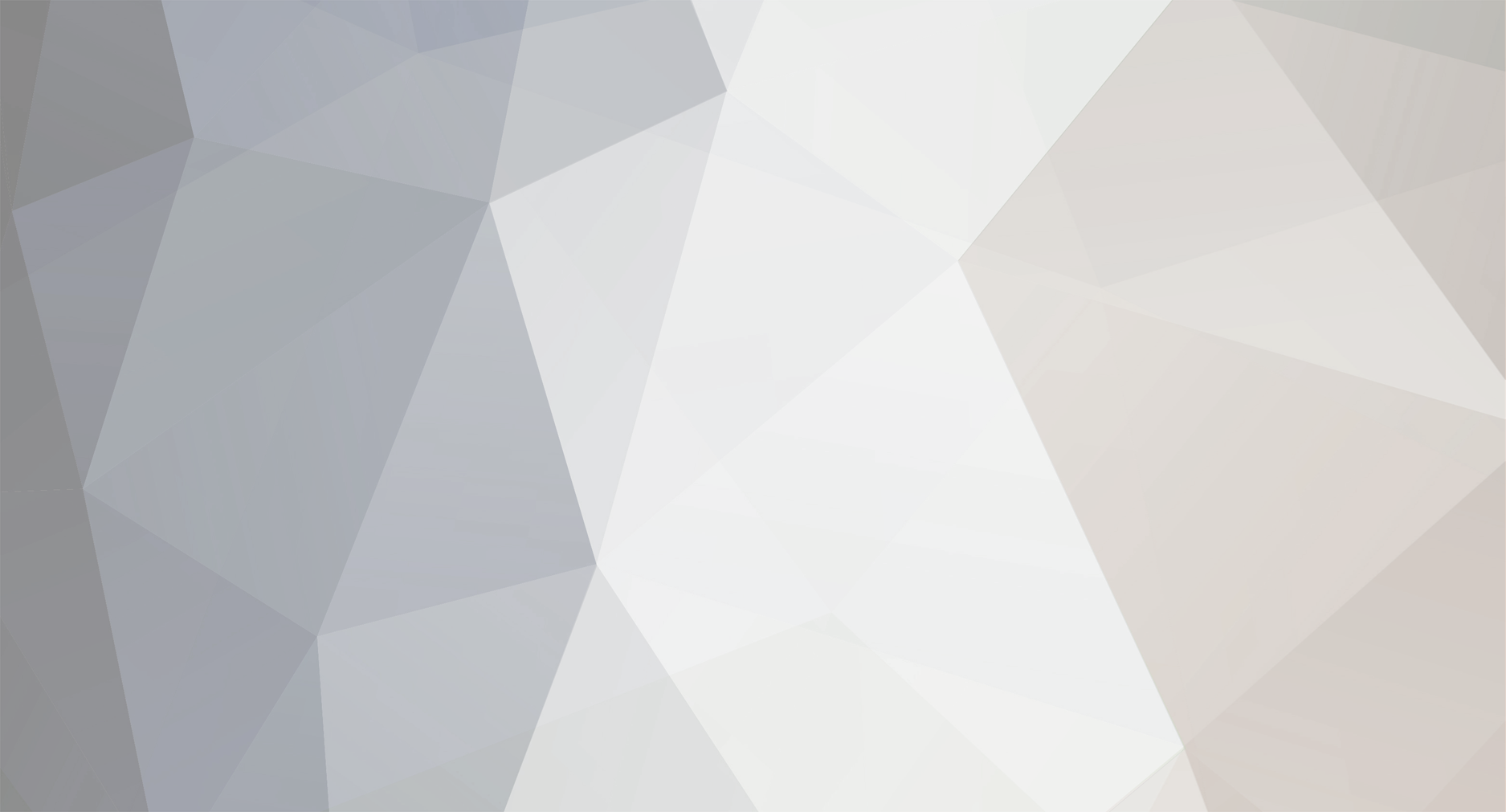
tube80z
Super Moderators-
Posts
1394 -
Joined
-
Last visited
-
Days Won
30
Content Type
Profiles
Forums
Blogs
Events
Gallery
Downloads
Store
Everything posted by tube80z
-
Hi Mike, What type of fire system? If you have halon or similar make sure you don't get sprayed directly because even wearing nomex I got a good burn when mine went off in a formula car. It also is very good at displacing oxygen you need to breath. Cary
-
Camber greater than -3
tube80z replied to RebekahsZ's topic in Brakes, Wheels, Suspension and Chassis
Most clubs have a test-n-tune event or something similar. If you're doesn't bring it up as an idea as I'm sure you're not the only one who would like the time to work on the car. I've been fortunate to have a club that has a dedicated track and we have a weekend event and Saturday is open practice. It's not uncommon to get 10 to 20 miles of actual autox practice. But if you don't have that option then you need to make the car adjust very quickly and it would help a lot if you can get a co-driver. About the only thing you're going to be able to do is adjust tire pressures, which can help. Other ideas if the class allow would be cockpit adjustable sway bars or have the adjusters somewhere they can be moved quickly if you can't have driver adjustable versions. And on the camber plates if you build a turnbuckle arrangement to move the plate once loosened that might help too. This way you don't have to jack up the car. There's one guy I run with that built strut tops that come off so he can change the springs really quickly. He can do a spring change in about ten minutes per axle. It won't happen in line but it could between sessions if you had a small break. If it were me I'd lobby the club for a test and tune event. Hope this helps, Cary -
Camber greater than -3
tube80z replied to RebekahsZ's topic in Brakes, Wheels, Suspension and Chassis
The one thing that's really important for our cars is to make sure you are either in the car or have driver weight in the car when getting an alignment done at a shop. If this isn't done then you may not be getting the numbers you are asking for. Our cars are very sensitive to roll angle and sitting in the car puts a slight angle on the car that needs to be compensated for. Once you know that info then you could do the alignment without being in the car. Corner weights, ride heights, camber/caster are all in this boat. For camber I bought a fancy digital tool (smart camber) and it can also be used for caster too. Or if I had thought about it I could have used some trig and a carpenters square to get the same info. The latter is very useful at the track when you want to quickly check something. For toe you can build a string system that aligns with the car centerline and it makes things pretty simple. You can also setup a long piece of angle or square steel at hub height and do the same thing. And as Jon mentioned you can use floor tiles, carpet squares and even magazine pages to help level the floor. If you're at a shop or at home doing this it's good to also learn what a flat or a full turn does to the alignment. If you keep good notes you can always make a change this way at the track and not worry so much about all the alignment equipment. But I would recommend checking it later to make sure it was what you wanted. For camber you can use a tape measure with your camber plates to get similar info. For taking tire temps as a one man show there are a couple of options. If you don't have memory tire pyrometer I would recommend a handheld recorder. I quickly get out of the car and start with left front (inside, middle, outer), then left rear (same order), right rear, right front, and then left front again. Then drive the car back to the pits. Once there you can play back the temps and right them down. If you can get a buddy to help or offer to do this for someone else and they help you it works even better but you don't always have that luxury. Why do I do the same tire again? That's to see how they are cooling and figure that into my temps as I came off the track. And from the temps you can get fancy with averages to determine what end is working harder, diagonal, etc. And make adjustments and go faster. Okay, that's a lot to think about. Feel free to ask questions. There's a lot of knowledge on this forum and there may be far better ways to do this than I just offered up. Cary -
McKinney Motorsports Coilover install
tube80z replied to bryand2's topic in Brakes, Wheels, Suspension and Chassis
The one thing to keep in mind besides the weight of the car is the unsprung weight on the corner. If this is the same between the S30 and S13 then the frequency of the suspension should be the same and the damping should work. But the difference between wheels and tires is a lot larger than most people would think and this can throw the frequency and the damping way off. I believe John is referring to the quality of the shocks and the damping curves above rather than the coil springs. You can have a car that's stiff (2.5 to 3 Hz) that is damped in the 65 to 70 percent critical range that doesn't ride too bad. Up that number and the ride is likely to become a lot harsher, which could be bouncy. For a street car where ride is important there are typically setup with what's called flat ride. This takes into account how bumps are encountered and how the car would feel to occupants. Generally this is a setup that has the rear slightly stiffer (higher frequency) than the front. For a race car they are often setup the opposite to help support the chassis and put power down. And these often feel much rougher when riding in them. There are a lot of kits out there that claim they are "valved" for a certain car. I'm sure they were but unless you have a setup really close to the car used for development then you may not get very good results. It really doesn't cost all that much extra to have this done for your car but it does take a lot of work to get all the measurements. You can find more information in the shocks/springs/suspension sticky. Cary -
Front droop limiter straps
tube80z replied to RebekahsZ's topic in Brakes, Wheels, Suspension and Chassis
That will surely work but it's a little overkill. I drilled a hole in the front of the strut tower for the top of my limiter mount. This is the one you really want to make easily adjustable of you intend to try and tune with them. On the rear just keeping light tension on the spring will be good enough. On the front you can try some compression but I would recommend not trying zero droop. The car will instantly turn but is very bouncy. Perhaps if you had a huge splitter making downforce it might work. Keep up the good work. Cary -
240Z Chassis prep / reinforcements
tube80z replied to Kurai's topic in Brakes, Wheels, Suspension and Chassis
I just notices these. Very nice and thanks for posting. The bar from the passenger corner to the middle of the front cross bar is very effective at increasing the torsional strength of the car. I have a few grape models I made I need to post showing some of these small changes and the difference they made. Also adding the boxes in the front behind the wheel is helpful but I think the tube that Jon adding in his cage going from the bottom of the rocker to the top of the front strut rail is much more effective. Cary -
240Z Chassis prep / reinforcements
tube80z replied to Kurai's topic in Brakes, Wheels, Suspension and Chassis
And if you have a cage you can tie the pedal box into the front cross bar. If you do this then you will really notice a difference. It's always good to have someone push really hard on the brakes while you watch the pedal box/masters. Many times you'll be surprised at how much all this moves around. Removing that will help with brake feel. And then you just keep going down the line. best, Cary -
It should work fine and I like it. Another option you might consider is to link both sides with cable and use some rollers to allow the cable to move back and forth. What this does is allow you to droop limit when you lift the end up but not constrain roll. And then you can start doing tricky things like keeping the amount of lift limited when you hit the brakes or drop the throttle but still have full travel for roll. If you're playing with underbody aero or a diffuser that might be useful. Or if you hillclimb and deal with a lot of road crown this can help to better put the power down. And you can also use the helper springs. Cool idea though. Cary
-
The one thing you'll want to add if you haven't already taken it into account is a pinion snubber. The ears will not hold the front of the diff from lifting and will eventually break on a V8 car. Just a piece of square across the top with a basic rubber block should be good enough. Cary
-
Woodward power steering project
tube80z replied to JMortensen's topic in Brakes, Wheels, Suspension and Chassis
Let the splitter be the skid plate. Put a few tubes to capture the back of the splitter on the crossmember and then use this as the mount. Cary -
High End LS3 With Harrop ITB, T56 and R230 Build Log
tube80z replied to gt40rick's topic in Gen III & IV Chevy V8Z Tech Board
Nice car, now I need to come up with 5K for that awesome manifold. -
Yet another Rear control arm design
tube80z replied to tholt's topic in Brakes, Wheels, Suspension and Chassis
Looks really good Jon! -
That's awesome Cameron. Harold Knoebel is a multi-time national DMOD champion and you beat a host of other people in really fast cars. From watching the video it looks like a couple of sections are pretty rough. It doesn't look like you're that far from being able to fight for King of the hill. Looks like a great venue and sounds very similar to what we have in the PNW with regards to event atmosphere. Great job! Cary
-
Recessed engine mounting (into the firewall)
tube80z replied to z1 zonly's topic in Fabrication / Welding
Having been around that car for a long time I can tell you it had nothing to do with the motor placement. It had a lot of other issues. A local racer put the motor even further back in his 510 (Larry Nelson) and it was one of the best handling 510s I've ever had the pleasure of driving. Put another way, the 510 has heaps more PMOI than most sports racers or formula cars and normal humans don't have issues with those. Claude Rouelle shared a number of stories in his seminars about weight distribution and PMOI. Up until the Pirelli tire era most F1 teams arrived and the track and only changed weight distribution according to him. They had sophisticated simulations to determine all the other parameters before they even showed up. Claude shared one story where moving two 7.5 pound blocks was worth three quarters of a second. You can do some simulation based on either data or by guessing by using the free version of Bosch Lapsim. If you have data you can build your own track and create a model of your car. From there you can play with certain parameters and see what happens to laptime. The free version assumes a perfect driver and doesn't really take suspension into account. From what I recall it's predictions matched what John said, which is what you would expect. So if you want to try and optimize you can have lots of fun with that tool. It was fun to build that 1000 HP Z and see what my 0 to 60 time would be. Cary -
Sorry, I should have called it a hydraulic release bearing. These are stiffer and easier to drive. The engagement point will be something you'll want to work on. The small clutch will bite very quickly so any flex makes this harder to manage. Your definition of free play is correct. You need a specific distance from the bearing to the clutch cover. You also need to have a precise pedal stop so you don't over push the cover. That can also damage them. The crank thrust is the bearing area that takes the pressure when you push down the clutch pedal. If the bearing doesn't have the specific free play and is tight these surfaces can be under pressure most of the time. And over time the bearing wears down and then the machined area on the crank. And then things get expensive. As long as you follow the directions you should be good but make sure the free play is correct and the travel doesn't over extend (pedal stop recommended). Then it's just a matter of getting used to how easy these grab when you let out the pedal. Luckily with the V8 you have extra torque so it won't be as easy to kill the engine. Cary
-
Sorry I missed this part. For the small clutches you will probably need to remove the arm and go to an annular style bearing. These either replace the end on the transmission where the sleeve for the throwout bearing would normally sit or they can be mounted to the bellhouing. These clutches need a smaller bearing and a precise amount of engagement for release. You also need to be very careful you have the prescribed amount of free play or you can run into crank thrust issues down the road. Take a look at what's offered for the LS engines and the T56 conversion. This will give you an idea of what you need to do for the VK56 and G35 gearbox. Hope this helps, Cary
-
Hi Dave, A button is what they call a friction surface with no ring gear. You use a the stock flex plate and then sandwich on this friction surface (using normal flywheel length bolts), which is exactly what you're looking to do. Only change is longer bolts will be needed for the crank hub. Take a look part way down the page on this forum to see a CADed up view of how this works http://www.audizine.com/forum/showthread.php/333627-GURU-s-official-LS-B5-Quattro-Swap-for-under-5k/page11 The flex plate is usually about 0.125 and the button is around 0.25 or so. This gets you to the normal flywheel thickness. The cool thing in all this is the buttons are usually around $125 new from the speed shops but even a custom one shouldn't be too bad. For a button all they really need to do is take a standard one and put eh VK56 crank pattern on it. They may even sell blanks that you could do this your self. Or I'm guessing that Taylor would do this for you. On the clutch I'm not sure if you found a good deal on this one and that's driving the purchase. You'd be better off with the newer v-drive style as they run cooler. On a friends Z the older style like this in 5.5 needed a rebuild before the year was out. The newer v-drive (optiumum V) has shown less wear. I only gently nudge in the 7.25 range as they are all over e-bay for around $200-$250 for units in good shape. That's what I did for the LS one I have. BTW, as you probably know there's no loading your car on the trailer without a wing with one of these. Cary
-
Is there a reason you're not using a button and the VK56 flexplate? OR is it a problem with the G35 6-speed tranny not aligning the starter to the flexplate? I had a custom flywheel built years ago for a 510 conversion. For it I sent them the flex plate from the engine to establash crank pattern and general spacing and then a flywheel that fit the other tranny to get the starter gear spacing correct. So with those two and working back from the block mating face you could come up with your dimensions. You'll need to know if the VK56 is flat on the back or has any offset to figure that in. If this is a track only car the 5.5 will probably be okay but if you autox you may find that you have to service the clutch every year or sooner. A 7.25 has a lot more heat capacity and is going to be a little easier to get started. Just my two cents. I went with the 7.25 on my LS swap. C
-
I'd check your alignment and make sure you don't have anything that's worn out (tie-rods, inner/outer), worn rack bushings. And obvious things like the wheel is round. If all that checks out then it may be the tire. Over the years I've seen some weird wear patterns on tire from autox. I can only assume caused by what's under the rubber. The new GoodYear production slicks get a wear pattern that looks like massive toe-out. You run them once and then flip to take care of it. So another suggestion would be to check with other Nitto owners to see if they see a similar thing.
-
On most hills it takes a third of the way for them to really start working. One trick for any street legal car is to drive around at legal speeds but use a lot of brake gas to build heat into the tires/brakes. As you sit in line that latent heat can make a huge difference. If you have a hill where you all drive to start make sure you do real work to get heat into the tires. Often that can make a second or two up in the bottom third of many hills. Driving at normal speeds on the course can help you at times. But many times the difference between legal and race speeds is so much that it seems completely different. Almost all hills have a required novice program where they often take all of you up the hill in a truck and talk about key areas (usually safety related) and show movies of the course. No matter how many times I've ran a hill I always go to these often taking crap for where I went off on what year and so and so. I'd look for vids on youtube and make sure to record your own. You can watch them at night to help memorize what it looks like at speed. Just make sure the car still drives after the event. At some point we all have a moment when pushing really hard.
-
I've done a number of hillclimbs in the Northwest. Assuming the roads are similar your setup sounds reasonable. One thing to make sure is that your alignment doesn't make the car follow ruts/lines and that road camber changes in the road aren't a major issue. In general you won't be using your brakes as hard as you might on a track/autox course for most hills. For us a lot of corners have apex speeds in the 45 to 60 range and only a few in the 75 to 80 range, which is usually major pucker when a tree or rock is very close to you. I lost a door mirror on a rock wall at Bogus Basin (Boise ID). At hills you'll probably see more suspension travel than anywhere you race. So make sure you don't hit bumpstops or that could make the car very nervous. My only other advice would be to drive the hill as you see it at about the 95% level. As you learn it you can know what areas you can really keep the throttle down. But be careful you don't try and gain too much time each run. Keep each run close and inch up. I've seen too many people do a few slow runs and then really go for it only to crash. Generally it takes 2 to 3 years before you know the hill well enough to start chasing records, at least for an amateur like myself. And then mother nature often has her say. Hillclimbs are probably the most fun thing I have done in a car. You may go faster on a track but the feel from a hill is something else. And when you're done and talking very quickly or foot won't stay still you'll know it was a good run. Cary
-
I think a lot of this depends on how high you rev your engine. In most of the cars I've ran we typically used a 3.70 to start with and launched in second and then used third for most of the course. I found that quicker for me than dropping to second and having to deal with managing a lot of torque at the rear wheels. It also depends on whether your willing to change diffs for track/street versus autox. If you don't want to change diffs then I'd look at a lower ratio 3:55 or 3:36. If you're willing to change then maybe lower than what you have and start in second and go for third. As many others have written you want a gear that's good for 75 to 80. I wouldn't use a 4.38 for track days as they generate a lot more heat than a 4.11 or at least that's been what I've seen.
-
Adjustable front control arm options
tube80z replied to wheelman's topic in Brakes, Wheels, Suspension and Chassis
The only thing I saw I might change would be to use safety washers that has a built in conical spacer so the rod ends have more clearance to their bodies. To keep from trying to move the top of the strut you need this extra degree of freedom. Dan did an excellent job in the sticky discussing all this. That's why the majority of the aftermarket arms for the back of the Z aren't really a very good design. I did a quick and dirty set for a friend's car where we wanted to try adding some antisquat. While we never went down that road we did notice the car seemed to put power down a little better. This was on a car with 15 inch FA rears and 436 WHP. I know that's anecdotal but the toe-link arms do remove some stiction from the suspension and any where you can do that it will help. I think another area of development we haven't looked at too close is the outer mount on the rear strut. It would seem to me that we can do this in a more adjustable way that's a lot lighter and mount the heims flat so we're not rotating the bearing in the housing. -
I've had good luck with real hammerite. I put it on with a roller and it holds up pretty well. Cary
-
That rule of thumb doesn't apply to race/high performance cars. It's really intended for ride (flat ride) for not causing discomfort. For racing we are more concerned with balance in the corners and control. As long as the car doesn't hop off the ground in a straight line it's okay. It's also perfectly acceptable to have the same frequency front and rear or the front stiffer. In a high HP car that often is quicker. Cary