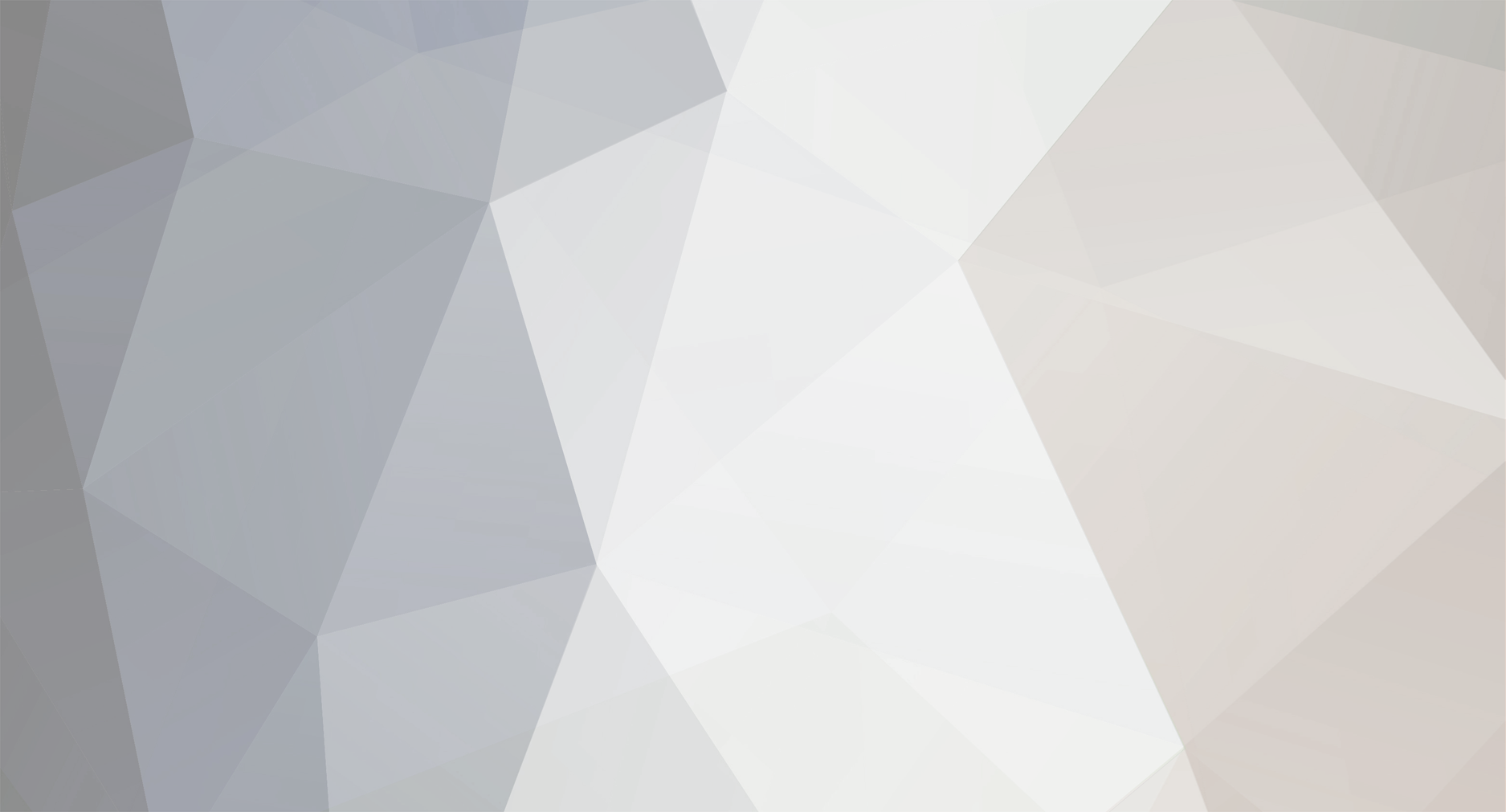
Ironhead
Members-
Posts
529 -
Joined
-
Last visited
-
Days Won
18
Content Type
Profiles
Forums
Blogs
Events
Gallery
Downloads
Store
Everything posted by Ironhead
-
280Z build w/ LS3 and 2015 Mustang spindles/8.8
Ironhead replied to 280Z-LS3's topic in Gen III & IV Chevy V8Z Tech Board
Sorry D1t...I don't completely follow. Did you precisely ream the TTT control arms, or arms of your own construction? -
280Z build w/ LS3 and 2015 Mustang spindles/8.8
Ironhead replied to 280Z-LS3's topic in Gen III & IV Chevy V8Z Tech Board
If your "Z" turns out similar to mine, you will find it equally unrefined. I'm actually a bit surprised how hot it gets inside. I have Lizard Skin temp control on the inside, and reflective heat shield in the trans tunnel, and it still gets really warm inside. Let's just say, a heater is unnecessary. I guess just a function of too much engine/HP/exhaust in too small a space. It's all good though. I knew I wasn't building a luxury car. -
280Z build w/ LS3 and 2015 Mustang spindles/8.8
Ironhead replied to 280Z-LS3's topic in Gen III & IV Chevy V8Z Tech Board
Dude! We're in Cali....I drive my project cars in the winter more than the summer.....LOL. As far as the steering....keep in mind that in addition to the 275 tires....I also have a significantly quicker than stock rack (can't remember the ratio)....the shorter Apex steering knuckles.....and 6.5 degrees caster. The steering is go-cart quick....maybe a bit too much, really.....but even once up to speed it takes a lot of effort to turn the wheel. My initial plan was to have the power steering go off at 15 MPH....but after driving it.....nope....power is staying on. I thought I wouldn't like the feel of the EPS....but it really isn't bad at all. You are right that there is a lot of confusion about bolts used in tension vs shear. In aircraft many bolt applications are pure shear, and AN bolts are designed to actually be used as such. That's why you can get 1/2 height AN lock nuts...because the tensile strength is irrelevant. But yes, on the TTT arms it is different, as the pivoting takes place in the Heim joints. I should have realized that failure to fully tighten the bolts would lead to clunking. -
280Z build w/ LS3 and 2015 Mustang spindles/8.8
Ironhead replied to 280Z-LS3's topic in Gen III & IV Chevy V8Z Tech Board
I really like your design for the hub uprights. While there is nothing inherently wrong with the TTT ones, they are needlessly heavy, and in fact I have noticed on their website that they now have a new design with a lot of metal removed to reduce weight. Yours look even lighter. Part of me hates seeing better designed parts, because it makes me want to bin mine and trade up. But I have to stay the course or this damn car will never be "finished".... Just a few notes about the TTT rear control arms/uprights....and I think would apply to your design as well.... I have been driving my car around quite a bit trying to iron out all the little details. One thing I have noticed is a fairly loud clunking from the back of the car as the rear suspension loads and unloads going over bumps. I "think" I have narrowed the source down to the long bolt on the outer end of the control arms....it goes through the two Heim joints and also through the tube at the bottom of the rear hub uprights. I didn't initially have this bolt super tight, just snug, because I figured it only needed to function in shear and I also didn't want to put a bunch of side loading on the Heim joints. But I think the clunking noise was caused by the uprights moving up and down on the bolt when driving over bumps. The bolt is a fairly precise fit in the Heim joints but pretty loose where it passes through the tube at the bottom of the uprights. So I carefully shimmed the long bolts to fully tighten them without putting a bending load on the Heim joints. I'm hoping this sufficiently stabilizes the hub upright tube and gets rid of the clunking. I was going to do a test drive today, but the potentiometer for my electric power steer decided to crap out, and the car is fairly undriveable without power steering....so I have to sort that to know if I succeeded in eliminating the "clunks" or not. -
Has anybody have problems dealing with ZCAR DEPOT?
Ironhead replied to toolman's topic in Non Tech Board
I've had good luck with Z car depot, bit I guess all businesses drop the ball from time to time. It is important to remember that many/most of these Datsun parts sellers are one-man operations. It doesn't give them much flexibility if they get busy or things go wrong. Many of them drop communication first when they get busy, which is 100% the wrong thing to do. TTT is definitely an exception. I've been in there several times over the past 4 years building my car, because they are only 30 minutes from me. At first it was a quiet shop with perhaps 3-5 people working. Now they are on fire, like a full grown factory. The shop is overflowing with inventory while perhaps 12-15 people struggle to fill orders. Good to see the Datsun aftermarket is booming. I know TTT sells parts for other cars, but I am pretty sure Datsuns are the bulk of their business. -
240z SCCA vintage race car, restoration
Ironhead replied to AydinZ71's topic in S30 Series - 240z, 260z, 280z
Very interesting project. I for one would like to see some higher res photos posted. Hard to discern details with the size you are using. -
Yeah, Honestly today what it really boils down to is whether you want to buy US made or Chinese. The US machines are significantly more expensive. Many life long hardcore welding experts will say the US machines are the only way to go in terms of long term quality and reliability, and that the Chinese machines won't last. But many also say that about Snap On tools, and I know that's no longer true.
-
I have a Miller Diversion 180. It's been great for my needs....but it has limited features and still runs about $2K...so I'm not sure it's exactly a great bargain.
-
IMSA GTU vintage racer build
Ironhead replied to clarkspeed's topic in S30 Series - 240z, 260z, 280z
Very interesting project, I will definitely follow. What year did IMSA allow sections of the GTU cars to be replaced by tube structure? I used to watch the races as a kid, and in '78/'79 they all still had the full OEM body that was reinforced with tubing. Sometime in the early-mid '80s, they were suddenly all tube frame "silhouette" cars with little or none of the OEM body remaining. I'm just not sure exactly when the change occurred. I wanted to also add, that is a huge project. If you can complete it in 12 months, my hat is off to you... -
ANOTHER Datsun Z/LS3/T56 Swap Thread
Ironhead replied to Ironhead's topic in S30 Series - 240z, 260z, 280z
Thanks for the link. Coincidentally, I called Essex yesterday and talked to their "brake pad guy"....might have been this same dude...not sure. Anyway, he told me that currently their closest thing to a perfect pad is the DS3.12....which is what I have installed. He asked me if I had heat cycled them yet, which I have not. He said he was very confident that once I had heat cycled them, their cold bite will greatly improve. My "Z" as set up is a bit of a challenge for brakes. I am definitely going to need high heat capacity on track as the car can build momentum very quickly. But as I still plan to street drive it, cold bite is an issue, exacerbated by the fact that it has no power boost. He assured me that once properly heat cycled, I will be happy with the DS3.12 pads....so my plan is to soldier on with them. -
Just a quick blurb: I think it is a mistake for any business to overly rely on Facebook. I don't FB, never will, because I disapprove of the company and their business model. Many, many others feel the same....
-
I agree with above, that it is more the reaction of the company to fixing mistakes that counts. Nothing in a small market like this is ever going to be developed and tested to perfection prior to release. I've had a lot of experiences with the "Z" after market while building my car, as like many here virtually nothing on it is OEM Datsun. I've had very clear and definite problems with several company's components, which I articulated and documented (including video) and communicated to the company that made them. The response, more often than not, has been crickets chirping. My "correct" response of course would be to not do business with them anymore, but that isn't always an option. Certain parts, unless I want to produce them myself, are only available from one or two companies. I don't want to mention the specific companies, because fairness would demand a detailed, exhaustive, and objective report that I don't feel like writing. I am NOT however, talking about Apex with these experiences. I know there have been problems with Apex products, but realistically, who is their competition? There are other suspension components out there, but none as complex (and probably over-engineered, IMHO) as Apex. So if the Apex approach is what you want on your car, you really have no options other than doing it yourself. Based on what I have read here, anyone who goes with these components had better expect delays and some snafus that they are going to have to work out themselves. I think it would be wise for Apex to offer the option of selling parts in bare metal form rather than powder coating them. It would make it much easier and simpler to do whatever modifications the end users need for their application.
-
ANOTHER Datsun Z/LS3/T56 Swap Thread
Ironhead replied to Ironhead's topic in S30 Series - 240z, 260z, 280z
Yeah I noticed that too. Each set of these pads costs $300-$500....trying new ones is getting expensive....lol I thought about putting in "street pads" and just swapping them out at the track. This would be a bit of a PITA, but the big problem is I don't think anyone makes street compounds for the AP calipers. -
ANOTHER Datsun Z/LS3/T56 Swap Thread
Ironhead replied to Ironhead's topic in S30 Series - 240z, 260z, 280z
I've tried both the 2500 and the DS3.12. Both to some degree have the "no cold bite" issue, but I found the DS3.12 to be the better of the two. I've used the 2500 in my other track car for many years. In that application it's been great. -
ANOTHER Datsun Z/LS3/T56 Swap Thread
Ironhead replied to Ironhead's topic in S30 Series - 240z, 260z, 280z
My current pads are good hot, but terrifying cold. Since I don't plan to trailer the car to the track, it's a problem. I'm probably looking for that magic bullet pad that doesn't exist. -
ANOTHER Datsun Z/LS3/T56 Swap Thread
Ironhead replied to Ironhead's topic in S30 Series - 240z, 260z, 280z
Out of curiosity, what pad compound do you use? -
ANOTHER Datsun Z/LS3/T56 Swap Thread
Ironhead replied to Ironhead's topic in S30 Series - 240z, 260z, 280z
Thanks. I remember your car has large rear flares. Do they get absolutely peppered with rocks? I think part of my mistake was driving the car without the front fenders installed...but I got rock chips on the front of the rear over-fenders and on the leading edge of the doors. There was literally like two fist-fulls of gravel deposited on the inside of the rear over-fenders. The front fenders will solve the issue with the leading edge of the doors, but in the rear I decided some kind of protective coating was the only option. I also made some tight fitting fender liners out of 1/16" ABS to somewhat control the flying rocks (I was going to forego this step in the front). I don't entirely get it. My other track car has Toyo R888s on it, and doesn't have this problem with thrown gravel. On the "Z" I am running R888Rs, which apparently are significantly softer. -
My first response to the fuel cell next to the driver's seat is horror, but why not I guess? Really no more dangerous than having it in the hatch area. Maybe safer, in terms of less likely to take a major hit. But don't the rules require a metal partition around it, and either braided steel lines or hard lines? Or am I all messed up and that's not a fuel cell?
-
ANOTHER Datsun Z/LS3/T56 Swap Thread
Ironhead replied to Ironhead's topic in S30 Series - 240z, 260z, 280z
I could have.... I already had significant rock chipping from one short drive. This would have needed touching up, or even a repaint...before PPF. I was blown away by the amount of gravel thrown up by the soft compound tires. The Raptor Liner killed two birds with one stone. I really like Raptor Liner. It is affordable, easy to use, durable, and simple to seamlessly retouch. I thought about doing the tintable Raptor Liner and matching the paint, but decided this is a track car, not a show car, and just went with black. I would have had to outsource the PPF work, and I have trust issues...what can I say? -
ANOTHER Datsun Z/LS3/T56 Swap Thread
Ironhead replied to Ironhead's topic in S30 Series - 240z, 260z, 280z
I added a couple of coats of Raptor Liner to the areas I knew would almost immediately receive rock chips if left unprotected. I'm not crazy about how it looks, but figured it's either that or pock-marked paint. Now I have to let the car sit for a while. Raptor Liner "mostly" dries fairly quickly, but remains soft for a surprisingly long period of time....I am going to refrain from driving the car for at least a week while it fully hardens. -
ANOTHER Datsun Z/LS3/T56 Swap Thread
Ironhead replied to Ironhead's topic in S30 Series - 240z, 260z, 280z
I think the Borla and Magnaflow straight-through mufflers are fairly equivalent. The key is just to have as much volume (large mufflers) as you can find a place for. I have two large Magnaflows under the fuel cell (lots of heat shielding) and they have good ground clearance. But, to accomplish that....I raised the fuel cell a couple of inches when I was designing the rear end of the car. Which, of course, raises CG a bit.... Everything is a tradeoff. -
ANOTHER Datsun Z/LS3/T56 Swap Thread
Ironhead replied to Ironhead's topic in S30 Series - 240z, 260z, 280z
This is the resonator(s) I used: https://www.summitracing.com/parts/vpe-1794 As far as ground clearance, I have a couple of low spots, but the header collectors are the lowest. I would like to see someone build 1 7/8" long tube headers and dual 3" exhaust without winding up with compromised ground clearance. I sure as hell couldn't find a way to do it. If you went with single 4" exhaust you could better tuck it into the driveshaft tunnel and pick up ground clearance without losing much (if any) flow, but the headers would still be a problem. I thought about making shorty headers...so the collectors could be higher up and not lower ground clearance, but I just don't think there is enough room to do it. -
ANOTHER Datsun Z/LS3/T56 Swap Thread
Ironhead replied to Ironhead's topic in S30 Series - 240z, 260z, 280z
I would say I am happy with it. Reasonably quiet at idle, pretty aggressive sounding when you step on it. Definitely quieter than I expected it to be....which is fine. I'm not really a fan of loud cars....even track cars. -
ANOTHER Datsun Z/LS3/T56 Swap Thread
Ironhead replied to Ironhead's topic in S30 Series - 240z, 260z, 280z
I got the front end of the car pretty much assembled.... The only drama I encountered was that with the 6 degrees of caster setting, the front wheels are far enough forward that they now interfere with the headlight buckets. So I have to sort that out one way or another. It's always something. Thanks for looking. -
280Z build w/ LS3 and 2015 Mustang spindles/8.8
Ironhead replied to 280Z-LS3's topic in Gen III & IV Chevy V8Z Tech Board
Sitting here with "brake envy"...telling myself "size doesn't matter"..... But seriously, everything looks really great. I wish I had done something similar with my engine mounts to allow for a larger scavenge pump. I agree with you, get wheels/tires in hand ASAP. Without them you will very quickly find yourself unable to progress with mockup. So much hinges on the wheel/tire setup. Also expect the wheels to take two or three times as long as Ryan "estimates". That was my experience, and is, from what I have heard from others, the norm.