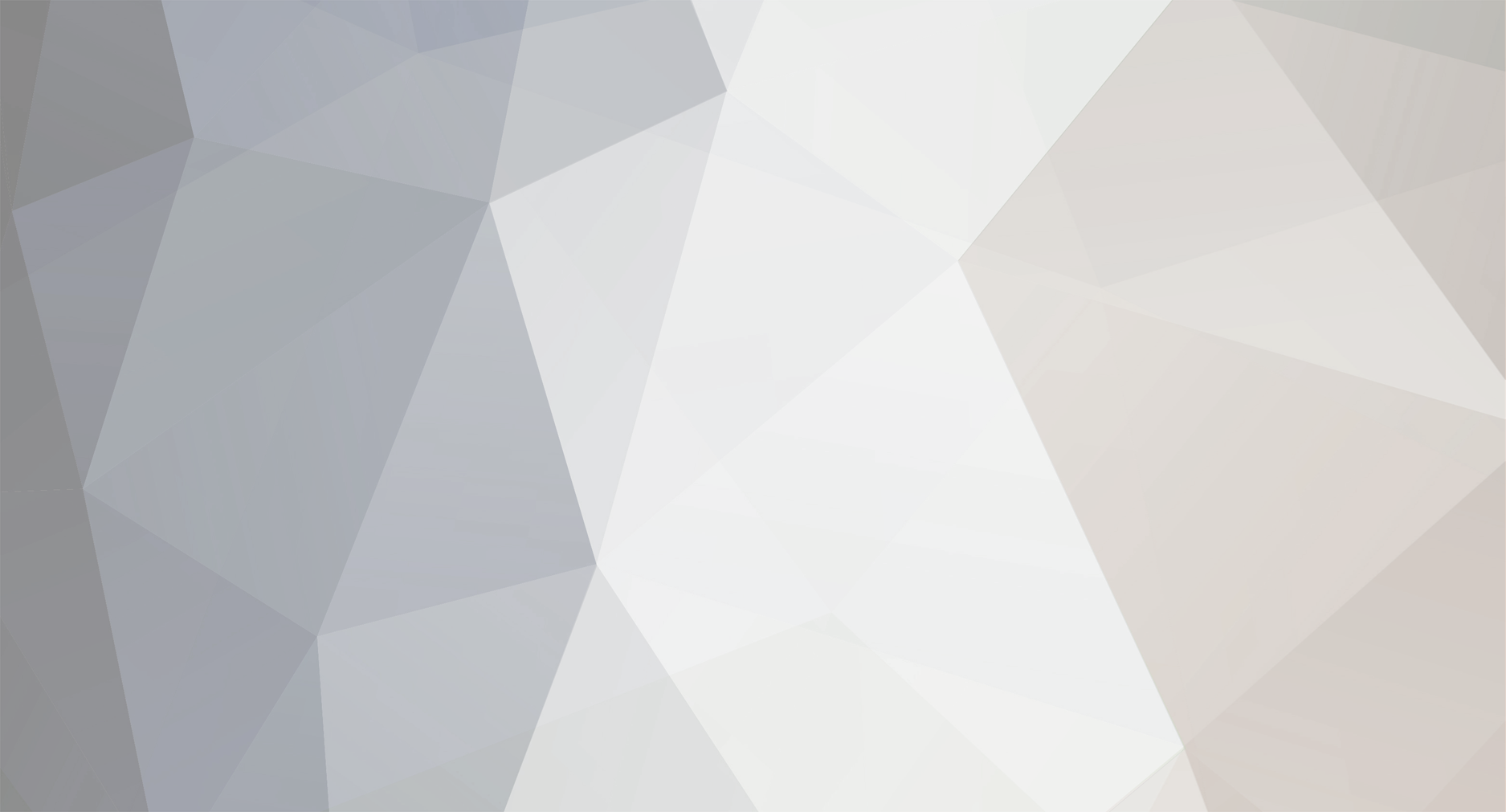
tube80z
Super Moderators-
Posts
1387 -
Joined
-
Last visited
-
Days Won
25
Content Type
Profiles
Forums
Blogs
Events
Gallery
Downloads
Store
Everything posted by tube80z
-
If you think this is harsh you should see corner carvers In the back nothing is usually done. You can only change the angle of the control arms by moving the inner pickup points or the outers. Both require a lot of fabrication that most aren't willing to do. That aside as long as you don't get them past flat you usually won't see any issues. You can adjust the front to make it work with the new rear. It was a definite improvement. As far as setup goes I don't think you'd have anything that different than an autox or track car. I think you really want something that is close to neutral and easy to drive and it will be adjustable anyway. Watching the D1 guys in Fontana a couple of years ago it seemed like they needed to be able to get under their competition and then control the angle as they were very close. Steering may be the area where you'd diverge from the normal thinking. I'm thinking at high slip angles parallel steering would be better than any ackerman. I'm also wondering if fiddle brakes might be something worth looking at as those would likely have more control when you are really sideways. Cary
-
If you think this is harsh you should see corner carvers In the back nothing is usually done. You can only change the angle of the control arms by moving the inner pickup points or the outers. Both require a lot of fabrication that most aren't willing to do. That aside as long as you don't get them past flat you usually won't see any issues. You can adjust the front to make it work with the new rear. It was a definite improvement. As far as setup goes I don't think you'd have anything that different than an autox or track car. I think you really want something that is close to neutral and easy to drive and it will be adjustable anyway. Watching the D1 guys in Fontana a couple of years ago it seemed like they needed to be able to get under their competition and then control the angle as they were very close. Steering may be the area where you'd diverge from the normal thinking. I'm thinking at high slip angles parallel steering would be better than any ackerman. I'm also wondering if fiddle brakes might be something worth looking at as those would likely have more control when you are really sideways. Cary
-
Anyone done away with Strut - Spindle pins?
tube80z replied to gearheadstik's topic in Brakes, Wheels, Suspension and Chassis
To clean out the holes I use a steel brush on the end of a drill. Seems to work and is easy and quick. I usually spray a little WD40 or similar on it to help get the gunk out. The last two I took apart definitely galled in this area. I put them on my lathe and used a file to flatten them down. Then loads of anti-seize as they went back together. I think when people tighten the wedge too much it does this. My race car was put back together with 5/8 bolts. When torqued they don't seem to move at all in the strut housing. I usually inspected them a couple of times a year. No wear issues that I could see. Cary -
Recommendations for AutoX Slicks
tube80z replied to heavy85's topic in Brakes, Wheels, Suspension and Chassis
Formula V works wonders too. Use that when the tires start to go off. Cary -
Recommendations for AutoX Slicks
tube80z replied to heavy85's topic in Brakes, Wheels, Suspension and Chassis
With 13 inch R25As I get two years before they cord. It took a set or two to figure out how to do that. I run two complete sets (8 wheels and tires) and rotate and flip the tires. I have a log that I keep of all running and keep the pairs matched. Yes it's a lot of work to do this but when you have a tight budget it makes all the difference. Typically I run 10 to 12 autoxs and 2 to 3 hillclimbs a year. Proper storage when not in use is important too. Cary -
WOW this would help with making headers or cages....
tube80z replied to 80LS1T's topic in Fabrication / Welding
I don't know about ultimate strength. I've seen fit up with gaps filled on a number of cars and some of those have survived big wrecks. But I can tell you that I did a few basic tests before I started putting my car together. I fit a couple of tubes very well and did a basic torsion test. I fitted some poorly and did the same test. The results for me were that the poor fitup had different torsional strength in one direction versus the other. My guess is that this may have had something to do with the weld wire being stronger/stiffer. I'm not sure. But for my car I tried to get the fitup as good as I could without spending too much time on each tube. Cary -
Dyno with stock damper? I am I taking a risk?
tube80z replied to violacleff's topic in Nissan L6 Forum
Another sign of impending doom is bits of rubber on the hood and inner fenders. I've lost a number of them over the years before moving to better alternatives. And when the bolt gets loose on the front it's a good idea to pull the motor and check the flywheel bolts. You'll sometimes find that those will loosen up too. And vice versa. Cary -
Controversial idea...
tube80z replied to OlderThanMe's topic in Brakes, Wheels, Suspension and Chassis
I don't think increased damping is really the issue for a Z. As far as offroad vehicles go many of the multiple shock installations are to control certain speed ranges. Cary -
The poor man's rear toe-in adjuster
tube80z replied to blueovalz's topic in Brakes, Wheels, Suspension and Chassis
Thanks Jon, that seemed to have jogged the memory. So there's no reason lower cost clevice or solid joints could be used if someone wanted to save more money on this "poor" adjustment. Cary -
The poor man's rear toe-in adjuster
tube80z replied to blueovalz's topic in Brakes, Wheels, Suspension and Chassis
I can't remember why heims were used. Since this slides more or less in a straight line couldn't something solid be used? Did we already discuss that and I'm too stupid to find it? And a trick you may or may not know. If you need really fine adjustment use two different thread pitches rather than left and right threading. Cary -
A DIY way to do this is put paper behind the car and shine a light head on and outline the shadow on the paper. Then add up the area on the paper to see the total area. The basic idea is to see how big a hole you're trying to punch in the air. Cary
-
Jon is right. It's an easy experiment to prove with yarn tuft testing. Cut some pieces and tape it to the hood and see how the air moves with the hood open and closed. I used to think this would help until I watched the yarn go into the engine compartment. On my race car I put holes in the inner fenders in front of the strut tower to allow air to escape. I then added gurney's to my fender flares that could be moved out if I needed more airflow. And in front of the radiator I used a box to help slow the air as it hit the radiator face. Also make sure to use the stock belly pan or add an upgrade. If I wasn't in FP at the time I would have made a duct that came out the hood for the radiator. Louvers in the front section of the hood would probably have a similar effect. Cary
-
I use the Davies Craig with pump controller on my race car. It seems to work as well as the belt driven pump did for me. I don't know how long the pump is rated for continuous duty. It does make wamring up quicker and is nice to circulate the coolant when it's turned off hot. Cary
-
Dual master cylinder sizes with 4 psiton calipers
tube80z replied to a topic in Brakes, Wheels, Suspension and Chassis
If you're brakes are pushed on equally by a rod that goes through the brake pedal you might see if you can get a copy of Race and Rally car sourcebook. In it they have a low buck bias adjuster that would be easy to build. Cary -
I know this isn't a car but had your friend considered something like a 125cc shifter cart? You can haul it around in the back of a pickup or large SUV. Or on a really small trailer like you can get at home depot. A 125cc shifter kart is a serious little ride and the racing is as good as a car. The new TAG 9touch and go) models are easy for one person to deal with and well within this budget. Cary
-
I'm not sure that's really correct. My understanding is that the sub strap is designed to keep the belts low so that the load is spread across the larger bones in your body. If they belts rise then you do nastly things like blow out spleens or worse. From what I've read you really should be using 6-point belts as they do a better job. Mounting for all this is critical and a number of people do it incorrectly and most people don't have the belts tight enough when they are in the car. And if you're running at speed it makes sense to add a head and neck restraint into the equation. And if you have a dedicated track car then you should have a proper seat and it should be mounted correctly. Aluminum seats with bead liners work well. I never used to worry about all this but as I've seen a few wrecks in the last couple of years that could have been far worse. And I'm building a car that will be a lot faster than anything I've ever had before. And when Newton is driving you typically have little input on where you go. Cary
-
Hi Paul, That looks pretty involved. Do you do any flowbench work in conjunction with this? Is this all on a per quote basis or do you have standard rates? Cary
-
Recommendations for AutoX Slicks
tube80z replied to heavy85's topic in Brakes, Wheels, Suspension and Chassis
Their site is http://jbracingtires.net/index.htm Cary -
New pics of damaged 240, How would you proceed?
tube80z replied to a topic in Brakes, Wheels, Suspension and Chassis
Quit stressing -- this is nothing. Take it to a shop and have them pull the corner out and then replace what is mangled too much to fix. If you go somewhere decent they should have the tramming measurements that are needed to verify alignment. I had a car that hit a tree at a hillclimb that had the strut towers pushed back. I fixed it at home, ugly and temporary I might add, and squared it up as best I could. It worked fine and won quite a few races. You don't need another shell. Far worse are fixed all the time. Cary -
I think you're correct. John also provided some good info that I thought was happenning with the rear mustache bar bending. I had a couple of ideas on how to fix this but I never got around to doing them. I was going to use a stock mount (broken) and weld it up solid and have tabs to extended below the crossmember. Then this would be bolted under the crossmember. This was all doable with flat stock, a few pieces of tube, and some bolts. This would spread the load from a sinlge point as well. I do think making a subframe for the back isn't a bad idea as it allows you to keep a lot of bits from flexing and would make the suspension mounting stiffer too. But that's a personal opinion that not everyone shares. The moral of the story is when you start using an old car really hard you need to keep an eye on it and I'm not running a V8. I torqued all bolts before I used the car and replaced them when they started to routinely loosen. Cary
-
In the past year on my autoxer I have pulled the hole (washer and all) through the front crossmember with a solid mount. The mustache bar was solidly mounted as well as the engine and tranny in this car. At the time I figured it was old metal and that was it. In hindsight I think that it would make sense to reinforce this part or make a new one in a car that will see major abuse. I would also rethink the mustache bar/rear suspension mounting i fyou intend to solid mount the diff. I'd be looking at creating a cradle (dicussed in other threads) very much like you see done on rally cars. Cary