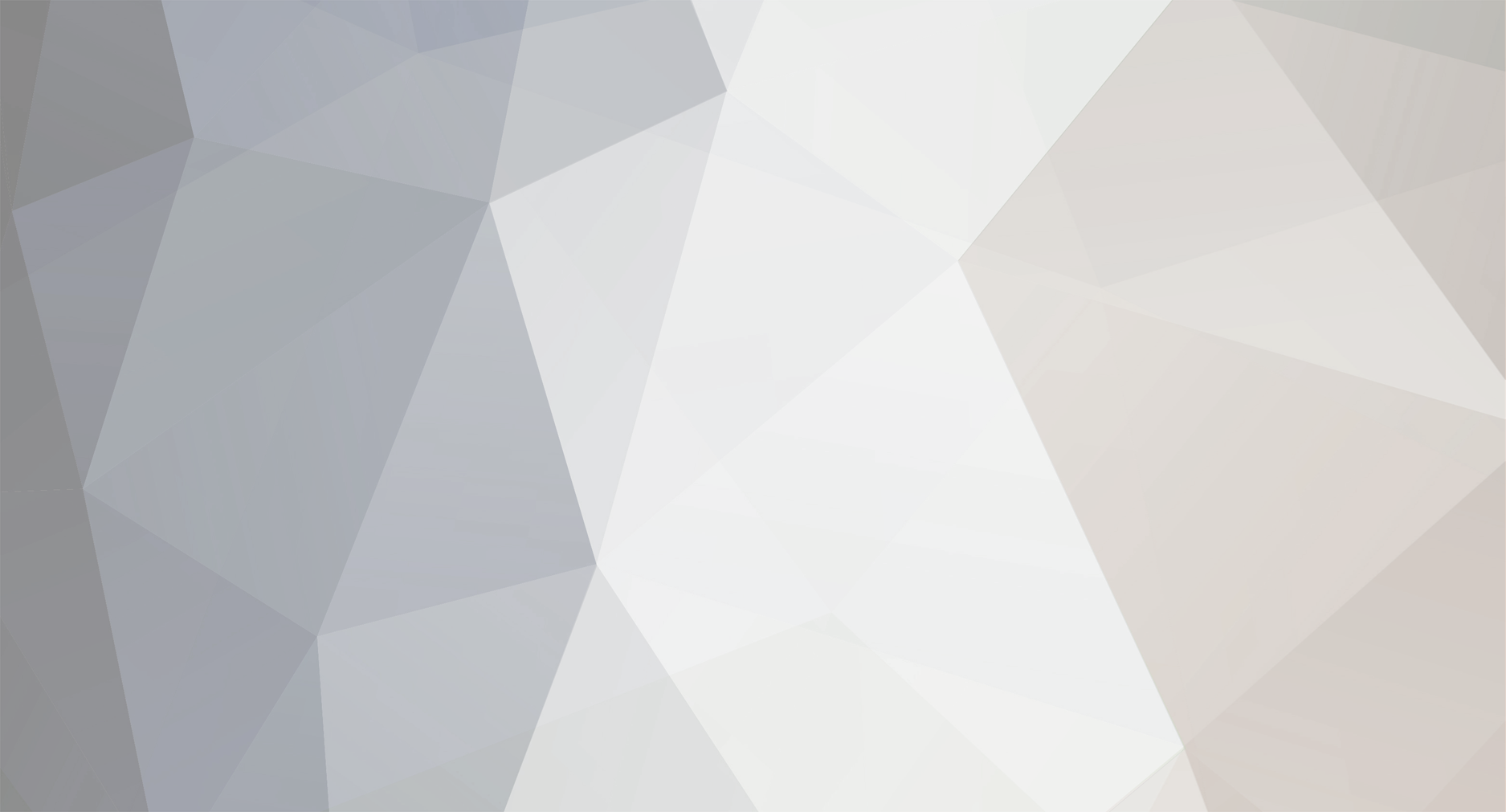
NewZed
Members-
Posts
6681 -
Joined
-
Last visited
-
Days Won
70
Content Type
Profiles
Forums
Blogs
Events
Gallery
Downloads
Store
Everything posted by NewZed
-
Anywhere between the fuel filter (a sizable pressure drop from the pump pressure) and the carbs would be fine. You want the gauge to show the pressure that the carbs see. That's what you're trying to monitor and control. Carburetor fuel bowl pressure.
-
The engine management system is designed for a certain flow rate. http://www.fuelinjector.citymaker.com/Fuel_Injector_Flow_Rates.html http://www.rceng.com/technical.aspx
-
bradyzq makes a good point. The ECI control conditions are described in the usual place, including O2.
-
I'm just going through the basics. Seems like you have them covered. I'd separate the stuff that affects cruising mileage from things that don't. Like "running 12psi intercooled" doesn't have much to do with cruising at 70 / 2600 RPM. Then there are the basic tuneup items, like valve lash and ignition (clean plugs, no misfires, etc.). That's about all I have. Sleeper is the standard, maybe he's got something.
-
All that matters is the relation of the camshaft to the crankshaft with the straight side (driver's side) of the chain straight and tight. The chain links just end up where ever once things start rotating. The bright links are just a convenience for chain installation. The effect of cam timing on power is well-documented all over the internet. What's probably going on is that the guy you bought the engine from moved the sprocket to #3 to get more low end. You probably have a race cam that will never work well at low RPM. Or there's something else not right and you're just focused on the wrong thing. What's your ignition timing set at and what's the advance curve of the distributor? Is it working right? Carbs or EFI? Cam timing doesn't seem like the source of the problem. http://www.compcams.com/Pages/413/cam-timing-lobe-separation-angle.aspx
-
So this is an aftermarket cam. You should set it up the way the manufacturer recommends. Although most cam shops use the stock factory marks. So the notch and groove are still relevant. Also, your thinking seems to be backward. Advancing cam timing moves the power curve to lower RPM. You said that you should have more power at low RPM, "no power below 5k". So you're going the wrong way to get more low end. Nissan set the holes up so that each higher number advances cam timing to make up for chain stretch. You're already maxed out to get more low end. If the head was off the engine, you could put a wrench on the sprocket bolt and spin the cam pretty easily, with all valves and springs installed. You're probably just being too careful. BUT, you're still missing the point about the holes only being 4 crankshaft degrees apart. That's only 2 camshaft degrees. You already have 10 degrees of movement. Why are you trying to rotate it farther? You should stop what you're trying to do and study up. You're wasting your time.
-
The O2 sensor still seems like the place to focus. Are you using the one for the L28ET, the VG30E, or the VG30ET? The VG30ET ECU expects a different type than the other two. Just asking. I never really know what people mean when they say they "did the test and it passed".
-
Posts that begin with "sigh" are almost always irritating to read. It's so hard being superior... Just realized I'd seen that "sigh" before . Six Shooter is the only guy that knows how to tune a GM Engine Management system correctly. It's easy. Or rather, it would have been if he'd finished. Weird how things repeat.
-
So what is the relation of the notch to the groove then? If the engine runs why would you pull the head? The logic train has no tracks...
-
Define freely. The shiny mark only matters during the first installation. Once the engine turns it will only line up occasionally. The notch and groove are what you use on a complete engine that has been turned. Seems like you're not really sure how things work, be careful. Read the Engine Mechanical chapter to learn about the notch and groove. Study the valve train parts to see how the parts work together. The springs close the valves and the cam lobes open them, against spring pressure. So of course the springs will resist. But there are also springs trying to close valves that are already open. It's a wash. If you can only move the cam shaft +/- 10 degrees, something's more wrong than cam timing. But you shouldn't need to move it that far anyway to switch holes on the cam sprocket. You're going to bend a valve if the head is installed. Did the engine rotate before you decided the cam sprocket needed moving? Edit - just realized, considering all, that odds are high the problem is bent valves. Might be too late for cam timing adjustment.
-
It's a start. A few observations: - 36 psi at 19 inches of vacuum is too high. Maybe you were reporting two separate things. Added a chart from the 1984 FSM. 36 is about right with the vacuum line to the FPR removed. - there are six years of Z31. Which year do you have? - You can check your odometer via mile markers on the freeway at any speed. - Extra resistance can make a difference on the CHTS circuit. "Functioning correctly" is not the same as optimized for efficiency. Always good to check the chart. Just some small things that might add up. There's also a test procedure for verifying that the O2 sensor is working right. I don't know how bad the sensor has to get before you get a code, with the early ECU's. Later ECU's like my 95 Pathfinder will tell you that the O2 sensor is bad. Might not be so in early 80's. But that's where you can lose a lot of efficiency, the ECU uses the O2 sensor to trim the fuel mixture as lean as possible. Sleeper can help you with the fine details of getting it running best since he has one. I only know generalities.
-
He hasn't even established that his is set up right. Each of my questions is relevant to determining if it is. Doesn't matter if you or anyone else got 29 mpg. Could be that yours is actuality set up incorrectly, down on power, but up on gas mileage. Who knows. All that's here so far is one Z31 ECU with 19 mpg, one with 29 mpg on one trip, and one "same here" (converted to "regularly"). There's nothing here to work with. Let's get some facts.
-
He said he's trying to move the cam shaft. Should move pretty easily with a wrench or big pliers on one of the knobs (the rough part of the casting) on the shaft itself. Why he's looking at the dowel position with the crank at zero timing (#1 at TDC) is a question though. Should be looking at the notch and groove.
-
Sounded like you made an adjustment, things worked right, then they didn't work right. Not clear what's happening, or what the final state of the situation is. Anyway, the hydraulics should never hold pressure after you release the pedal, unless you have the rod to the MC extended to far. All pressure is released in to the reservoir when the pedal is up, on a properly adjusted setup. Someone just posted on this. If you can press the slave cylinder piston in by hand (that's what they did, it's a good test) and fluid gets pushed in to he reservoir, there's no way pressure can be maintained by the hydraulics. The problem is between the fork and the pressure plate. If you can't press the cylinder in because the slave cylinder rod is too long and piston is all the way back, that would be a problem, but with the adjustable rod, should be fixable.
-
I was asking the OP.
-
For every person who says they get 29 there's another guy who gets 20. 20 is the most common number I've seen. That's combined city/highway though. You're running an ECU designed for a different engine, one that should have EGR, and O2 sensor feedback. Do you have an O2 sensor connected to the ECU or are you just using one for AFR readings? Is EGR functional? Are you getting any codes from the Z31 ECU? Have you checked CHTS readings to be sure they're correct? Are you using a stock FPR or adjustable or an FMU? What is fuel pressure? Did you put the system together or buy it that way? There are lots of tuning tricks you can do to increase MPG. A simple one is to reduce fuel pressure. But that will have other effects also.
-
Could be that the TOB collar is too tall as you thought, and that expansion when everything heats up is causing the slipping. If you let it cool and it starts working right, then slips when it gets warm, that would be a clue. If so, that can only be fixed with a shorter TOB collar. You have an odd assortment of parts so nobody can really give you a combination of parts that might work. With the stock flywheel, the collar ears (where the fork rides) should be 92 mm +/- a few from the surface of the flywheel (bottom of the pressure plate cover). I'd guess that Fidanza dimensioned theirs for a straight swap, so 92 should work for you too, but who knows for sure.
-
Without knowing how many were sold these facts are meaningless.
-
cog·ni·tive dis·so·nance nounPSYCHOLOGY the state of having inconsistent thoughts, beliefs, or attitudes, especially as relating to behavioral decisions and attitude change.
-
Isn't the fuel added at the start of the runners? The pseudo-carb? Should be the same ratio for all, unless air is slipping by without picking up fuel then passing to individual runners unequally. With mulitport injection, you could see a runner air flow imbalance. but equal fuel injected for all, leading to varying AFR per cylinder.
-
Modern ECU's will hold the idle speed up to charge the battery, among other reasons. 2500 seems high but who knows what your algorithm is. And the idle speed was probably controlled by the Idle Air Control Valve. Lets air past the throttle blade, electrically controlled by the ECU.
-
At last you're not focused on AFR's. From too wet to too dry. Still no plug examination. The old counting horse teeth without looking inside challenge...
-
Then your plugs would be wet with fuel. Don't trust the gauge if you don't have to. You'd most likely smell gasoline also.
-
You've been lulled in to the false sense that the computer or phone screen will tell you all that you need to know about the outside (inside in this case) world. Happens to all of us. I've found myself checking weather pages to see what's happening outside instead of just opening the door. Remove a spark plug and look at it to see if you're flooded. Use a timing light to see when spark happens. Check fuel pressure with a gauge. Real touchy-feely stuff, right at the actual engine.