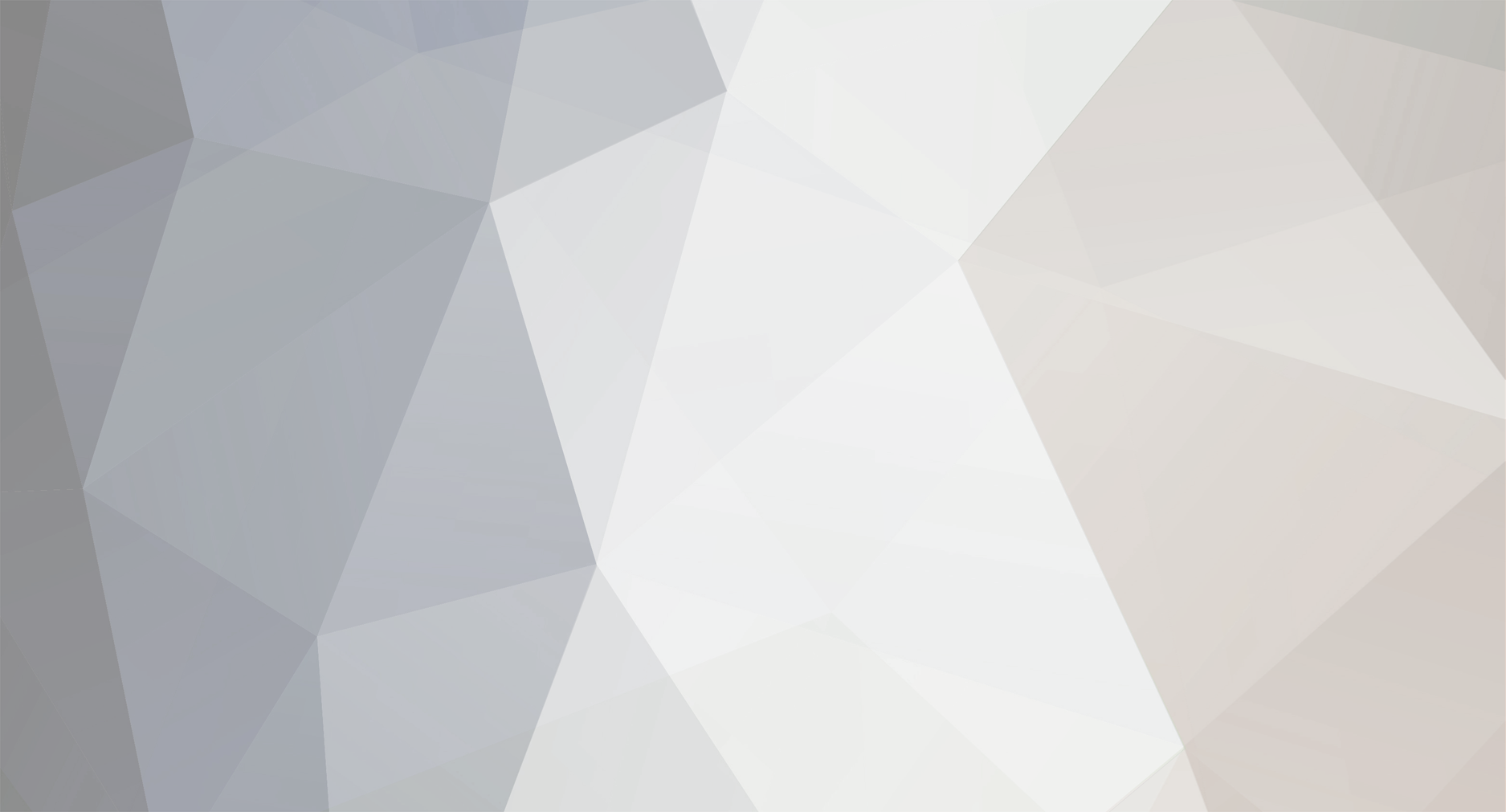
tube80z
Super Moderators-
Posts
1394 -
Joined
-
Last visited
-
Days Won
30
Content Type
Profiles
Forums
Blogs
Events
Gallery
Downloads
Store
Everything posted by tube80z
-
Stiffer springs vs bumpstops
tube80z replied to RebekahsZ's topic in Brakes, Wheels, Suspension and Chassis
True, but much of that can be overcome by how we add the airdam, floor, and diffuser. They don't need to attached level with the car. Perhaps too into the weeds. -
Great rear diffuser article
tube80z replied to JMortensen's topic in Windtunnel Test Results and Analysis
It's worth reading many more of Willem's posts at https://www.linkedin.com/today/author/187006218. While he has worked in F1 for many years he's also an avid hillclimber and has talked about his own car on many of the technical discussions. His post about power and control is quite good as are almost all the posts he shares. Highly recommended. Cary -
Stiffer springs vs bumpstops
tube80z replied to RebekahsZ's topic in Brakes, Wheels, Suspension and Chassis
Actually I'd argue you don't want rake, perhaps the opposite. Primarily because you're standing the windscreen up, which will add drag. Get the car low but perhaps run the tail down or at least try level and then nose down. Cary -
Stiffer springs vs bumpstops
tube80z replied to RebekahsZ's topic in Brakes, Wheels, Suspension and Chassis
I personally would use shocks with a lot of rebound to pull the car down, just like NASCAR. That will allow less air under the car and help with lowering the drag number. The bumpstops I talked to Keith about were actually linear bump springs. The idea being he could run softer main springs at a higher ride height but when running this event lower the car and use packers to engage the bump spring. This would raise the rate similar to running a higher rate main spring but you don't have the rougher ride when using on the street at normal ride heights. These springs can stack solid or be used in combination with other rubber or poly bumpstops when maxed out from aero load. Cary -
I think it's cool they picked a Z. I'm disappointed that with all the professionals involved they didn't really do more. It would have been awesome to see this used to create some really cool one off parts that added more function than the flares. At least that was what I was expecting for SEMA. Cary
-
240Z LS swap : Anyone using the batwing pan?
tube80z replied to Ryan Merrill's topic in Gen III & IV Chevy V8Z Tech Board
A friend of mine had and LS with the JCI kit and we built a brace that turned the standard crossmember into a k-member. This was made from 1 inch 0.095 square tube and had 14 gauge sheet metal welded to it forming a skid plate for the pan. On more than one occasion it took a hit big enough that would have probably cracked or damaged the pan enough to ruin a weekend of racing. If you look closely on the attached picture you can see it. -
TC rod mount ideal location?
tube80z replied to heavy85's topic in Brakes, Wheels, Suspension and Chassis
What is the distance from the stock pivot? I'm hoping to finally get all the pieces in place this week to drop all this is susprog. Cary -
Dry Sumpin' it... What worked for you?
tube80z replied to Mikelly's topic in Gen III & IV Chevy V8Z Tech Board
All manufacturers of hose will have limits for their products. These will lbe temperature limits, working pressure, burst pressure, bend radii, and vacuum for each hose family. Some of the newer high tech hoses can handle vacuum fine (Starlite, BMRS, etc.). But best to check your master catalog to know. If you need to make a sharp turn from the pump to the pan is another issue. So if either of these are the case then you'll need what's called AN hose inner support springs. You can find these at Jegs, speedway, summit, etc. Each manufacturer will have a special version for their hose if needed. The problem is that the pump generates considerable suction and when the oil heats up the hose it gets very pliable. These springs will keep it from momentarily pinching off. If that happens you loose oil supply and bad things happen. It's not as big an issue on the scavenge side but you still don't want a hose getting pulled shut. It all comes down to the pump and the hose rating. It's not whether or not the hose is any good. General rule of thumb is on any of the new high tech hose solutions the non-metal braided hoses will not have enough vacuum resistance to be used in a dry sump system. I'm using BMRS progold plumbing for my dry sump and section 1.2 of their master catalog lists AN 12 hose as being capable of withstanding 28 inches of mercury of vacuum at a minimum bend radius of 2.5 inches between -57 to 400 degrees Fahrenheit. At diameters larger than AN 16 these ratings drop quite a bit. Hope that helps, Cary -
Techno Toy Tuning - GTX2 Control arm and T/C Rods
tube80z replied to ktm's topic in Brakes, Wheels, Suspension and Chassis
I think 10 or more years ago I took a racecar engineering class from ICP. It was two days in a shop for 12 to 13 hours each day. The topic of bumpsteer came up and the shop owner had one of the gauges above. Steve Lathrop said they were fine but there was a much cheaper setup that was faster to boot. His rig was a welded frame with two roller bearings that ride along the plate. He did warn it's best to measure near the actual radius of the tire so not to have error get out of hand. To use this setup you run the wheel up and down and watch the gap on the rollers. Make a change and note if things are better or worse. Repeat until the gap is very fine 1/16 of an inch was good enough for them. Done this way it should go much faster. I made an even cheaper version of this using 2x2s so I could get this done between races. This is more about process and less about tools. The longacre system is nice but unless you need to do this a lot I'd try a lower cost set up. Cary -
Techno Toy Tuning - GTX2 Control arm and T/C Rods
tube80z replied to ktm's topic in Brakes, Wheels, Suspension and Chassis
And they shouldn't. Carol Smith would not be happy. -
Techno Toy Tuning - GTX2 Control arm and T/C Rods
tube80z replied to ktm's topic in Brakes, Wheels, Suspension and Chassis
My guess would be they found it didn't work and went solid. Nice end they used. -
Nice find. Having taken apart Bilsteins and my Penskes you can see a very big difference between the quality of the pistons compared to the BC shocks. Penske have a lot of pistons available in 46 mm that are available as castoffs on ebay from NASCAR teams. Swapping the pistons would be a nice performance upgrade. Cary
-
Dry Sumpin' it... What worked for you?
tube80z replied to Mikelly's topic in Gen III & IV Chevy V8Z Tech Board
Are you running vacuum springs in your scavenge hose? -
LS/T56/240z Project Mentor Wanted
tube80z replied to RebekahsZ's topic in S30 Series - 240z, 260z, 280z
A few thoughts. You could make some nifty rocker extensions like the front splitter to lower the car and keep air from rolling under the sides. You could even turn that into a nice flat bottom too. We need to have a discussion about bump stops/springs and packers. You can keep your softer ride for the street and have 500+ springs that can be engaged by pushing in some plastic packers on the shock shaft. This keeps the car off the ground and when the event is over you remove them and gave softer springs back. Think valve spring on the shock shaft that you can turn on or off. It's really great watching someone so passionate about their Z. You are definitely a true HybridZ person. Cary -
LS/T56/240z Project Mentor Wanted
tube80z replied to RebekahsZ's topic in S30 Series - 240z, 260z, 280z
Love the pics but one thing I notice is that you have a lot of air going under the car. Can you run a rear spoiler? It's pretty amazing what you have accomplished with your car. Kudos Keith! Cary -
TC rod mount ideal location?
tube80z replied to heavy85's topic in Brakes, Wheels, Suspension and Chassis
I'm going to guess 4 inches then. I can try lower or higher to see how that goes. Actually, I'm going to move a number of things around so everyone can see effects of moving pickup points. Cary -
One area to lose some weight is the clutch. Go to a 7.25 or 5.5 multi-plate clutch either use a flex plate with flywheel or integrated unit. That will get you 15 pounds or a tad more of rotating weight. These aren't as expensive as they used to be and you can find good used ones on ebay from the nascar cast offs. Lithium battery is another easy upgrade. Good luck getting the cars all on the same line. That would be very cool. Cary
-
Modifyed Miata power steering rack for 240Z
tube80z replied to BoonZ's topic in Brakes, Wheels, Suspension and Chassis
I wouldn't do the electric assist personally. The woodward rack is a real racing rack and doesn't have all the damping that normal street car parts do. You can change the t-spring in the spool valve for different levels of assist. You can fine tune how it feels and it will have better feedback than most of the electric columns you can get. I have one of the older woodward racks that you can swap out the pinions. It looks like they may have dropped this on their newer racks. I picked up my rack off ebay for $400. It's 19 inch center to center measurement and while Woodward doesn't like it Sweet and others make rack spacers to change the length. You could go this route to get your 22 inch width for a lot less than the new price. Just a thought. Cary- 13 replies
-
- bump steer
- 260
-
(and 4 more)
Tagged with:
-
TC rod mount ideal location?
tube80z replied to heavy85's topic in Brakes, Wheels, Suspension and Chassis
That seems like an easy solution until you actually start looking at doing it. Now you need to add more chassis in front of the car, change to rear steer, deal with rack/oil pan interference. So while it makes one thing much easier you then have many more things to fix. And in the end you adding mass in front of the wheel base rather than moving it backwards. While a small amount it all this adds up. -
TC rod mount ideal location?
tube80z replied to heavy85's topic in Brakes, Wheels, Suspension and Chassis
If you have the ground to bottom of the crossmember I can figure the rest out. I have measurements for the chassis assuming the strut towers haven't been moved. Thanks for the best wishes. She's doing fine but still has a lot of pain. Cary -
1st build, Tube chassis 280z
tube80z replied to mjp147's topic in Brakes, Wheels, Suspension and Chassis
One thing to keep in mind is locosts are mostly built from 1x1 0.065 tube. 0.125 at 2x2 will be strong, hugely overkill, and weigh a lot when you're done. You could easily get away with the 0.065 for most of the frame and if you need to add strength in certain areas then bump it up to 0.095. Good luck and have fun with this. Cary -
TC rod mount ideal location?
tube80z replied to heavy85's topic in Brakes, Wheels, Suspension and Chassis
What is the ride height? I also need to know the top strut location (where the mono ball is). I can fudge a lot of this if you want but ride height will be important. And to set expectations it may take a few weeks to get this for you as my wife is recovering from surgery. Susprog just gives you numbers and those will need to be plotted in excel. I'll overlay the two options so you can see if this is important. Cary -
1st build, Tube chassis 280z
tube80z replied to mjp147's topic in Brakes, Wheels, Suspension and Chassis
My advice having gone down this road is that if you want to make a tube chassis don't start with an actual car. Just measure out the big stuff on the floor or your build table and start from there. Ship in a bottle construction will take 3 to 4 times longer and you run the risk of copying issues from your base car (I would know, my first tube Z chassis is now hanging on my shop wall as an art project). If you really do want to do this you might consider a slightly different track. Cut off the front end and make it from tube. That will take less time and the car won't be down so long. Then when ready do the rear. If you're going to do this you need to have a plan on what it is that you want to change. You also need to be very careful that you don't fall into the trap of using too thick of tube or your tube car will weigh more than a unibody one. People may laugh at that but when you add up everything needed to complete the car you may find that is true. Cary -
TC rod mount ideal location?
tube80z replied to heavy85's topic in Brakes, Wheels, Suspension and Chassis
You could move it to mount on your k-member. That would be slightly forward of the TC mount but allow it to align. That said a long time ago a friend measured all this and used wingeo to see the curves. While it did change it wasn't some major issue. When you pushed the front wheels forward for more caster the curves were very close again. If you want to do the measurements I'll put it in susprog and then we can share the plots so you can decide. -
First impression of Formula Atlantic slicks
tube80z replied to 74_5.0L_Z's topic in Brakes, Wheels, Suspension and Chassis
You can't trail brake effectively that way. So when you put a big splitter on the car and need to keep it flat on the ground in entry that will become important. Dan did mention the car moving too much. Part of that may be too much suspension travel. From the second picture there's too much roll and that has decambered the outer tire. So even if the car feels great there's a higher level to be had. And these spring rates aren't stiff by any means. Starting points for slicks these days should be wheel rate equal to corner weight for no downforce and that can go up to 1.5 or higher. Add XP/EM downforce and numbers over 2 can be used. On radials .8 to .9 seem to be the norm. On track cars running at higher speeds other ideas could be used.