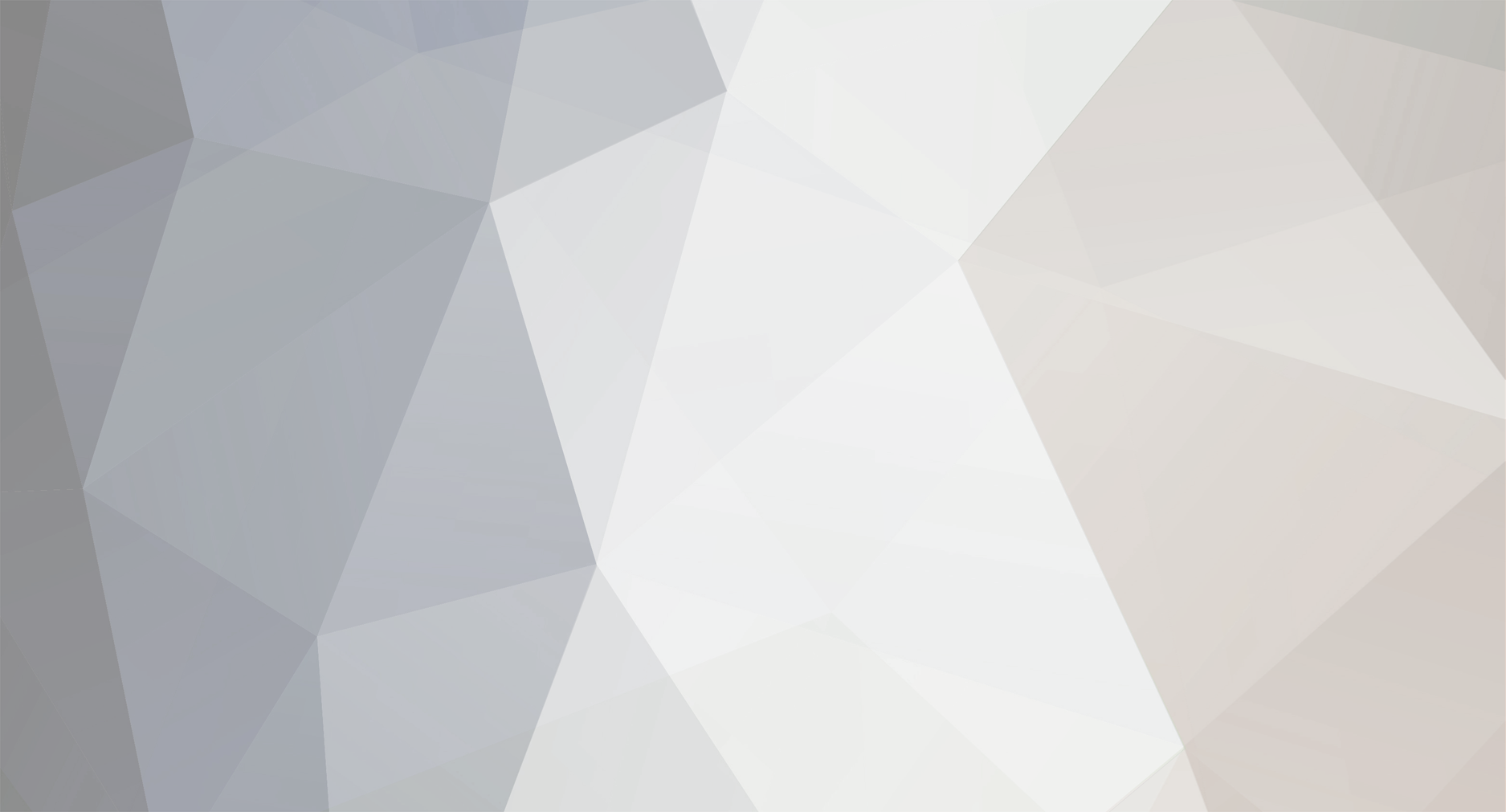
tube80z
Super Moderators-
Posts
1399 -
Joined
-
Last visited
-
Days Won
30
Content Type
Profiles
Forums
Blogs
Events
Gallery
Downloads
Store
Everything posted by tube80z
-
Just remember when starting with a strut as an upright you should fix the high SIA/KPI. Cary
-
Older supras and MR2s had a strut suspension with additional arms that located the strut to take bending loads off. As John mentioned you need to figure out the anlges and articulation so you don't bind things. Another option for drag only would be what they do the front of many FWD cars. Those funky traction bars. As long as everything was in rubber or poly you could use those to keep the arms from moving, again assuming that's the real issue. If not then you need to look at making the bushings less compressible. The only option is then a monoball or heim. And since someone is good at fabrication it sounds like they would just build new tubular lower arms with heims/monoballs. Not that those are cheap. But before this all gets carried away some simple tests need to be done to understand what the problem is. cary
-
If you do this turn them upside down. The lower mount them becomes an a-arm to the old strut tube the the top is a reverse a-arm and toe-link. This will make getting the geometry right a little easier while letting you burry the upright into the wheel. Here's a pic of the idea. Cary
-
rear control arm movement/fatigue
tube80z replied to a topic in Brakes, Wheels, Suspension and Chassis
This car is an automatic isn't it? Get a buddy to power brake it for you and watch what happens to the wheel position. Does it move forward? A friend showed me this once on his car and it had a major toe-change. He used to run some toe-out to deal with the deflection and claimed it made the car easier to drive. If you see deflection then you may want to get creative at seeing where the deflection is coming from. Until you know the issue is the wheel moving or not coilovers may just be a waste of money. I can't think of any easier way to do this. Cary -
rear control arm movement/fatigue
tube80z replied to a topic in Brakes, Wheels, Suspension and Chassis
I don't have any answers for you but I can tell you how to test to see what the problem truly is. You need to perform what is called a parasitic compliance test. To do this you will need to build a jig for the front and rear tires that bolts to the hub and is the same radius as the tire (quarter wall 2 inch square tube should suffice with some bracing). You will also put a toe plate on the hub to measure toe, camber, and lateral/logitudinal displacement can be measure with a plumb bob. These will be bolted to the hubs and then you will lock them in place using either brake pressure or some form of clamp to keep the hubs from rotating. Then at the bottom of the jig you will attach a porta-power with a pulling attachment (it also needs a guage). This will simulate the force of the launch of the rear tire and braking at the front. This should be configured so that you can slowly go up to 3000 to 4000 pounds of pulling force between the wheel pair. I would recommend going up 250 pounds of force at a time and measuring everything. Be careful doing this as you'll end up with a lot of force on things as you measure it but this should show if you have an issues that are force related. I know this sounds like a lot of work but it may show you things you can fix that will make your car even faster. I was curious what MPH you see in the 8th and what the time was. I've been trying to figure out 0-60 and 0-100 times for a high horsepower Z. Your car sounds like what I was looking for. Hope this helps, Cary -
Now come John, you should know the TIG is for the house Cary
-
My fuell cell installation, can I install it the other way?
tube80z replied to pjo046's topic in Fuel Delivery
This what I did on my car. It also makes the plumbing a lot simpler than having it stick out the back. I could run down to about 1.5 gallons before I started to see slosh related problems. I got the car this way and it was much easier to tilt the cell than turn it around. Something to think about. Cary -
remounting the Master Cyl inboard
tube80z replied to 660Z's topic in Brakes, Wheels, Suspension and Chassis
I was going to use these on my unibody car. As you mention they don't fit well unless you cut a hole into the firewall to position them. On my tube car it has space for these so it isn't an issue. I prefer floor mounted pedals for how they move. If you think Tilton is expensive AP makes a really cool setup that has the master mounted facing backwards that fits just fine. The price involves another zero. Cary -
That's pretty much how it went. I was overly optimistic on how much braking force the car could generate. I've routinely seen the range you show above. I've been able to get to 1.2 only in a few straight line tests. I really couldn't understand why the car can corner at 1.4 to 1.5 and only stop at around 1. I found out last year that it was the tires that are my limiting factor. This year I plan on logging brake pressure to try and get better at braking. I know that I'm not very good at that and need to improve. Cary
-
-
It's interesting but unclear to me if you can be semi-tube like the front of your car. I know you can't molest the firewall. Cary
-
I went looking but seem to be challenged in finding pics today. This sounds interesting. In my early investigations it became clear that a two piece strut is better as it allows you to partially seperate changing camber from changing RC. Is this what he's done? Cary
-
That's pretty much what I did. I used a tilton balance bar assembly and modified a stock pedal box to accept dual masters. Then I used the tilton prop valve to get the initial rear bite just right. The beauty of this setup is that I have enough variation to be able to handle wet or dry. In the new car I can display brake pressure on the dash from the datalogger so setting bias becomes very simple. Cary
-
Is that one of those double ball-joint versions? I played with that idea for a while but couldn't get everything to live in my tiny 13 inch wheels. Cary
-
Need some help on a NHRA Rollcage design
tube80z replied to cyrus's topic in Brakes, Wheels, Suspension and Chassis
Just curious, why is that? Cary -
Thanks for the pics, those helped a ton. My only reservation on all this would be mounting this bolt in single shear and adding spacers to it. I think you could get away with it in single shear (similar to a balljoint on the bimmers) only if the spacer was really short. It would be much better all around to make the mount double shear. I'd also make sure to have as close to the amount of surface area for the bracket as the original. If you decide to go this way I'd use a tube to support the bolt rather than the clevis idea. The top could wrap over the top of the frame rail and the bottom the same. The tube would be welded to a plate that would cover the inside of the rail. Very similar to the clevis but with more surface area. I would stack spacers in this application. I'd make them one piece. I'd also suggest looking for a nord-lock washer system in this application to keep things tight (http://www.nord-lock.com/) In looking at this on my car it appears it could come off. I do think it adds to the strength of the rails but how much off it is used for taking the load the TC box would be a question. If you look at what 74_5.0Z's car you'll see that's pretty much what he did and I really like it. Bummer on the off, BTW. It was such a pretty car. I'd opt for this one myself. Either cut the rail for the square tube to go all the way through and use it as a double shear TC box. Or put a tube in it to hold your bolt. This would be the path I'd follow myself. Cary
-
So here's what I'm thinking. I spent a little time looking at this over the weekend and I didn't see an easy way given the frame rail is curved. If you look at 74_5.0L_Z's car he has flat frame rails and the TC box could be simpler. Don't laugh at my great power point CAD skills The idea would be to cut out around the round area to open it up for the TC rod to pass through (the red lines). The green lines would be a doubler plate on the frame rail that gussets from the original TC box would go to. Not shown would be the back side of this covered so that it forms a box. Hopefully that makes sense. For the adjustment I'd use two safety washers and aluminum rod as bushing material. This would give you good range of movement and an easy way to have bushings cut that would raise or lower this pivot. Now for the underbody brace I was looking at doing a triangle like this under the engine bay. The tubes from the rockers would be welded into the TC box. From the TC box to the crossmember I'd make these bolt-in using countersunk machine screws. I don't have a pic of this but you essentially slot the tube and weld it to a flat plate. The idea being that it is strong in tension and weak in compression. So if you ever had a major collision the engine could still eject out the bottom. Hopefully that helps. I couldn't figure out how the clevises would work that you described above. Wanna take a shot at a visual of your idea? Cary
-
I ran a similar amount on my car using bias ply slicks (13" FA fronts). In the motec seminar it was pointed out that caster is very tire dependent. Claude's example of how to think of a tire was as a number of interconnected springs. If you coilbind any of them you slide the tire. Some tires need a lot more caster than others. Claude told us that one car they run uses 29 degrees of caster. The trick in testing this is to also realize that you'd need to change the caster trail as you increase the angle to test just caster. And the trail will change with tire diameter. It's the caster trail that leads to increased steering stiffness as you add more caster. Cary
-
I ran a similar amount on my car using bias ply slicks (13" FA fronts). In the motec seminar it was pointed out that caster is very tire dependent. Claude's example of how to think of a tire was as a number of interconnected springs. If you coilbind any of them you slide the tire. Some tires need a lot more caster than others. Claude told us that one car they run uses 29 degrees of caster. The trick in testing this is to also realize that you'd need to change the caster trail as you increase the angle to test just caster. And the trail will change with tire diameter. It's the caster trail that leads to increased steering stiffness as you add more caster. Cary
-
If you're really serious about porting you might try and find Practical gas flow by John Dalton. I think it may be out of print. It details how to make molds of the head, build a basic flow bench, and various techniques. Get an old head and section to see how far you can cut before striking water. Then prepare to spend a year or so of spare time to develop a port shape that works well. Taking of sharp edges and blending mold moarks is not too hard. But trying to alter the shape of the port to flow more air across the entire lift range is not trivial. And no engine shop will port any head for $200. If they quote that for a price I wouldn't let them work on anything of mine. Cary
-
Another useful item to add is the little felt lubricator/cleaner before the liner on the inside of the machine. It will help to make things work/last a little longer. I've also found is that some liners are made much better than others. When I adjust tension I set it so that the drive wheels just slip if the wire is pushed directly into the concrete floor. That's saved me from dealing with bird nesting. I don't know how I could function without a welder. Cary
-
front frame collision repair
tube80z replied to Muskrat's topic in Brakes, Wheels, Suspension and Chassis
What about MIG brazing http://www.google.com/search?hl=en&q=MIG+brazing&btnG=Google+Search Cary -
One area I'm going to work on this year is getting up to pressure much more quickly. That was one area pointed out in the motec seminar where amatuers and pros often diverge. In the first bit of brake application it is almost impossible to raise the pressure fast enough, although you can have too much and lock wheels. The trick is to hit hard and fast in a controlled manner. Cary