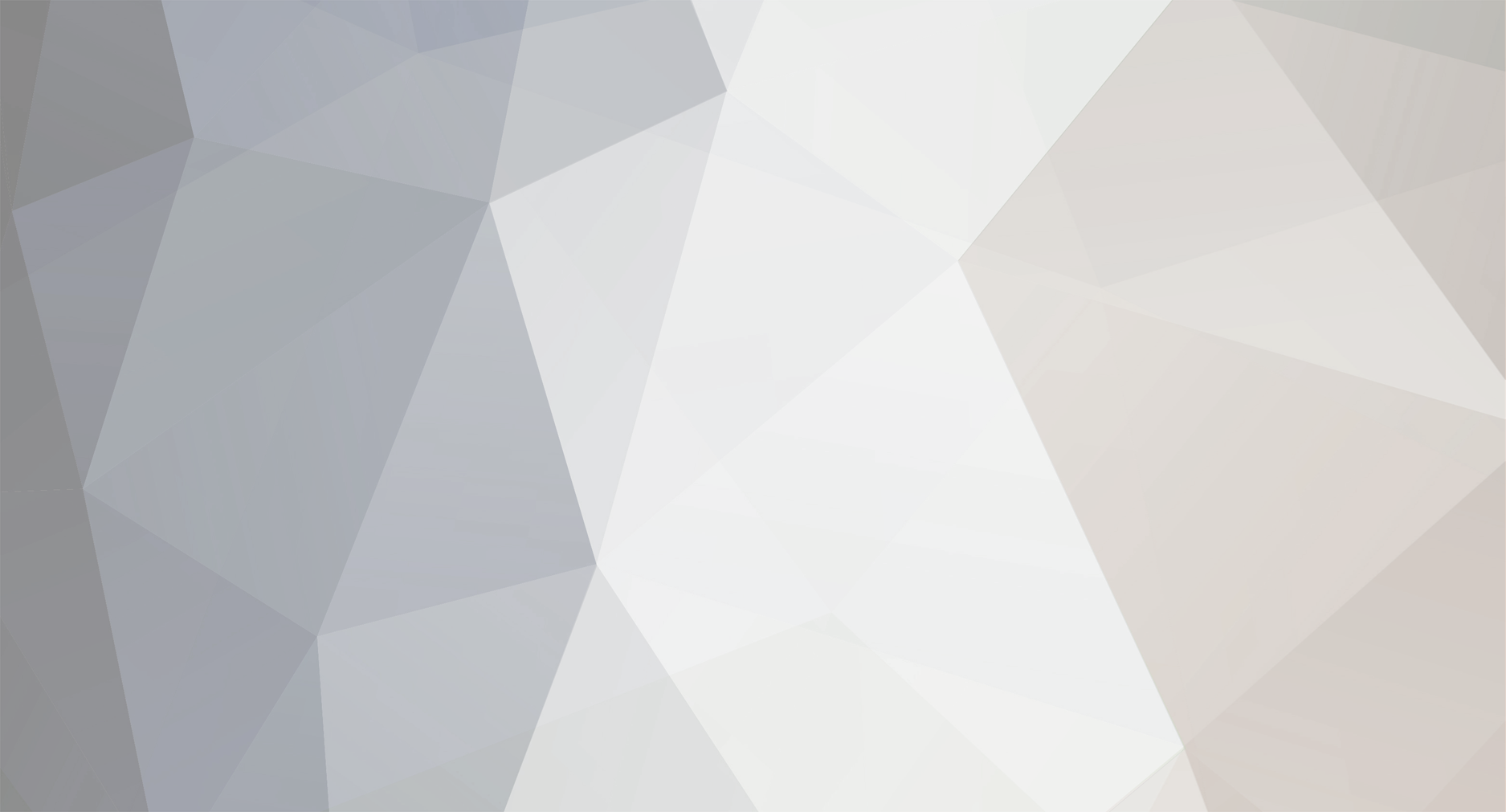
tube80z
Super Moderators-
Posts
1394 -
Joined
-
Last visited
-
Days Won
30
Content Type
Profiles
Forums
Blogs
Events
Gallery
Downloads
Store
Everything posted by tube80z
-
You have a really nice car. It would be a shame to try and hack it up to run in EM. As mentioned below you have two options for classes, XP and SM. SM doesn't allow for any chassis mods outside of strut bars and a basic cage as I understand it. XP allows more freedom on the chassis but you can't mess with the firewall. Your car could fit in either class and probably be fun to drive and locally competitive. To be nationally competitive is a whole another story and would require a completely different direction I'm afraid. If you like to drive your car on the street and do track days then I'd look at SM. If you have to put it on a trailer and run on slicks and do autox/track days then XP is probably a better match. EM will require that fabrication become your hobby and you'll most likely end up with a silhouette of a car. If you really want to run in EM I'd either fund a rusted out junker or just build from scratch and put a fiberglass funny car style body on. As mentioned below the best way to pick springs is by frequency. For a more streetable car I'd look at springs in the 2.5 to 2.75 Hz range (most likely 300 to 400 lbs/in). You'll also need inserts that can deal with this and ideally you'd want something custom valved. It's not as big of an expense as you might think and money spent up front is going to be better than buying three of the same part. I'm sure you already know that pain. For an XP car on slicks it really depends a little on the tires. I'd probably start at 3 Hz for a sedan/GT based tire and look at going stiffer. If you run the FA tires then I'd look at springs in the 3.3 to 4.5 Hz range (that's very stiff and requires very good shocks). And to run rates that high you really need to have a cage that ties the car together. So the easy route would be to start in SM and then progress up. But truth be told you won't be much faster in XP than in SM unless you do some serious work to make all the new bits work together. There are a lot of really smart people on this board that can help point you in the right direction to go faster. But the ROI quickly goes south. For bushings you really want to look for other options than poly. The stiction is way to high and that hurts grip. Where ever you can it would be good to change over to rod ends/monoballs. Again this all depends on class. We're all happy to share what we know around here. Hopefully this helps. Cary
-
One option I haven't seen discussed is to put an X in the floor. Very common in the pro touring car categories (BTCC, V8 supers, etc.) For about the same weight as the subframe connectors a lot of people put in you can increase the stiffness a lot. Ideally this should tie into the cage completing the bottom. The rocker reinforcement shown on Dave's car was at my prodding. We had a hillclimb accident where the driver was seriously injured because this area folded up and struck him. The door bars did their job but the rocker and floor gave up. He now has a limp and was off work for about a year. If you look at newer cars this area has been massively reinforced compared to the Z. Cary
-
A friend glued the window on his 280Z chump car. It worked great and we saved a nice gasket from being wasted. Oddly the car drove very different before and after. Gluing in the windshield makes the car stiffer and at least in this old clunker you can feel it. cary
-
Auto-X tuning ideas, want feedback
tube80z replied to wheelman's topic in Brakes, Wheels, Suspension and Chassis
You've already gotten a lot of good info so far. One thing I found is that my car worked much better when running stiffer springs and less bar on surfaces that had less grip and/or when it was damp. I would be looking at 100 to 150 more in spring rate and a much smaller front bar and possibly no rear bar. You can then tune it using rake (lower the end for more grip/raise the end to take more roll stiffness). That's a better way to balance the car than reducing traction on one end. For autox the quicker the car will transition the faster it will generally be. I'd look at how much droop you have with the spring seated and see about removing some of that with a limiter. I'm guess you have somewhere around 1.75 inches of droop presently. Try removing 3/4 of an inch and see what you think. It should be an easy and cheap thing to try. And another things most people don't understand when changing only one thing at a time is a change in springs requires a change in ride height or you have not changed one thing at a time. BTW, to go faster you really need to start looking at reducing friction on the suspension. That means getting rid of poly and any bind you may have. That's where the next big gains will come from. Cary -
I would see a couple of advantages to this. It should keep the tires flatter on the ground and if done correctly would have a roll center that moved with the car in a 1:1 relationship. Unlike the strut that moves at a different rate. I could see this making the car feel more stable in corners when putting power down or when trail braking. And I could see that making the car quicker just because the driver feels more confident. Cary
-
Suspension alignment tools for the home garage
tube80z replied to Zmanco's topic in Brakes, Wheels, Suspension and Chassis
We use toe plates at the track and can get within a 1/16th with them. That's measured on an alignment rack after the fact. I can't see how you need to be more accurate than that. My preferred method is to use parallel strings. Tom Holt had a good design I stole from his site (thanks again Tom!). -
bump steer spacer question btwn zcc or msa
tube80z replied to nissun1's topic in Brakes, Wheels, Suspension and Chassis
I'd read some of the stickies and do some searching much of what you're asking has been talked about many times. The spacers change the roll center height and where you are on the stock curve. My only criteria would be the thickness of the spacer and quality of the hardware. -
Suspension alignment tools for the home garage
tube80z replied to Zmanco's topic in Brakes, Wheels, Suspension and Chassis
I have the smartcamber and it works very well. It's been at the track for a number of years with no problems. It measures caster by checking the camber at a specific inner and outer steer angle. If you download their instructions you can see the procedure. You could probably do the same thing by using a carpenters square, a tape measure, and some basic trig. I' quite happy with mine. Cary -
I think most people never make it past step one.
-
I don't really want to get into a FWD/RWD battle but BTCC is interesting. If you watch much of it you can see the BMWs often make up a ton a places on the start and then struggle until about mid race where they get strong again. The FWD cars are much harder to get off the line and then are often very quick but seem to lose pace towards the end of the race. And certain tracks are seem to favor certain configurations. At least in this series the different configs use the tires at different rates and that often has a lot to do with the outcome. And in single lap qualifying there's often very little difference between the two even when you figure in ballast. Cary
-
I need suspension help
tube80z replied to Matt 78Z's topic in Brakes, Wheels, Suspension and Chassis
Rake is a powerful tuning tool. You can use it to balance different spring setups Generally you want to lower the end that isn't sticking but you mustn't overdo it. Most cars will respond to 2 to 3 turns on the spring mounts. For the understeer problem you've been given many things to think about. If you can get some pictures of your car under load in a corner where it is pushing that would really help us point you in the right direction. If you haven't noticed almost all the suggestions are around making sure the front tire has proper camber when loaded. On a Z roll is something you need to aggressively control or the tires will end up in a positive camber placement to the road and you will lose traction. Cary -
I need suspension help
tube80z replied to Matt 78Z's topic in Brakes, Wheels, Suspension and Chassis
It was a discussion we had some time ago about increasing installation stiffness. I tried searching but couldn't find it. This mod was quite common on many of the higher end Zs that raced in the 80s. I'll have to see if I can get you a picture of the rear mod they did. It was a bridge plate similar to the front. It might have been in the same discussions where the rear suspension braces were talked about (bridging tranverse link to the mustache mount). -
Woodward power steering project
tube80z replied to JMortensen's topic in Brakes, Wheels, Suspension and Chassis
25% underdrive balancer is 6.25 inches in diameter. I got mine from Scoggin Dickey and it's an Australian powerbond brand. I needed the extra clearance this gave the the stocker was almost touching the datsun rack I used as a mockup. -
Cables will work but they are not always the easiest to adjust. In another post you were looking to be able to make changes to droop and see how that made the car handle. Your turnbuckle may have anywhere from 200 to 400 pounds of tension on it depending on your spring rate and the amount of droop you're allowing. And to adjust length you will need to hold one end or the entire limiter will try and twist on you. It can work but isn't a super quick I want to change from 3/4 inch of droop to half an inch and test. At an autox you typically don't have a lot of time and may find removing the wheel, adjusting the turnbuckle, putting the wheel back on, and measuring droop takes too long. My new car will have a mechanical system like a reverse bump stop. This should allow me to be able to set the droop based the stop clearance. And I could build a simple step gauge to try different amounts of droop quickly at the track. In my case I'm looking t integrate this into the front ARB. Cary
-
Have a question about weight transfer
tube80z replied to OustedFairlady's topic in Brakes, Wheels, Suspension and Chassis
John's reply has a lot of good info. Maybe this will help too. The suspension movement really has little to nothing to do with the overall weight transfer. That's a function of CG height and wheelbase. But where it will make a lot of difference is on how the car is used. Using a RWD road race car as an example you may want it to squat when coming out of a corner. When the rear suspension drops the RC generally lowers, which would shift some of the roll stiffness forward. This would allow the rear tires to have more longitudinal traction if they are not fully utilized and help the car come of the corner harder. For a FWD car you might want to try the opposite of this. The other thing to keep in mind is the geometric changes cause load to transfer much quicker than spring/shock/arb changes. These can have an effect on a car over a longer run where they may heat up or overheat a tire by working it too hard. And an example where we may want to use a lot of antisquat is on a car that needs to keep a certain ride height (underbody aero). In this case the aero is more important than the mechanical traction. In a lot of the newer books and publications they are not looking at a single axle as much and talking about pitch centers. It's kind of the same thing but looking at what happens the car overall. Hope this helps, Cary -
Braces on the rear control arms
tube80z replied to 280z"Vador"'s topic in Brakes, Wheels, Suspension and Chassis
-
Toe Changes for Track Use
tube80z replied to heavy85's topic in Brakes, Wheels, Suspension and Chassis
From what I remember of the Roulle seminar the ackerman versus anti-ackerman argument depended on the tire construction. It had to do with how the peaks of force versus slip angle changed. So what works on one set of tires may not necessarily work or be right for the next set. Neil Roberts didn't think it was too important for road course work but also mentioned you might as well set it at 100% to make pushing the car in the pits easier. My personal feel is this will be more important for tracks with slower corners and more steering angle (more autox like). -
First impression of Formula Atlantic slicks
tube80z replied to 74_5.0L_Z's topic in Brakes, Wheels, Suspension and Chassis
I've had more experience with Kumho than Hoosier street radials. In watching a few local guys it seems like the Kumhos may not be as quick but they last much longer, often to the cords. For the GY slicks the new radials are light years faster than the older bias plies. I would not even consider bias slicks if you have the new option. In back to back tests the radials were three quarters of a second faster on a 46 second course. We only changed camber for the radials (similar to what a Kumho/Hoosier would run). The only downside is they are heavy and a ***** to mount. Compared to Hoosier/Avons the GYs are currently the quicker tire. Cary -
autox/track 280z roll centers
tube80z replied to mustard-z's topic in Brakes, Wheels, Suspension and Chassis
Dave's running 436 WHP and 430 WTQ on the 36 with no problems. Neither he nor I were very kind to it this summer. The real downside is ratio choices compared to the 44. On the plus side the price is a lot less. Send me a PM and I can get in contact with Dave/Sonny. Cary -
autox/track 280z roll centers
tube80z replied to mustard-z's topic in Brakes, Wheels, Suspension and Chassis
Either above or below ground can be made to work. The are some subtle difference and some major ones. Geometry transfers forces quicker than springs/shocks/bars. This can be felt by the driver and a key tool in changing balance. Generally above ground RC will generate higher tire temps and raise the front of the car as it rolls. My advice would be to make this adjustable if you can because if you change tires or do more track days. If you can't I'd shoot for running the lower control arm level. If I had to be pinned down on a range I'd pick someting like -2 to +3. The rear RC definitely needs to be adjustable in my book. Lower to put power down and higher to get the car to turn. You have to manage the loading of the rear tires so that they don't get overheated but still let the car turn and put power down. While this isn't adjustable in a stock configuration I would make sure you take this into account on the C4 rear end. It will also let you experimentally determine what works best with the front suspension, in case you don't have time to make it adjustable. There's a good thread at corner carvers that shows a bunch of C4 geometry. It's listed under putting this into the rear of a Mustang. Dave and Sonny run this rear in different cars in Medford. From what I was able to gleam the C4 uses a ton of rear antisquat to keep the suspension from bottoming, which is a consequence of spring rates picked for a flat ride. Removing most of this makes them work better. On Dave's locost the difference between mounting stock and making the links adjustable made a large difference in how well the car put down power. Install with the halfshaft near level and build adjustable inner brackets (or buy the ones from vette brakes). This will let you change the rear RC. I'd also make sure you have some leeway in being able to raise or lower the batwing and the front mounts. We learned this the hard way. I'd run less than 20% antisquat in the back. Also get rid of the stock spring and go to coil overs. It's a lot easier to setup and work on. Cary -
When you mention 1 inch of droop is that total or how much you reduced it by? On 550 Pound springs my car had a little less than 1 inch compression. In the rear I typically set the limiter so that I can slide a 0.040 feeler gauge between the spring and seat (like adjusting valves). In the front I was running around 5/8 to 3/4 total droop. On a really smooth track sometimes less and if really bumpy setup the same as the rear. I didn't have any of the jerkiness you describe. I'm guessing with your softer springs you need more droop in the rear. Try the procedure above for the rear and I think you'll find it helps. We accidentally eliminated droop from a friends car in and it behaved very similar to what you're seeing. So that's my long winded way of saying I think you're on the right track. Cary
-
Well we won't accuse you of not trying a few changes For tire temps you really need to get down in the rubber. I measured surface temps and they often were cooler and closer together than down in the rubber. As Jon mentioned the key is getting to them quickly after you've been loading the tires up.
-
Looking at your pressures shows me that you're working the front end much harder than the rear, which you would see as understeer. Ideally the front and rear will build pressure at a very similar rate if the setup is balanced. As a first step I'd go stiffer on the rear springs and add some rake. More camber won't hurt but the pressure rise should stay about the same. If/when you get a pyrometer and average temps you should see a similar trend. Hope this helps, C
-
I had a similar weight distribution on my 240Z when I ran the FA tires and that makes it very out of square. What I found was that I could tune the car to allow for extra cornering grip and still take a lot of throttle. This proved to be quicker than running the car square with four front tires. I was never able to get four rears to clear everything to see if that was faster. I'm not saying that one is better than the other but I think driving style plays a lot into this too. But if you look at a number of racing cars there are a lot that run staggered setups that don't necessarily have rear bias. But then again there's the acura LMP1 car that got a lot quicker by going square. Definitely something that will need to be tested this next year. Cary
-
Looking at your pic it appears you don't have enough camber on the loaded side. If you don't have a pyrometer you can also look at air pressure rise. The end that is being worked the hardest will show a larger increase in pressure. Did you track this at all? Your setup doesn't mention coilovers but if you have those I'd try raising the rear of the car (start with two to four turns). This should raise the rear RC up, which should shift balance towards the rear. You could also try lower the front but make sure you don't go too far or the turn-in will get lazy. Hope this helps, Cary