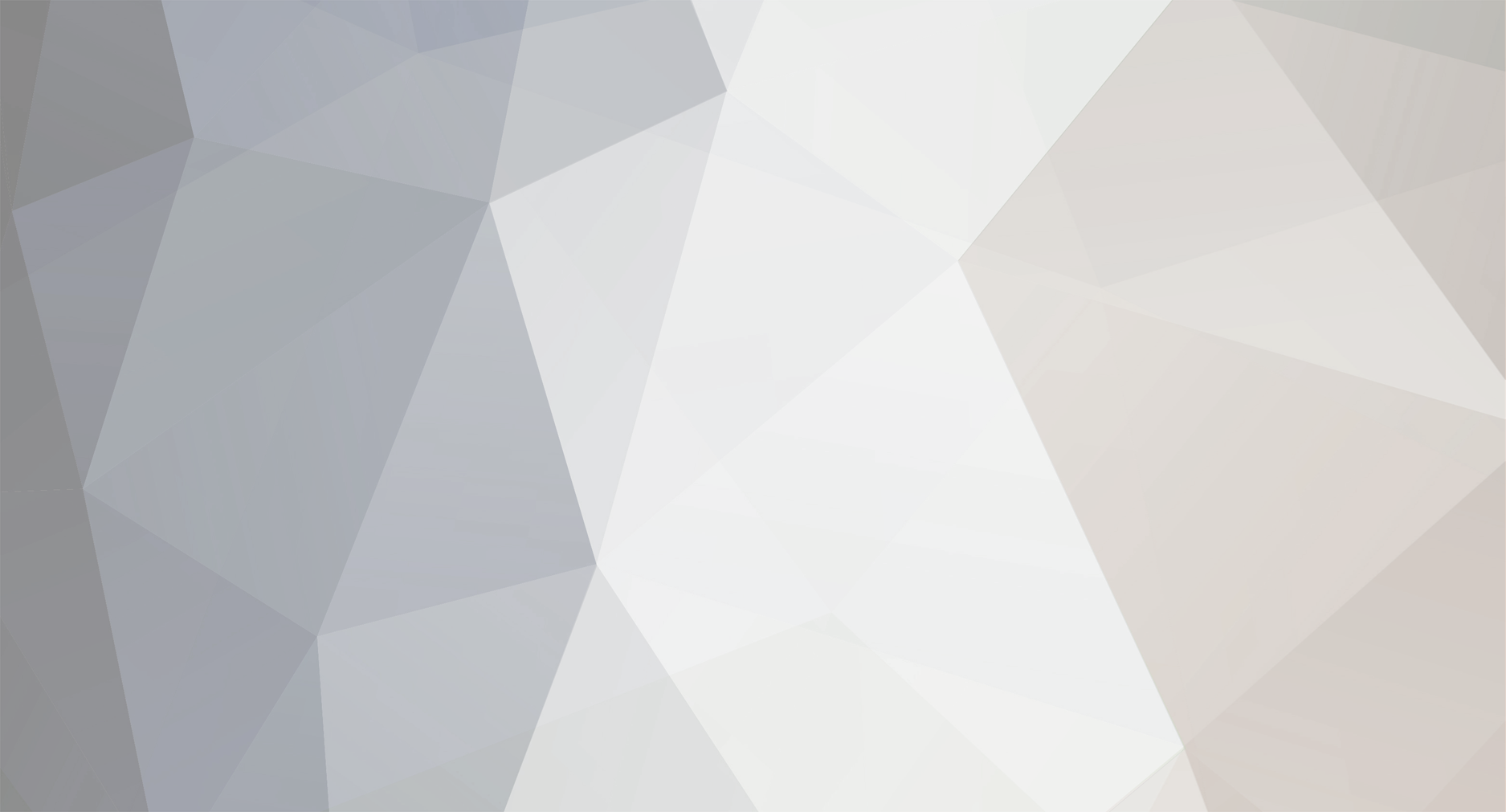
tube80z
Super Moderators-
Posts
1399 -
Joined
-
Last visited
-
Days Won
30
Content Type
Profiles
Forums
Blogs
Events
Gallery
Downloads
Store
Everything posted by tube80z
-
The poor man's rear toe-in adjuster
tube80z replied to blueovalz's topic in Brakes, Wheels, Suspension and Chassis
I can't remember why heims were used. Since this slides more or less in a straight line couldn't something solid be used? Did we already discuss that and I'm too stupid to find it? And a trick you may or may not know. If you need really fine adjustment use two different thread pitches rather than left and right threading. Cary -
A DIY way to do this is put paper behind the car and shine a light head on and outline the shadow on the paper. Then add up the area on the paper to see the total area. The basic idea is to see how big a hole you're trying to punch in the air. Cary
-
Jon is right. It's an easy experiment to prove with yarn tuft testing. Cut some pieces and tape it to the hood and see how the air moves with the hood open and closed. I used to think this would help until I watched the yarn go into the engine compartment. On my race car I put holes in the inner fenders in front of the strut tower to allow air to escape. I then added gurney's to my fender flares that could be moved out if I needed more airflow. And in front of the radiator I used a box to help slow the air as it hit the radiator face. Also make sure to use the stock belly pan or add an upgrade. If I wasn't in FP at the time I would have made a duct that came out the hood for the radiator. Louvers in the front section of the hood would probably have a similar effect. Cary
-
I use the Davies Craig with pump controller on my race car. It seems to work as well as the belt driven pump did for me. I don't know how long the pump is rated for continuous duty. It does make wamring up quicker and is nice to circulate the coolant when it's turned off hot. Cary
-
Dual master cylinder sizes with 4 psiton calipers
tube80z replied to a topic in Brakes, Wheels, Suspension and Chassis
If you're brakes are pushed on equally by a rod that goes through the brake pedal you might see if you can get a copy of Race and Rally car sourcebook. In it they have a low buck bias adjuster that would be easy to build. Cary -
I know this isn't a car but had your friend considered something like a 125cc shifter cart? You can haul it around in the back of a pickup or large SUV. Or on a really small trailer like you can get at home depot. A 125cc shifter kart is a serious little ride and the racing is as good as a car. The new TAG 9touch and go) models are easy for one person to deal with and well within this budget. Cary
-
I'm not sure that's really correct. My understanding is that the sub strap is designed to keep the belts low so that the load is spread across the larger bones in your body. If they belts rise then you do nastly things like blow out spleens or worse. From what I've read you really should be using 6-point belts as they do a better job. Mounting for all this is critical and a number of people do it incorrectly and most people don't have the belts tight enough when they are in the car. And if you're running at speed it makes sense to add a head and neck restraint into the equation. And if you have a dedicated track car then you should have a proper seat and it should be mounted correctly. Aluminum seats with bead liners work well. I never used to worry about all this but as I've seen a few wrecks in the last couple of years that could have been far worse. And I'm building a car that will be a lot faster than anything I've ever had before. And when Newton is driving you typically have little input on where you go. Cary
-
Hi Paul, That looks pretty involved. Do you do any flowbench work in conjunction with this? Is this all on a per quote basis or do you have standard rates? Cary
-
Recommendations for AutoX Slicks
tube80z replied to heavy85's topic in Brakes, Wheels, Suspension and Chassis
Their site is http://jbracingtires.net/index.htm Cary -
New pics of damaged 240, How would you proceed?
tube80z replied to a topic in Brakes, Wheels, Suspension and Chassis
Quit stressing -- this is nothing. Take it to a shop and have them pull the corner out and then replace what is mangled too much to fix. If you go somewhere decent they should have the tramming measurements that are needed to verify alignment. I had a car that hit a tree at a hillclimb that had the strut towers pushed back. I fixed it at home, ugly and temporary I might add, and squared it up as best I could. It worked fine and won quite a few races. You don't need another shell. Far worse are fixed all the time. Cary -
I think you're correct. John also provided some good info that I thought was happenning with the rear mustache bar bending. I had a couple of ideas on how to fix this but I never got around to doing them. I was going to use a stock mount (broken) and weld it up solid and have tabs to extended below the crossmember. Then this would be bolted under the crossmember. This was all doable with flat stock, a few pieces of tube, and some bolts. This would spread the load from a sinlge point as well. I do think making a subframe for the back isn't a bad idea as it allows you to keep a lot of bits from flexing and would make the suspension mounting stiffer too. But that's a personal opinion that not everyone shares. The moral of the story is when you start using an old car really hard you need to keep an eye on it and I'm not running a V8. I torqued all bolts before I used the car and replaced them when they started to routinely loosen. Cary
-
In the past year on my autoxer I have pulled the hole (washer and all) through the front crossmember with a solid mount. The mustache bar was solidly mounted as well as the engine and tranny in this car. At the time I figured it was old metal and that was it. In hindsight I think that it would make sense to reinforce this part or make a new one in a car that will see major abuse. I would also rethink the mustache bar/rear suspension mounting i fyou intend to solid mount the diff. I'd be looking at creating a cradle (dicussed in other threads) very much like you see done on rally cars. Cary
-
I often cut it with a hacksaw blade being careful not to cut into the control arm. Then knock it out with a hammer and chisel. Sometimes an air hammer will work but not always. Cutting the sleave is a sure way to remove it. Cary
-
Car is "Jumpy" when Corrnering semi sharply....
tube80z replied to 240ZR's topic in Brakes, Wheels, Suspension and Chassis
Have a friend watch the car in a corner. I saw a car once that had a blow shock and the wheel would start jumping up and down as they accelerated in a corner. They complained of similar behavior. Cary -
The old aftermarket version used to be Delrin. The last one I bought was injected plastic. I've never had an issue with additional vibration through the wheel with these and it did improve steering feel. Cary
-
QA-1 makes a nice new high misalignment bearing good for 64 degrees or so I hear. But then it would be pretty simple to weld on a bracket the has the hole the other way. And you could get real tricky and slot the bracket, use mutilple holes, or a number of other ideas to play with dive if you wanted to. I've used a garden sprayer (deck sprayer actually) and used small rubber line for the tube. You drill a hole in the end of the rail and insert this then let the oil rip. I used WD40 that you can buy in bulk. Other things would probably be better. For my friends car we're going to put weldthrough on the rails and the back of the BD parts and weld then on. We'll probably follow-up with oil.
-
I had a super vee with a hewland dog box. The best way to shift it was quickly. On an upshift I'd simply lift the throttle a tad and select the next gear. If you tried to use the clutch you'd often hear a crashing sound out back. If you must use the clutch just bump it but don't hold it all the way down (maybe you have a pressure actuated ignition cut). Dog rings, unlike syncros literally grab the gears and engage them. You need to be careful on a downshift that you don't select the wrong gear. Because it will engage. Normally to downshift you'd pull the gear to neutral, rev the engine, and engage the lower gear. Normally I was left foot braking at the same time and going down gears with quick stabs of the throttle to match gear speed. In the hewland the part I hated most was selecting first to start. It sounded like parts were exploding in the box. It was best to quickly move the shifter after depressing the clutch (the gears need to be moving to engage. Often I'd ask people to push the car and I'd do this rolling. My EMOD project has a g-force dog ring T5 tranny that I'm looking forward to using. Cary
-
I'd, remove the part that covers the end of the tub and move that flush to the rear rail. Then I'd make extensions on the BD rails to come up to this. I think you want this solidly conencted to keep crap from getting up inside. Can you use a jack under the car and some of your tube in the other picture to press this up against the floorpan? Can you use the square tube to create your new TC bracket? Cut flush and capped on the outside of the rail and then openned up on the inside to give you the ears you need for a vertical bolt. Then metal on the bottom spreading the load forward on the frame rail. I'm also curious if BD gives you any info on how to prep these parts. I have a friend that is looking to do the same thing as you. Are you going to use weld thru on the back of all these parts are any other rust proofing? Cary
-
I'm curious. Is this at the same wall thickness? Since DOM is made from ERW does the work hardenning really make it that much stronger? Cary
-
Camber plate indentification, install looks odd
tube80z replied to a topic in Brakes, Wheels, Suspension and Chassis
It looks like you have a pretty trick car. And from what little I've seen of it I'd agree with Jon. Did they increase the front track on this car? That could be one reason to mount the plates they way they are. Cary -
rear poly bushings on outboard end of CA
tube80z replied to blueovalz's topic in Brakes, Wheels, Suspension and Chassis
Thanks for the info Joshua. On my tube car I widened the base by a fair amount. For the example about I wouldn't see changing this by more than a couple of inches. On the lateral load why can't you look at it like a triangle? It seems that I've seen a number of books show this for lateral force distribution it inner pickup points. Cary -
510 steering swap, Attn Braap, Jmortensen
tube80z replied to Bluto's topic in Brakes, Wheels, Suspension and Chassis
Many years ago that's how Michael Spreadburry's car looked. I helped him do a swaybar. We mounted it under the TC boxes on the front of the car. There was just enough clearance between the TC rods and the tie-rod but it never touched. On my 510 it uses Michael's old crossmember but I shortenned the rack and went to rear facing TC rods. That way I didn't increase the track width. It hasn't made it much farther than that as I started playing with Zs again. On the steering column you can take the end out of teh Z column (it has a bearing) and put this into the 510 column. Then all the 240 steering shafts will fit. You will have to lightly hone the end of the 510 column to get the bearing to fit. They usually have a bunch of gunk up in there from years of use. Cary -
rear poly bushings on outboard end of CA
tube80z replied to blueovalz's topic in Brakes, Wheels, Suspension and Chassis
On my car, which has longer arms than normal I have 9 inches of movement before the rod ends touch, and that's mocked without misalignment washers. What I read in my catalog claims 22 degrees of movement with them. On the back of my race car I typically only use about an inch to 1.25 inches of droop. I found it seems to work best by setting the rear limiter at the point where the spring just slightly touches (maybe 20 pounds preload) on a 450 pound spring. And for bump I have about 3 inches but it's really only using around 2. I think these numbers could easily be doubled and you'd still have no issues with clearance. But using some form of mechanical stop would be good so that you don't break the rod end. If that happens the outcome will not be pretty. These are all good things to think about though. And I think this only makes sense on a race/track car. Cary -
rear poly bushings on outboard end of CA
tube80z replied to blueovalz's topic in Brakes, Wheels, Suspension and Chassis
It's early and I haven't had any coffee just yet. But isn't the torque created by the traction proportional to the lever arm from the outside to the inside at the front and rear pivot? I don't see where we changed that distance. If you were talking about lateral force I could see where that went up due to a change in leg angle but it wouldn't be a factor of two. And what we're talking about here is just shortenning this by only a couple of inches at most. Cary