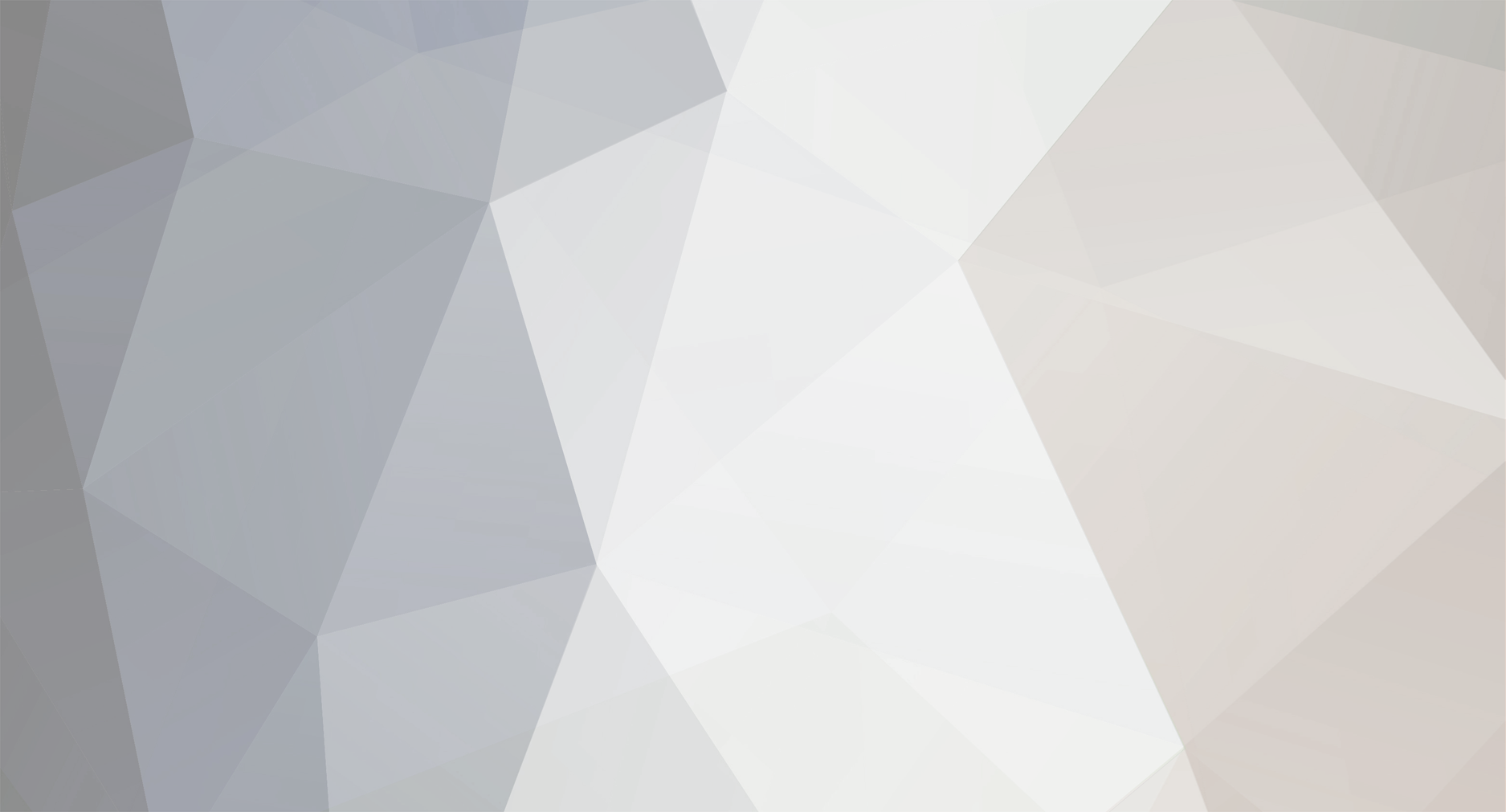
WizardBlack
Donating Members-
Posts
1444 -
Joined
-
Last visited
-
Days Won
2
Content Type
Profiles
Forums
Blogs
Events
Gallery
Downloads
Store
Everything posted by WizardBlack
-
Best undercarriage sound deadening remover
WizardBlack replied to g00kb0i's topic in Brakes, Wheels, Suspension and Chassis
Make sure you wear gloves and eye protection. That stuff will eat into your skin and make it burn like fire for a couple hours. You definitely don't want it in your eyes. -
It could be a rubber/silicone fitting with a leak or crack in it that is pushed open by boost. Those kinds of leaks can make some wicked noises. How about a pressure test of the intake tract?
-
I did as well, actually. I didn't really think about the warmup thing, but it does that too. Click my project car in my sig and you can see some pics of my own install.
-
Take your AFM apart and make sure it isn't stuck.
-
This is technical, not WTB. Try google, even. No need to specifically target freshalloy, zilvia, elitejdm, etc. etc. There's an entire market for this. C'mon.
-
who's got the highest output HY powered L series?
WizardBlack replied to Slow_Old_Car's topic in Nissan L6 Forum
Cam? Headwork? C'mon list all the basic details. -
Are you sure it's detonation that you're hearing?
-
WizardBlack's '77 280Z 'street' car
WizardBlack replied to WizardBlack's topic in S30 Series - 240z, 260z, 280z
Just as a quickie, I should mention that I finally got the welded diff out of the car. The PO had installed this; intended to autocross with it that way. Anyways, it would howl like a purpose built race tranny with straight cut gears. The inside was covered with bearing/race material like someone scooped up a handful off the floor of a machine shop and tossed it in before buttoning up the cover. The replacement is just an open diff of the same ratio, but it's blessedly quiet. Many thanks to Seppi72 (a fellow HZ'er and recent addition to the group) local to me who had one sitting about. Well, actually he had three and a Nissan gasket to go with it, etc. Plus two of his own Datsuns and a ton of other stuff. Check out his details. Long, long time Datsun enthusiast. I scrubbed the diff with a wire brush and then painted it with black engine paint. All the other suspension stuff has been lightly scrubbed for rust, etched with acid and then painted with POR15. You can literally beat two pieces together like cymbals and it won't even mar the surface. It's slick, too, so it rejects dust and dirt fairly well. They're a bit dirty in the pics and have antiseize all over them in places from installs. (that stuff gets everywhere) The diff will work until I get around to mounts for the Q45 diff and halfshaft setup I have waiting to go in. In the meantime, plenty of other stuff to work on. -
Did you get a console? I have a black '77 console that I think is good...
-
Wow, impressively clean.
-
Good to know. I've been thinking of going this route once I am ready.
-
Looks like a Factory Five Type 65 Coupe. I was pretty close to doing one of those, actually.
-
The OP's pic has them mounted right onto the door skins and they appear a tad smaller, but yeah. It looks similar to mirrors I've seen for other cars by jap body kit manufacturers. I wonder if they simply saw something that worked close and went with it.
-
Megasquirt and a MAP sensor.
-
WizardBlack's '77 280Z 'street' car
WizardBlack replied to WizardBlack's topic in S30 Series - 240z, 260z, 280z
OK, no pics on this one; just a summary. I got the car back together. First thing I did was break the cam in (idle high at 2krpm for 10~15 minutes). After driving it around, I realize that since I can now spin to 7k rpm, it is boost creeping really bad. I installed the wastegate actuator with the arm loose. This would set the base boost pressure as low as possible (spring pressure). I have a modified HKS SR20 adjustable wastegate actuator, so it's set for about 7 psi. By the time I hit 5k rpm, it is sweeping past 10 psi and at 6k rpm, it is on it's way to 20 psi. I have ported the Holset HE351 fairly decently. I think the HKS wastegate actuator is designed for a shorter stroke than the holset wastegate actuator (which has a base pressure above 20 psi, IIRC, so no one uses it). Having seen quite a few T3 turbos, etc., I believe the pivot arm on the wastegate flapper is longer on the Holset; thus requiring a longer stroke on the actuator to open the flapper fully. Because of this, at full stroke, the HKS actuator doesn't open the wastegate flapper enough; thus causing boost creep. I suspect others might be dealing with the same thing to some degree. Anyways, the car is pretty quick. It idles at 160* F now with the cooling mods and never really goes past 185. I consider it quick even though it essentially doesn't hit much boost until 5k, plus the fact that it completely misses the powerband of the intake manifold and stock head since I haven't intentionally forced it to spool beyond 7 psi, plus the fact that the EDIS sensor was 6+ degrees retarded. I never got around to re-setting it after disassembly/reassembly until today. I haven't driven it yet because I am trying to come up with a solution for the wastegate issue. I have Cam2 in the car, but haven't pushed timing or air/fuel ratios for octane beyond pump gas. I am merely using it as a safety factor until I decide if I want to switch off of pump gas. I feel 20 psi is safe for pump gas on the L-series if it's been modified (knock resistance) and tuned properly. I also adjusted the cold and hot start pulsewidths. To anyone using Megasquirt, beware that any basemap you borrow is very dependent upon the injector size. I am using 560 cc injectors. Since all cold start, hot start and priming values are explicit pulsewidths, they don't scale based on your primary map or by your basic fuel injector settings. My car was practically (well it was, actually) flooding itself on hot starts. I would use flood clear to get it going. Bah, too many things to adjust for the time I have. LOL. So right now, I am going to tighten the wastegate so it'll spool to 15~20 psi and run the #*#$ out of it for a little while and enjoy it while I tinker with other minor projects on the car. Next things I am considering: #1 - Fender Flairs (my wide wheels and tires rub on the quarter panels REALLY bad with any slight bump) Aluminum Door Panels covered in Alcantara to match the dash Installing a Kirkey passenger seat to match the driver's seat In-car inverter for the laptop Adjustable suspension mods to get toe, camber, etc. under control -
WizardBlack's '77 280Z 'street' car
WizardBlack replied to WizardBlack's topic in S30 Series - 240z, 260z, 280z
Since I never really identified my ignition system very well, I took some pics of this. Keep in mind that I did not make these brackets. I bought the EDIS trigger system that BRAAP had on his yellow race car. He machined the crank trigger sensor brackets out of aluminum. They feature full adjustment for sensor to wheel gap and for about 30 degrees of timing adjustment. I bought a new EDIS-6 trigger wheel and sent the wheel and my crank pulley to him to have it installed. He machined the second v-groove down, pressed the EDIS wheel on and then drilled and tapped for three screws right at the seam for additional support. This eliminates the possibility of the wheel spinning on the pulley. Neither the bolts nor my dual electric fans interfere with the sensor whatsoever. I installed the system, configured the Megasquirt in the pulldown for EDIS and it fired right up and I haven't looked back. I've spun it past 7k. This system requires you to relocate the alternator. I used a GM 1-wire alternator and mounted it on the driver's side. It doesn't interfere with my Holset turbo or K&N crank breather. I apologize, I didn't get pics of the VR sensor mount. I will try to do that later. -
WizardBlack's '77 280Z 'street' car
WizardBlack replied to WizardBlack's topic in S30 Series - 240z, 260z, 280z
Having read through the head cooling mod sticky thread several times, I decided to give it a go and add some coolant circuits. The gist of the situation is that the coolant flows into the head on the passenger side at the very rear (for the most part). The coolant can flow around the combustion chambers, but because of rough casting in tight spots and the fact that the passenger side is pretty open, it flows mostly on the passenger side and never flows laterally across the combustion chambers until it gets about halfway. The coolant exit is, obviously, the thermostat housing on the driver's side. This leaves cylinders 5 and 6 with relatively poor coolant crossflow. The idea is to drill into the coolant jackets, install an AN outlet, and route them to an appropriate location to draw coolant across these two cylinders. Given that 6 is on the end and therefore cools more from ambient air, 5 is the cylinder targeted for the heaviest flow. I routed 5 to the water pump inlet for a large amount of pressure difference. The water pump will literally suck the coolant across the chamber very well. I routed 6 to the thermostat housing. This still provides some flow, but not as much as 5. Aside from the "flow balancing" to match to proposed amount of cooling deficiency, you don't want too many circuits routed to the water pump inlet or you will bypass the radiator and thermostat to a large degree. Shown in the images is the location of the AN taps, the fittings on the thermostat housing and water pump inlet neck, routing of the lines, etc. I used push-lok hose instead of stainless braided line. For the holes in the head, there are two circle-shaped dimples cast into the head. I drilled my pilot holes about halfway between the very center of the circle and the bottom of the circle. Having peeked into the jackets, I feel these are at a good level. Please note that these lines make it harder to bleed all the air from your cooling system. I was careful to try to keep the cooling lines as low as possible, but there's only so much you can do with these lines. I use one of these to fill and bleed my cars. They are pretty much mandatory on some cars, like Subaru's. They basically install onto the top of the radiator, form a seal and act like an extra 12" on the height of the radiator. You run the car with it installed until the thermostat opens and you see all the bubbles stop coming up. You can keep the car running with it with no problems (just keep a level of coolant in it). All air will bubble out automatically and when the thermostat opens, it will suck quite a bit out. When you are done, the included rod pokes down into the funnel and plugs the neck so you can the whole thing out with the funnel still full of coolant. With these coolant lines, be sure to jiggle them vigorously to get air to come out, too. Likewise, I reach down and grab both coolant hoses, one in each hand. I slowly squeeze one all the way and then as I release that one, I squeeze the other one. Doing this back and forth causes the coolant to flow back and forth and dislodge air bubbles stuck anywhere in the system. Keep doing all this until you can't get anymore bubbles to come out. I do this before I ever start the car. -
WizardBlack's '77 280Z 'street' car
WizardBlack replied to WizardBlack's topic in S30 Series - 240z, 260z, 280z
Following that, I reassembled the head and looked around for what else I could mess with while I have it apart. I decided to do something about the detonation and head issues with the L-series to the best of my own abilities. After having the head machined flat at a local shop, Fowler Engines, it came back with a .010" shave. This bumped the compression ratio to about 8.63:1. I went through and bumped all the sharp edges with a 3M rolloc disk to reduce heat transfer (ie., detonation prone) spots on the combustion chambers. Likewise, I went through and tapered the throats out where the head had been cut for the valve seats but not transitioned into the runner properly. It had a large ridge all the way around; as much as 1.5mm in spots right after the hardened valve seats. I have an N47 head with the exhaust liners. To describe this area in more detail, if you imagine them installing valve seats in a new head, they machine a cutout in the raw head casting to press the seats into. Just past this, the diameter of the aluminum should be machined out to the diameter of the upstream end of the seat for a nice transition, but mine were not. It made for a nice step to disturb airflow. Just past this spot, it opens up again and starts the turn to the main portion of the runner. I made sure to carefully blend my work into both the valve seat and the short side radius. I wanted it improved, but I was careful to quit while I was ahead. Having done this, it was time to install the cam and cam towers. I could not use a pry bar to compress the valve springs to install the rockers, so I installed the cam and cam towers with the rockers in place. As I do this, it will compress some of the valve springs, so I very carefully alternated cam tower bolts to work it down. I will say, however, that I didn't follow the order in the manuals, but rather focused on the bolts in a cam tower on either side of a lobe that will bring a valve off of it's seat. Those are the ones under tension, so I worked those down carefully and went back every so much and made sure the "slack towers" were keeping up. With this installed, I decided it was time to focus on some coolant flow mods... -
WizardBlack's '77 280Z 'street' car
WizardBlack replied to WizardBlack's topic in S30 Series - 240z, 260z, 280z
After taking the head off, I realized the valve stems seals were shot, the valves were carbon-ed up, the springs were weak, etc. I decided to buy a set of Isky springs and retainers. The catch is, the Isky retainers are only used with a reduced base circle cam (ie., a reground cam). Well, shoot.... Time for a cam. I send my cam out and had them grind it. I went with the standard turbo cam; .490/.480 lift with 290/280 duration and a 114 degree lobe separation angle. I manually resurfaced my rockers enough to remove the oil varnish by wiping them face down on a piece of wet/dry 1500 grit sandpaper that was placed on a hard, flat surface. I lubed the paper with WD40 or PB Blaster heavily and changed spots frequently. Likewise, I counted the number of swipes and repeated with all rockers the same number of times. Using the new, thicker lash pads that I also got from them (.175" thick), I attained the wipe pattern shown. After discussing it in this thread, I decided to keep them pretty aggressive. Note that I used Permatex Ultra Slick for the assembly lube. This stuff sticks in place very well. -
The brass pieces are for a banjo fitting; what the 044 pump was originally intended for. They are not designed to seal, AFAIK. You need something like you would for a turbo oil inlet where it has a crush washer for the actual seal. Put a copper crush washer on your inlet fitting and that should work for that side. A similar thing for the other and you should be fine. I can dig my 044 out (still sitting on a shelf ATM) to look at it, too. EDIT: Using an ORB AN fitting would work, too, I suppose.
-
I think the simple answer they're kicking your way is that doing that would add more complexity to the behaviour of the cooling system. Besides, there really isn't much of a place to tap the line into on the upper. The lower is a nice block of aluminum with (typically) one or more unused threaded ports. Getting all the coolant flow back together before it hits the coolant temp sensors in the lower is probably a wise idea as well. As an update, in 70 degree weather, my car idles pegged at 160 steady. I had yet to dial in the EDIS sensor after reassembly and realized it was about 6~7 degrees retarded which didn't help with engine bay heat before.
-
Looks great! Very clean. Unfortunately, I'm a speed nut so your audio install reads like this to me: Btw, this thread is old. I've since gone to excess weight components in the doors, with an excess weight powered the excess weight. Then I also have a excess weight with 1 excess weight and another excess weight. Perfect size for the wheel well. With this setup now it finally has enough bass and it BUMPS! The excess weight in the doors were simply overpowered by the excess weight. BTW, Mitsubishi sells pedal covers for their EVO's which are anodized aluminum with embedded rubber nubs. They install the same way and are reasonably cheap. You can get them in blue, red or silver, IIRC.
-
LOL, I will order pizza and break out the beers. I guess I am joining your cheering section. I'm in Ohio so I can't help you directly...
-
What?