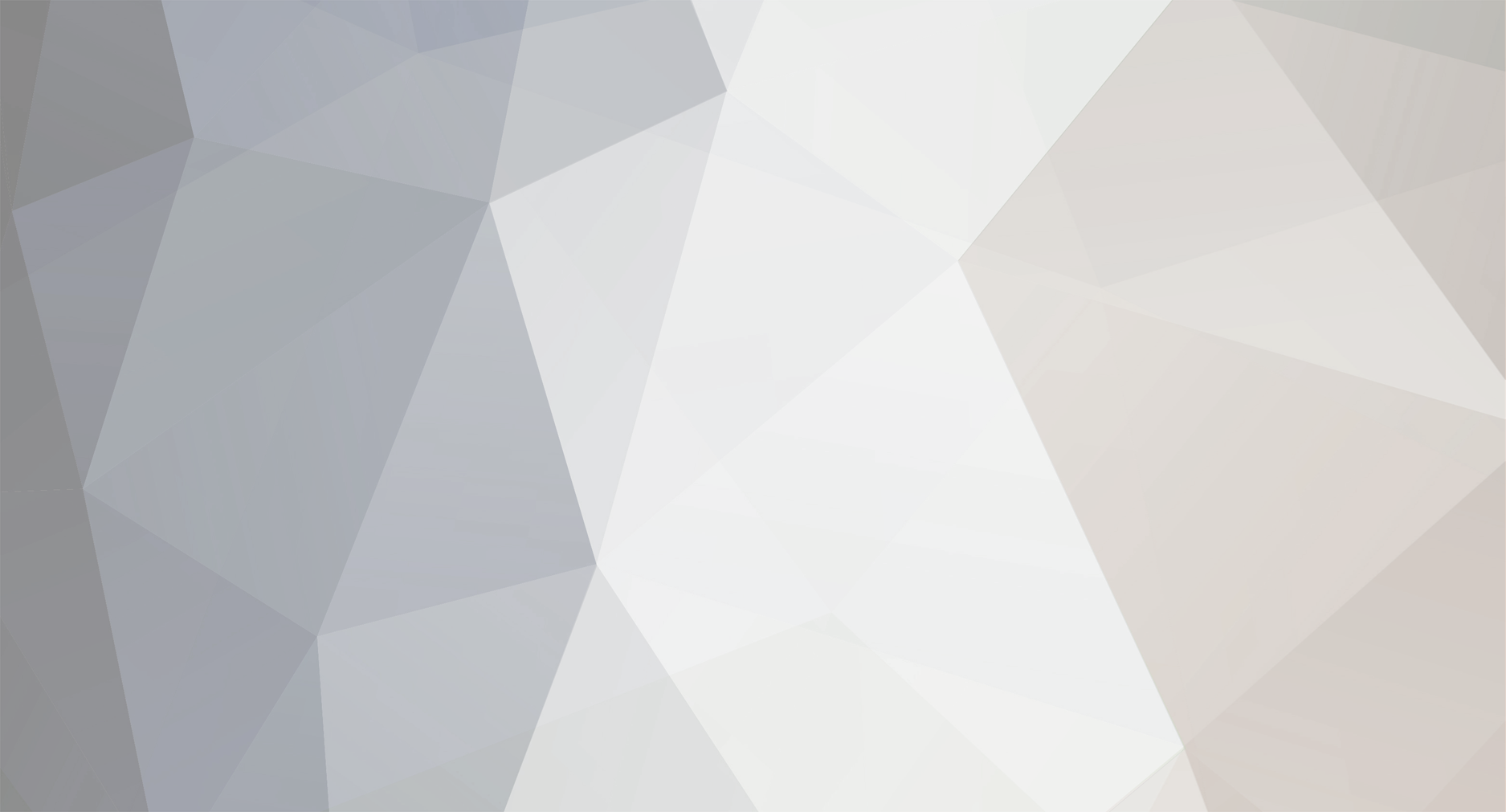
tube80z
Super Moderators-
Posts
1387 -
Joined
-
Last visited
-
Days Won
25
Content Type
Profiles
Forums
Blogs
Events
Gallery
Downloads
Store
Everything posted by tube80z
-
Brake Cooler Testing (i.e. what not to do)
tube80z replied to jrd's topic in Brakes, Wheels, Suspension and Chassis
I ran those for about a year and had similar problems. I found that if you flip the pads each session (or event for an autoxer) and use spacers to keep the pistons from coming out too far it will help. But you can cook the seals. Then there's that issue with how to cool the brakes properly. Cary -
Interesting webpage on tubing sizes/strength
tube80z replied to JMortensen's topic in Fabrication / Welding
Prepare to Win, page 56 Straight Gusset Plate Not too good -- can be improved by flanging long side Shaped Gusset Much better I found some additional papers in seismic bridge design that were interesting to read by I'm not sure how much they align with what we're doing. I will be interested to hear what your friend has to say. I remember many, many moons ago when racing BMX bicycles the frames with the single gusset would break at the end of the guesst. And those with the guessets on the outside of the tube didn't have this failure. Cary -
I know this is commonly stated and may be true. What I do know is that almost all DOM tube that I've seen these days is made from ERW and then has a die ran down it to set the ID. This will cause some work hardenning but I don't know how much stronger that really makes it. Some good hard data would be great. I only have a few simple experiments I did to see if DOM was really any better than ERW and in my case I didn't see any advantage.
-
Attached are a couple more photos to help with the idea. The reinforcement is 2x2x0.120 wall tubing. The rocker was openned at the front and rear the a continuous piece of tube was fitted. In addition they sectioned the inside of the rocker to allow the cage to be hooked directly to it and for better attachement to the car. The idea for this originally came after seeing a competitor get seriously injured at a hillclimb. His car left the road and hit a tree at speed. The cage worked perfectly but the car rolled up onto the rocker, which failed and the this lead to his getting partially crushed. Looking at the wreckage it was pretty clear that is this area were stronger his injuries may have been a lot less. The car belongs to Dave Kipperman and if you happen to be at Shasta you can ask to get a closer look. Dave would be more than willing to show some of the hidden details of this car. Cary
-
airzona z car big piston struts?
tube80z replied to Larryz 260's topic in Brakes, Wheels, Suspension and Chassis
They look like an inverted design, meaning the large shaft is really the shock body like the bilsteins. My guess is the piston is the same size. Cary -
IMHO, you should have taken weight out of the sides, rather than top or bottom. Think I-beam for holding in the cell. Still, it sounds like it's strong enough to me. Cary
-
Chassis reinforcement pics, opinions
tube80z replied to bjhines's topic in Brakes, Wheels, Suspension and Chassis
You mean something like this: I've seen a few of the WC cars setup like this. On my tube car the bars will be done like this but will be out into the door. More of a pyramid shape. Cary -
Chassis reinforcement pics, opinions
tube80z replied to bjhines's topic in Brakes, Wheels, Suspension and Chassis
In my car the roof bracing is 1.5x0.049 tube. You could also use 1x0.065. I stole that idea from a DTM cage design I got pictures of. I've seen in a few other cars as well as a PDF for a NASCAR FEA study. Most of the general non-cage bracing could be 1.5x0.65 and the guesets could be 16 guage. On my car the lower X is 0.065 tube. I use an X brace in the rear hoop along with this to help in side impact. What I have is a little misleading. It would also have the tower braces down to the swaybar mount' date=' which is missing in the pic. The rest of the structure, which would probably be something like 1x0.065 tube would be a bolt in. Yes, it is removable. Take a look at a viper competition coupe and you'll see some of where the inspiration came from. The rest was how to close the large open box teh Z has for an engine bay. I'm not a big fan of tieing into the cowl as most people are. I'd rather hook to the corners of my cage, which I believe would make it all stronger. If you do hook to the cowl I think creating an X with bracing down to the sides of the tunnel where the transmission mounts wouldn't hurt. My old GT/FP car had a tube that ran from the back to the front to brace this area. Perhaps, but it was light and made major improvements in my model. And in my tube car I have no structure here. If you decide to go nuts you could remove a lot of teh structure and let the tube take its place. I have a taxicab bulkhead in my behind the seats. If I was doing a track day unibody car I'd do this to keep the hatch area from becoming a parachute. I had a similar brace on my car that cleared the exhaust. It was removable. If you use a heimed TC rod mount you could box the bottom of the TC area and use this to bolt this brace to. Cary -
Chassis reinforcement pics, opinions
tube80z replied to bjhines's topic in Brakes, Wheels, Suspension and Chassis
Here's a version based on my tube car and what I'd do if I were to build another unibody car. I don't have any fancy FEA analysis this was done the old fashioned way by building a model out of welding wire and looking at where it deformed when twisted. My powerpoint CAD skills are a little lacking. The big changes over your original design are a lower X tieing into the strut towers, an X in the roof also connecting into the strut towers in the rear. In the front there's a lower K member and an X that goes from the sway bar mounts to the strut bar. In my basic models I just had a flat floor. I was only looking for changes in stiffness in the cage figuring anything I did that made this more stiff would translate to a stiffer car. In real world testing hooking the cage into the windshield frame and adding gussets around the windshield frame helped a lot with torsional strength. In my opinion the rockers in a Z are really weak and I'd reinforce these with tubing. This isn't the end all be all by any means. I hope it helps to spark some discussion. Thanks for the photobucket tip Cary -
AZC Billet steering arms
tube80z replied to Clifton's topic in Brakes, Wheels, Suspension and Chassis
510 arms will not bolt to the the Z unless you have ZX strut tubes. The spacing of the bolt holes is off by about 10 mm. 510 arms do have a twist but you could switch them side for side to gain ackerman. The problem is that they are longer than the stock Z arms. So I don't think you'd want to do this. Attached are a few pics of some arms that were built for a race car. These were flame cut from T3 steel plate. Another option for the DIYer. Cary -
Bumpsteer adjustable tie rod ends
tube80z replied to JMortensen's topic in Brakes, Wheels, Suspension and Chassis
Sounds like you have it nailed Jon. For welding the pipe I would clamp it to a section of you TC tubing if you have any left. That should be good enough. Cary -
Large tires killing handling?
tube80z replied to jonzer12's topic in Brakes, Wheels, Suspension and Chassis
I have direct experience with my car and hotter on the inside is what is generally required. How much hotter depends on the tire characteristics and toe can have an effect as well. What you're really looking is to have the tire optimized when cornering, which leads to the higher inner temps when measured at the end of a run. In the Motec seminar Claude shared IR tire temp data that showed surface temps during a lap and you could see this. What we measure is well off what the tire sees. He even showed us examples where we would have done the completely wrong thing based on pyrometer data we'd measure in the pits. It also became pretty damn clear that if you're doing any serious racing or chassis development you must have this level of data or you will be working in the dark. Cary -
Bumpsteer adjustable tie rod ends
tube80z replied to JMortensen's topic in Brakes, Wheels, Suspension and Chassis
Allergies here too. I know this all too well. Some things to think about. Ideally you want the rack to be at the same level as the LCA inner pickup point. If not you'll get some bumpsteer from that. Did it raise a lot more than your pickup points? If you had studs that were in the crossmember you could use spacers under the rack mounts to move it up and down. Along with your slots this would allow for some variability in the front RC. But it may be a little hard to get the rack any lower that you currently have it. You can use a couple of plumb bobs to align the rack and crossmember. I have yet to see a Z that is straight as far as crossmember alignment is concerned. I think it has to do with how old the cars are these days. My bent race car had the crossmember cocked to try and straighten it out. You also need to weld a tab to the mount near the rack pinion. The aluminum appears to be pressed to the tube and I had one that came apart after a lot of use. You can bolt through the tab to the lower ear of the aluminum mount. Or that was the solution I used. You could probably drill a hole and use a set screw into the metal rack housing but that would be more work and the rack would need to come apart. I think you'll have to clearance more of the rack for the tie rod. I had to remove some of the flange on my old car. Be careful you don't have oil pump clearance when moving the rack. I had the motor set back and this was a major issue on my car. Cary -
Diamond Racing Wheels
tube80z replied to christiansagun's topic in Brakes, Wheels, Suspension and Chassis
In general I've found diamond are made much better than some of the other cheap ministock wheels. MRT is one that doesn't have a decent center hole and you'd probably need to use lug mounted balancing. Cary -
Why don't you run in super production, If I were you, I'd look more at the ITE or open IT class as this would be a better match I'd think. You're really jumping into the deep end of the pool. As far as suspension goes take a look at the threads at the top of this section and look for advice from Katman and Johnc. This is assuming you want to keep running struts. Super prodction doesn't put limits on the type of suspension that I'm aware of. So you can do things like double a-arm conversions, etc. Cary
-
In order to use more caster without power steering you need to move the spindle forward on the strut. Increased steering effort is caused by the lever from the actual turn center to the tire's contact patch. You can do a little of this with custom RC/bumpsteer spacers and moving the lower balljoint. Cary
-
Stock Spring Rates
tube80z replied to palauoriginal's topic in Brakes, Wheels, Suspension and Chassis
Don't forget even though the rate is low there is significant preload on the stock springs. Cary -
stiffening frame rails- yay? or nay?
tube80z replied to a topic in Brakes, Wheels, Suspension and Chassis
I wonder if putting an X in the core support would work. I've seen that on a few rally cars. I also wonder if a car setup this way is doing this because the front and rear roll angles are vastly different, causing the chassis to take more of the load. Cary -
Cool dude. So we'll we see it out this year? Cary
-
Bumpsteer adjustable tie rod ends
tube80z replied to JMortensen's topic in Brakes, Wheels, Suspension and Chassis
For a street mod car I'm not sure you can do much with the rack. I guess you could eliminate the bushings and move the rack and possibly pour in some new ones but I'm not sure how much, if anything that would gain. I had thought SM allowed liberal creativity on the outside, as in tubular control arms, custom fabricated strut housings, etc. I would think you could take some advantage with the steering arms and if you used a two piece strut you should be able to set the pin lead on the strut. This would let you experiment with much larger caster angles. I don't know if this will work with low profile street radials or not. Cary -
Bumpsteer adjustable tie rod ends
tube80z replied to JMortensen's topic in Brakes, Wheels, Suspension and Chassis
Coleman lists them in their catalog. I believe they are set for the some of the basic chasis that might be bought. So some custom fab would beed to be done for a datsun version. Cary -
Bumpsteer adjustable tie rod ends
tube80z replied to JMortensen's topic in Brakes, Wheels, Suspension and Chassis
The mount you have above is basically what I've done to my nissan rack. I welded a mount to the rack tube and use that to attach. Very similar in the end. I only chose this route because I had the rack and I'm cheap. For your ackerman adjustment why not build it maxed and then put spacers under it as needed. You'll have to watch the clearance to the oil pan but this should work fine. If you try and lower the car a lot you may have interference issues if you raise the crossmember/inner pickups too much. I still like the idea of doing something like this and have spacers that would allow one to move the crossmember to adjust the roll center. You'd need adjustment like Jon has on for the TC rods but it seems like it would work. For racks you might also take a look at a number of the sand rail companies. They have some low cost options that might work as well. Cary -
The basics are that you want it adjusted so that the bar is straight across when load is applied. When they are not loaded you may see the bar skewed at an angle. Ideally the monoball should be very close to the center for optimum use and safety in the event of a failure of one of the circuits. A properly built system will not let the monoball shift as the car experiences side loads. This is a good think to check as you'd have different brake balance corner to corner if this happens. Cary