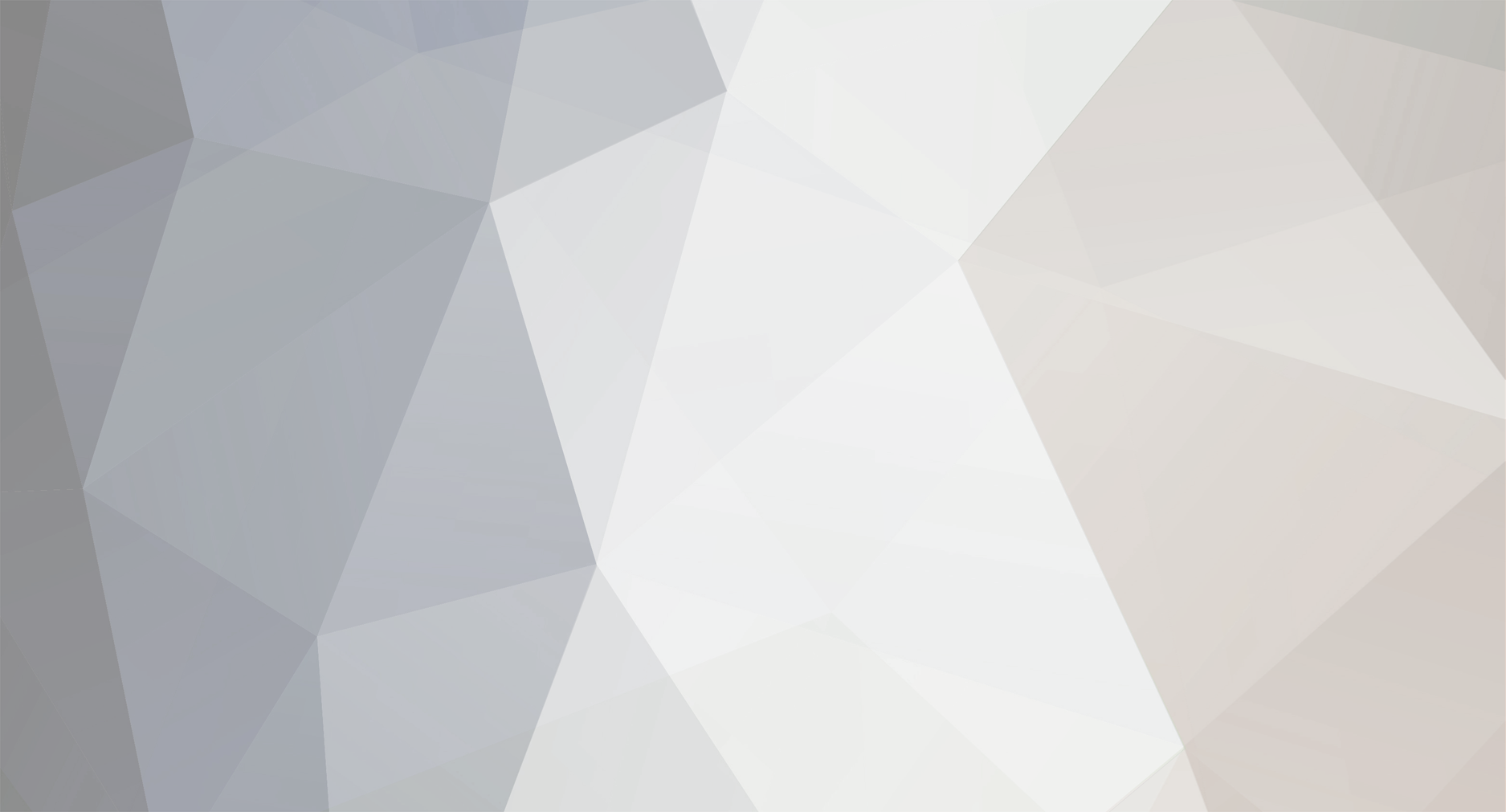
AydinZ71
Members-
Posts
1073 -
Joined
-
Last visited
-
Days Won
27
Content Type
Profiles
Forums
Blogs
Events
Gallery
Downloads
Store
Everything posted by AydinZ71
-
240z SCCA vintage race car, restoration
AydinZ71 replied to AydinZ71's topic in S30 Series - 240z, 260z, 280z
Hey all! What are your thoughts on hood pins for road racing? All four corners? Hinge the front, pins near the cowl? Got a recommendation to use the quick-latch, and they seem to be fairly light. I just picked up my FRP hood from John Washington (Ztrix) for the race car. Now to mock-up the mounts. -
yep, I have a V07 crank and N42 core at the machine shop now. Sonic testing wall thickness, and deciding where to go from there.
-
240z SCCA vintage race car, restoration
AydinZ71 replied to AydinZ71's topic in S30 Series - 240z, 260z, 280z
Thanks for the encouragement Clark! Yeah i need to save up for the 3-day course. Its ~$2500 if you use their cars, and $2k if i bring my own. Maybe late winter/spring on 2022. Since you recommend using their car, I will look into that! -
I would just like to point out how multiple people on this thread are more or less saying the same thing, and have a pragmatic sense for these things based on direct experience. This didn't happen when I was younger. There would be disagreements on figures, and those promoting outlandish numbers would often win the ego wars. This explains why I enjoy this forum over facebook. Gathering very experienced people into one part of the internet for free without all the trolls is an accomplishment of note. Now lets just manage to not get "canceled" LOL.
-
@Tbob Here is my street car (turbo) setup: - Complete L28et motor from late model 280zx. That is to say it has an F54 block and a P90a (meh...hydraulic lifters) head. - I tapped the OEM gas tank drain plug to create a new 3/8" hard line from the bottom of the tank through to the engine bay. I did this literally when I was 16-17. In hindsight I was being cheap and this is not a recommended solution. - low pressure pump to the engine bay, filling a fuel surge tank. bottom nozzle feeding a walbro 255 high pressure fuel pump. From there it is regulated by an aeromotive "return" style regulator that drains into the surge tank. Finally, the tank has a nozzle at the very tippy top which overflows back into the OEM fuel line, back into the fuel tank. I was OBSESSED with building a reliable fuel system to avoid lean/knock. - OEM intake and turbo manifolds. There were not affordable options at the time. - T3 "Super 60" compressor wheel trim. I think these are rated to about 325hp. - OEM MKIV supra Intercooler with 2.5" steel tube plumbing and an HKS racing (large diameter) BOV - Bosch (76'?) Mercedes diesel high impedance 420cc injectors -OEM downpipe and 3" exhaust terminating in a magnaflow straight-through muffler - Simple Digital Systems (SDS) EFI system. Uses crank angle sensor with little magnets I drilled into the pulley. - 280zx turbo distributor used only to distribute the "spark" to the right plug. Ignition timing managed by SDS\ - OEM clutch disk, with dual pressure plates. Holds the torque At 16psi, she was making a hair under 300hp, and about 310ft-lbs of torque if I remember correctly. Overall a modest tune. This was all assembled nearly 20 years ago. I daily-drove for about seven years, then on-off for the last twelve. I mentioned she ran reliably for about 15 years because I sold her 6 years and bought her back last year. New owner did not have any complaints, and did not touch the engine. Engine has had absolutely no mechanical problems. Wore out a Walbro pump, and the turbo is nearly dead. Shaft play, and burns oil at spool-up. I have been assembling parts for the next iteration. Here is what I have, just waiting for the race car to be done: - Protuners intake, exhaust manifolds, and downpipe. Exhaust and manifold have shipped, and already got the intake. - CD00A L-series trans adapter designed by Derek (a member here). Nissan 5-speed is borderline over 350 ft-lbs. They are going for nearly $1k here in LA, so id rather just sell it or keep it for the race car. - Wlad's Ford super 8.8 diff cradle, CV's, and hub uprights. all aluminim case "Torsen" (Helical) LSD diff a 17' mustang GT automatic Still to be purchased - eyeing a G30-550 turbo from Garrett. They are nearly $2k though, but have enormous potential - larger injectors - larger fuel pump - air-to-water intercooler, and plumbing These next upgrades will not be done until I get the car on jack-stands and stiffen the chassis. getting too far over 300 ft-lbs of torque without stiffening the thin sheet metal unibody on a 240z is not advisable. I am sure I am forgetting something. Feel free to ask. -Aydin
-
240z SCCA vintage race car, restoration
AydinZ71 replied to AydinZ71's topic in S30 Series - 240z, 260z, 280z
ah man that’s a GREAT question. I think we have learned that I’m incapable of just “flipping” a car. Certainly throw my passion into it. I’d like to race it, and see if paltry skills are up to the challenge of this over-thought race car. To be honest, I have 0 racing experience but I’d like to try! Maybe I get some track time before I get my novice license ($2200 course). heck I’d even be willing to loan the car to a driver at the track to get their perspective and learnings on how the car is handling (and should handle). I do have a lot of great canyons and windy roads for me to “test” her out. Nothing dangerous or speeding. The corners are tight enough to stress the car without excessive speed. I just need to get a neck brace since the chassis crush zones are mostly gone. she is licensed, insured, etc. other than the roll cage, she isn’t a huge attention grabber. I do need to focus on sounds attenuation as much as I can before hurting performance. Most track out on the west coast have sound restrictions, and my neighbors would appreciate it during tuning. -
My mind is blown…. No words
-
IMSA GTU vintage racer build
AydinZ71 replied to clarkspeed's topic in S30 Series - 240z, 260z, 280z
Agreed! Yeah the rule of thumb you provided sounds pretty close to what we apply in engineering. We use AL over Steel when considering other huge differences in performance like Ductility, machinability, resistance to chemicals and corrosion etc. My lightweight-structures professor thought a whole lecture on when you use AL and over steel. He actually got into how AL was “made” for aircraft as it meets the weight/lift performance and the forces on an aircraft are all distributed very evenly. AL isn’t great at dealing with long-term vibration, shock, heat cycling, and spot welding the way mild steel is. Unless it’s forged or cast with a lot of excess material (like an engine block), it exhibits fatigue cracks earlier than steel for similar cycling loads. However, for things like brackets, braces and forged subframe components (A-arms, crossmembers etc), it works great. he suggested going thinner steel cross-section on a race chassis vs AL. Especially if you switch to stiffer alloys (still ductile) like 304SS. Increasing stiffness does mean you need to worry more about shock and vibration, as the metal becomes less forgiving. You will obviously need to add more braces/crossmembers to increase the “truss” effect of the structure (like a bridge) vs big heavy conventional subframe rails. -
Agree with @rturbo 930. The L series head is not designed in a way to meet simultaneous goals of high output and street ability. I mean, for the time it was designed it’s a fantastic engine. even when you put in a race cam with high lift and long duration, the 2-valve setup and modestly sized runners are going to limit you (even on a P90). There are some bench test results out there that shows the L series head flows only a fraction of what a modern DOHC I4 can handle, like a k24 or even an SR20. All this to say, getting above 220hp on a 3.0L stroker will start to exhibit loss in daily driving ability, considerable loss of gas mileage, and some big expenses on head work. Upping the RPM band on a stroker also means big expenses on lightweight rods and pistons. I definitely suggest an L28et setup. I have one in my street Z pulling 300hp with no issues, 15 years of reliability, and modest turbo lag. Very streetable
-
240z SCCA vintage race car, restoration
AydinZ71 replied to AydinZ71's topic in S30 Series - 240z, 260z, 280z
Added a fresh-air engine intake as well (terminates to a 3” flange for mounting a duct). Greg has some critical comments so I may have gone a bit too far. I may have spent too much time on this 😂 IMG_7088.MOV IMG_7091.MP4 -
240z SCCA vintage race car, restoration
AydinZ71 replied to AydinZ71's topic in S30 Series - 240z, 260z, 280z
hey that is really helpful Clark! I’d love to run EFI on a 3.0L if I could! Be nice to have a reliable, consistent race engine. Carbs are such a pain. the background you provided on the different groups and classes was helpful! Since EP has such a well-documented rule book, I gravitated to that class since it’s more on spec and less reliant of experience (dealing with judges). So far everything was purchased, built, and installed to meet EP (including the 2.4L and head mods). there are a few other things that are borderline, like my engine bay to cowl vent relief, or new circle cross section frame rails. Not a true tube frame since the skin material remains in the unibody, and the mounting locations for all components (subframe mounts, engine placement, rad placement etc) is all OEM. Strut towers are still OEM too. this sucker just had too much rust, it seemed silly to replace with OEM frame rails when they were heavy relative to their strength (designed to crush in an accident), and thin-wall box frame is hard to find in the right size. EP states you can remove/replace unibody structural components as long as the unibody does not require “additional support” as a result. I interpret this as putting in frame rails so thin they need to be stiffened with additional ribs, stringers, angled tubing etc. after I boxed off the frame rails, it actually looks pretty OEM. The upper rad support/crossmember is the most non-OEM looking thing in the engine bay. -
240z SCCA vintage race car, restoration
AydinZ71 replied to AydinZ71's topic in S30 Series - 240z, 260z, 280z
-
240z SCCA vintage race car, restoration
AydinZ71 replied to AydinZ71's topic in S30 Series - 240z, 260z, 280z
Thanks @clarkspeed @jhm! For some reason I thought some of the vintage org’s were pretty lax on engine specs if it looks stock and still using carbs 🤷🏽♂️. For instance, I know Greg is running HSR next week and he has a crazy hot cam that would never fly in EP. I would never bother putting the 3L in SCCA. People know their stuff and I would look silly (unless like you said, I was classed right). It is pretty damn tempting to throw in a 3L though! john, I just finished the fresh-air intakes. Here are some pics with the radiator lower mount in as well. I need to bridge across now, and finish the rad upper mount. The two intakes are not identical/symmetrical but who cares. The drivers-side one is bigger, which is the one I need most. -
IMSA GTU vintage racer build
AydinZ71 replied to clarkspeed's topic in S30 Series - 240z, 260z, 280z
Same. I don’t have a TIG. Lack the skill now, but more importantly a decent one is expensive! The Lincoln electric MIG already set me back $400. Honestly, steel is the way to go for structural. You don’t get as much weight/strength savings as you would imagine going AL. AL is great as skin material though, where you are not leveraging the qualities of steel on a tube frame, the way it’s essential on a unibody. your build is looking great! -
240z SCCA vintage race car, restoration
AydinZ71 replied to AydinZ71's topic in S30 Series - 240z, 260z, 280z
Some updates, and a few questions for the phenomenal team here! 1) finally got my hands on a decent L28 short block core (N42). Need to decide on whether to use this with the V07 crank I have to make a 3.1L for vintage racing, or for a 3.0L L28et for the street Z. Open to suggestions! I already have the L28et (F54 block), but don’t have the time or space to pull that motor out the street Z. It is mechanically stock, and needs a rebuild. 2) I got my stahl header! She is a beauty. Any thoughts on the collector? She ends in 2X 2-1/4” tubes now. I can go single conventional flange, slip-on with clamp, or dual V-band. I feel the slip-on option will be the lightest option but certain to get some exhaust leak and into the cab. Made an intake for the fresh-air box which will straddle the top crossmember. IMG_6997.MP4 IMG_6991.MOV -
IMSA GTU vintage racer build
AydinZ71 replied to clarkspeed's topic in S30 Series - 240z, 260z, 280z
I have a suggestion if you are planning on rebuilding the fuel cell mount. Look into thin-wall stainless steel seamless tubing. I use it for high pressure applications in oil and gas. It’s a bit hard to weld to, as it burns through easily. However, it is phenomenally strong in tension, and has a pretty good crush resistance. It’s the lightest, strongest tube I have worked with. Not as light as AL, but stronger in tension per unit weight and weldable with a MIG. I am using it for some light structural stiffening near my radiator mount. -
240z SCCA vintage race car, restoration
AydinZ71 replied to AydinZ71's topic in S30 Series - 240z, 260z, 280z
@JMortensen @clarkspeed thanks for all the help Jon, Clark! Yep his will definitely help me once I get to the windshield. I may not be that far away! updates: 1) got a push/pull remote actuator for my Accusump. I don’t want to have that much warm oil in my cab, and it’s time to start mock-fitting all the components so I can make brackets and drill holes before primer. 2) settled on an oil cooler. Setrab series 6 34-row. Good balance of performance, price ($300) and pressure-drop (2psi). Needed it in-hand to lock-up the front and get brackets in. 3) Front-end chassis is coming along. Got the radiator lower mount welded so I can remove the top rad crossmember. Braced in 2-places to avoid warping. Almost done with inner wheel-well skin. IMG_6939.MOV IMG_6935.MOV -
240z SCCA vintage race car, restoration
AydinZ71 replied to AydinZ71's topic in S30 Series - 240z, 260z, 280z
Thanks @clarkspeed! Where do you get your Lexan from? I found A local spot that sells the right thickness I need for about $200 for a 4’X4” sheet. With your input, I think i will give it a shot! -
Trouble on initial starting..please help
AydinZ71 replied to jersey280's topic in S30 Series - 240z, 260z, 280z
If you are able to rule-out fuel pressure, try checking/replacing your ignition system consumables and replacement parts. Cap, rotor, plugs, wires, coil. Check your ignition timing to make sure it has not wandered. in my case, most times I have had poor cold-start was because my Spark had weakened or become inconsistent. This is most obvious when the car is cold. Once she is up and running, a poor/inconsistent spark can improve as the ignition parts and plug warm. -
Control arm damage fix opinions
AydinZ71 replied to calZ's topic in Brakes, Wheels, Suspension and Chassis
Can’t argue with that! My Brian is in “race car” mode, and I’d probably stick to soft bushings for a street car too. honestly I feel like you are probably OK to just reuse them. If I remember right, the 22mm bolt goes right into that sleeve you cut right? The bolt will keep the tube from collapsing. The plausible failure mode here is the lateral stress cracks/peels the steel back at the spot you nicked, but could it really go far enough for the bolt to come out? More likely it causes the bolt to loosen. PU bushings are more rigid, and will “hold” the OD of that tube better but they are a rougher ride of course. If you choose to run them, I’d check if the bolt may have loosened for a few days/weeks until you have some confidence it’s in there. Could also use blue locktite, but at 22mm that is a LOT of torque to break free when you do want to remove them. With that said, you can remove them without removing the 22mm bolt by unbolting the bushing shackle, then pry the 22mm bolt loose on a bench. The bolt is there to pre-load the bushing as newzed described. You don’t really need my advice. I have two kids and don’t have any car friends nearby, so consider this as a technical rant from someone spending too much time on their car alone 😂. I do enjoy the “what if’s”. -
Control arm damage fix opinions
AydinZ71 replied to calZ's topic in Brakes, Wheels, Suspension and Chassis
If you look at the risk, it might just be easier to buy one for like $50. All the T3 and Apex junkies are throwing away their OEM LCA’s like they are bras at a Grateful Dead concert. I bet you could snag one in decent shape. if it were me, I would cut off the whole end and make it a Heim/end-link, but I recognize most folks may not feel confident. -
240z SCCA vintage race car, restoration
AydinZ71 replied to AydinZ71's topic in S30 Series - 240z, 260z, 280z
I have been weighing OEM components (albeit rusted) as I remove them, and weighing the replaced metal. Here is what I found: 1) the OEM pedal assembly & steering column mount. Going to Tilton assembly net 3lbs savings (including the independent rear brake MC). 2) cowl being replaced with 20-gauge single layer of steel saved about 4lbs. 3) engine bay unibody frame stiffener: this was a wash. The stainless tube is pretty heavy, but is a more efficient cross-section and I stronger. 4) my reinforced rockers added about 3lbs per side. 5) little floor pan support extension is about 1.5lbs per side. since the front end isn’t supporting much weight, this will be a thinner gauge of tube. Net, I think I’m up maybe 10-15lbs with the strut tower reinforcements. I have gone back and ground down all my welds to reduce as much unnecessary steel as possible. I’m also concerned about the additional weight I have added, but there is also quite a bit of unnecessary stuff I have removed (mounting tabs, weld-nuts, lap-joints etc.) -
240z SCCA vintage race car, restoration
AydinZ71 replied to AydinZ71's topic in S30 Series - 240z, 260z, 280z
Other things I’m working on, and a few questions for the team: 1) bought all the electric gauges I need, and working on gathering the sending units and wiring leads. Settled on: tach w/ light. fuel pressure 0-12psi oil pressure oil temp Water temp fuel level Volts 2) looking at oil coolers. Setrab most likely. Struggling to determine if an “oversized” unit would be bad in any way. The oil can’t get too cool when racing since water temp is thermostatically regulated and a cooler oil will just warm to the block/water temp. 🤷🏽♂️. 3) looking for an affordable Lexan front windshield, but struggling to find one. Rear hatch is easy since it is flat. 4) just got the FRP hood ordered and already have the FRP ear hatch. Looking at the 280z FRP bumper as it is touted for having a positive aero effect. -
240z SCCA vintage race car, restoration
AydinZ71 replied to AydinZ71's topic in S30 Series - 240z, 260z, 280z
Latest updates. Replacing my rusted unibody frame stiffener w/ 316 SS tube. Will box-out the front, mount the rad for clearance, and replace the top crossmember next. Also finished my little project replacing my rusted cowl box with an engine vent out of the OEM cowl vents. Might not fly with the SCCA judges, but I can always block this off with a sheet of steel if I have to. IMG_6894.MOV IMG_6878.MOV -
IMSA GTU vintage racer build
AydinZ71 replied to clarkspeed's topic in S30 Series - 240z, 260z, 280z
Sweet! Sounds like you have it figured out. The front-end scraper is a great idea. How do you plan to mold the front-end radiator shroud? Keep the slip-stream from going over the rad. Plastic or AL? ideally I want to run a air splitter from the 280z FRP bumper, and use the bottom intake for the oil cooler. Setrab makes a really neat, long oil cooler that would span the width, but they are super expensive (~$500). Their regular oil coolers are about half that. I am tearing my front-end apart. Il post some pics.