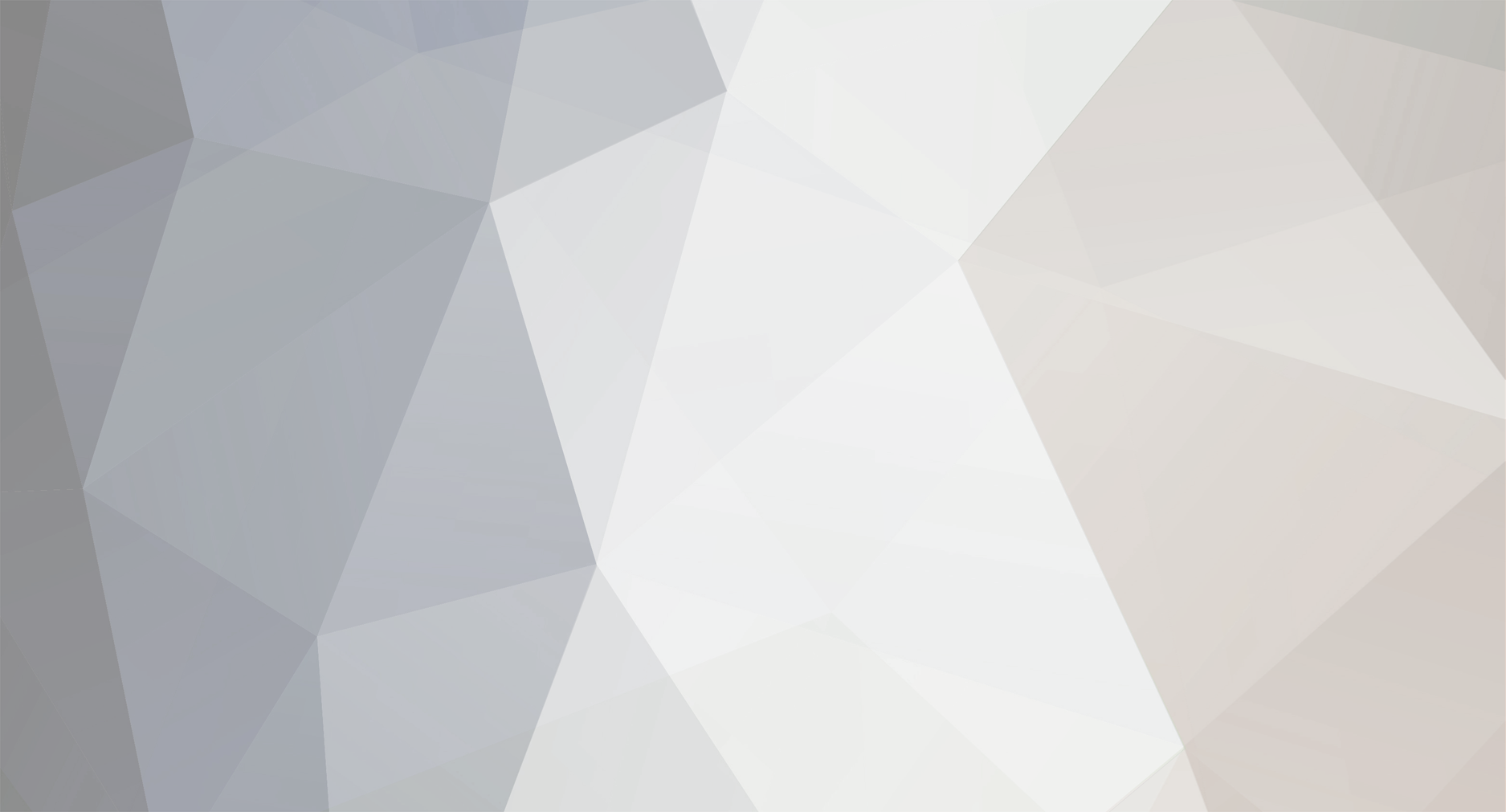
mikeatrpi
Members-
Posts
380 -
Joined
-
Last visited
-
Days Won
1
Content Type
Profiles
Forums
Blogs
Events
Gallery
Downloads
Store
Everything posted by mikeatrpi
-
Sean, keep updating your build thread like you did the other day. Its very helpful! I'm going to the basement now to see about relocating my PCV a-la sean style....
-
Can you slip the hose over the oil pan fitting and clamp it? Don't use the AN fittings on the pan side. You can measure to find the appropriate sized hose. The drain has little pressure. My 2c.
-
I have seen the spring on the outside trick, but I need to do some more reading on that. As for lengthening the rod... won't this open the flapper a little bit?
-
The turbo did indeed need to be clocked. I loosened the bolts around the perimeter was was able to easily rotate the outside. I did not adjust the hot side at all. I basically did it using the notch in the drain as reference for the bolt nearby. The wastegate flapper moves easily without the actuator. Due to the improper clocking, the actuator was fully extended. After fixing the alignment, the wastegate actuates at 12 psi. That says the diaphragm is good. Unfortunately its too high for me. The seller told me it was modified when I bought it. My fault for thinking that could be easily un-done. Anyone got a spare 7psi actuator? Anyone need a 12psi one?? Thanks for all the advice fellas.
-
I initially thought it was clocked a little bit off as well. The wastegate shaft has a bump and rubber washer, presumably where it mates with the diaphragm part. That bump and washer are fully extended... clearly seen in my first photo. I can't imagine it having any additional extension beyond that point. I also had to grind a little bit off the drain fitting when I was bolting that up for a test fit. The side of it hit a bolt nearby. At the time I chalked that up to an order of operations error. Now it seems like more evidence that its clocked a little bit goofy? Time to figure out how to fix that...
-
I mounted the wastegate actuator onto my turbo today and attempted to determine what PSI caused movement of the lever. Well, it was very difficult to get it to bolt up, and the rod was under tension. With the WG actuator attached as shown in these pictures, I am unable to move the flapper with my hand. 20 psi blows through without actuating anything... I can feel / hear the air leaking out. Any suggestions?
-
That screw is the one that connects to the vacuum advance. It threads into to the top plate, goes through the vacuum advance actuator (which I removed) and fits into the slot on the bottom plate. By welding the screw to the lower plate I locked the advance.
-
Forgive the bump of an old thread, this information is very useful! I concentrated my efforts on the #8 assembly (referring to the diagram posted on page #1). I removed the vacuum advance, and put the screw back in. Then I placed a tack weld from the underside to lock the screw. I did not weld the top screw. At least not yet. Once I get this into the car, I'll evaluate that. I might just run the threads through some jb-weld... better than loc-tite! I also didn't remove any parts permanently. When re-assembling the distributor, the slots on #9 have to align with the pins on #11, correct? The diagram leads you to believe that #9 fits perpendicular to those pins. I ran it on megatune with an electric drill... got the RPMs up to about 2000.
-
Short of a specialty faster store, I've had good luck in the Help! section of the parts store (zone, advance, etc)
-
NA to turbo conversion - questions and answers...
mikeatrpi replied to mikeatrpi's topic in Turbo / Supercharger
Question for you all - should I replace my head gasket before I swap over to the turbo? If I blow it, is the car still drivable (limp it home) or am I looking at a tow bill? I will need to drill and replace one, maybe two, exhaust studs on the head. I also suspect the valve seals could use replacement. Both of these are easier with the head out of the car... sigh. Its only money, right? -
Well now I am embarrassed by the lightheartedness of my earlier post. I misinterpreted your earlier message. I don't "know" you but I feel like I do through your videos. If you have to get a loan to afford the bike, maybe you should rethink the decision based on that alone. Its one thing to get a loan for something you need - education, medical, housing - but for another toy? I wouldn't get into debt and cause a rift with the missus... you must like punishment?
-
NA to turbo conversion - questions and answers...
mikeatrpi replied to mikeatrpi's topic in Turbo / Supercharger
I bought mandrel U bends from JC Whitney, then cut and welded to fit. Thanks for the compliments! -
"its better to beg forgiveness than ask permission" (disclaimer - I'm not married)
-
NA to turbo conversion - questions and answers...
mikeatrpi replied to mikeatrpi's topic in Turbo / Supercharger
Here is the intake manifold ready to run. Its just the NA manifold cleaned up, sandblasted, and coated with PPG epoxy primer and MC161 clear coat. That's right, no paint. The details - bolts, block off plates, springs, etc are all painted silver. I blocked off the EGR, cold start injector, idle air controller on the bottom of the manifold, and an air fitting on the throttle body. I also plugged the hole that the PCV used to occupy. Instead, I'm going to route it to a spare fitting on my throttle body. Pics of that soon. I left the water passages open on the throttle body. I also built half of the downpipe and a pipe to connect the turbo to the airbox. Which was also primed / cleared My flange is only 1/4" steel. I might need to replace this if it warps in the future. I didn't have anything thicker on hand. This lenox bi-metal hole saw from the depot, with a little cutting oil, worked nicely on the plate. It makes an awful noise though. Lastly, the valve cover. I primered, painted and cleared this one. Its the same silver as the details on the intake manifold. -
That looks amazing! Great job!
-
I did exactly what you're trying to do, about 4 years ago. I was using rustoleum primer on my car as I completed each section. When the car was done in rustoleum primer, I mixed up PPG epoxy primer and sprayed a coat. It immediately lifted the finish... it wrinkled up and was terrible. I had to strip it all back again. That's when I noticed I had to redo some bondo work, as the rustoleum let some water in. How you proceed depends on your goals for the car. If you want it to be a nice, don't mess with it again, finish - do it right. Epoxy, bondo, epoxy, primer, paint. If you want a good enough for now or the next few years, maybe give the roller-rustoleum paint job a try.
-
I bought a 40 cu ft cylinder on ebay for under $100 shipped from Indiana Oxygen Co a few years ago. You can exchange it locally for the fill, at the price of gas. For the regulator - I'm surprised you can't find one used somewhere. Just to be sure, the rest of your machine is set up to MIG? Edit - regulator http://cgi.ebay.com/HOBART-WELD-IT-BY-SMITH-MIG-ARGON-CO2-WELDING-REGULATOR_W0QQitemZ250283353481QQihZ015QQcategoryZ67055QQssPageNameZWDVWQQrdZ1QQcmdZViewItem cylinder http://cgi.ebay.com/40CF-WELDING-CYLINDER-NITROGEN-ARGON-ARG-CO2-HELIUM_W0QQitemZ370077744347QQihZ024QQcategoryZ11774QQssPageNameZWDVWQQrdZ1QQcmdZViewItem
-
Willens, how do you plan to balance the assembly when you do the rebuild? Can you share photographs and / or tips for the rest of us? Thanks! Mike
-
No, it won't seal out water. Furthermore - speaking from experience - you can only topcoat Rustoleum with more rustoleum. If you plan to use any kind of "real" automotive paint product, you will need to remove all of the rustoleum. BTDT.
-
I run a Rigid 18tpi blade from the depot in my JET. I have been meaning to buy a bi-metal blade but this one is still working so there's no need to replace it yet. I have tried using WD-40, cutting / tapping oil, and just dry... so far, dry seems to work just fine.
-
Warren, thanks! I have that problem on my T-tops too.
-
A sealer is opaque, not sure how you intend to keep the bare metal look? That said I'd spray one coat of epoxy. When its time to do a proper paint job you can scuff it and put bondo on top. Then scuff the entire car and spray one more coat of epoxy, some high build primer, then paint. Sounds easy, doesn't it? I like PPG Omni MP170 epoxy. You'd need two quarts epoxy - that's 3 quarts mixed with its companion part. Its inexpensive too... I think a gallon is $100 or so.
-
I'm in the same boat as you, Derek. I was outbid for the stock fitting that junglist posted. The block it 1/8" British standard pipe thread, tapered... BSPT. Not exactly the same as NPT. You can buy adapters between the two. I believe - but don't quote me since I haven't actually tried it yet - that you can thread the stock oil pressure sender into a BSPT female thread, but you can't thread a male NPT fitting into the BSPT block. That means you only need one adapter. Again don't quote me. I am planning to piece together my oil feed using AN lines and adapters, when the time comes. Especially if someone outbid's me again on ebay!! Edit - Proxlamus has a good post in the archives describing how he welded the stock banjo bolt closed then drilled it to .060" to serve as a restrictor.
-
Careless, any news? Did you decide to use a nissan bearing, and are you glad you did? PS my white smoke and clutch smell went away after about 100 miles. I'm very happy to be back on the road!
-
I agree with Ron - spray a test piece first. You'll probably need a new bottle of hardener and reducer though.