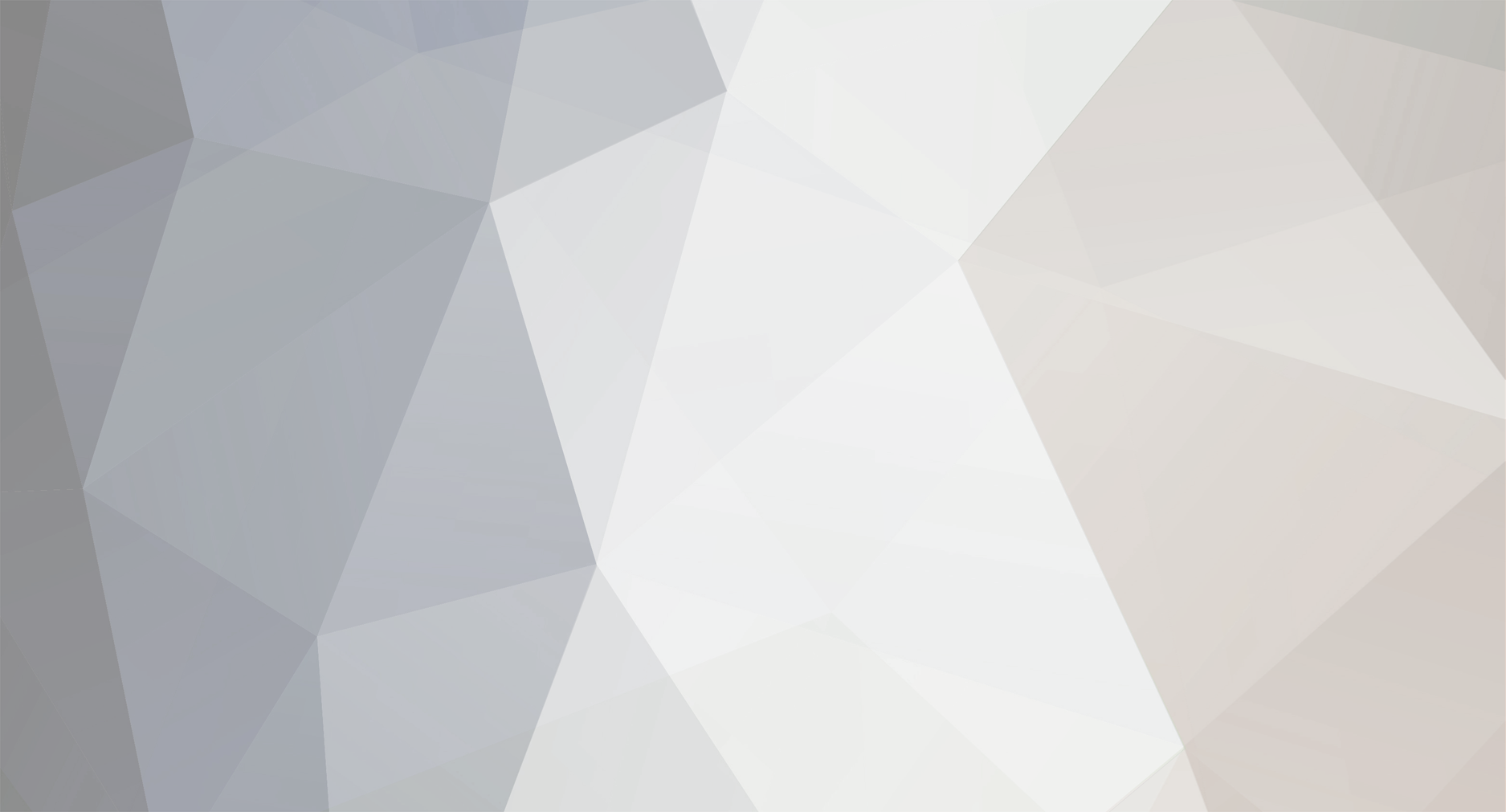
Ironhead
Members-
Posts
529 -
Joined
-
Last visited
-
Days Won
18
Content Type
Profiles
Forums
Blogs
Events
Gallery
Downloads
Store
Everything posted by Ironhead
-
I have a 260z, not a 280zx, but on my car at least I much prefer a larger diameter wheel, similar to stock. There are several 380mm wheels on the market, from OMP and MOMO at least. I don't know exactly what it is on these cars, as I am more used to wheels in the 330mm range. But I tried those on the Z and did not like them. Much better feeling of precise control with the larger wheel.
-
That's a tough one. Based on what you have done, I would conclude the noise is coming from somewhere besides the diff, but I am sure you have already investigated that possibility? I know bad bearing howl can be quite difficult to pinpoint. Any chance you have a fried wheel bearing? Could the noise be from the transmission? Apologies if these are stupid questions, but it sounds like you have addressed potential diff problems four times over....
-
Stainless steel vs plated steel vs aluminum rivnuts
Ironhead replied to fusion's topic in Body Kits & Paint
I know this isn't what you asked, but for fender flares I would use rubber well nuts. https://www.mcmaster.com/well-nuts/ They seal the holes without damaging the paint, allow for a bit of misalignment (much more than rivet nuts), and IMHO are much easier to use. I have used a lot of rivet nuts in various applications where there is no better option, but find them pretty temperamental in the sense that they always like to spin and have to be drilled out and replaced. Well nuts also have the advantage, that in any sort of collision they will shear off rather than greatly damage the underlying bodywork. -
One of the things in my experience that makes older cars unreliable is corrosion in the electrical system, primarily the connectors. You can track down all sorts of elusive and intermittent electrical gremlins, only to find the corrosion was the issue. It is never ending, because once corrosion has begun, cleaning it off only seems to provide a temporary fix and it returns. I have found once you re-wire the car (assuming you do it "right") all the nagging glitches and issues disappear.
-
I used a Tilton pedal box in mine. Hard to recommend this approach unless you have the dash area of the car pretty much completely dismantled. You are going to have to weld in structure/brackets to support pretty much any aftermarket pedal setup.
-
ANOTHER Datsun Z/LS3/T56 Swap Thread
Ironhead replied to Ironhead's topic in S30 Series - 240z, 260z, 280z
https://www.jongbloedracingwheels.com/ -
I know what you are saying for sure....the inclination is to cut out as little metal as possible. But where there are pinholes, there will be pits, so the surrounding metal that is not pin-holed will be massively thinned and weakened from the corrosion.... Working on my shell, I found myself making larger and larger patches. It just seemed to work better than trying to fill pinholes or using a large number of smaller patches.
-
I don't know what your skill level is at TIG welding, but if you can do what you propose, it would be a good repair. I can tell you that using TIG on the thin Datsun sheet metal....particularly when it is even thinner from corrosion, is very difficult. Even at 20 amps, burn through will happen extremely quickly. If you can pull it off, you are way more skilled than I am. I found the best way to remove pinholes was to cut out all the corroded metal and weld in a patch. But that's just me....
-
ANOTHER Datsun Z/LS3/T56 Swap Thread
Ironhead replied to Ironhead's topic in S30 Series - 240z, 260z, 280z
If the issues continue, that will definitely be the next step. The belt is obviously "mission critical" and I am tired of dicking around with it. -
ANOTHER Datsun Z/LS3/T56 Swap Thread
Ironhead replied to Ironhead's topic in S30 Series - 240z, 260z, 280z
I have been driving this thing longer and longer distances, trying to correct all the bugs and other things that I didn't like. Some of the issues: After 50 or 60 miles, it would shred the serpentine belt. I found that the tensioner was approximately .12" out of alignment with the other pulleys. This was strange since the tensioner is a GM LS3 part, but I shimmed it a bit and solved the shredding problem. Then it started throwing the belt. I switched to a belt a couple of sizes smaller (shorter) and that problem seems solved. I had minor leakage around the passenger side door when washing the car. Fixing this was just a matter of loosening the window frame screws, moving the frame inward so it made more solid contact with the seal, and retightening the screws. All good now (I think). The hatch gets water inside it when washing the car. I am 99% sure the entry is via the spoiler hardware, and can be fixed with rubber gaskets and thread sealant, just haven't dealt with it yet. Assorted clunking noises from the rear end when going over bumps. This was partly due to having too long adjusting screws for the rear upper strut adjustment plates. When the suspension bumped, the upper spring perch was hitting the screws. Shorter screws fixed that. It still clunks a bit, which I think is due to the exhaust hitting the hardware for the diff mount. Still have to sort that out. After re-locating the oil cooler and better sealing the radiator for improved airflow, cooling is no longer an issue, at least not road driving. Track remains to be seen. The stock steering column had loose bearings, and it was driving me crazy because it clunked when the steering loaded up. I modified the electric power steering and replaced the column with a modified Woodward one. Now steering is rock solid. However, the stock turn signal/high beam controls no longer were viable so I added steering wheel buttons for those things, and also the reverse lockout switch. I am pretty much calling the car done. I mean, it will never be "done"....but it is fairly well sorted. I'm sure I will be tinkering with it as long as I own it. Plan is to put a few more road miles on it (has about 700 ATM) just so I feel reasonably comfortable in its reliability, then do some track days when the weather cools a bit. -
IMSA GTU vintage racer build
Ironhead replied to clarkspeed's topic in S30 Series - 240z, 260z, 280z
My freakin car is half Ztrix, and I agree their parts are great, particularly considering the offerings I have seen from some other suppliers of Z body parts. For a show car, even the Ztrix parts are going to require a lot of work. But for a track/racing car, you can pretty much just paint em and go. -
ANOTHER Datsun Z/LS3/T56 Swap Thread
Ironhead replied to Ironhead's topic in S30 Series - 240z, 260z, 280z
Respect, Rossman. Too many on the internet just double down or remain silent when they realize they might have been mistaken. It takes a big person to admit they were wrong. It takes a bigger person to laugh at that person.....lol.😄 -
ANOTHER Datsun Z/LS3/T56 Swap Thread
Ironhead replied to Ironhead's topic in S30 Series - 240z, 260z, 280z
I included an "H" in my heater hoses so the coolant would still flow through when the heater (defroster, really) is not in use. Beyond that, I might have given the wrong impression about the engine's cooling status. After moving the oil cooler and sealing the radiator area from "leaking" airflow, I took the car out and drove it hard in mid-90s weather and things stayed cool just fine. I was surprised by how much the fans were running...but that isn't really a problem in itself....that's why it's there. Would the car cool adequately during a 100+ degree track day? Not sure yet, but it's kind of moot....because I can't deal with 100+ degree track days anyway....LOL. I do know enough about tuning to know that I am not going to mess with the engine's factory tune. Odds are I would just make things worse. Also, I read on the 'net that in some OEM applications, the LS3 fan doesn't even come on until the engine reaches 225 degrees, or somewhere around there. That blew my mind....but I guess a hot running engine helps with emissions. Anyway, my plan currently is to call the cooling status "good" unless something happens to change my mind. -
ANOTHER Datsun Z/LS3/T56 Swap Thread
Ironhead replied to Ironhead's topic in S30 Series - 240z, 260z, 280z
No, ECU is stock GM part. I think there is software you can buy to allow tuning some aspects of it, but tunability was not GM's intent. The one thing I learned about tuning, is that you really need to learn to do it yourself. Doing it right is extremely time consuming and tedious, most of the professional "tuners" around know little more about it than you do, and unlike you they are not willing to put in the time. Also, any slight engine change, even as small as a different air filter setup, will require some re-tuning if you want the car to run its best. Constantly having to put it back on a dyno to re-tune is maddening. For fuel tuning, the challenge is logging AFR in as many cells as you can. To do this you wind up doing all sorts of creative things, like driving up steep hills, driving while dragging the brakes, etc. You always wind up doing some extrapolating of cells based on AFR for neighboring cells....but hopefully as little as possible. Another option, several owners of the same model car I had found that our engine builds were identical. One guy in the UK had a "no holds barred" professional tune done on his car, then started selling the ignition and fueling data and other parameters to others with the same build. -
ANOTHER Datsun Z/LS3/T56 Swap Thread
Ironhead replied to Ironhead's topic in S30 Series - 240z, 260z, 280z
I drove it yesterday in 94 degree weather. Temp stayed good, but cooling fans were going on A LOT, even when car was at speed. Fans go on at 203 and switch off at 196. Not sure, but still seems like it points to inadequate airflow, although no matter how good airflow through the radiator is, the fans would still increase it by creating a low pressure zone behind the radiator. Obviously I couldn't duplicate track conditions on public roads, but I drove it pretty hard. Honestly, I'm not sure though that I will even track this car in warm weather. My home track (Thunderhill) gets hotter than hell, and I have done summer track days in the past in my other car (no A/C)....really not much fun. In addition to no A/C, the Z also picks up a lot of heat from the trans tunnel, and it gets...unpleasant....inside on warm days. For summer I used to go to Laguna...but the noise restrictions there have pretty much 100% driven me away. I could write a book on my experiences with dyno "tuners" from my other car, which has a highly tuned four cylinder engine. None of it would be good. I eventually learned to use the ECU logging function and tune it myself, which was my only salvation. One of the main reasons I went with a crate engine with GMPP ECU on this build was to avoid having to use those bozos. I do know of one tuner I would trust, but it would involve taking the car to So Cal, full day rental of a dyno and payment for the guy's services. As I understand it, he can work miracles, but it results in a $5000-6000 day. Do you think any dyno tuner could improve upon the GM factory tune anyway? As a crate engine, the tune is in no way compromised for emissions or mileage or anything else....pretty much just to run its best. -
ANOTHER Datsun Z/LS3/T56 Swap Thread
Ironhead replied to Ironhead's topic in S30 Series - 240z, 260z, 280z
Finished the revised oil cooler installation. I thought it would be a one or two day job, took me about a week and a half. Basically the (new) cooler now sits in the gap between the undertray and bottom of the radiator support. This should get tremendous airflow, without in any way disrupting or heating the airflow to the radiator. As a side benefit, this location also blocks off a major spot where a lot of the airflow that would otherwise go through the radiator could previously escape. I installed a "T" fitting in the lower line to use to drain the cooler/plumbing when doing oil changes. Might be a bit anal, but the cooler and plumbing hold well over a quart of oil, so I thought this was worthwhile. Since the cooler sits fairly low, I wanted to install screening to protect it from rocks and keep out leaves, bugs, whatever. Otherwise the ducting would create sort of a trap for garbage to collect in front of the cooler and it would be a PITA to remove. Hopefully (I REALLY hope) this modification will solve my cooling issue by improving cool airflow to the radiator. If not, I will have to add additional ducting to force more air through the radiator, which I don't really want to have to do. Thanks for looking. -
Holy crap. That is beautiful, clean work.
-
Anyone else find this site and its pages to be balky and often very slow to load? I'm trying to figure out if there is an issue with my computer or something specific to the site. Thanks.
-
240z SCCA vintage race car, restoration
Ironhead replied to AydinZ71's topic in S30 Series - 240z, 260z, 280z
Holy Crap. Time warp. I read that book in high school in the (I don't even wanna say what decade) when I first became interested in cars. You jogged something in the back of my mind, otherwise I had forgotten it even existed. I vaguely remember racing cars with drum brakes, things like that in the book. -
ANOTHER Datsun Z/LS3/T56 Swap Thread
Ironhead replied to Ironhead's topic in S30 Series - 240z, 260z, 280z
Good idea. I also definitely think the first place ducting would be of benefit is where you suggested above, to prevent air from slipping down and below the radiator. Currently, the hood should keep most air pressure from escaping upward, and the sides of the chassis create sort of natural "fences" to keep airflow from escaping to the sides....downward is the biggest problem (I also need to plug the passenger side cabin fresh air intake hole). -
ANOTHER Datsun Z/LS3/T56 Swap Thread
Ironhead replied to Ironhead's topic in S30 Series - 240z, 260z, 280z
Will do. I think Ron Davis' advice is pretty much something that I should have followed from the beginning, and which I knew I should have followed, it's just sort of a PITA to actually do, so I let laziness prevail. I am starting off by moving the oil cooler and sealing the airflow gaps around the radiator with adhesive backed polyurethane foam. Then I am going to test it and see how much improvement is noted. If it still gets too warm, next step is going to be increasing amounts of aluminum ducting to further force the air through the radiator. I'm just hoping that step won't be needed, as it will involve some significant fabrication time that I would just as soon skip. Laziness again. -
ANOTHER Datsun Z/LS3/T56 Swap Thread
Ironhead replied to Ironhead's topic in S30 Series - 240z, 260z, 280z
The radiator is a two row, 1.25" tubes, dual pass, 2.50" core. It has two huge Spal fans, but it seems more like airflow at speed is the issue. It holds temp very well at low speed and idle. I am going to start out with relatively simple ducting, and keep testing to see when adequate cooling is achieved. First step is to use some adhesive foam strips to seal the top and bottom of the radiator so air won't flow around the core. -
ANOTHER Datsun Z/LS3/T56 Swap Thread
Ironhead replied to Ironhead's topic in S30 Series - 240z, 260z, 280z
Agree that front end air ducting would definitely help. Putting the oil cooler behind the radiator would require massive modifications to the build in my case, as with fans and radiator plumbing there is almost no room. What do you think about a wide/short air-oil cooler in the opening in the air damn? That would clean up the flow to the radiator and also offer unobstructed airflow to the oil cooler... -
ANOTHER Datsun Z/LS3/T56 Swap Thread
Ironhead replied to Ironhead's topic in S30 Series - 240z, 260z, 280z
Took the car out in 95 degree weather a couple of days ago, and it wanted to over heat. Nothing catastrophic, but it started to get a bit warm when driven hard and I question it's capacity to withstand a warm day on track. My oil cooler location seems like an obvious first place for improvement. It clearly impacts airflow to the radiator, particularly once the oil is hot and the air passing through to the radiator is going to be very warm. There are a thousand other places I can put an oil cooler...and I figure it is time to experiment. The only real problem is that I will probably need a differently shaped cooler. Or a coolant/oil based heat exchanger. Opinions? While there is no question the radiator will work more efficiently with the oil cooler elsewhere, do you think it would be a huge difference or a subtle one? I know this is not the first application wherein an oil cooler is mounted in front of the radiator, but that is a damn big oil cooler.