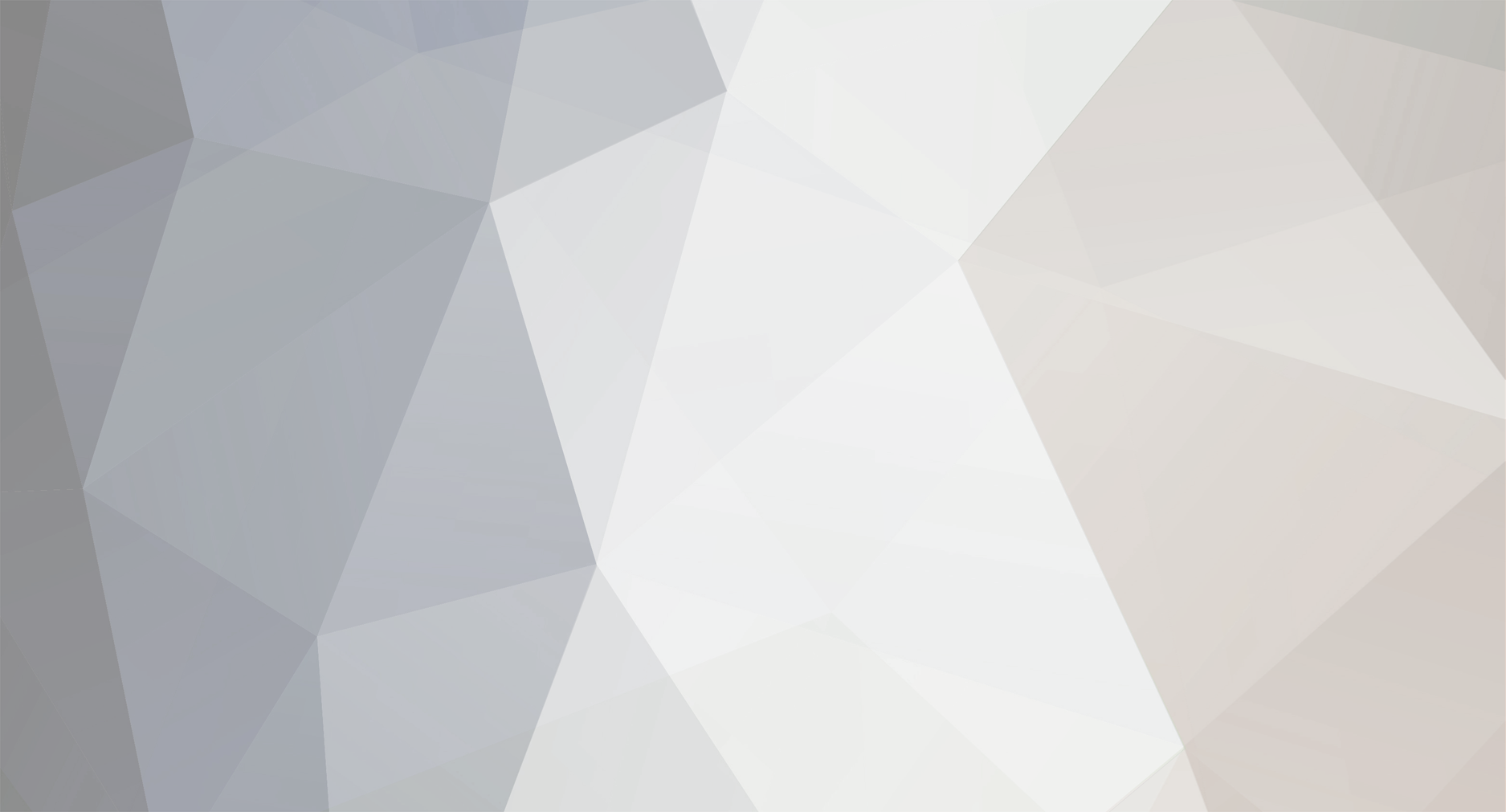
Ironhead
Members-
Posts
529 -
Joined
-
Last visited
-
Days Won
18
Content Type
Profiles
Forums
Blogs
Events
Gallery
Downloads
Store
Everything posted by Ironhead
-
ANOTHER Datsun Z/LS3/T56 Swap Thread
Ironhead replied to Ironhead's topic in S30 Series - 240z, 260z, 280z
I didn't. I've read several opinions that the Tri-Y design is likely to offer benefits over 4 into 1 on LS engines, but this was really a "how can I make things fit better" exercise rather than a quest for more power. I too would be curious about the differences between each design, but nowhere near curious enough to actually do it. The headers can be swapped with the engine in the car, but it requires some dismantling on both sides and is a bit of a PITA. Also, the 4 -1 headers won't mate up with the updated downstream exhaust. -
ANOTHER Datsun Z/LS3/T56 Swap Thread
Ironhead replied to Ironhead's topic in S30 Series - 240z, 260z, 280z
"Tri-Y" headers finished. Completed exhaust installed. So a few weeks work and I-don't-even-want-to-tally-how-much-money to gain an inch or so of ground clearance. I think maybe I have lost my mind. -
Looks great, I really like the color. I think the key to getting a good paint job as a relatively unskilled painter with marginal equipment and environment, is to put the clear on slightly thicker than normal (maybe three coats instead of two) and just plan on wet sanding/buffing the entire job. It is a bit of work to do, but actually goes fairly fast. It allows you to remove all the dust nibs, orange peel, and other flaws that you are bound to have no matter how careful you are. Even runs are fairly easy to sand and buff out. Basically by doing this, you are using your own labor (free) to make up for defects and flaws that come from lack of painting experience and facilities. Most professional paint jobs will not include wet sanding/buffing unless it is really a big money job, just because it is so time consuming to do.
-
ANOTHER Datsun Z/LS3/T56 Swap Thread
Ironhead replied to Ironhead's topic in S30 Series - 240z, 260z, 280z
Every method I could conceive. I pressure bled them multiple times, and also did so by pumping the pedal while doing the fronts simultaneously, then the rears. I tapped on the calipers with a plastic mallet to knock air bubbles loose. I bled them with the pistons in different positions.... Gradually the pedal got better and better....now it is rock hard, like standing on a brick. I wish I could tell you which step was the magic one....but I don't know. It was a PITA though, and it doesn't seem like it should be that difficult... The switch to .75/.70" master cylinders also helped a ton. My prior setup was just...all wrong. I also switched to Carbotech XP20 pads in an effort to improve cold bite. I only briefly drove on them before starting the exhaust re-do, but I can tell you they REALLY bite. Even completely cold, it almost felt like I had power brakes again. I need to break them in and test them a lot more to know the full picture....but they definitely work when cold. They also were squealing like I couldn't believe....but that might be due to lack of break-in. -
ANOTHER Datsun Z/LS3/T56 Swap Thread
Ironhead replied to Ironhead's topic in S30 Series - 240z, 260z, 280z
I haven't run it yet in its current iteration....just now finishing the headers. Hopefully will know soon. -
I agree about the post. Hard to put much credibility in it. I think the lithium Brailles are great for project/weekend/track cars that don't get driven often....IF (and this is a big IF) you have a cut-off switch in the car that completely removes the parasitic drain. If the battery is fully disconnected, you can ignore it for a year + and it will still have pretty much a full charge.
-
ANOTHER Datsun Z/LS3/T56 Swap Thread
Ironhead replied to Ironhead's topic in S30 Series - 240z, 260z, 280z
Well, there is a Y-pipe at the beginning and end of the large oval tubing, so as I read exhaust theory, it is like the entire center section is a giant X-pipe. -
Where to Order Stainless Tubing and Vbands
Ironhead replied to Dat73z's topic in Fabrication / Welding
I have some experience with this.... To some extent it depends on what you want/are willing to pay. It is not all the same. One of the problems I have encountered with the cheaper stuff is that the tubing is distorted more in the bends. So if you cut an angle out of the bend to weld to another piece of tube, you will find that the bent portion is not round and doesn't fit without a ton of tweaking. My #1 choice...also a bit more expensive...is SPD Exhaust. Everything they sell is US made, superb quality, nearly always in stock, and they ship same day. They do not have an "add to cart" website, so you have to call or fax/email an order sheet. Stainless Headers is good too, but they make everything to order and it usually takes 7-10 days to ship currently. Vibrant is another great source...never had a problem with anything from them. I've heard great things about Burns Stainless, and they have a great website, just never ordered from them. -
ANOTHER Datsun Z/LS3/T56 Swap Thread
Ironhead replied to Ironhead's topic in S30 Series - 240z, 260z, 280z
Exhaust V: 2.0...... I am trying to tackle my problem with the exhaust hitting the ground. First step was to make a new crossmember. It is basically the same design as the Hoke one I was using previously, just with wider and deeper exhaust recesses: This is what I came up with for the exhaust. There is a huge advantage, clearance wise, to building tri-"Y" headers, because the final 2 into 1 collector is much narrower than the 4 into 1 units, and thus can tuck MUCH higher up between the transmission/bellhousing and car body. This was the lowest point with my previous exhaust, and I would estimate with this setup that I gained 1.5-2" of ground clearance in this area...which is a ton. The problem I had with the mid section on my old system was that the two 3" resonators were too wide to tuck very far up into the driveshaft tunnel. With my new design, the center section is 4.5" oval tubing...slightly larger in area than two 3" tubes....so it should add no restriction. And, even with the 4.5" oval resonator it will fit up in the narrow part of the driveshaft tunnel as far as I wanted to put it. The only limiting factor is I didn't want it too close to the CF driveshaft. Building another exhaust is an expensive PITA for sure....but I didn't feel I had much choice. The tight ground clearance was seriously limiting the driveability of the car. Now I just have to build a couple of tri-Y headers..... -
While it pains me to admit it, I too switched valve covers primarily for aesthetic reasons. I wanted to get away from the "stock engine from a Chevy truck" look as much as I could. I also wanted to get rid of the oil filler cap, since my car is dry sumped, but that was mostly an excuse.
-
There comes a point....and I think Whitehead is there....where this sort of behavior becomes criminal...literally. Knowingly taking money without returning agreed upon goods/services, which at this point could be proven is being done with intent and pre-meditation, is prosecutable criminally. I don't know exactly how all this works in Canada, but it might be time for a call to the state prosecutor/district attorney/whomever in the area out of which Whitehead operates. I know most people would rather write off the loss and move on....which I understand....but think about the people who have been screwed who haven't posted to hybridz.....
-
Personally, of the Nor Cal tracks, I consider Laguna the most potentially fun to drive....but the sound limits have become laughable. Some new stock cars off the showroom floor won't pass unless the driver coasts past the sound booth. I find the politics that led to this situation so infuriating that I have vowed never to return there. Sonoma, to me, is the most challenging...by far. Thunderhill is nice because it is wide open. You could have a major "off" there and you are unlikely to hit anything or significantly damage your car. There are almost no walls or other obstacles.
-
IMSA GTU vintage racer build
Ironhead replied to clarkspeed's topic in S30 Series - 240z, 260z, 280z
I don't pretend to be an expert, but I experimented a ton with this on my build.... What worked best for me: When butt welding panels with MIG, make sure you have a small gap...like 1/32" or so...between the pieces. If you don't do this, the weld will remain on the surface of the two panels, and when you grind it flush you will have poor fusion and a million pinholes. Use .023 or .024" wire. Go hotter (like 15-20% over what the machine recommends) rather than colder, but make the weld extremely quick....almost as quick as you can tap the MIG gun trigger. If you are watching/guiding the puddle, you are going WAY too slow. If you time it right you get good fusion, the weld flattens out well, but nothing has enough time to burn away. Once you have adequate tacks to hold everything in alignment, continue the weld by building on the existing tacks. This makes it much easier. And...I agree with you....impossible to make it look super pretty. But most of the time you will be grinding it flush anyway. After MIG welding a lot of Datsun sheet metal, at least your other MIG ventures will seem a breeze in comparison... For me, it was using TIG on the Datsun panels that I found totally impossible. You need 100% perfect fit, and even then, TIG by nature is a slow process and I found controlling the heat adequately to be extremely difficult. I know many experienced welders recommend TIG for butt-welding body panels, but I think they are mostly talking about 18 gauge stuff. I would like to see them try it on a Datsun. I mean, I know it can be done, but it requires exhausting focus and concentration. -
ANOTHER Datsun Z/LS3/T56 Swap Thread
Ironhead replied to Ironhead's topic in S30 Series - 240z, 260z, 280z
I have about 400 miles on the car now, just gradually ironing out bugs... Last time I drove it, I noticed a (new) clunking noise coming from the rear on acceleration or deceleration. So, I figured it was time to jack it up and check things out, tighten bolts, etc. Well, when I did final assembly on the car I could not find my HUGE washers that went on top of the front diff mounts. So I used large thick washers, but not HUGE. You can see what happened below. The upward loads on the diff "circumcized" both of the mounts. Easy fix, and probably something I should have anticipated. The exhaust is a much bigger problem. I knew it was very close to the ground, and driving the car is really pressing the point home. It just hits the ground too much, too easily, and under too wide a range of circumstances. It's doesn't require road debris or a speed bump, just loading the suspension, like when you level out at the bottom of a hill, is enough. It's taking too much damage too fast to continue ignoring the problem. So I have abandoned denial and accepted that I have to do something with the exhaust. It's going to require new headers and modifications to the center section. Fortunately the back section/mufflers are fine and I can keep them. The only way I can think of to raise the header collectors is to make them a "Tri-Y" design. Then the final collector will be a two-into-one instead of a four-into-one. If arranged vertically, it would be much narrower than the four-into-one and I should be able to tuck it up quite a bit higher between the transmission and car body. As the car is now, the collectors are the lowest point. Most of the center section I plan to convert from twin 3" round to singe 4.5" oval tubing. It will have roughly the same area as the twin 3", so flow should not be restricted. There is even an oval 4.5" resonator on the market that is still narrow enough to fit within the trans tunnel. The hassle will be the transitions...from twin round 3" to oval 4.5".....then from oval 4.5" to twin oval 3". No such transitions are on the market, so I will have to just get metal in hand and figure it out. This is a huge PITA, and the exhaust is among the last things I wanted to have to re-do....but driving the car constantly cringing as to when it is going to hit the ground is no good either. So for those of you doing exhaust on a Z, when you think it is high enough, move it up some more! My goal is to have nothing lower than the frame rails....which may not even be possible. Time will tell. If I could just gain a solid inch, that would make all the difference in the world. -
I find it funny how people tend to put a negative slant on sharing poor experiences they have had with a particular company, like they should feel guilty doing so. You essentially had $3K stolen from you. If there is a company out there doing this sort of thing, other potential customers need to know about it, before it happens to them. IMHO the victims of these rip-offs have almost a duty to share it publicly. That's one of the great things about the internet. It's not a "smear".....just sort of a "buyer beware".
-
Stainless steel brake line problem
Ironhead replied to RDuff's topic in Brakes, Wheels, Suspension and Chassis
I've tried using SS tubing as hard lines several times in the past. While it's possible to do and make them leak-free, it's such a hassle that I will never attempt it again. IIRC (it's been a while) the only way I got it done was to constantly anneal the ends I was trying to form. IMHO, SS is too hard and is simply poorly suited for the job at hand, yet we still try to use it for the bling value (and partly for corrosion resistance). I have to admit, properly done SS hard lines look really damn cool. -
It's horrible on both ends. A customer gets screwed unjustifiably, and a once honorable and valued company (Whitehead was good to me) is irreparably damaged at best, about to go under at worst. Whether it's Paypal or a straight credit card purchase, I keep a close eye on the dispute deadlines. If they are approaching, I always file a dispute/claim, regardless of what the merchant claims or excuses they have. Unless it's a trivial sum of money that I am willing to risk. Long range, often international transactions, would be completely undoable without some sort of claim/dispute process. Shady merchants could rip off customers with impunity. I've disputed many, many charges over the years, and sadly many of these problems have been in the course of purchasing Datsun items.
-
Question about potential engine swaps
Ironhead replied to Projectcarguy's topic in S30 Series - 240z, 260z, 280z
I am just finishing an LS3 build. I chose the engine largely because I have another car with a highly modified four-cylinder, and I have always envied the small block Chevy crowd for the wide spectrum of affordable speed parts/engines available to them. Make no mistake though....if you are a fan of the S30 Z in anything resembling stock form, the LS swap changes the character of the car completely. In a very real sense it is not even a Z anymore. That can be either good or bad, depending on what your goals are. But in terms of power/torque per dollar spent, the LS is impossible to beat. -
ANOTHER Datsun Z/LS3/T56 Swap Thread
Ironhead replied to Ironhead's topic in S30 Series - 240z, 260z, 280z
On a related note.... Since with the small front master cylinder I was getting too much pedal travel, I started to analyze possible ways to improve the situation. When I plumbed the brakes on the car, I used entirely AN-3 steel braided lines....no hard lines whatsoever. Many were of the opinion that this would lead to a soft pedal. I started to wonder if this had something to do with my excessive pedal travel....if the AN3 lines were expanding under pressure, they would certainly contribute to the problem. I had a lot of hardware left over from plumbing the car, so I concocted a little experiment. I bought two six foot lengths of steel brake "hard" line. With adaptors, I connected one end of each to each of my two master cylinders. The other ends were dead ended into a bleed valve. So, basically, I had two six foot lengths of hard line with two valves to bleed the air out, which I did. Twelve feet is probably roughly the total length of brake plumbing on most cars. Once charged with fluid and bled, I stepped on the brake pedal with all the strength I could muster. The pedal was rock hard, not surprisingly. It felt completely immovable, like it was bolted in place. Then I repeated the experiment using AN3 steel braided Teflon line, exact same setup, two six foot lengths of hose, bleed valves on each end, bled, and attached to each master cylinder. This too resulted in an immovable pedal, rock hard, completely indistinguishable from the hard lines. Could there have been a miniscule difference in the pedals, so small that my foot could not detect it? Yes....but if your foot cannot detect it, who cares? Now there might be other good and sound reasons to use hard lines rather than steel braided Teflon, like cost or weight. However, I feel the methodology in this experiment was reasonably sound, and can state quite confidently that pedal feel is not a sound reason. I've read a lot of opinions on the internet that hard line should be used wherever possible, but it has always been the standard internet "cuz I say so"....or "so and so says so" reasoning. I have never seen anyone try a simple test like this that took perhaps an hour to do. So to anyone who thinks AN3 Teflon brake hose expands and causes a soft pedal, I call BS. -
Very sorry to hear this. A rebuilt diff and Quaife....you must be out something like $3K? That's horrible.
-
ANOTHER Datsun Z/LS3/T56 Swap Thread
Ironhead replied to Ironhead's topic in S30 Series - 240z, 260z, 280z
I've been having trouble getting the brakes adequately set up. Based upon tech advice a few years ago from one of my suppliers of parts, my starting master cylinder sizes were .612" front and .812" rear. The problem with this combination, is that the front cylinder moves so little fluid into the relatively large front caliper pistons, I get a ton of movement of that side of the bias bar. Conversely, the larger rear master cylinder, moving much more fluid into the relatively small rear caliper pistons, barely moves at all. The consequence is that the balance bar gets massively angled and effectively "bottoms out" before I can apply sufficient pedal pressure to get full braking front or rear. Clearly something was amiss... So I contacted support at Essex Parts (A+/massive kudos to them, BTW). He took all my data and subjective experience and said he thought my best starting point was to go with .75/.75 master cylinders. In an effort to understand what was going on, I plugged all my data into this calculator, that 280Z-LS3 brought to my attention a while back: https://www.tceperformanceproducts.com/dual-bias-calc/ There are some figures on this table that required an educated guess, but most was hard data. As I played around with it, gradually it emerged that the .612/.812 master cylinders made no sense at all for my car/setup. It provided much more line pressure/brake torque to the front wheels than I needed, and far too little to the rear wheels. At least, that's how it looked to me. After punching in a bunch of numbers, it indeed appeared my best starting point was either .700/.700, .750/.750. or .750/.700. If I wanted minimal possible pedal pressure, I could go .612/.612, but I had already found that would give very long pedal travel, possibly more than I had available before the pedal hit the firewall. This all definitely makes more sense. Most front and rear calipers, even aftermarket ones, are designed to be usable with OEM style master cylinders that are the same size front and rear. Many people using them will not have aftermarket style balance bar/dual master cylinder setups. I don't want to name which place recommended the initial screwy sizing, because I might well have messed something up in the data that I gave them. I honestly think that is more likely than believing that they got the math wrong. I already have a .75 M/C lying around, because I bought that for my clutch before learning it was a couple of sizes too small. So I am going to order a .70 for the rear and try that combination. If I did the math right, I should get maximum braking with something like 65# of pedal pressure, which "sounds" doable. Time will tell. -
ANOTHER Datsun Z/LS3/T56 Swap Thread
Ironhead replied to Ironhead's topic in S30 Series - 240z, 260z, 280z
Great input guys, many thanks. I think what I will do is take the damn splitter completely off while breaking in the car and ironing out bugs. Driving on the road, damage is inevitable. Or just leave on the ABS one until it destructs. Looking at the photos, I think even with six turnbuckles, the ABS still would not hold up. -
ANOTHER Datsun Z/LS3/T56 Swap Thread
Ironhead replied to Ironhead's topic in S30 Series - 240z, 260z, 280z
This is the smallest size that they have that would work....https://www.flatironpanelproducts.com/store.html?model_number=AHP-04038--B-250, unless I made it out of multiple pieces....which I guess I could. That's still less than a CF sheet that size. This stuff would work well....but DAMN....$$$$$$: https://www.mcmaster.com/sheets/composite-fiber-aramid-honeycomb-panels/ (they also are not "rated" to use outside) Even regular fiberglass sheets are expensive in the needed size...not to mention I'm sure shipping would further the pain: https://www.mcmaster.com/sheets/fiberglass/ I could make my own fiberglass panels....but...you know....mess and PITA. In a lot of ways plywood makes the most sense...it just seems so...redneck....especially if I didn't bother to paint it black....LOL. Or maybe some plastic that is much stiffer than ABS? -
ANOTHER Datsun Z/LS3/T56 Swap Thread
Ironhead replied to Ironhead's topic in S30 Series - 240z, 260z, 280z
I've been driving the car around a lot to get a feel for it, break in the moving parts, and iron out all the bugs. Among the bugs, the 1/4" ABS is not really stiff enough to use as a splitter. In the picture below you can see that it is already deforming in the areas not supported by the turnbuckles....and I have not yet driven the car over 80 MPH. It's kind of a quandary: The part is going to take a lot of damage and need to be replaced often, so CF would be too expensive. Maybe a flat piece of fiberglass will be my next move, not sure. I know some use plywood too. In the short term I might just remove the splitter. Driving on the street it makes the car significantly more unwieldy than it already is. Issues with the diff: The OSG LSD clunks and bangs horribly during tight, low speed turns. I mean it sounds like things are tearing themselves apart. I talked to an OSG tech, and apparently my decision to use Motul gear oil during break-in rather than the $50/quart OSG oil is the main cause. He said the Motul will work fine and protect all the parts, but that it will make the diff extremely loud, particularly during break-in (500-1000 miles). So I guess I will ride out the noise and change to the OSG oil once things are broken in. I am also questioning my decision to install a diff pump/cooler. Just driving around for an hour or so, the diff temp rises to around 200 degrees and stays there. I'm sure track use will heat it up more, but track day sessions are typically only 20 minutes, and the OSG tech said their oil is fine to around 270 degrees. I doubt mine would get that high during track days, and if it doesn't I am going to yank the pump/cooler in the interests of lighter weight and simplicity. Still not happy with the brakes. Once up to temp after some hard braking, they work pretty well. But, when cold they are a bit scary. All this would be fine on a pure track car, but it isn't a pure track car. This is with the Ferodo DS3.12 compound front and rear. My next move is to try Carbotech XP20 pads. The DS3.12 pads have a friction coefficient between .50 and .55 once up to temperature, but Ferodo doesn't state their "bite" when cold. I will say it's "not much". The XP20 pads supposedly have a .70 friction coefficient at all temperatures, which is about the highest bite of any brake pad material. So I'm hoping they will give adequate cold bite and lower pedal pressure a bit at all temperatures. Have to try them though, I'm sure there will be a downside of some sort. Otherwise, car is running well. No overheating or other problems. I've never driven a completely "stripped" car before, and sometimes I feel like I am driving in a garbage can, but I knew full well that was coming. Thanks for looking. -
280Z build w/ LS3 and 2015 Mustang spindles/8.8
Ironhead replied to 280Z-LS3's topic in Gen III & IV Chevy V8Z Tech Board
Ahhh...that makes sense then. Good work BTW.