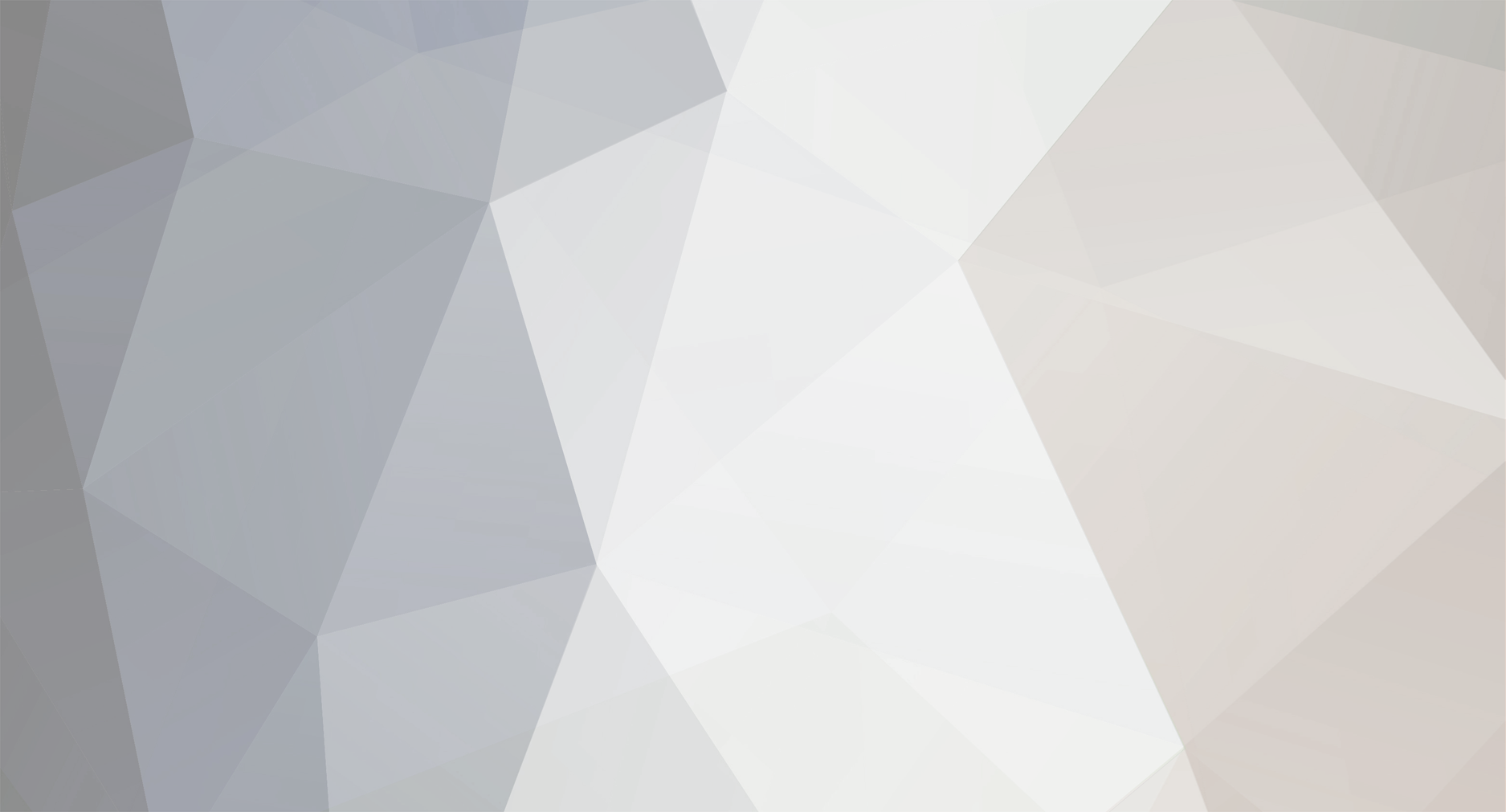
NewZed
Members-
Posts
6680 -
Joined
-
Last visited
-
Days Won
70
Content Type
Profiles
Forums
Blogs
Events
Gallery
Downloads
Store
Everything posted by NewZed
-
L28et swap RICH in the >10 AFR's, AFM at idle?
NewZed replied to SDgoods's topic in Trouble Shooting / General Engine
A though - are you testing your TPS at the TPS or at the ECCS connectors? Better to test at the ECCS connectors so you know what the ECCS sees. As far as 0.3 volts, I think that the narrow band sensors jump rapidly from .2 V to .8 V when they go rich (low O2). But Ithink that when the mixture is way off, the sensors can foul and don't work right anymore. The wide bands apparently go the other way, in a more linear fashion, from high V to low V when the mixture gets rich. You're not using the same type of sensor for your AFR gauge and the ECCS are you? They're different. And there's a newer type of sensor that uses resistance, not voltage to calculate the ratio. You're probably right on the EGR effect, since there is no extra fuel added with the added EGR gas. I got my gases mixed up. I still can't see any reason for the AAC or the AAR to affect the fuel-air ratio. Good luck. At least you have a good reason to dig in to all of technology behind the system. -
L28et swap RICH in the >10 AFR's, AFM at idle?
NewZed replied to SDgoods's topic in Trouble Shooting / General Engine
It might be a correlation, not a cause. The attached diagram shows that the AAC only bypasses the throttle blade. The EGR gas might affect the O2 reading, since it as adding O2 depleted air to the intake system, which is not the same "reference" air that the O2 sensor is calibrated to. The AAC and EGR system are tied to the same VCM. Looks complicated and the variables probably interact. Regardless, the 81 Turbo Supplement is a good document to study. -
L28et swap RICH in the >10 AFR's, AFM at idle?
NewZed replied to SDgoods's topic in Trouble Shooting / General Engine
The AAR has no effect on the air-fuel ratio. It only lets air past the throttle blade, not the AFM. All air should pass through the AFM, if the AAR is plumbed correctly. 70 ohms is correct for the AAR, that's the resistance of the heater wire on the bimetallic strip. And the AAR only opens when the bimetallic strip cools off. Even so, it's only effect is on idle RPM, not AFR's. The AAC also only affects air flow, not air-fuel ratio, but through a different control mechanism. EGR will affect the amount of fuel, but it only dilutes both air (O2) and fuel equally. There's a great chart on page EF-49 of the 81 Turbo Supplement. EF-35 has a nice diagram of the inputs to the ECCS. 81 was the early days of the ECCS Analyzer though, so much of the FSM assumes it's being used. Makes it a pain to figure things out., but there's still some good clues in there. For example, at mid-throttle, mid-RPM on a warmed-up engine the ECCS should go to closed-loop control, using the O2 sensor. Maybe your O2 circuit is showing a constant lean condition and the ECCS is compensating. Might also explain the jerky behavior, and good perfromance under load. cg knows more about the closed-loop control since he's installed a few complete systems. Just a possibility. -
L28et swap RICH in the >10 AFR's, AFM at idle?
NewZed replied to SDgoods's topic in Trouble Shooting / General Engine
-
I feel like a parrot sometimes for saying it, but have you checked the FSM's? There are complete drawings and diagrams in the AC chapter. Look down in the lower right corner of the drawings for the drawing number and you might find that they used the exact same drawing. That would be a good indicator of sameness.
-
I would list the parts used to run the engine, to start. Is it a completely stock straight-across swap from a ZX turbo? What year? Any changes from stock? Turbo AFM, turbo ECCS, etc. Have you used the FSM to do some troubleshooting? Need more facts...
-
I get it. The "boss" being on the drive shaft side, to fit the hole in the flange. Thanks.
-
Center boss? Can you elucidate? Will the difference affect a transplant from one assembly to another? Just trying to learn more stuff. Would probably help RZ out also.
-
I thought that there were only two flanges - the ones used on the 76-83 Z and ZX R200's and the one used on the 1975 280Z and the 84 and up ZX R200's. 1975 is the oddball, but otherwise the break is at 83-84. That's bolt-pattern and size I'm referring to. Somewhere in the 76-83 range they changed from square to round in shape but the bolt pattern is the same. You didn't give the pattern dimensions, which are the most important piece.
-
L28et swap RICH in the >10 AFR's, AFM at idle?
NewZed replied to SDgoods's topic in Trouble Shooting / General Engine
Weird that you know the resistance range that the AFM pins should show but you don't set your fuel pressure to the stock setting. Are you working from the FSM or just from threads on the internet? 4 psi, plus the +, might not be huge but it's certainly not helping your rich condition. -
How much tread is left on the tires?
-
It's a metric-sized engine. Should have tipped you off when you saw 7/16", that something wasn't right. I found the 202-5406 instructions using Google and "280Z head stud" search words. 10 mm studs typically use a 12 mm bolt head or nut (sometimes 13 mm). You got the wrong instructions. Or the wrong studs and you cross-threaded 7/16" studs in to 10 mm holes. Seems that your main problem in your engine work is picking the wrong people and trusting that they know what they're doing. "Trust but verify" is a good old Reaganism to keep in mind.
-
I think those might be 12 mm nuts, not 1/2 inch. Just looking at the internet info. Try a 12 and start over. http://arpinstructions.com/instructions/202-5406.pdf Even if they are 1/2 inch, you might still be able to hammer a 12 mm on to get it out. 1/2 inch = 12.7 mm.
-
Check the specs in the FSM. The lash gets looser when the engine gets warm. If it's quiet in the morning, when cold, you'll have a pretty good idea.
-
280ZX Misfire under idle or slight acceleration
NewZed replied to Connor280ZX's topic in Trouble Shooting / General Engine
Sounds lean. I would measure fuel pressure before getting too carried away. If it's right, look harder for vacuum leaks, including the EGR system. Download the FSM and read Engine Fuel... chapter to get a good understanding of the EFI system. Might not solve your problem, but it will help you in the long run. In future posts, tell what year car you have, how long you've had it and whether or not it's stock. -
Page 10 here looks interesting, although the whole catalog is worth browsing - http://www.ntn.ca/Catalogues/NTN/CVJ-ForIndusrial_en.pdf Here's one of the Pathfinder axle threads, only because it was mentioned, sounds like you're going a different way - http://forums.hybridz.org/topic/72805-using-pathfinder-and-zxt-axles-to-install-30-spline-nismo-lsd-kit-56k/page-3?do=findComment&comment=942447
-
Thinking about brass, steel and shifting, the other teeth that grind are the splines on the coupling sleeve and the dog teeth, if I understand things. Maybe yours are rounded or damaged. That's the thing about rebuilding transmssions, it seems like you'd have to rebuild them before they start grinding, if you want like-new performance after the rebuild. Once they start grinding the parts that don't come in the rebuild kit are getting damaged.
-
You wrote "61.1" twice, in the title and in the post. Did you mean 6.1? 61 volts would be five batteries wired in series. I don't think it's possible to generate 61 volts from six 2.1 volt lead-acid cells (the typical 12 volt battery). Sounds fascinating though.
-
Use your meter on a 9 volt or 1.5 volt battery. It will probably read 0.9 or 0.15.
-
Regarding the star "walking" on the shaft - it's either supposed to be free to move around, or it's supposed to stay in one place. But walking to a new spot and getting stuck so tight that you have to bang it off with a hammer can't be right. It's either a cause of the problem, or a result of the problem. Might be worth focusing on how and why that happens. If the balls were pressing on the circlip, that force would be pushing against the star and cage, preventing it from getting stuck on the inner spline portion. Since the star is stuck, that suggests that the star walked doen the shaft first, got stuck, then held the balls against the clip until it popped out. I've found that the weird small stuff is sometimes the clue to solving the big problem. Good luck.
-
Thanks for doing that work and posting those videos. It seems like the star/bearing race/cage walking down the shaft might be the problem, not a result of the problem. For whatever reason the star walks, pulling the balls with it. If the cage and star walk far enough inward, that makes the end of the axle get closer to the stops, effectively. After the star walks down the shaft, is it possible for the balls to be on the circlip and the end of the axle to be on the stop, binding the axle end and balls between the stop and the circlip, until one or both give? If you could lock the star in place at the end of the shaft it might solve the problem. Just a guess. I can't imagine that the star is supposed to move on those splines while in use. You might compare a stock Q45 shaft to the MM shafts and see if the star can walk on the stock shaft, and measure the distance from balls in the star wheel and the axle end, with the star walked inward, and see if it's longer then the cup can take. A fix might be as simple as peening some splines on the inside of the star to stop it from walking. As far as shaft length - I can see that I missed something when looking at the drawings and the shortest shaft may not be at full compression. The hub doesn't tilt when it pivots around the control arm axis, it stays essentially perpendicular to the ground. Two things happening, one pulling it away and one drawing it closer. Looks like pulling away wins based on your videos, the shaft is shortest with the wheels hanging (as jmortensen has said in previous posts). Thansk again, those videos show a lot.
-
quick question, yes I searched
NewZed replied to Robftw's topic in Brakes, Wheels, Suspension and Chassis
If you mean the half- or drive-shafts by "axles", then rolling it around won't hurt anything, The hub axles and bearings are separate self-contained assemblies. The mustache bar bushings are available in the Nissan stock rubber from or you can get aftermarket polyurethane replacements. -
I'm short on terminology also, so my post might not have made much sense. And I don't understand the fine details of the CV joints, that's why this thread is interesting. Rossman and texis offer the best suggestion, especailly after you've had so many problems. Put one or both axles back together with no boots and watch what happens as you lift the suspension up and down and rotate the wheel. You've probably seen this thread (it's in the FAQ's), it mentions joint problems if you put the cages in backward (Post #48) and has pictures of assembling the joint. Circa 2005, yours is not a new problem. http://forums.hybridz.org/topic/25054-r230-axle-assembly-a-pictoral-review/ As far as the length, everything pivots around the inner control arm attachment point. The inner CV joint is above the control arm attachment point, therefore gets longer as the wheel drops and shorter as the wheel rises. You can verify this by moving the suspension up and down as suggested. If your diff really is lower its CV joint axis might be the same as the control arm's so it will be shortest when level. See the attached picture. I could be wrong but that's what the picture tells me. Maybe one axle joint is binding under load and pulling the other side out. Another possibility, hard to verify in the garage.
-
I think some people call it the "star wheel" or something like that. But in bearing terms I think that it is the cage and race combined. Maybe the stops are there more to keep the axle from moving far enough to let the balls out of their "cage". Axle with "cage" moves (too far), balls get left behind, come out of cage, get stuck between cage and circlip, circlip pops out on the reverse movement. There is probably a critical relationship between the cage, cup, stops, circlips and cage/star position on the shaft. The balls should never be able to come out of their spot between cup and cage/star, but yours might be. Hard to tell what happens first but you might be able to work the joint with the shaft off the car and figure it out. I would guess that the stops should have been taller. As far as the stops getting worn down, if you take a compass to the drawing in the FSM, draw some lines and take some measurements you'll see that the drive shaft is most extended with the wheels hanging, and most compressed with them up. You might not have needed that spacer at all, and your problem was the stops all along. The spacer may have destroyed your stops. Sorry I didn't suggest this sooner, you could have at least considered it and taken some measurements on the car.
-
Newly rebuilt engine with loud tapping noise even at idle?!!?!
NewZed replied to JCan's topic in Nissan L6 Forum
You might run that pressure test again, or a leak down test A slanted motor shouldn't cause a 17% drop from high to low. Reporting the values from all cylinders would tell more also, not just two. That link works. Sounds terrible. Good luck.