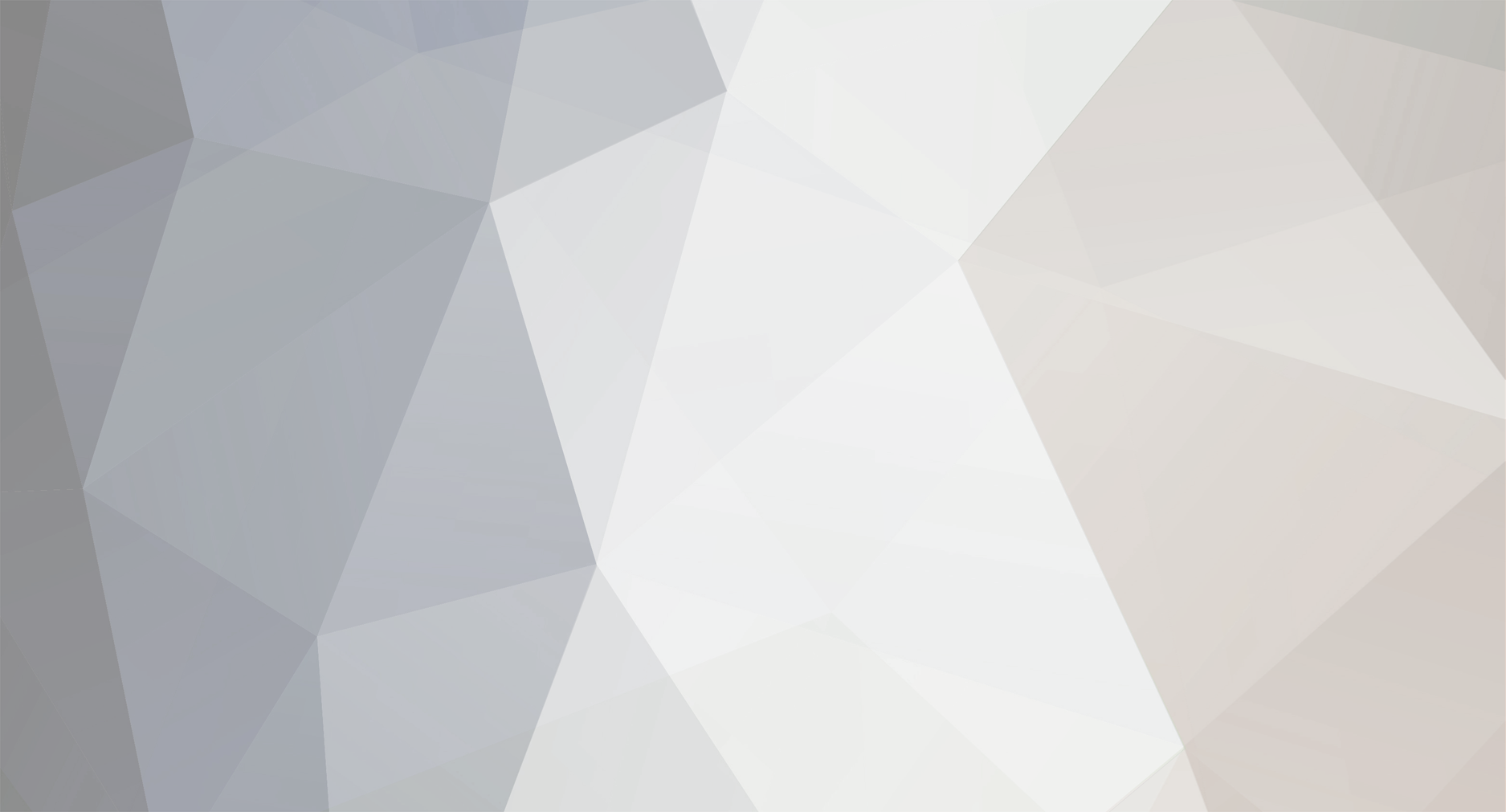
Brad-ManQ45
Members-
Posts
1775 -
Joined
-
Last visited
-
Days Won
6
Content Type
Profiles
Forums
Blogs
Events
Gallery
Downloads
Store
Everything posted by Brad-ManQ45
-
I know HKS and Deltagate are out there, but don't know of others or which would be best in the 400 HP range venting a Stage III trim .63 A/R turbine section.... What are your opinions?
-
R230 or another R200
-
Bad Stem seals or Rings?
Brad-ManQ45 replied to speeder's topic in Trouble Shooting / General Engine
If you do a compression test on each cylinder, then do it again adding a tsp of oil to each cylinder through the spark plug hole abd the compression doesn't raise appreciably, then it is your stems/guides. -
I think you should be looking into a Synchrowave 350DX or Dynasty 300DX, depending on whether you're partial to inverter technology. The Dynasty has a few really neat features. Ask some experts on the Miller and Hobart sites...
-
Monkey on her back? Bet she's a bitch... Now - how do we get this bitch to buck? Who's hounding the hound? Whoa Bitch!
-
The trailblazer is an excellent setup - best in its' class. Won't handle 3/8ths aluminum - you only have ~200 amps output AC/TIG. Almost all machines will have to multi-pass on 3/8" aluminum - you need ~375 amps to single pass it. Do you need the portability? Nothing you've stated in the past threads leads me to believe you are going to make a living on the road with this - do you really need to be able to weld outside the shop? I would be inclined to get the one with the Kohler engine - parts seem to be easier to find. The nice thing about the Trailblazer is that it has a completely divorced AC output, so whatever you are doing on the A/C output doesn't affect your arc. All that said, with quality being job #1 (sorry, couldn't resist a Ford Phrase here), I think that you should get a squarewave TIG. The quality of welds from these machines are awsome. Here's an article: http://www.millerwelds.com/education/tech_articles/articles11.php
-
Being an old FORD man, I never did mess with Chevy's much, and never used the ported vacuum provision on some of the Holley's I used. Ford DID use ported vacuum on some of their engines - the 351C for instance had a vacuum canister that you attached both maiifold AND ported vacuum to. As a hot rodder, I simply used only the middle port on this distributor when turboing and hooked it to the manifold port. Normally the middle/inner port was for ported vacuum and the outer port for manifold...or was it the other way around????? We're talking over 25 years ago....
-
This poses an interesting question in fluid dynamics: On one hand you have high speed air being introduced before the turbo, keeping it spinning (faster) if you recirculate. When you do open the throttle to build boost again, air will need to START being drawn through the filter again (if in fact there hasn't been any pushed OUT the aircleaner (or MAS) - I doubt it would be possible for this to happen on an AFM). On the other, you are constantly drawing air through the filter and this pumping (or drawing) slows down the turbo more, but the air is constantly being drawn through the filter. In this scenario, you have a column of air already moving throughout the intake tract before the turbo when you get back on the gas. I'm willing to bet on the recirculating method being more conducive to quicker spool-up, the high speed air and higher compressor speed more than making up for any inertial difference in getting the air moving through the filter again. What's everyone else's take on this?
-
Actually Pyro, when you first open the throttle, the vacuum is lowered until the engine reaches steady state again, during this time, there is not as much advance. The air/fuel ratio is higher because of the shot from the accelerator pump as the throttle is opened requires less advance because the mixture is richer. Basically, at light load (high vacuum conditions) there is more advance dialed in to work on the flamefront, which moves slower under high Air/Fuel ratios. Under load, when Air/Fuel ratios are lower, there isn't as much vacuum and therefore not as much advance, which isn't needed because the A/F ratio is more conducive to propagating the flamefront. The mechanical advance it there to provide for the proper amount of advance at a certain engine speed when there is no vacuum advance - under full throttle conditions. Think of vacuum advance as a way of tuning the timing when not operating under full throttle conditions. It is the combination of fuel injection and timing maps that work to make modern cars more driveable at low speeds/cold start conditions and get good fuel mileage. It is only an aproximation because it doesn't take into consideration temperature like FI systems do. The accelerator pump/cam is basically an approximate way of covering up the lack of airflow/vacuum signal to draw in fuel when the throttle is initially opened. Sure, there are ways to tune this behavior, but it still will not come close to matching FI done right as regards fuel economy.
-
This has been covered many times before, but: It should be routed back before the turbo and after the AFM (or in a mass air system the mass air unit) because the air measuring device in the system has already measured the air. If you just vent it to atmosphere,when you decelerate quickly after boosting, the engine will run very rich and if you have to get on the gas again quickly you lay down a lot of smoke and don't have as quick a response because the A/F ratio is off. This wastes gas, pollutes the air, lowers the responsiveness of the engine and sounds rice. The bling blings that do this are all drain bamaged (get the double entendre?).
-
You will wantto treat your bare metal with ospho or picklex, then cover with epoxy primer. The ywo products convert the deep rust to something that won't rust again.
-
Which ignition to use on turbo conversion?
Brad-ManQ45 replied to 240ZinTN's topic in Ignition and Electrical
You can pick that up at a JY cheap - sell the Crane get the part and have $ left over for fun... -
Looking for a new turbo for my car. Need advice
Brad-ManQ45 replied to EZ-E's topic in Turbo / Supercharger
That isn't a T3 turbine housing - it's a tangential T4. No wastegate provision. Nice divided housing though - depending on A/R anmd trim it might work.... -
My garage is 20X20 and I can tell you it is a bit on the small side for the Q45 and Z project that is in it on rotisserie. The Town Car takes up that whole side when the Z isn't in there. I have some pics I can post of the selving I put up across the front and part of one side wall. The front set has a fold-down workbench that even when open allows the Q in without having to raise the work surface - but I have to back the Q partway out to utilize the workbench. The other side has the supports for the lowest shelf high enough for the TC to pull in - only about 11" of clearance on both ends.... I have my compressor in the basement in the furnace room and have the air piped to the garage upstairs and over to my workshop in one corner of the basement. Currently the basement is unfinished. One of the first things I will do is to enclose the furnace room because that 60 gal Husky compressor gets loud when I work down there and use it (not very much). If I were to build a house again I'd have a garage with 2 9' doors (not 8'), and would measure 24' deep and 25' wide - enough room for a good workbench and ability to get around bigger cars and projects. Actually, my better half says we'll have a regular farage for the house and a detached Workshop - meaning I could have it even BIGGER, with a lift, pit, hoist (more power - grunt grunt). Were talking Mike Kelly here -I'll have to put an apartment above it because I'll be in the doghouse from wanting to spend too much time in it.
-
LS1 / T56 Update #34, 7,000 miles
Brad-ManQ45 replied to Phantom's topic in Gen III & IV Chevy V8Z Tech Board
Glad you got it fixed! -
Grumpyvette: Already have 'em! They ARE STURDY....
-
The reason that the ride is suppler than the 15/60 setup inspite of the reduction in sidewall height is the higher loading of the tire contact patch along with the lower unsprung weight. One has to be careful when changing tire sizes to make sure that the load capacity stays near the same or higher than stock, or else at high speeds or heavy cornering the tires won't hold up to the demands put upon them. A great example of this is the '90-'96 Q45 (4000 lbs + passengers). Stock tire was a special Michelin 215/65/15 tire on 6" rims. The current crop of tires this size's load ratings are about 25% below the original tire specs. To get a current tire with the load capacity that that special tire had nowadays you have to get a Michelin 235/60/15 Pilot HGT4 (actually a smidge higher in load capacity). This is a bit big for 6" rims, but the other choice is a 225/60/15 which is smaller in diameter and no extra load capacity. Fortunately I have aftermarket 7" rims, and love the Pilots, although the Q can chew tires UP!.
-
What to use for painting/coating underside of car?
Brad-ManQ45 replied to 80LS1T's topic in Body Kits & Paint
I have the needle-scalar attachment that I will be using. After everything is down to metal and floorpans replaced and subchassis connectors put in, I wil put on 3 coats of Zero Rust, the either 3M undercoating or bedliner... -
tinted headlight cover legal in texas?
Brad-ManQ45 replied to Sleeper-Z's topic in Body Kits & Paint
JMHO, but anyone driving at night with those things is seriously drain bamaged. Why cut down on the light that lets you see where you're going. I have refused rides at night from these mental midgets... -
When I lived in Round Rock, Texas we had a bad hail storm. My wife and I were out back under the covered porch when we heard a loud bang on the roof, then saw a hail stone between the size of a baseball and softball land 3 feet ftom the edge of the patio. We got it and kept it in the freezer until we moved to Atlanta, showing everyone that it CAN get that big.
-
some suspension questions for 280z
Brad-ManQ45 replied to a topic in Brakes, Wheels, Suspension and Chassis
Sorry, don't know the answer to this one. -
In a 2 year period, my 280 ZXT was backed into TWICE and my Q45 ONCE by women. I think there is something about the physical act of putting a car in reverse that disconnects their brain.... Glad it wasn't any worse.
-
some suspension questions for 280z
Brad-ManQ45 replied to a topic in Brakes, Wheels, Suspension and Chassis
HGS130 is a 280ZX and will not fit a 280Z. At least I THINK that's what you are asking. You could provide a link so, we can see what you're trying to say... -
Very nice - what did you use to form the vents?
-
Please let us know what you decide!