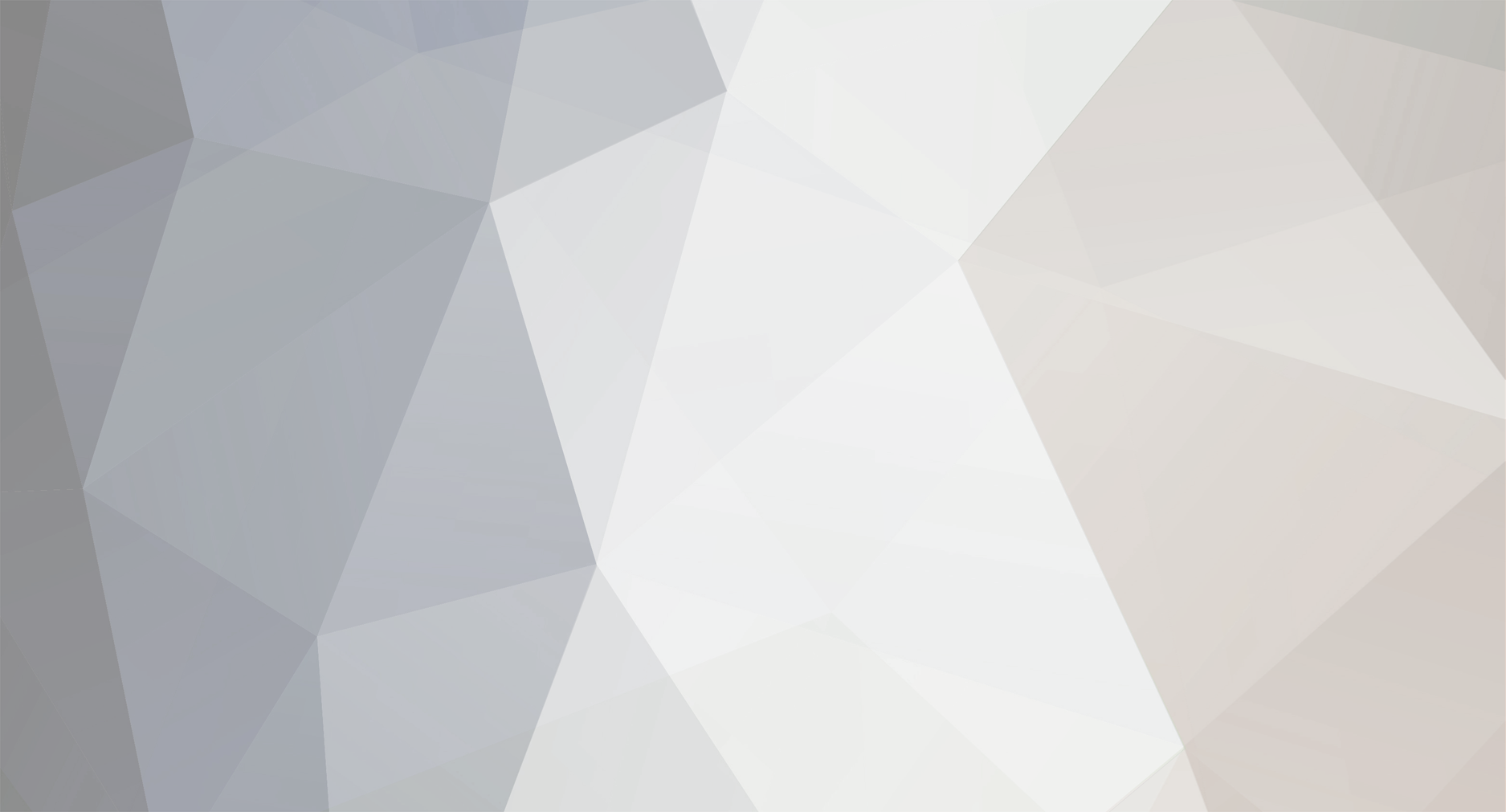
tube80z
Super Moderators-
Posts
1388 -
Joined
-
Last visited
-
Days Won
26
Content Type
Profiles
Forums
Blogs
Events
Gallery
Downloads
Store
Everything posted by tube80z
-
rear poly bushings on outboard end of CA
tube80z replied to blueovalz's topic in Brakes, Wheels, Suspension and Chassis
Try searching ebay. I've seen a few sellers selling lots of ten at really good prices. Cary -
Question about dual master cylinders...
tube80z replied to JMortensen's topic in Brakes, Wheels, Suspension and Chassis
If that's the case then they will interfere with how the system should work. Safety stops should only be on one side if you have them. Cary -
rear poly bushings on outboard end of CA
tube80z replied to blueovalz's topic in Brakes, Wheels, Suspension and Chassis
I have had good luck with the XM series QA-1 rod ends. Before that I used mostly aurora. They have similar monoballs. If you're camber plates put all the load on the bearing then you won't see them last too long. It's not loading the bearing in a way it was intended and short life is the result. While not really built for our cars the larger com-12 would probably last longer. Cary -
Question about dual master cylinders...
tube80z replied to JMortensen's topic in Brakes, Wheels, Suspension and Chassis
What are the washers supposed to do? From your pics it's not clear what you're trying to do here. You need to clearance the inside of the bolt above and I would recommend adding the lip back in around the firewall mount as it adds stiffness. Cary -
East Coast vs. West Coast setup?
tube80z replied to wheelman's topic in Brakes, Wheels, Suspension and Chassis
We've got a number of the used tires in Portland for a lot less than that, more like $200 a set at times. John Berget has these as well as a few other people if you don't want to make the drive to PIR. FWIW, I'm told Hoosier radials will have a similar price tag new. Cary -
Agreed, I would see this as dangerous without locknuts. Moving the LCA forward has the most effect on ackerman. In some ways you have a small amount of tuning available by moving using these spacers. You can also move the crossmember back and forth a certain amount too. Ideally you want the LCA to be perpendicular to the ball joint in plan view to take the majority of the force. Otherwise you'll start putting more lateral load on the TC rods. Cary
-
East Coast vs. West Coast setup?
tube80z replied to wheelman's topic in Brakes, Wheels, Suspension and Chassis
If you decide to go the slicks route make sure you jump straight to radial slicks. Currently the hot setup is the GY FA radials, which we've found to work much better than the Hoosiers. I'm sure Hoosier will respond with a radial as there seems to be a lot of people talking about them after nationals this last year. And if you run where it is cold you will probably be faster with a good DOT radial (Kumho, Hoosier, or possibly Hankook). Their tread compounds generally work about ten degrees less than any of the slicks. cary -
coilovers and wilwoods
tube80z replied to rztmartini's topic in Brakes, Wheels, Suspension and Chassis
If you were you'd still be analyzing all your options and trying to consider if the changes would be safe. Then you'd probably have used a metal lathe to cut the struts, applied a specific bevel to the strut tubes, created an overly elaborate jig to hold things, had then welded using a process known have ever heard of, etc. Sometimes all you need are simple blacksmith skills Cary -
coilovers and wilwoods
tube80z replied to rztmartini's topic in Brakes, Wheels, Suspension and Chassis
Sometimes too soft will make it understeer. My rule of thumb, and I seem to be all thumbs , is that if you make two steps in the direction that should have a certain outcome (like less understeer) and you don't get your desired result then go the other way. I know this seems obvious but I've watched really smart people chase their tails as the keep going softer and softer and it works worse and worse. Cary -
Rear suspension design. Looking for opinions.
tube80z replied to RTz's topic in Brakes, Wheels, Suspension and Chassis
Two, one on top one on bottom. Jon gave you the part number above. The procedure to determine the friction reduction for this or any other mod is as follows. You press the car down slowly and let it rise back up and measure the ride height. Now we raise the car and let it lower back down and measure the ride height. The difference in ride height x 2 x spring rate at the wheel = the force required to move the chassis. The goal is to make this number smaller. I don't recall the actual reduction in pounds but there was a measureable, but small, laptime reduction on the enduro course -- damn you more secrets extracted Take a look at the hyperco perch video and you'll see why this works. Cary -
Rear suspension design. Looking for opinions.
tube80z replied to RTz's topic in Brakes, Wheels, Suspension and Chassis
Yes, I was probably the original source. And that info came from Richard Pare who was one of the designers. Richard has a business with Steve Lathrop called ICP. They build a number of special parts for formula cars. Richard and Steve used to go around the country teaching a club racer race engineering class. I learned a lot more from those guys than I did from Claude Roulle's seminar (not to say that it's not good). And the best part was it was only $250 to attend. Sadly they quit doing it because they couldn't get enough attendees. Richard shared that these were super secret and used by WilliamsF1 a some years back. Williams was one of the last remaining cars that ran coil springs. And these almost won at Monaco. And for what it is worth, Richard said these won't help strut cars at all because we already have so much side load on the shafts. He said to do the standard racer trick of using bearings under the spring to reduce friction and that's about the best you could hope for. I guess I should also mention you don't need these if you don't have a coilover arrangement, meaning the spring is separate from the shock. Just another thing to think about Cary -
Rear suspension design. Looking for opinions.
tube80z replied to RTz's topic in Brakes, Wheels, Suspension and Chassis
Reiger makes such pieces. There are very common on rallycross cars and used to be used on a number of rally cars. I don't know if ohlins, penske, or any of the other high end brands do this. Maybe JohnC can tell us. I think he ran Penske tripples on his car. At one point some of the high end touring cars were using hex shaft in an effort to have increased stiffness. I don't think anyone does this anymore because of the sealing issues. Cary -
Rear suspension design. Looking for opinions.
tube80z replied to RTz's topic in Brakes, Wheels, Suspension and Chassis
I think that would be a fine way to go. I guess I don't understand how you do this unless you start restricting movement with the LCA, like roller bearings instead of sphericals. And when you do that you run into issues with compliance as parts bend. This is sorta like the sway bar mod you did. You could use rollers but when the bar and frame rail bends they bind. So until I see a better way to do this I'll stick with what I know works. So if anyone can show me a better way then I'll be happy to scrap the current parts and build those. This car will never be done and this is why. Cary -
Rear suspension design. Looking for opinions.
tube80z replied to RTz's topic in Brakes, Wheels, Suspension and Chassis
Just to set the record straight. The tube80 has yet to run under its own power. Hopefully this coming year. But the old design of parts have been statically tested. And we ran this configuration on a modified stock-type arm (toe-control link) on our old yellow Z for three years with no issues. I don't have the means to meaure side load on the struts. And to be honest I'm not all that worried either. What we have here isn't really much different than the front end of a FWD vehicle. I'm sure those have side loads too but it doesn't seem to be too big of an issue. Cary -
Rear suspension design. Looking for opinions.
tube80z replied to RTz's topic in Brakes, Wheels, Suspension and Chassis
That's already been done in a Jame's Bond film If you hit the curbs wrong on Medford you can get a little air. And their have been times when that extra little tenth seemed like a good idea. Bent parts after the fact seemed to indicated it may not have been. Cary -
Rear suspension design. Looking for opinions.
tube80z replied to RTz's topic in Brakes, Wheels, Suspension and Chassis
Bending the J-bar isn't going to happen often. I did it once and changed things a bit by adding a piece of metal to the bottom. Regardless, the J-bar isn't as good as using a double shear bracket and solid rod end. I think what bends this part is heavy braking and then hitting a FIA style curb or getting the car into the air and coming down under brakes. At least that was my experience. If you look at a number of formula cars from the early 70s and even some trans-am cars from the 80s and 90s they have figured all this out. I was trying to go the easy route and discovered that it isn't always as easy as it looks. The rear arms pictured about from the first version of the back of my car were tested and worked just fine. I didn't see any issues of bending the clevice or the attachment point. But since I'd already seen a problem with the similar joint in the front all this is changing to solid ends in double shear on the inside especially since I was going to double the HP/TQ. And since I did read the Carrol Smith books I owe him that much. And I will probably change the aluminum toe adjuster to a swedged steel part because it makes me nervous too. Although I've used the tubing for TC rods and tie-rods for a long time. I usually build new ones every other year. I had three reasons for wanting to do the rear arms this way. The first, which will sound silly to most, is to be able to quickly change rear toe. And before Johnc rips me a new one for that being stupid I would like to point out that it is an autox thing. By changing toe I can get more heat into the tires when it is cold. The second reason was to increase the installation stiffness and a side benefit I'm hoping for is reduced stiction. And lastly was to have an easy way to change squat/lift and RC positions. On the second version of the car this all attaches to adjustable mounts. All of this is easy enough to test if you have a porta-power and a pull ram. You do what is called a parasitic compliance test. To do this test you push and pull across the axle and note deflections versus force. The second is you push and pull longitudinally (front to rear) again noting defelction changes per load. These kind of tests will tell you a lot and give you an idea of what will most likely be the first thing to fail. This simulates how the forces are actually fed into the pieces. Not a mathematical proof but a nice old fashioned low tech way of measuring this before you do something stupid in front of your friends. It's much better to find something out in the garage where your emabarassment can be contained Cary -
Interesting Chassis work on sweet rx7
tube80z replied to LLave's topic in Brakes, Wheels, Suspension and Chassis
There are other bars, you just need to look real close. I'm curious why it appears to have a lot of production car still left in it. Cary -
Chassis stiffening ideas
tube80z replied to heavy85's topic in Brakes, Wheels, Suspension and Chassis
I'm not following all this but I don't think you'll get much stiffness from the rocker stiffenning on top and bottom. Maybe stick to the bottom and build an X across the floor. The center would need to come out but then you could connect the four corners. In lieu of a cage that might be the next best thing you could do. The only other option I would see is to make the car more of a back bone design by enlarging the tunnel and integrating the front and rear suspension loads into this. Before you start any of this you may want to build some basic models and see what works best. Even crude balso designs can help you figure a lot out. Class rules, if you're worried about that, will probably get in the way of a lot of this. Cary -
Question about dual master cylinders...
tube80z replied to JMortensen's topic in Brakes, Wheels, Suspension and Chassis
I raised them about a half inch. I don't really know why they look so low in the photos. Cary -
It's not the easy. When you open the roof or put a smoke bomb up there it will effect flow. A long time ago some backyard aero was tried on the freeway early in the morning. One car had yarn tufts all over and a chase car was supposed to video and take still pictures of the tufts. What we noticed is the chase car needed to be a long ways away to keep from changing the flow pattern. Claude Rouelle recommended a distance of at least 50 feet in his seminar. Cary
-
Question about dual master cylinders...
tube80z replied to JMortensen's topic in Brakes, Wheels, Suspension and Chassis
No by pedal ratio I mean where you put the balance bar. On a car wtih a vacuum booster it needs to go a little higher up the arm. I looked at the tilton pedals and used there leverage ratio when I modded the stock arm (distance from pivot to balance bar and total length of pedal). I have driven a car with the balance bar in the stock location and it requires a lot higher pedal effort to get stopped. Cary -
Take a look at this site, http://www.airtab.com/. I know one person that mounted these to their enclosed trailer and it does really work. If you look at people that have used them you'll find a link to a 914 that mounted them on the roof like the EVO. He reported that the car felt more stable at speed. Cary
-
There are a number of theories that also argue that momentum has a rather large effect in explaining how airplanes fly and spoilers work. Aero is an area of interest to me but I don't know enough to have an informed opinion. I can and do have data that tells me a spoiler is worth a large chunk of time even at autox speeds. And that's all I'm sharing Cary
-
Question about dual master cylinders...
tube80z replied to JMortensen's topic in Brakes, Wheels, Suspension and Chassis
I did option 4. Not that hard but you need to make sure you get the pedal ratio correct. You can see some shots at http://picasaweb.google.com/tube80z/BrakeUpgrade If these are a little small let me know and I can send you larger versions. Cary -
We can start with the basics. The car is a FWD chassis. The cage looks to be built for a RWD car and doesn't hook to the front at all. How the legs of the cage hook into the chassis don't seem to make sense. The fabrication is top notch. I wish I could weld that good. Cary