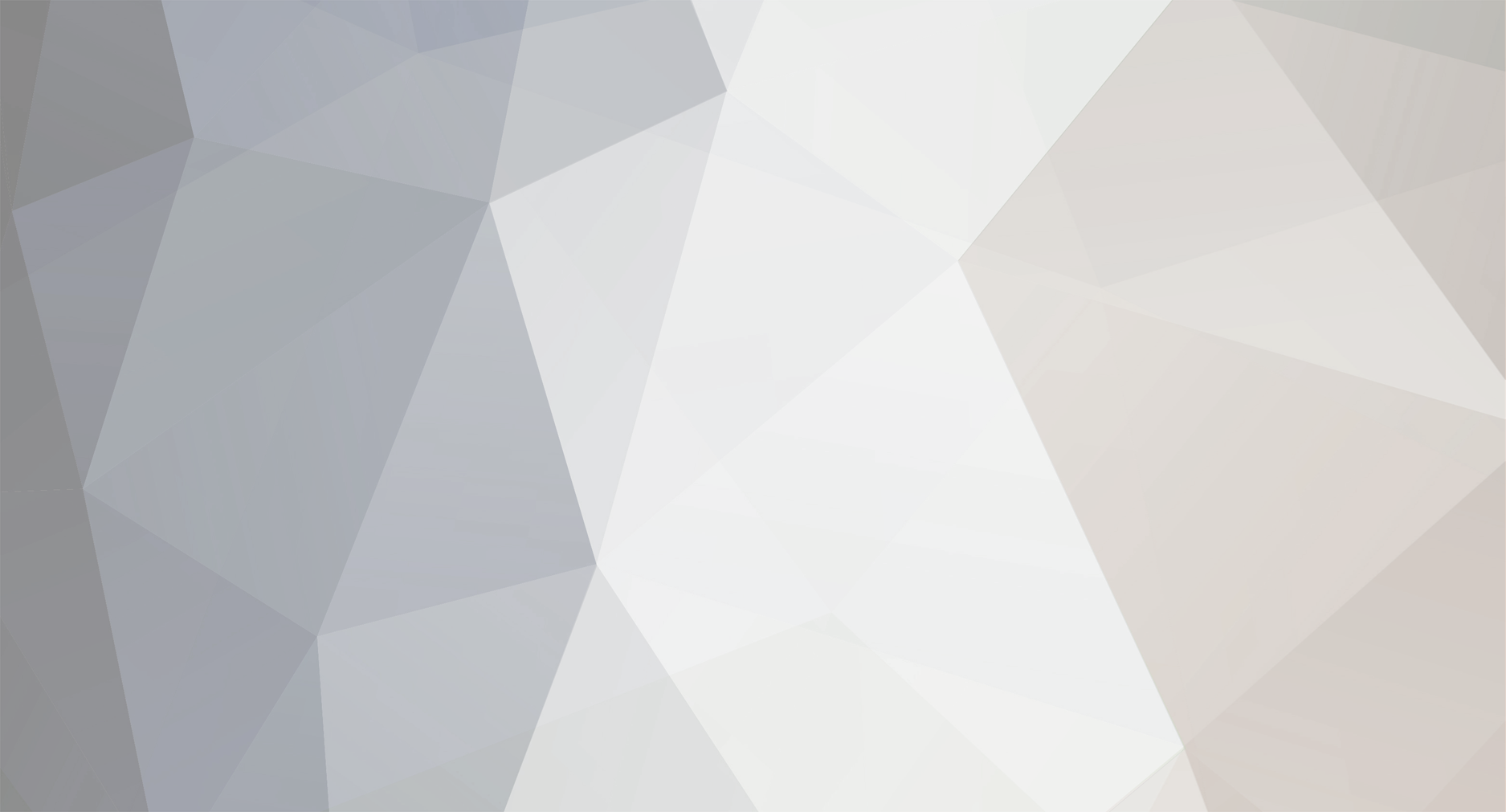
ktm
Donating Members-
Posts
1724 -
Joined
-
Last visited
-
Days Won
3
Content Type
Profiles
Forums
Blogs
Events
Gallery
Downloads
Store
Everything posted by ktm
-
"They sell surplus metal by the pound, as well as new stuff. It's RIGHT around the corner from McFadden-Dale hardware, as well! Perfect proximity for one-stop-shopping. Between those two places you can get in real trouble!" ....and Orvac electrical supply is a little ways down from them as well!
-
I am using the Wolf V500 EMS in my build. The Wolf system requires injector pulse width as an input versus load (as measured by MAP or TPS). I've developed a spreadsheet to calculate my injector pulses based on an AFR map for MAP load cycles and RPM. The spreadsheet also calculates duty cycle per RPM and load. I need someone to do a quick check on my injector pulse width calculations if possible. I know that this is for the MS system, but the Other EMS forum is a little dead and I figured that the folks here may have a clue as to these calculations. The RPM intervals and Load % in my spreadsheet are the Wolf standard intervals. I calculated the pulse widths for maximum boost first, and then reduced the pulse width based on the density ratio for different load cycles. Thanks. Injector Pulse Width.zip
-
Two inch piping? Nope, but I am running 2.5 inches. The turbo outlet is 2-inches; I am running a 2 to 2.5 inch reducer right off the turbo outlet and 2.5 inches all the way to the TB. At the TB I have a 2.5 to 2.75 inch reducer (my TB measured 2.75 ID). (2.5"/12 inches/foot /2 (for radius))^2 * 3.14159 = 0.0341 sq. ft. Assuming 600 cfm (400 hp - again, referencing CB's book), that yields 600 ft3/0.0341 ft2 / 60 secs/min. = 293 ft/sec.
-
IAT won't be a problem as I am going to run the Wolf EMS. I am running a T03/04E 0.63 A/R, 50 trim turbo. I'll be boosting from 15 to 20 psi. Welding the connections is something I may do in the future, but in all honesty there are only two connections that would be eliminated by welding. I still need the TB and both IC connections, as well as the turbo connection. Thanks all for the compliments.
-
Three inch piping would be quite tight. If your turbo outlet is 2 to 2.5 inches, just run a 2 or 2.5 inch coupler and short 90 degree pipe to clear the steering shaft. You can then run a reducer up to 3 inches. However, three inches will not clear the stock holes in the front radiator support.
-
Pop, exactly. I mentioned the very same concerns in my reponse to the first poster (intake volume increase). However, velocity does play a role with the volume increase in the form of Q = V x A. For the incremental increase in intake tract volume, the flowrate of 400 to 600 cfm will quickly fill that additional volume. Thus, I do not expect an appreciable increase in response. Your comment regarding pressure drop is dead on as well, and is a concern of mine too. I am more worried about the pressure drop across my I/C than I am about the slight increase in length of the pipe. If you play around with compressed air flow calculators, you will see that for the tract lengths we are talking about, the incremental increase in length, while doubling the pressure drop, is still below 0.3 psi. (3 foot pipe - 0.17 psi; 5 foot pipe - 0.28 psi). As a matter of fact, my piping is less than 5 feet. It is actually 4 feet long from the turbo outlet to the I/C inlet. http://www.engineeringtoolbox.com/pressure-drop-compressed-air-pipes-d_852.html Edit: Please don't take this the wrong way. I thoroughly enjoy learning and I view everything as a learning exercise. If I am wrong in my understanding, please explain. We got off on the wrong foot in the fuel pump thread.
-
Opinions Sought - Spinners/Knockoffs on Turbines - Pic
ktm replied to ktm's topic in Brakes, Wheels, Suspension and Chassis
Sweetleaf, I do not know anybody by the name of Ryan. -
Pop, you are correct about head loss and lag. However, I shall refer to Corky's book as a guide, which states that at 400 hp/600 cfm the velocity would be around 293 ft/sec (see page 62 of his book). The book also states that a 2.5-in. diameter tube will be adequate to flow 600 cfm without unreasonable drag. Using 293 ft/sec, an extra 2 feet of pipe takes the charge air .007 secs longer to travel. Even moving 200 ft/sec, the extra 2 feet of pipe would only increase the time to .01 seconds. Cygnus, Sam Adams Black Lager.
-
My intercooler core measurements are 20x12x3. It's a little on the smaller side, but should flow enough for my horsepower goals. The overall measurements are 27x12x3. I looked for hours for an intercooler that would fit exactly between the upper holes and also include as many flow channels as possible, while not impacting the lower valence. http://cgi.ebay.com/ebaymotors/ws/eBayISAPI.dll?ViewItem&rd=1&item=190139189047&ssPageName=STRK:MEWN:IT&ih=009 That is the intercooler I bought. According to Corky's book, I should be looking for a charge area of 66 sq. in. for 400 hp/600 cfm.
-
The air is moving at over 300 ft/sec.....an extra couple feet is nothing. The slight increase in volume is the other issue, but that would only impact the turbo lag. Again, given the velocity, the flowrate would be such that the incremental increase in volume would have a minimal impact. As for the bends, there are no more bends in this setup than there are in a convential behind the fan setup - 4 bends for the inlet, 3 bends for the outlet. As a matter of fact, my outlet bends are very smooth. One 90 degree and two 45 degree. The bend coming up from under the engine is a 70 degree bend.
-
Opinions Sought - Spinners/Knockoffs on Turbines - Pic
ktm replied to ktm's topic in Brakes, Wheels, Suspension and Chassis
If I don't run them with the spinners, I won't run them with center caps either. It's not an all or nothing deal, I don't like the look at the normal center cap. I am having a hard time deciding on these which is why I am asking. -
I routed my intercooler piping under the car for a couple reasons. I was originally going to go with an I/C with the inlet and out on the same side, but I did not like how crowded the driver side would be. I searched for hours and hours, went through a couple six packs just staring at the front of my car before I decided to run my piping under the car. As you can see in the following photos, it is a very clean setup. What you see is the entire setup. I hope these help someone in the future thinking about the same route.
-
Strengthening Front Anti Sway Bar Mounts
ktm replied to 260DET's topic in Brakes, Wheels, Suspension and Chassis
I had a local shop weld reinforcing gussets I had Baddogparts custom fabricate based on his original design. Instead of an angle plate, mine is more of a C-channel that slips over the top and bottom of the rail. I had the shop cut open the rail and insert steel tubing before welding on the gusset. They then rosiette weldd the plate to the rail. -
Wheel Show! Post your pics of you wheels
ktm replied to k3werra's topic in Brakes, Wheels, Suspension and Chassis
Old wheels - still in garage with 95% tread left "New" wheels - I just added 3-spoke knock-offs/spinners. Thinking about painting/powdercoating the wheels flat charcoal dark grey and leaving the spinners chromed along with the lugs. -
Go to Autozone. You can borrow them for free - sort of. You pay a deposit, use the item at your leisure, return them and get your deposit back. I've done it myself a few times.
-
Found On Ebay 240z L28et Hybrid Downpipe Worth Buying?
ktm replied to REISHOKIN240Z's topic in Nissan L6 Forum
The $500+ is for aluminized pipe, Vildini's quote is for aluminized pipe, stainless is more. Stainless bends are PRICEY, as Wizardblack attests to. -
Found On Ebay 240z L28et Hybrid Downpipe Worth Buying?
ktm replied to REISHOKIN240Z's topic in Nissan L6 Forum
Ok, someone tell me what magical place they are having $300 custom fabricated, mandrel bent 3-in. exhausts made? I can tell you that after visiting 5 reputable shops in Orange County, CA, the CHEAPEST I could find was Vildini Motorsports at $400. Their price did NOT include the muffler. Every other place wanted anywhere from $500 to $700 without the muffler. -
Wow. VERY nice photos demonstrating the problem. I know I switched BACK to urethane from a solid mount (did not drive with it, only mounted it), after doing hours and hours of reading. I agree with Pop.