to AydinZ71's topic in S30 Series - 240z, 260z, 280z
Thank you Cary! I must have been channeling your thoughts or something because I finally gave-in and added the critical “inward” facing brace. This late in the game, I am hyper critical about adding weight, but I weighed the 18-gauge 1” tube I am using, and all-in it will only be 3lbs added (including the cabin attachment to and from the firewall/roll-bar. I already used a stiffening tube on the drivers side to keep the reinforced pedal assembly from flexing. Greg said he pushes so hard (tilton assembly, no booster) he can feel the firewall flex, so I thought I’d get ahead of it. therefore, only passenger side needed the extra attachment in the cab (hence 3 vs 4lbs) the great news on the strut bar is I can add it anytime. I have a T3 one sitting around I bought used a while ago. Clearly, the permanent reinforcing NEEDS to get done at this stage. the camber plates are ground-control bolt-in (EP rules) and they have a HEAVY 1/2” thick mild steel plate. I have thickened the tower mounting surface with some MIG metal, since the overlapping spot welded 20-gauge isn’t doing me much favors. Also stick welded the bottom lip of the OEM tower mounting surface (thicker, my guess is 16-gauge equivalent) so the tower braces I installed have continuous steel to the thickened portion. Can’t rely on the spot welds to transmit the stress without a ton of flex. if my setup is anything like Greg’s, I will need a 2-3” bump steer/roll-center correction spacer. Do you have any pics of the “bend” you were describing? I have not sectioned my front struts yet (tears are done) and I’m a bit of a front suspension novice. attached are some updated pics. thanks again for or you input Cary! Sometimes feels like folks aren’t using the forum very much, so your comments motivate me to continue posting. -
240z SCCA vintage race car, restoration
AydinZ71 replied to AydinZ71's topic in S30 Series - 240z, 260z, 280z
accusump is mounted, along with remote actuator cable. cleaned up the inner fender (unibody). Removed about 0.75lbs which I will use for reinforcement elsewhere. added vertical strut tower reinforcement. Trying to avoid using a strut tower brace. Trying to convince myself the tower reinforcement will make it irrelevant. found an exhaust collector that works for the header tube OD. Needs to be modified for 2.75” outlet. made a rad overflow dip tube (plated copper sold for toilets) so it will “suck” overflow back into rad. Topping off the rad and draining the overflow seems silly. Greg said my 3” cold air funnel was too small. Widened it to 4” equivalent perimeter. My used accusump leaks from the air-oil side. Bummer… live and learn IMG_7250.MP4 -
I put a sheet of thick copper flush on the opposite side of the hole, then go to town with my mig. I can fill in a 1/4” hole in just a few minutes then grind flush with an angle grinder and flap wheel. Works for me, but takes some practice. The cooler helps pull the heat from the molten steel and “dams” it so it doesn’t flow through to the other side. Here are the inner fenders with all holes and OEM rack welded nuts removed.
-
Stainless steel vs plated steel vs aluminum rivnuts
AydinZ71 replied to fusion's topic in Body Kits & Paint
Let’s just say I have a lot of experience now 😂. 15 months of continuous rust repair, metalwork and welding. Im pretty comfortable with it. Have not ruined threads or seized a bolt yet. To be clear, nothing wrong with rivnuts. I just don’t use them and don’t have the tool. Being a race car and weight being a concern, I rarely use anything more than 20 gauge. Here are some pics of fabrication I have done with tack welded nuts. Ignition coil mount, oil cooler mount, and 5-pt harness bolting locations -
Stainless steel vs plated steel vs aluminum rivnuts
AydinZ71 replied to fusion's topic in Body Kits & Paint
In some cases when I can’t reach the other side I will drill an over-sized hole and weld-in the nut flush. In other cases, I will drill a through-hole and tack weld the nut right into the hole. This works for low-stress small-size nuts (M5 for example) where a flush-mount is not necessary. For example, nuts for mounting brake or electrical lines. I can’t explain why I never did rivnuts 🤷🏽♂️. -
Stainless steel vs plated steel vs aluminum rivnuts
AydinZ71 replied to fusion's topic in Body Kits & Paint
I must be dumb as f***. I’m still drilling holes and tack welding nuts on the other side 🤷🏽♂️ -
@fusion nice! Looks good. so there is an alarming trend whereby folks “freak out” over using filler. Probably because there are some hack jobs out there with 1” deep spots. I think it’s impractical to attempt a steel repair without SOME kind of filler. Sounds like you are practical guy, and we’re on the same page.
-
Have you performed any metal work yourself? That little area doesn’t look to bad. I bet you could fabricate a replacement with a sheet of 20-gauge steel, hammer+dolly, and MIG welder. It won’t be perfect, but even a replacement section from another car won’t be. You will still need a small amount of filler or glaze prior to paint. Very few people can perform a flawless steel patch in a contour without any filler of any sort (even if just primer). Try hammering out a little piece yourself in a bench and see how she looks!
-
My shop won’t charge me till the jobs done, but my guess is 2hrs to sonic test. My shops rate is around $100hr.
-
bump Any takers? I’m leaning towards a +2mmD overbore. That would leave me with .120 at the very minimum spots which are off-thrust sides of the walls. respectfully -Aydin
-
I just bought an N42 short block in decent, usable shape for $250. I’m in Los Angeles. Here it is getting sonic tested.
-
240z SCCA vintage race car, restoration
AydinZ71 replied to AydinZ71's topic in S30 Series - 240z, 260z, 280z
EDIS coil (for megajolt) is in. 3.5lb sucker, she’s a brick. Mounted low and back. Any further back and she will interfere with the accusump. IMG_7190.MOV IMG_7193.MOV -
240z SCCA vintage race car, restoration
AydinZ71 replied to AydinZ71's topic in S30 Series - 240z, 260z, 280z
-
Hi all! Got the results back on sonic testing my N42 (early L28) core. Copy-paste from my machine shop (Mountune, race engine shop here in Southern California). “So we are seeing .160" in a few places on non thrust sections of the bore. Our view is this is about the minimum thickness on a turbo engine. We would not go more than another 0.010" and .020" on an NA engine. Thrust areas are .305" to .196". “ Other than the .16 non-thrust thickness, overall I’m encouraged with the results. Keep in mind, although the machinists in the shop have experience with L-series, they don’t have experience “pushing the envelope” on these engines. They (re)build race engines for Honda, and specialize in custom made Ford Cosworth crate race engines. NA application: Based on the forums direct first-hand experience on engine wall thicknesses, what are your thoughts on overbore? It seems they are recommending no more than 0.02”R, or +1mm dia. With the wall thicknesses provided, do you feel they are being a little conservative? How far would you go? Turbo: if I chose to use the block for my upcoming turbo project, I will not be boring at all. The extra stroke will help with low-end spool and the extra displacement from boring is not worth the risk.
-
240z SCCA vintage race car, restoration
AydinZ71 replied to AydinZ71's topic in S30 Series - 240z, 260z, 280z
-
240z SCCA vintage race car, restoration
AydinZ71 replied to AydinZ71's topic in S30 Series - 240z, 260z, 280z
Thanks Clark! the link to speedway was just a reference to what is already on the car (I didn’t know the “official” name of these fittings). Sorry for the confusion. I don’t plan on buying or installing anymore of these twist things. Thanks for info on the camlock! attached are some progress shots. Rad support is done. Need to work on oil cooler and accusump mounts. -
240z SCCA vintage race car, restoration
AydinZ71 replied to AydinZ71's topic in S30 Series - 240z, 260z, 280z
@clarkspeed thanks Clark! You have given me plenty to think about. Some responses below. Again, thanks for all the feedback! 1) yep, the quik latch is something Greg told me about last week. He said he uses 6 in total but he was busy preparing for Daytona so I could make out on which car he had done so. The reviews all seem pretty good too. I liked they came in different sizes for varying load and were pretty light (more importantly, they POST the weight in their FAQ. Have not had such luck with Info on others). It will be years (if ever) before I will need to worry about being competitive by any means, so I might not have sabatoge to worry about 😂😂😂 good point though! 2) I also found some cheap knockoffs but I’m anxious to take the risk. If I can’t get the silly thing to latch right at an event, I’m toast. Im going broke, but broken is worse 😂 3) il look into the shear coupling again (sliding the hood into a “slot” towards the cowl so you don’t need a vertical latch). If I can attach a bracket to the hood with some confidence, maybe you are right about giving it a shot. Then like you said, I’d only need 2 in the front. The hood is certainly light enough to handle as one person in this manner (12.25lbs). Gotta hand it to mr. Washington. 4) I do need a solution for the FRP hatch. A link, pic or info on the camlok coupling you are using? I was going to use a single quik-latch alternatively. I am going to get their mini ones for my fuel cell cover. Button latch seems pretty damn convenient. 4) I currently have these old-school butterfly locks on my air dam and doors. Previous owner used them. I think il keep them for now, just so I have less fab work. https://www.speedwaymotors.com/Butterfly-Self-Ejecting-Quarter-Turn-Fasteners-700-In-Grip-Pack-10,29694.html?sku=91007126&utm_medium=CSEGoogle&utm_source=CSE&utm_campaign=CSEGOOGLE&gclid=CjwKCAjwoP6LBhBlEiwAvCcthDdqalvfzcDCctGA6VfGBdR-ev_hJLk6YUC8RNqy9s0w8ars3t7-CxoCS7EQAvD_BwE -
240z SCCA vintage race car, restoration
AydinZ71 replied to AydinZ71's topic in S30 Series - 240z, 260z, 280z
Whoa that’s pretty cool! Greg suggested quick latch so il giving it a shot. He said he has 6 total! I’m encouraged to hear you got away with two, that is helpful. I bought 2X 3/8” quick latches for the front, and 2X 1/4” for the back (cowl). I thought about using a mechanical shear coupling in the rear instead of a pin, but when I thought it up I was not convinced it was any lighter than just using pins. Sounds more convenient though! Just slip it into place, then click the front latches. -
240z SCCA vintage race car, restoration
AydinZ71 replied to AydinZ71's topic in S30 Series - 240z, 260z, 280z
-
240z SCCA vintage race car, restoration
AydinZ71 replied to AydinZ71's topic in S30 Series - 240z, 260z, 280z
-
240z SCCA vintage race car, restoration
AydinZ71 replied to AydinZ71's topic in S30 Series - 240z, 260z, 280z
Hmm… yeah the hinge does sound infinitely easier, but the hinge, bolts, and mounting nuts are all quite heavy. I’m leaning 2X 3/8 quick latches in the front and 2X 1/4” in the rear. There is a tremendous amount of force on the leading edge, and at only 12.5lbs the Ztrix hood doesn’t have much weight to counteract. I might even go with 3 in the front 🤷🏽♂️. now I need to carry around foam pads to set the hood down every time I take it off 😂 -
@jonbill Looks gorgeous. Good old peanut head. looks like your octane rating in the UK is a combo of higher labeling and truly higher octane. https://aircooledbug.co.uk/usa-versus-uk-fuel-octane/ Most we have here at the pump is 91. Everything over that is non-standard at the pump, is harder to find, and significantly more expensive (mostly due to the low volume of sales). In Southern California, a gal of 91 is close to $5 a gallon (~4L), while 100 octane race fuel is $10 a gallon. So you still have the weather and Brexit to contend with, but you do enjoy the superior fuel!
-
hmmm… yeah il probably stick to 10:1 until I can replicate someone else’s success. Yep the EP head has polished chambers and deshrouded seats, but I’m not sure what more I can do. I do still need to cut back the excess sparkplug threads. I know those are a definite hot spot. The block has flat-top OEM pistons, with a -0.35mm deck clearance.
-
@madkaw tell me more about running 11:1 on pump gas? Il fascinated. I have not had such luck. Open to it!
-
@madkaw agreed! Only distinction I’d like to make on the bottom end is that you are getting close to square bore/stroke with a stroker setup (86/83). I couldn’t say how much your short-block redline is de-rated from a standard L28, but the extra stroke will put higher acceleration forces on your rods. Since F=MA, you get the picture. For an NA engine, your most likely bottom-end failure point is blowing a rod at high rpm due to excessive rod acceleration forces. Therefore, if you are running a mild cam and using it for street applications I 100% agree you should put all your money into the head and just use OEM piston/rod combos (Z22piston/l28 rod for example). However, if you are going wild with the head: race cam, beehive springs, upgraded retainers. At some point, your heads RPM potential will exceed the bottom end of the stroker engine. If I choose to use the my V07 crank for an NA application, I intend on going with lightweight AM rods and pistons to alleviate the momentum forces from a near-square bore/stroke (again, F=massXaccel) In contrast, my L24 race engine is ALL head, with an OEM block. She should be able to run through 7500 reliably. Greg Ira runs his out to 8200, but has swapped in the right rods to make it happen reliably, and our shitty 4-spd class rules means we need to go well beyond peak HP before shifting. Racing application: This might be a controversial opinion, but running an L-series past 8500 is kind of silly to me. The head just won’t flow what you need to maintain torque this high. Your torque is going to start nose-diving after 6k rpm even with 320+deg valve opening durations. Therefore, the gain on you HP influenced by more RPM is not enough to counter the nose-diving torque. Especially if you have good gearing, why run the engine out so far, if your peak HP is somewhere between 6-7k? Anyhow, I’m sure some folks will disagree with me and I am comfortable with that. To save us time, I concede and you are right 😂😂