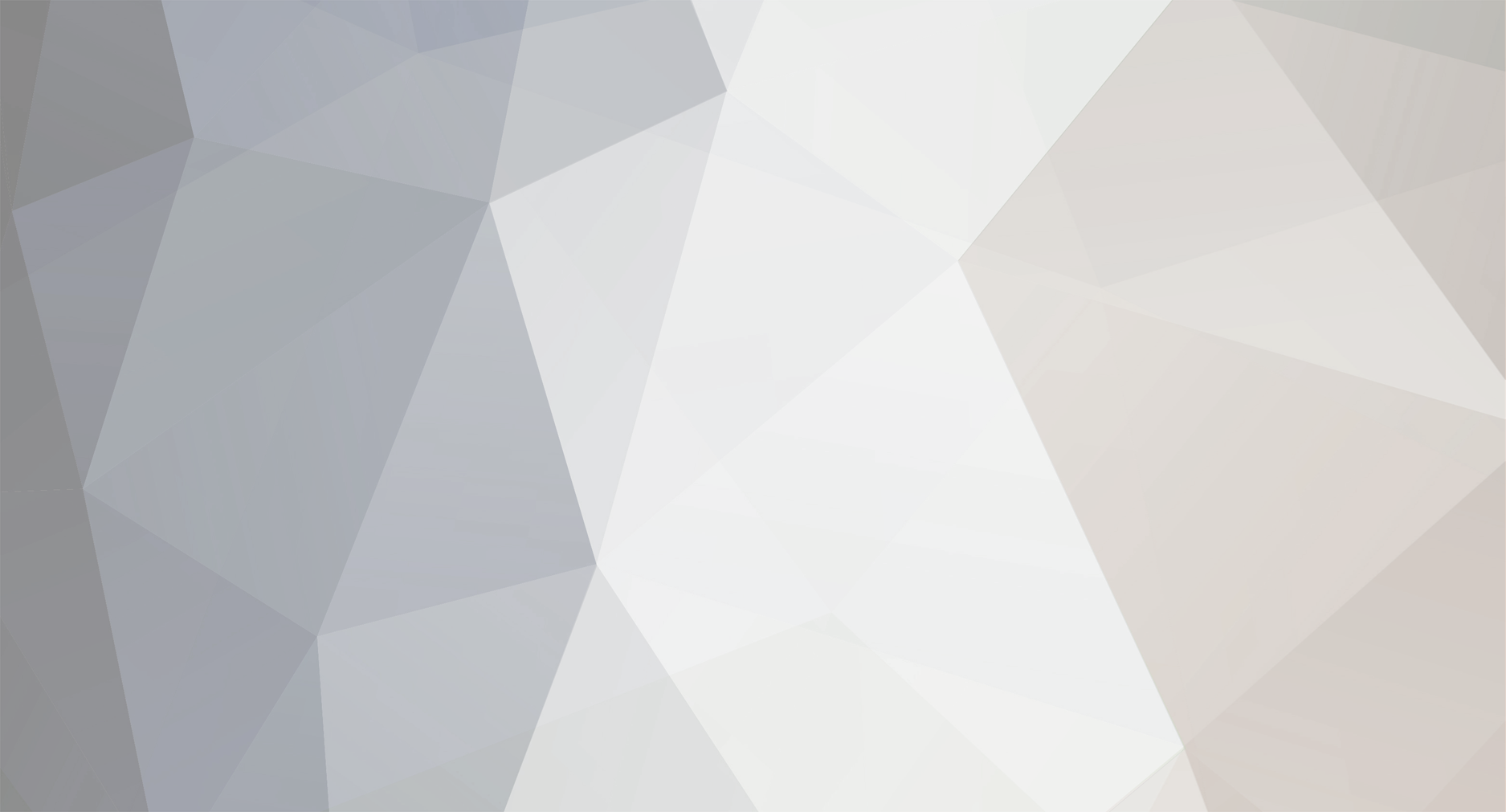
mikeatrpi
Members-
Posts
380 -
Joined
-
Last visited
-
Days Won
1
Content Type
Profiles
Forums
Blogs
Events
Gallery
Downloads
Store
Everything posted by mikeatrpi
-
Here's my build. Its still in progress. It gets better on the 2nd page or so. http://forums.hybridz.org/showthread.php?t=127833
-
I'm just a hobbyist, so caveat emptor. But I'd use epoxy instead of etching primer. Google it, there is a debate over the two products, but epoxy seems to be the stable choice for long term. And for the single stage, I'd use a urethane... not an enamel. I'd have pretty good luck spraying PPG Omni products. If your underhood metal is in decent condition and you're spraying a light color, you could probably avoid a sandable primer and just topcoat the epoxy. With a darker color (which hilights defects), you might want to use some high build and sand it down before the SS.
-
NA to turbo conversion - questions and answers...
mikeatrpi replied to mikeatrpi's topic in Turbo / Supercharger
For my MAP hose? I used the tubing that came with my boost gauge, but I'm worried about it too. I'll shop for something more reliable. Thanks. -
NA to turbo conversion - questions and answers...
mikeatrpi replied to mikeatrpi's topic in Turbo / Supercharger
Update time... Here's some more stuff attached. The intake manifold fit OK... I also had to trim a little with the dremel on the edges, like I did with the exhaust manifold. Here's what I did for the PCV. Its a variation on Sean's method (X64v). I used some heater hose and plumbing fittings to route the PCV plumbing up to an unused fitting on the bottom of the throttle body. It takes a 3/8" hose easily, which also routes around in a loop without kinking. Here's my megasquirt wiring in progress. I mounted it a small piece of lexan from the depot. I didn't even bother to peel off the paper - I sorta like the white look. I used the stock wire grommet (sadly I had to cut my harness to get it off), and I passed the MAP hose through it and shrink wrapped it all down. The plastic hose didn't collapse, so I think this will work to keep everything neat going through the firewall. The vacuum tee is for my boost gauge. Wiring. I made all of my wires 10 ft in length, and trimmed to fit once in the car. I probably could have gotten away with 7-8 feet and still had plenty. I bought 18ga and 14ga wire spools from del-city. Stock CHTS, and my battery attachments. Coil (I had to move it; it hit my 1g DSM BOV). I just bent the bracket and moved it up. You can also see my MS ground. Don't worry that's not my only one. OK here's the turbo oil feed pulled out of the way, and you can see how I routed and attached the MAP vacuum hose. Ta-da So far, I have the Datsun CHTS calibrated, TPS calibrated, and a tach signal in MS from my locked distributor. Hopefully with my next update I'll have the timing dialed in. -
Regarding the fetch and burn - its almost like it automatically sends the changed values to the MS for me. In the spark window there were two red messages - unsent and unburned (or something like that). From the manual it looks like it puts my changes directly to the RAM but does not burn them to the flash unless I tell it to.
-
Moby thanks! I calibrated the TPS, restarted megatune and rebooted the MS. The values stuck. I added 3 to the closed, and subtracted 3 from the full to absorb some variance I noticed trying this several times. I now have a working TPS signal!! I also just got my RPM to register from the VR input by adjusting the pots all the way counter clockwise. I'm using a locked distributor directly into the MS v3. I have some more wiring to do and I need to get #1 to TDC so I can clock the rotor properly. Thanks again!!
-
Thanks. I'll leave the stock + and - wires on the coil, and add only my spark out (pin 36) to the - side of the coil. I just realized I never connected pin 15 of the DB37 to ground, per the MSnS instructions. So I have to do that. Other questions: 1. I'm using the GM IAT and the Datsun CHTS (with values from the sticky). They are reading about 8-10 degrees F different. The IAT is pretty close to the air temperature... but the CHTS is colder. Should I try for a more individualized customization or is this normal? The car hasn't been run yet (meaning I'd expect the block and air temp to be close to the same) 2. Trying to calibrate the TPS. I ran their wizard and got some numbers. How do I "save" these? 3. Should "Fetch from ECU" and "Send to ECU" in the various MS menus change things? It seems like "Fetch" doesn't actually do anything. I want to make sure my settings are making it to the ECU. MANY MANY thanks!!
-
I am adding a turbo to my 82 280zx NA engine, using megasquirt. Its a MS1 V3 PCB. I'm using a locked VR distributor, and plan to use MSnS. I have about half the wiring done - Datsun CHTS, GM IAT, TPS from a Quest, etc. I don't have the coil, injectors or fuel pump attached yet. I installed the MS in the stock ECU location. There was a plug there with a single lead that I'm using as my switched 12v source - it has power in RUN and CRANK. But - there are two wires on the 280zx coil. If I disconnect them, that switched lead no longer works. So, what should I have attached to the coil? There's a stock wire on the +, do I keep it? Another stock wire on the -, ? [side Question - is this for the Tach?] I have a 12v + from the fuel pump relay, not yet attached. Should I? The IGN OUT from the MS for the - ? Thank you!!! PS I'll be back with more questions and pictures soon
-
NA to turbo conversion - questions and answers...
mikeatrpi replied to mikeatrpi's topic in Turbo / Supercharger
Thanks Sean. Unfortunately I turned the motor over a few times without the distributor attached. I think that means I do need to set #1 to TDC and bolt up the distributor then. -
NA to turbo conversion - questions and answers...
mikeatrpi replied to mikeatrpi's topic in Turbo / Supercharger
The drain, again - this is the final product with hose clamps, etc. I put some jb-weld putty around the pan fitting to plug a small weep it had. And, here's the oil feed parts. 1/8" BSPT Tee with an NPT fitting on the side... this threads into the block where the stock sending unit was. The sending unit goes to the female BSPT fitting on the tee. Then I have an adapter and -4 AN push-on hose and fitting running to a banjo. All that stuff cost a hair over $50 from British American Transfer... BAT, Inc. I put all of the fittings together dry. I know the AN doesn't require any sealant, for sure, and I didn't think BSPT or NPT did either. And - I tried turning over the car a few times to prime the oil line... but I was unsuccessful. Either I didn't crank long enough, or there's just not enough oil pressure until the engine is running. I welded up the tip of the stock banjo bolt, and drilled it to 1/16" to serve as a restrictor. Got this idea from the archives. In the car: -
Looks great, Dave! Everything is so clean...
-
NA to turbo conversion - questions and answers...
mikeatrpi replied to mikeatrpi's topic in Turbo / Supercharger
Another dumb question. Is my oxygen sensor too close to the turbo output? Is there a rule of thumb where to put it? Thanks all -
NA to turbo conversion - questions and answers...
mikeatrpi replied to mikeatrpi's topic in Turbo / Supercharger
At the risk of sounding really dumb... Do I need to set #1 to TDC? Do I then need to orient the rotor in the distributor (by loosening the screw and turning the assembly I welded) so it points to #1? Or does none of that matter and the computer handles the adjustments?? -
NA to turbo conversion - questions and answers...
mikeatrpi replied to mikeatrpi's topic in Turbo / Supercharger
Another update. I took a few days off work to start the swap. I'm going to need to burn a few more to get this finished... Let's say I had a few set backs. I was able to ez-out both the front and back studs which were broken off in the head. I chased some of the threads with a tap (I know its not the proper way to do it) and installed studs to hold up the exhaust manifold. I later backed out the studs and used the nissan bolts. My manifold must have been pretty warped, because I had to do a little trimming with my grinder and dremel. This is a fel-pro gasket with copper spray. I had to modify my oil drain slightly too, since my initial measurements when I tapped the NA pan must have been wrong. I cut a pie slice, bent, and welded the drain. Its great and it still clears the steering rack housing. (no bolts or hose clamps yet - this was a test-fit) I pieced together a downpipe and exhaust system using 2.5" mandrel bends from jc whitney. The oxygen sensor bung is actually an 18mm spark plug non fouler that I cut in half and welded on. I found that tip in the archives. I now have 2.5" exhaust from the turbo to the cat, and 2" out a straight pipe. I'll replace the back half in the future. There's so much left to do... finish the drain, do the oil feed, install the intake manifold and all the other stuff... Question for the MS crew - when installing my distributor, does anyone have tips for lining it up and setting the angle in megatune? -
Why are you using the FIDLE output to drive the MSD? Shouldn't you use the ignition out pin #36, with the v3 board?
-
I pulled one out of a quest van for mine. It had three wires coming out the side, plus three more on the connector. Use the side wires, not the connector, for the gradual reading. perhaps yours is the same, with multiple sets of wires?
-
Ditto, I'm only using 1,2,3 with 4,5,6 unplugged. My TPS is out of a Nissan Quest from the junk yard.
-
Very nice! Clive gave us a fly-by getting on the Merritt yesterday. That car sounds __fantastic__ as it roars past you!! We got lucky that he had a straight shot and open lane to take off. It was good seeing you guys again.
-
NA to turbo conversion - questions and answers...
mikeatrpi replied to mikeatrpi's topic in Turbo / Supercharger
I soaked them in fuel injector cleaner, per this guy's instructions: http://fordfuelinjection.com/?p=82. It smelled like kerosene though. The cleaner did darken a little bit after several hours, but it wasn't nearly the dramatic transformation I was expecting. Either the injectors I bought from Derek were in really great shape, or my cleaning experiments were flawed. I won't really know until I put them on the car and try it. I bought new plugs from a guy on EBay for $2 a piece, and the filters / pintle caps / orings from cruzinperformance (rich jensen). I'm pleased with both of their products... particularly Rich's thoroughness. We talked on the phone and emailed several times to ensure I was purchasing the correct parts. I used an ez-out to pull the filters out of the injectors. I couldn't get a screw to grab. Make sure to test the resistance of the injectors and also use a battery to fire them off and on when you're blowing out the crud. -
NA to turbo conversion - questions and answers...
mikeatrpi replied to mikeatrpi's topic in Turbo / Supercharger
Cool Sean, thanks for the answer. I remember seeing your head gasket photo describing proper orientation in your build thread. I will be PMing you soon, looking for a good MS map to get started with. I am a few weeks away from installing this beast... -
Thanks guys. It was really hard to start the die - I put the small end in my drill press to get leverage, and rotated the chuck by hand. The rod that was connected to the wastegate however was more difficult... I used vice grips and a c-clamp to attach it to my bench, then basically put all my weight and force into the die while rotating. Raff the PO is a well known guy on this forum *cough* bruce lee z *cough*. He basically gave me this actuator along with the bulk of the turbo parts I bought from him. He couldn't remember the details of all of the modifications - if the spring was stock or not - but with the help from this forum I found a solution that will let me dial the boost back to a usable level for my application!!
-
NA to turbo conversion - questions and answers...
mikeatrpi replied to mikeatrpi's topic in Turbo / Supercharger
Time for an update. I built a megasquirt kit... thanks, diy-auto tune. MS1 v3.0, with MSnS firmware. I locked the distributor advance by removing the vacuum actuator and welding the advance screw to the lower plate. I tested this in megatune with an electric drill spinning the shaft. Seemed to work ok for a first test. I did a little junkyarding too. I couldn't find a 240sx, so I grabbed this TPS from a quest minivan. It works! I had to build an adapter plate, with holes drilled and tapped to accept the new TPS. The turbo is ready to run... I had to clock my turbo a little bit by loosening the six compressor nuts and rotating the housing. I also cut a section out of the wastegate actuator rod, threaded it with a 1/4-20 die, and installing an external spring. I adjusted the external spring tension so that the wastegate opens at only a few PSI. Finally - I serviced the fuel injectors. I disassembled and soaked them, blew them out with compressed air, and installed new o-rings and filters from cruzinperformance. I also cut and welded off the cold start injector. -
I ended up cutting about 1/2" out of the arm, and threading it with a 1/4-20 (coarse) die. It was really hard to start the die by the way! Then I put a spring from the hardware store between some washers and reconnected the arm with a connecting nut. I adjusted it to open at only a couple of psi... I can easily adjust this in the future. I have more photos at the link in my sig.
-
The job thread. What do you do for a living?
mikeatrpi replied to Sideways's topic in Non Tech Board
I design computer chips. -
I disassembled the actuator. There were five tabs epoxied on the sides holding it together. It sure is a big spring in there! He installed a washer and used screws to pre-load the spring from underneath. I removed the washer and screws. Now, it seems to open slightly sooner than 12 psi, though I need a more precise measurement method to be more accurate. The wastegate flapper should be fully closed when < 7psi, correct? When it starts to open, how much should be open? This one goes fully-open around 15 psi. Photos of the insides: