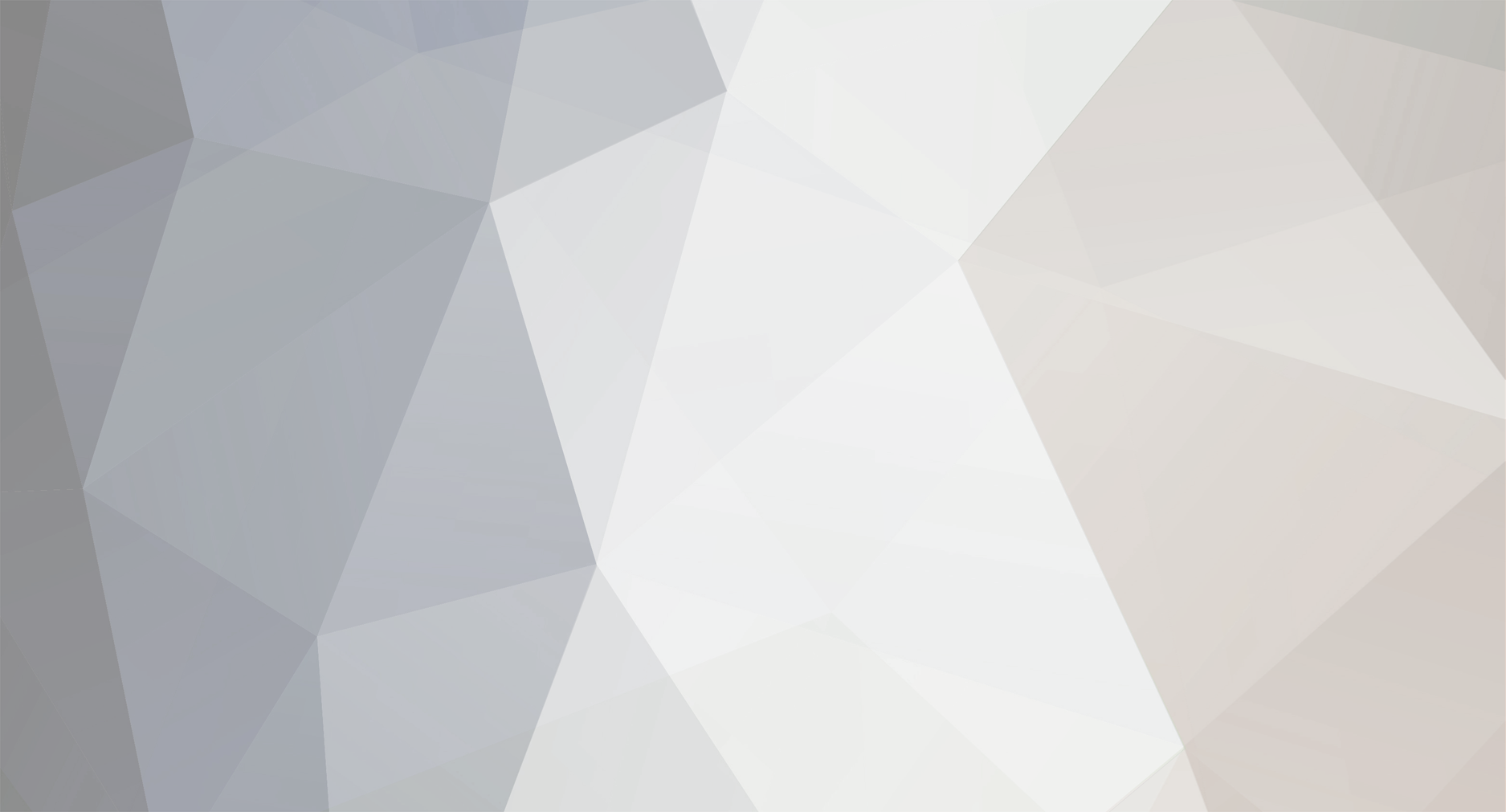
garvice
Donating Members-
Posts
706 -
Joined
-
Last visited
Content Type
Profiles
Forums
Blogs
Events
Gallery
Downloads
Store
Everything posted by garvice
-
The shifter cages had a round bar welded between them. I cut the bar out and welded the cages together. I also used one of 240hoke's shifter relocators. This brought the remote shifter forward about 50mm and now it sits at the rear of the original hole. Haven't put the centre console back on to see if still fits.
-
Looking good mate. How does the liquid metal compare to actual metal? I.E. Building it up with weld.
-
Looking good Ron. I can definitely understand your reluctance in not wanting to move the transmission mount (since you have the later style mount). I just had to do it for my 300zx transmission in my 260z and while it wasn't overly hard, it did require a lot of patience and will not be a reversable change (not that I will ever go back) without a lot of work. The 240z mount would make it so much easier as it would just require a different crossmember.
-
Hi guys, I am putting a RB26 in my 260z with a 300zx transmission (RB26 bellhousing, 300zx transmission). I found very few photos of custom transmission mounts so wanted to share what I had done in the minor chance it might help someone else in the future. I included lots of photos as they tell the story far better then words. I have sat my engine completely vertical to allow more exhaust space, this is why my transmission is on an angle. As most are away, the 300zx transmission is longer then the existing L series 5 speed and and the mount is further back. My original transmission mount was the later style with two ears off either side of the tunnel and a crossmember between. I started by cutting the ears off (spot welded on). This is the drivers side, don't have a photo of the passenger side. I then folded some 2mm sheet to make the drivers side mount parallel to the existing mount (essentially taking the thought of extending the existing mount base). The existing mount is 2mm and is spot welded to the transmission tunnel (which is much thinner) so I felt this was an appropriate thickness. To get the mount to marry up to the tunnel I used a profile gauge (quick google search will bring up what it is). Worked a treat and got the profile spot on first time. I plug welded it to the existing mount and then seam welded around the edges. I hope I never have to remove this as it will be a complete pain to remove. The passenger side was a bit more difficult as the tunnel actually narrows rear of the existing mount rather then getting wider like the drivers side. So I just plated the tunnel with some 2mm sheet (it is not parallel to the existing mount like the drivers side is). To weld this on, I plug welded through the tunnel from the inside, then again seam welded around the mount. The next couple of photos are of the existing crossmember and two different isolation mounts. The first is the L series isolation mount and the second is the GM mount (that I bought for the diff). I had to move the fixing hole in the existing crossmember over to allow for where the transmission sits in the tunnel. This created an issue with the crossmember hitting the transmission bolts. In the end I decided to go with the GM mount as it felt like it had a better construction. The white pipe is 90mm water pipe to simulate an exhaust and the blue tape is in line with the chassis rails. I wasn't overly happy with how the crossmember sat on the GM mount in relation to the new tunnel mounts (sat a bit low at the mounting points). So after a bit of deliberation I decided to make my own crossmember (also didn't want to have to burn out the isolation mount, burning rubber stinks). The original is a 2mm pressed mount (a top hat construction with a small bridge over the bottom), so I built mine out of 2mm sheet. The 2mm sheet is rather easy to bend over some pipe. Here is how I made it. Cut a 40mm strip of 2mm sheet, bent to the shape of the mount I wanted. Laid the shape on a sheet and drew a line offset 20mm from the top sheet. Bent a 60mm strip to match this line. Held them together with magnets to offset them 20mm and transfered the shape onto some 2mm sheet. Cutout the shape in two pieces and then had my four sides. Used some 30mm pipe for the isolation mounts. Ok here are the pictures that really explain it. Reinforced the bolt hole section with more 2mm sheet Measure twice cut once people, I drilled some holes in the bottom sheet and then realised I had drilled too far over, had to weld the hole back up. Had to turn down the isolation mounts as my pipe is a bit smaller then the existing crossmember. The new crossmember although larger is considerably lighter then the original (not quite as wide). Cardboard templates for the mounting ears Made the ears out of 4mm sheet (existing ears where a folded piece of 2mm sheet and then a second piece of 2mm sheet to reinforce), notched and seam welded from both sides. Finished crossmember and mount
-
Ah fair enough, came up very good. Thanks for the help.
-
I love the datsun on the coil cover, how did you do that? Feel like making a second?
-
Nice, thanks.
-
Man I love the look of flat black. So what will the final colour be? Definitely coming together.
-
Must not have explained it correctly, I am only using the mount that the ears attached too, I will build new ears off of this. Check out the following pictures to explain it better. And this is the start of my crossmember
-
Thanks for the photos mate, mine is looking a bit different then your mount. I have kept the original support (minus the ears) so that I could use that as a point to weld to, then I have fabricated some 2mm plate (same thickness as original mount) into a box section on the drivers side and welded it flat on the passengers side. My crossmember I have started making out of 2mm plate but have built a box section similar to the original crossmember but with longer arms as the new transmission sits lower. Just got to work out a way to attach the crossmember to the tunnel mounts. Was thinking of cutting off the circular mounts from the original crossmember and using those as a basis for my new crossmember.
-
Ah, great. I am building my transmission mount now, I have the latter model mount in my car which has the ears sticking off the transmission tunnel so it will probably look different to yours. Will be good to see someone elses to compare against though.
-
I got a good work light for christmas. It is actually a single led on a flexible neck (a foot long) and a strong magnet base. So you just stick it to the car floor and point the led at the area your working on, lights up a good foot square from about a foot away. Great for when your welding under the hoist and need the extra bit of light. Like your idea though.
-
Big-Phil goes Rb30!!!!!!!!!!!!!!!!!!!!!!!!!!!!!!!!!!
garvice replied to big-phil's topic in Nissan RB Forum
Good luck Phil, but $550!!! http://cgi.ebay.com.au/nissan-rb30-motor-transmission-auto-great-turbo-project-/150543767371?pt=AU_Car_Parts_Accessories&hash=item230d1b974b#ht_500wt_1156 http://cgi.ebay.com.au/nissan-skyline-r31-rb30-engine-auto-ecu-computer-/180607551305?pt=AU_Car_Parts_Accessories&hash=item2a0d0c8749#ht_602wt_1141 Plenty more for even better prices. Also, if you haven't already seen it, download this guide. http://www.skylinesaustralia.com/forums/topic/15420-r33-rb30-conversion/ -
Wood is temporary (should get something proper within 10 years, ha). Seriously though, this timber is about 50 years seasoned hardwood and the seem is not touching the bottom of the cut. Good pick up though. Was thinking eventually using poly prop blocks with rubber coating
-
Well the car has been lifted several times from these points without a hitch, looks like it is a suitable way to lift the car.
-
Woodward power steering project
garvice replied to JMortensen's topic in Brakes, Wheels, Suspension and Chassis
Ha, J, look at my signature. I pulled the head off my L28 to replace a gasket. Now it is on my hoist with a RB26 sitting in it. This is not going to be done anytime soon. I have a 4month old son, by the time it is finished he will probably be old enough to ask for the keys. Ha (nice try though) -
Woodward power steering project
garvice replied to JMortensen's topic in Brakes, Wheels, Suspension and Chassis
Subscribed. I want to see how this one turns out, lots of good info there. Power steering would be great, but I would hate to lose the feel of what the car is doing, this is looking promising. -
My car is down (well up actually) at the moment getting a new build. RB26 in, just building some transmission mounts for it now. Once I build those it will probably sit collecting dust while my money gets spent on the new family.
-
I know I'm not the only one with a non-running car!
garvice replied to AlwaysBroke's topic in Non Tech Board
I pulled my car down to change a head gasket, found a welded harmonic balancer and a bunch of other issues from an incorrect engine rebuild. Bought a half cut, pulled engine and have now dropped a RB26 in. Then my son was born so the project is now on hold. I think by the time it is ready my son will be asking for the keys. -
Well today was a glorious day, I finally got my car up on my hoist. I have a question of how I am lifting the car though. My hoist has asymmetric arms, so to get the small arms on the Tie rod points, the only place that the longer arms would reach (other then frame rails) was the pinch weld. I assumed this was fine since it is a standard jacking point, however just wanted to confirm or ask if there was anywhere else that I should lift from. I think if I ever move home I will mount the hoist closer together so that arms had a bit more reach.
-
Mate the engine looks great, but I got to point out your electrical system. You have all these nice braided hoses and anodised fittings then you have split conduit and red electrical tape. Surely you could do something a little nicer then that, perhaps some fibreglass sleeving and heat shrink. I have used this and find it really nice to work with (in black or course) http://buyheatshrink.com/braidedsleeving/fiberglass-sleeving.htm and this is a bit stiffer http://buyheatshrink.com/braidedsleeving/saturated-fiberglass-sleeving.htm and of course some glue lined heat shrink http://buyheatshrink.com/heatshrinktubing/4to1adhesive.htm#B Still seriously jealous though, my RB26 is sitting in the engine bay waiting for me to work on it. It's like it just sits there mocking me.
-
Looking good mate, just a small problem with your statement but don't worry I have fixed it.
-
how many guys still have several local car buddies
garvice replied to grumpyvette's topic in Non Tech Board
I have a good number of car friends. In fact one mate had my Z stored at his shed for a good 4 months while I was building my shed. His shed became the workshop for my engine swap while I got my shed together. I am also going over another mates place on friday night to help him wire up his ford. I think once I get my shed/hoist powered up I will miraculously have a lot more friends coming to see me then I did before. HA. I got to say though, it is hard to find the time when marriage and especially kids come along though. Some of my mates are considerably under the thumb and trying to catch up with those guys for car speak is very difficult. -
The engine is a 7MGTE, I have read about a few swaps on here. There is also a youtube video of someone killing a ferrari in one. Just do a search on the above and you will find plenty of info.