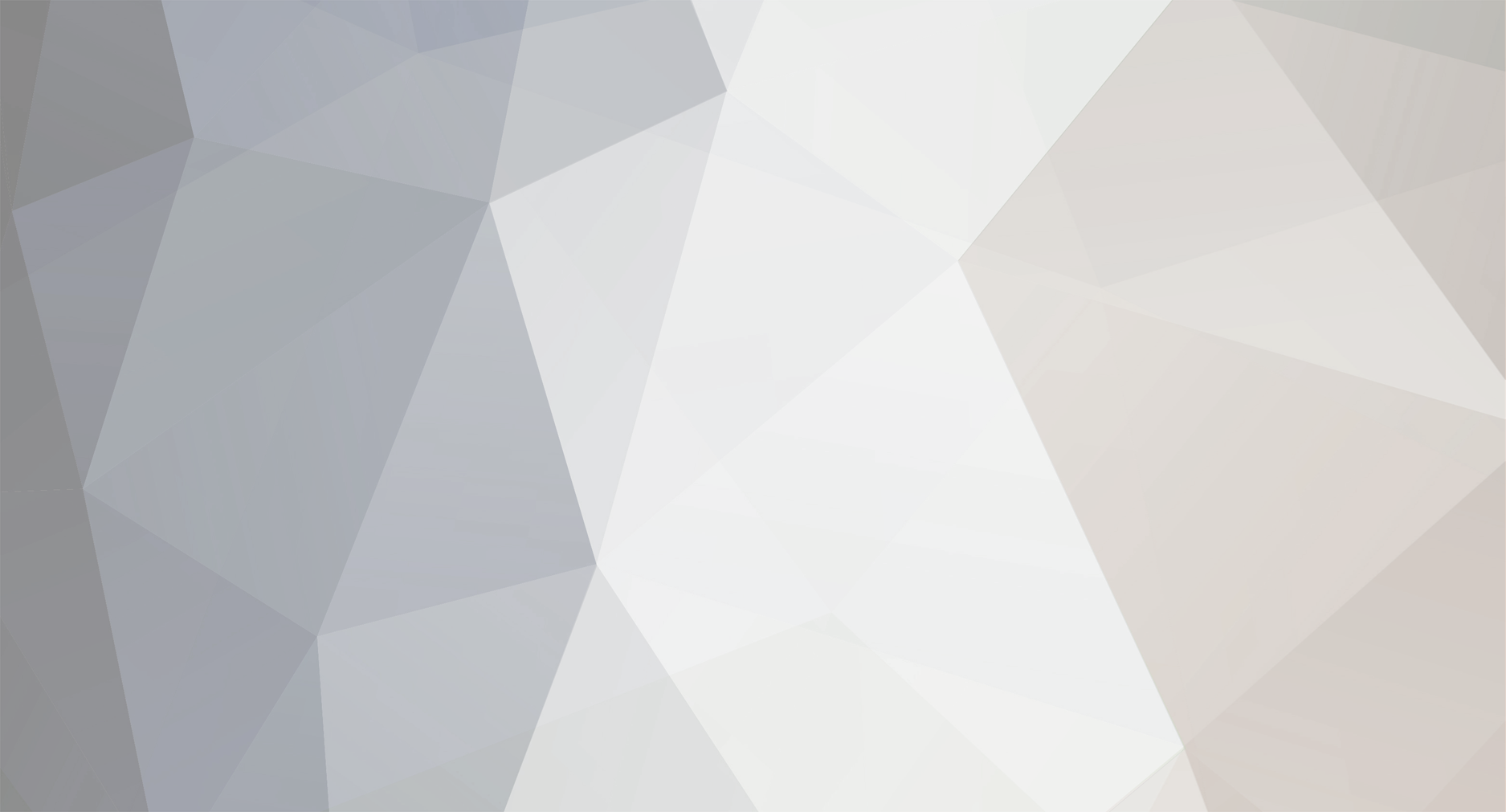
AydinZ71
Members-
Posts
1073 -
Joined
-
Last visited
-
Days Won
27
Content Type
Profiles
Forums
Blogs
Events
Gallery
Downloads
Store
Everything posted by AydinZ71
-
I blew up my kid's 240.....sorta
AydinZ71 replied to jvandyke's topic in Gen I & II Chevy V8 Tech Board
I have never tried what @NewZed suggested by lifting the car and running through the gears, but he has a lot of experience. I was always too chicken to try that, but with 2 people you will find the problem in no time. The R180 was going to break with a SBC. I looked up a ZZ4 crate motor and it looks like you have around 405ft-lbs of torque! Even at 300, the r180 would be suspect. there is one other option... if y’all want to go big. @Invincibleextremes sells a kit for dropping in a mustang super 8.8 diff. His total kit is less than $1500 and you can use an off-the-shelf mustang GT diff. Just an idea. -
240z SCCA vintage race car, restoration
AydinZ71 replied to AydinZ71's topic in S30 Series - 240z, 260z, 280z
Thanks a bunch!! I will 100% do it this way . Il snap some pics for the community. I got the assemblies off the car yesterday but naturally I forgot to pick up a pipe wrench for the darn gland nut. Borrowing tools never works when you think it’s “one and done” haha. good call on the hose clamps. Without that tip I would have probably tacked them on. -
I blew up my kid's 240.....sorta
AydinZ71 replied to jvandyke's topic in Gen I & II Chevy V8 Tech Board
how much torque is your V8 pulling? Just remember, torque is what breaks things on a drivetrain. I would avoid the Subaru unit. It is also an R180. The LSD in there will make launching fun but even more traction means even more things breaking LOL. I’d go with the R200 open if you don’t mind peeling out in low gears. The cheapest LSD options that are worthwhile on an R200 start at around $1k, and still require some assembly. Meanwhile, I sold my open R200 recently (with axle shafts) for $350 recently. also, search “technoversions 240z” in a browser and pick up a top-mount for the diff. About 130 bucks but you can get Rid of that lower front diff mount altogether. You can keep the cables as a souvenir -
240z SCCA vintage race car, restoration
AydinZ71 replied to AydinZ71's topic in S30 Series - 240z, 260z, 280z
Yep! I am super glad I kept the old lower perches with about 3" of tube each. I'll lop 1/2" off each side to get them square and to an even 2" a piece. My technique (worked the first time) was to wrap the koni in tin foil and gently shove it into the tube. The foil does 2 things... 1) acts like a "bushing", centering the strut in the tube and providing resistance to the "loose" tube section from pivoting off-axis (falling out of concentricity). 2) acts as a heat shield while I tack four equidistant spots onto the seam, leaving a 1/32" gap. The tacks hold it concentric. Then I pull out the shock and finish the weld. voila! Trick is not to penetrate too deep with the weld or you will get interference when you drop the strut back in. @calZ Thank you! I already had these guys sand blaster, painted, and the lower perch welded so I will give this a shot. I may reach out to you if I screw this up, and you still have them available? -
240z SCCA vintage race car, restoration
AydinZ71 replied to AydinZ71's topic in S30 Series - 240z, 260z, 280z
@Noll @clarkspeed My issue was I used intuition instead of the write-ups. I followed the instructions from GC correctly (which they confirmed), but I neglected to realize the Koni insert is much shorter than OEM. So when I sectioned the struts, I just slid the insert in just cut the strut tube to the right length. I figured as long as the gland nut ended up with 50-90% thread engagement, the precise length of the tube was irrelevant. This approach would have worked just fine, had I put in the 2" spacer in the bottom of the tube. (DOH!) I read the posts that were available but obviously missed the 2" spacer in the bottom of the tube. I think it was one of those "I don't understand, so I'l gloss past it" moments. This was my first experience with any suspension adjustment at all, so even the terms were new to me. At lease I know its fixable! Going to add 2" of strut tube back, just below the gland nut threads. YEP! I just found that post a few hours ago. I didn't have the balls to drive the car with it clearly not having enough droop. At least I caught my mistake Still its going to be a pain in the ass to add material to the strut tube. It looks like I do have 2" of material from what I cut to add-back. THANKS AGAIN FOR ALL YOUR HELP GUYS! the community is great. -
I blew up my kid's 240.....sorta
AydinZ71 replied to jvandyke's topic in Gen I & II Chevy V8 Tech Board
looks like an R180, but it’s hard to tell from this angle. They don’t handle much torque, so if it is the diff I would replace it with an R200. Plenty of posts on here about that. First, confirm it’s not the engine, flywheel or clutch. If you hear the noise when you rev the engine in neutral, it’s not the drivetrain. If the noise is 100% dependent on the cars speed and on/off throttle just makes it worse, it’s downstream of your engine. next, feel for play. It could be your trans, driveshaft, diff, or axle shafts. If it’s the driveshaft or axle shafts, you will notice obvious looseness (play) in those U-joints when you try to turn them by hand. diff: turn the axle shafts and driveshaft by hand with the car in neutral and on off the ground. If the diff makes a clunking noise when you turn any of those shafts, the diff is toast. The most likely failure in the Nissan diff in my experience are the spider gears. They are really loud when damaged, especially on engine braking. The spider gears won’t usually add much play when you turn the driveshaft, but you will hear/feel it if the car is in gear and you turn one of the wheels off the ground. If the play is felt on the driveshaft side of the diff, then it’s likely your ring/pinion gear. it could also be your front diff mount. Lots of torque often pulls up on this mount and eventually comes loose. Happened to me, and there is a product out now that solves this by converting to a top-mount. it is unlikely to be your trans since that will make an obvious whining or grinding, and not a loud thud like you described. Also, it would be right next to you since the trans is literally 6” from your calf. I have blown everything except for a trans in my 240z career. -
240z SCCA vintage race car, restoration
AydinZ71 replied to AydinZ71's topic in S30 Series - 240z, 260z, 280z
Gosh this is strange... So I called Ground Control and sent them pictures. They said the 7" dimension I am showing is from the bottom of the strut tube to the spring perch is correct. They are telling me the shock is too short... However, the 8310-1437's seem to be used by a lot of folks, so I am still lost what I did wrong. Was I supposed to drop a spacer in the bottom of the stock tube to prop up the shock by a few inches? I threw a wheel on there, and it sits pretty high up even with the shock extended fully. Im thinking about propping up the shock by 1.5", and adding 1.5" of strut tube back. -
240z SCCA vintage race car, restoration
AydinZ71 replied to AydinZ71's topic in S30 Series - 240z, 260z, 280z
I think I found the bust. The GC instructions seem to be for a 10” free-length spring (see attached) Mine are 8”. The adjustable sleeve is 6” long. With that in mind, I’m leaning on the side of not needing to get shorter springs. -
240z SCCA vintage race car, restoration
AydinZ71 replied to AydinZ71's topic in S30 Series - 240z, 260z, 280z
Just checked, and they are 8" springs. Rear's are 300lb, fronts are 350. The strut is sitting pretty high at the moment (control arms nearly level), so I will put some wheels on just to check ride height. If I understand correctly, the overall height of the assembled strut is ultimately set by the height of the shock? I am using 8310-1437's all around. The spring is snug in top spring perch, so lowering the adjuster anymore will just unseat the spring under no load. A little irritated at the moment since I provided GC all my specs so not sure what went wrong. I am a total suspension newbie, so il chalk this up to experience. Fingers crossed my only problem is the 1.5" of collar rising above the gland nut, since that is pretty easy to solve. Otherwise, I'm more worries about the combination of the shock length with an 8" spring. As you said, if it sits too high now I need to go with a shorter spring (damn). Diff is in, so il add some weight to the trunk to simulate fuel and axles. Still, brakes, steering is all apart so not sure how to release the pre-load pressure (in the direction of camber) on the tires so she will sit higher when I lower her in the garage then she will after a drive. thanks again for all your help! EDIT: threw a wheel on and snapped a pic before I put on the ground. -
240z SCCA vintage race car, restoration
AydinZ71 replied to AydinZ71's topic in S30 Series - 240z, 260z, 280z
I just measured and the adjustment sleeve sits almost exactly 1.5” above the top of the strut gland. Il pull the sleeves off and cut that amount off the sleeve. Bummer GC’s dimensions are off. Now I know to consider the length of the sleeve, and not just follow their measurement for the perch -
240z SCCA vintage race car, restoration
AydinZ71 replied to AydinZ71's topic in S30 Series - 240z, 260z, 280z
Unfortunately, I followed the directions from GC which called for the perch to be 7” from the bottom of the strut tube for the rears front call for 10” I wonder if anyone else has had this issue with the GC weld-on kit. I might e-mail GC just to check if I did something wrong. Otherwise, I agree the solution would be to cut the AL sleeve. Too bad I can’t do it on the car 😂 -
Reviving this thread for a specific application. My L24 head is currently down to 38.5cc’s, yielding a 10:1cr with a 1mm crushed felpro gasket. Machine shop advised the cam tower shim and lash pad correction is nearing its limits. Only options I see to safely up the CR from 10 to the production max spec of 12, is domed pistons or weld-in AL into the chambers. Given the complexity and labor of the later, Im looking at domed. I need a quick sanity check. Race gas is a trip for me, and obviously expensive. Assuming I go domed pistons, I’d like to swap out gasket thicknesses so I can alternate between pump (10:1) and race gas (12:1). This way, I can get more time on the car tuning my suspension etc. without burning though expensive hard to find fuel. Already seems a bit impractical since my math says I need to go from a 1mm to a 3mm gasket (unless I target a lower CR on the domed pistons) am I just way off base? Should I just get a spare L24/28 to for testing/tuning instead?
-
240z SCCA vintage race car, restoration
AydinZ71 replied to AydinZ71's topic in S30 Series - 240z, 260z, 280z
yeah I was looking at that and a bit confused as well. Of course, I have not adjusted the ride height at all yet, just got them in. I adjusted the perch until the spring fit snuggly into the top mount. Il throw some wheels on and adjust the height before I cut the sleeve, but I agree it looks like they would need to be cut. I wonder if anyone else experienced this and needed to cut the sleeves. Il also double check that the sleeves for the front are the same length as for the back. -
240z SCCA vintage race car, restoration
AydinZ71 replied to AydinZ71's topic in S30 Series - 240z, 260z, 280z
thanks! Gosh I’m not sure how to adjust the res of the photo’s uploaded here. I can try e-mailing them to myself and uploaded from a computer instead of from my phone. The pictures themselves are huge files on the iPhone. Here is a vid I posted on IG today. Got my rear suspension in thanks to the helpful folks here at HybridZ @JMortensen, @jhm, @Ben280 And more IMG_5985.MP4 -
I run SDS so I don’t know how to tune mega squirt. I can give you some broad tips. first, get it idling. Try to tune for ignition timing before worrying about AF. Are you using a timing light to ensure the what the computer “thinks” is your timing matches what you are seeing at the crank pulley? If not, adjust to factory specs with the light, and set that as your new baseline on your tuner. Ignition advance is needed on throttle input (TPS or MAP), and higher rpm’s. If you eliminate the advance all together, it will just run inefficiently and with poor response. Point being, go safe on ignition first so you can confirm that’s not your problem. If you advance beyond a certain range, the engine will die so keep your advances incremental On the AF, you will be adding a little more fuel per RPM from idle up to about 3000rpm. What I mean is, 2000 rpm will need a little more than double the fuel of 1000rpm. Above 3000, your rpm/fuel relationship should be more linear. This is because the engine’s volumetric efficiency peaks and stays pretty steady after 2500-3000 rpm on a stock cam. the relationship between how much fuel you need per vacuum or boost is dependent on your MAP sensor. This should be pretty linear, or the base mapping from your EFI should be OK. so back to my original point, get it to run OK at idle, then work from there. This is how I tuned my L28et before I put it on the dyno.
-
@HuD 91gt looks like you have some decent work on your head, but I think your EFI needs some work. When you say platinum sport ECU, is that an independent EFI system or a plug-and-play into the existing harness?
-
unbolt the cover and read the stamp on the ring gear (that giant circular gear). That will give you the ratio. OEM S30 diffs are sold as either an R180 or R200, and a gear ratio. You have an R200. You can’t tell the ratio unless you unbolt the cover or count the number of turns manually. It will likely be a open 3.545. people who are willing to pay top dollar will need to know the ratio.
-
it’s famous. Someone willing to spend 1k for it will know
-
Thanks! 1.5X diameter seems pretty conservative for a link that in theory should not be experiencing cantilevered bending forces. Both ends of the link should be free to move, but I suppose we are planning for the “upset” conditions like running over a blown tire. I agree with you. I checked for seven threads of engagement, but since the threads are fine I’m going to pull them off and measure what that comes out to in length. I might go with 1X or 1.2X the diameter (especially given it is fine threaded). The retaining/locking nut further supports the bolt and limits bending forces from reaching the engaged threads (keeping them in uniform tension).
-
+1 with @JMortensen General note, you can not rely of the casting numbers. My 17’ R180 Subaru diff has the same giant “K” emboss as the one on my 70’s era 4.11. You hear a lot of rumors that these numbers mean this and that. The casting numbers mean nothing to anyone except the engineers at Hitachi, and they didn’t share.
-
Have you looked at these guys? https://kfvintagejdm.com I have seen some folks on IG using them, and have not seen any complaints. If I buy new panels for the street Z, I think il give them a try. I can tell their floor pans seem to actually account for the tunnel contours, which is the first I have seen so far. I had to hammer and cut mine to hell (zedfindings), to make them work.
-
this is awesome! Thank you! Totally clear now. I disassembled the joints so I see what you mean by doing the rear one off-car (the joint needs to spin w/o the 5/8 bolt, since it’s not a turnbuckle). Il adjust the toe turnbuckle on the car il do some searching on ways to set my own alignment. @jhm suggested I could do this, since I’m the past I thought a shop was the only solution.
-
@Ben280 very helpful as always Ben! so if I understand correctly, if I want to maximize track width I would run out the bolt/nut just below both (fore and aft) heim joints to the max (leave at least 5 threads engaged). I would check that the spindle bolt is parallel with the ground, which would be a neutral toe. any recommendations on how to adjust the camber plate? If I understand correctly, I should be aiming for about 2 degrees if negative camber. The further out the control arm is, the further out the camber plate needs to go to maintain camber. So for maximum negative camber (just for the sake of argument), the camber plate would be shifted towards the centerline of the car, while the control arm would be adjusted to its maximum length.
-
Very clean paint job