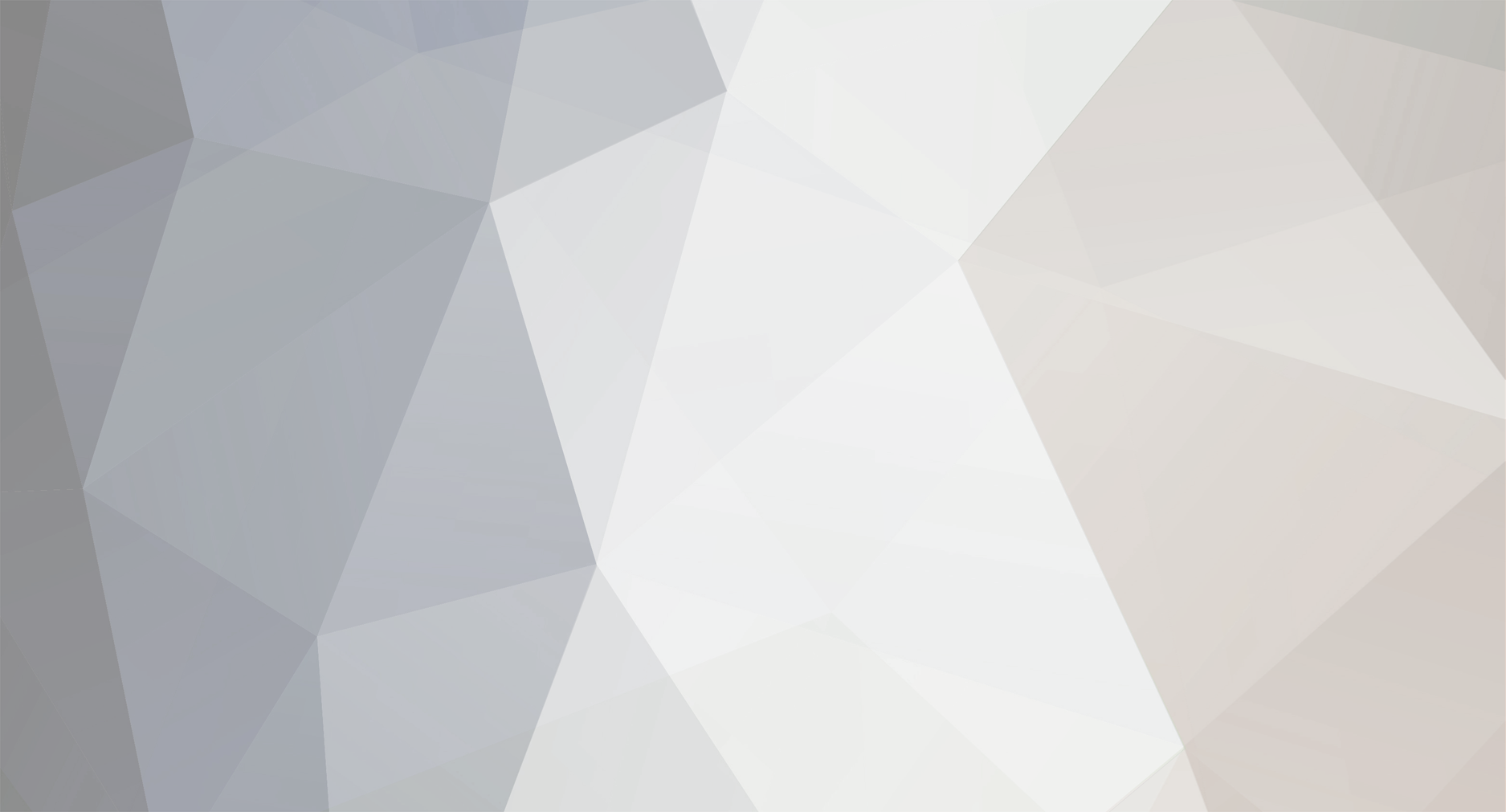
Pop N Wood
Members-
Posts
3012 -
Joined
-
Last visited
-
Days Won
5
Content Type
Profiles
Forums
Blogs
Events
Gallery
Downloads
Store
Everything posted by Pop N Wood
-
I think the oil in the intake is being overstated. From what I have read on LS1tech, it doesn't affect everybody. Only some cars are bothered by it, and it is less common on the later engines vs. the earlier ones. Worst case just take the PCV off and put open breathers on it. The other day I found a nice valley cover with built in K&N filter for $60.
-
Sounds like something shorted out DOWNSTREAM from the ballast resistor causing excess current through the resistor. Really, you should be able to jumper over the ballast resistor and the car will run fine until the points get pitted to the point of no longer working. You need to be careful, because whatever is shorted may have been the cause of your fusible link/alternator going out in the first place. Fix the short before you burn up another alternator.
-
I would use something other than carb cleaner. That stuff is too nasty.
-
Damn and I was just envying those nice, straight bumpers in the earlier pics.
-
You don't need more than 20 amps for the welders you are looking at. Just go to Homers and get a receptacle that matches the plug on the welder. I have a 50 amp plug receptacle on my 30 amp welder circuit. As long as the breaker is matched to the wiring size you are safe. Just don't go the other way around.
-
Final Question for the Californaio people befor i leave for Iraq!!!!
Pop N Wood replied to 240ZR's topic in Non Tech Board
Sound simple. Get Georgia insurance. -
The type of plug doesn't really tell you how much amperage the circuit is rated for. In a perfect world it should, but people take short cuts. Find the breakers that control the two plugs you showed. They should have separate breakers since all 220V outlets need a dedicated breaker each. That should tell you what amperage that circuit will handle. Keep in mind the amperage rating of a circuit is determined by the size of the wire and not type of outlet. If you need a bigger breaker, you may need bigger wire. You can alway change out the plug outlet to match you welder, but make absolutely sure the wiring matches the breaker size. Also you shouldn't have to up size the breakers. The MM175 in the first link says it only needs 19.5 amps of line current. If that is accurate, you should be good to go with only a 20 amp circuit. Go to the Miller web site and pull up the owners manual for that particular unit to see what it recommends. But couldn't hurt to go 30 amp. A 30 amp circuit needs 10 guage wire. That being said, unless you are planing on taking the welder to a buddy's garage, get the 220V unit. They draw much less line current and won't dim your house lights like a 110V unit can.
-
Guess synthethic oils might actually work http://www.msnbc.msn.com/id/16070928/
-
That is why I cut and pasted the entire head installation procedure. I wasn't sure what "GM P/N 12346139" was. Thought it might be lube, but turns out it is brake cleaner. But when searching for that info I found this snippit from a Helms manual http://www.ls2.com/boggs/torques/headboltinstructions.htm It specifically states the M11 bolts, which are fastened with angle gauge, must be set dry. I guess the moral of the story is to always read the manual.
-
Interesting aero design on WRX
Pop N Wood replied to thehelix112's topic in Windtunnel Test Results and Analysis
I thought it was so exhaust fumes wouldn't get sucked up into an open back window. -
That is not what the GM service manual says for a 2002 Camaro engine:: ----------------------------------------------------------------------- Clean the engine block cylinder head bolt holes, if required. Thread repair tool J 42385-107 may be used to clean the threads of old threadlocking material. Spray cleaner GM P/N 12346139, P/N 12377981, (Canadian P/N 10953463), or equivalent into the hole. Clean the cylinder head bolt holes with compressed air. Check the cylinder head locating pins for proper installation. Install the NEW cylinder head gasket onto the locating pins. Important when properly installed, the tab on the left cylinder head gasket will be located left of center, or closer to the front of the engine, and the words "This Side Up", and the engine displacement, will be visible. Inspect the gasket for proper installation. Install the cylinder head onto the locating pins and the gasket. Install the NEW cylinder head bolts. Notice Use the correct fastener in the correct location. Replacement fasteners must be the correct part number for that application. Fasteners requiring replacement or fasteners requiring the use of thread locking compound or sealant are identified in the service procedure. Do not use paints, lubricants, or corrosion inhibitors on fasteners or fastener joint surfaces unless specified. These coatings affect fastener torque and joint clamping force and may damage the fastener. Use the correct tightening sequence and specifications when installing fasteners in order to avoid damage to parts and systems. Tighten the cylinder head bolts. Tighten Tighten the M11 cylinder head bolts (1-10) a first pass in sequence to 30 N·m (22 lb ft). Tighten the M11 cylinder head bolts (1-10) a second pass in sequence to 90 degrees using the J 36660-A . Tighten the M11 cylinder head bolts (1-8) to 90 degrees and the M11 cylinder head bolts (9 and 10) to 50 degrees a final pass in sequence using J 36660-A . Tighten the M8 cylinder head bolts (11-15) to 30 N·m (22 lb ft). Begin with the center bolt (11) and alternating side-to-side, work outward tightening all of the bolts.
-
Two small town Irishmen were sitting in the town pub, when the first one says to the second " You know, Sean old boy, I think I've had every woman in this town, except of course for me Mother and me sister." To which the second Irishman says "Well then Patty me boy, between you and me we've had them all!"
-
LOL Did he rebut your negative feedback by saying you left a negative on him after he left one on you? Does he think people won't check dates?
-
Strength at the welds is the absolute least of your worries. None of your welds should fail. You could weld a U shaped bracket to the strut tower and pin it to the cross rods and you will still be 1000 times stronger than you need to be. All you really need to concern yourself with is the rigidity of the crossbars. In that sense try to make everything out of straight pieces with as few bends as possible. IMO connecting the bar to the radiator core support is just so much added weight. See what you can do to get the bar to go straight up over the engine, curving it if need be. Going back to the firewall is what most guys do with their strut supports.
-
UCLA has upset #2 USC in a huge rival in NCAA football!
Pop N Wood replied to a topic in Non Tech Board
I will never forget the 96 Fiesta Bowl that Florida was in. The SEC is an extremely competative conference. Has some great football. But they are also soft when confronted with a smash mouth team. Looking forward to it. -
Do a search on seam welding. The guy who started the thread you linked ended up seam/stitch welding his whole car. Seems like an very good idea to strengthen our rusty old chassis. I found an interesting tool the other day. It is a spot weld cutter with a stop that lets you cut a hole through the top layer of metal but stops before it hits the bottom. Would be perfect for cutting plug weld holes. http://www.blairequipment.com/Spotweld_Cutters/Spotweld_Cutters.html http://www.sjdiscounttools.com/blr11096.html Seam welding has the added advantage of sealing the joint against water.
-
I know that stuff works on boats. I have no idea if it would work on a car.
-
Did not retorque the heads after 1 hour of running
Pop N Wood replied to v80z's topic in Gen I & II Chevy V8 Tech Board
As long as the experts are here, is this even possible on an LS series motor? They have the use once head bolts that need an angle gauge instead of a torque wrench. -
Or his lap....
-
Have to rebuild the steering shaft...
Pop N Wood replied to rudypoochris's topic in Brakes, Wheels, Suspension and Chassis
Sort of makes me want to grab up every decent steering shaft I come across at the pick and pull..... -
Im my experience the majority of all backfiring through the carb issues are ignition timing related. A little bit of dirt in the dist cap can cause crossfiring between cylinders. I suggest you start simple. Basic tune up, new cap, rotor, points, plugs, wires etc. Rebuild the carbs if you know that is needed. If you still have the backfire problem, then do a compression/leakdown test. Should tell you the status of the rings and valves.
-
Not going to get much sympathy with that approach. There are no excuses for not answering PM's or emails, especially when you owe someone something. Unless, of course, you have something to hide. How the hell is the guy suppose to track down lost shipments if you won't talk with him? If you know the mail is so uncertain then it is up to you to make some effort. This kind of hoohah pisses me off.
-
Have to rebuild the steering shaft...
Pop N Wood replied to rudypoochris's topic in Brakes, Wheels, Suspension and Chassis
I think he is keeping the stock splined U joint on the rack and just splicing in a new U joint in the middle of the OEM shaft. -
Think power, not torque. Gearing needs to be set up to keep the engine spinning in the meat of the power band. Using steeper rear gears will help you accelerate faster if it keeps you in the power band longer. A car with a wide power band will go faster if the gears are spaced farther apart. The RPM drops more between shifts but hey, thats OK because the engine is still operating at a good power level. Less time shifting means more time accelerating. A car with a narrower power band needs more gears spacing more closely together to get the engine into the power band quickly and to keep it there. Going to 4th gear will improve the top speed of a car only if dropping one gear brings the engine RPM closer to the HP peak. Ideally you want the transmission to keep the engine spinning at the HP peak as the car speed changes. This will give you the maximum theoretical acceleration.
-
Have to rebuild the steering shaft...
Pop N Wood replied to rudypoochris's topic in Brakes, Wheels, Suspension and Chassis
I assume you have read the Borgenson's tech info page Especially their warning on welding. Wonder how hard it would be to grind double D ends on the cut shaft. Also Summit racing carries rod ends specifically designed for supporting steering shafts.