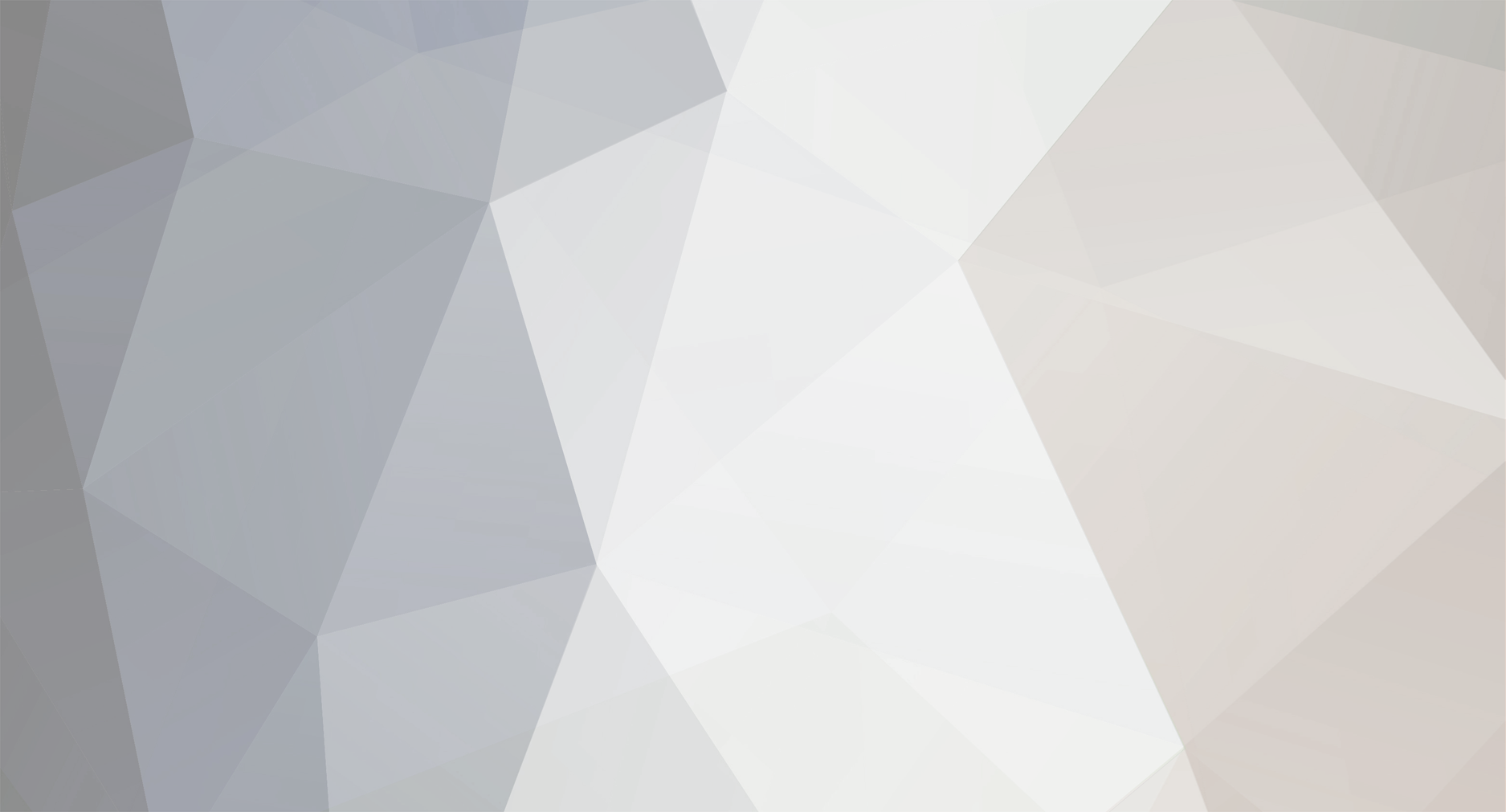
tube80z
Super Moderators-
Posts
1394 -
Joined
-
Last visited
-
Days Won
30
Content Type
Profiles
Forums
Blogs
Events
Gallery
Downloads
Store
Everything posted by tube80z
-
Underwhelming Lap Times
tube80z replied to Twisted46's topic in Brakes, Wheels, Suspension and Chassis
Do keep in mind that the way the crossmember is bolted in is considered a safety feature. It's designed to shear in case of a heavy frontal impact and allow the engine to go under the car rather than through the firewall. The downside to all this as you mention is there isn't a lot of stiffness available for the strut tower or the front suspension points. When you look at newer cars it's interesting to see just how much additional structure they have put in place in these locations. Cary -
It depends on what size chokes you plan to run. 45s with small chokes (aux venturis) flow less than 40s with similar size chokes. If I recall from memory that 33 mms is about the cutoff point where you'll find this difference. This will be an expensive and you want to think about what are future plans for your car. The other option would be EFI throttle bodies rather than carbs. This will be more expensive but probably offer better driveability.
-
Trying to report post, but says I already reported it.
tube80z replied to rturbo 930's topic in Site Support
Thanks for pointing this out. I removed the spam. I'll let Dan know there seems to be a reporting error. -
As jobill stated you need deeper retainers. Nissan Comp used to sell ranges that had to be used for specific depth lash pads. A quick google search turned up many companies that seem to have the parts. You also need to make sure these don't alter the installed height of your springs or you may end up in coil bind or not have the correct seat pressure and then have valve float issues. Sorry to say that the wrong parts were used when you're engine was built. At least you didn't have the rocker fall off and get in their sideways and royally screw up the cam, which happened to me when I learned you couldn't mix and match parts. Hope that helps, Cary
-
The really nice thing about switching to aftermarket calipers is you can get almost any pad in any compound. I've had good luck with Performance Friction. They no longer sell the same material I used but it was a medium torque, good initial bite, great release, and long wearing while easy on the rotors. This was the 01 compound. They now have a new compound that is supposed to be even better, the 11 is what I'd try. Keep in mind when they say medium torque they are looking at braking in the 1.5g to low 2g range. Stay away from the high bite stuff unless you're packing a lot of downforce. Or it will be skid city.
-
I use a higher temp race pad on mine. You need to do some preheating to grid or warm things up some other way. It can make the first run rather dicey if you can't get heat into the brakes and pads. But having consistent braking with the rotors glowing red is really nice. Now only if the car was back together sometime this decade.
-
Body harness wiring diet or aftermarket harness?
tube80z replied to 280Z-LS3's topic in Ignition and Electrical
I think the biggest reason for replacing the harness is its age. All those wires and connections are getting very old and who knows what you have for corrosion and any work hardening of the wire. It's a huge PIA to rewire a street car but you can use the existing harness as a guide and remove/add what you do or don't need and go from there. On modern cars you have a much higher amperage in the charging circuits so all that wiring, fusible links, fuse block need to go. And you're already pitching the engine harness for your Holley ECU so there's little left in the front. You'll most likely replace all the gauges so much of the dash wiring will be changed. And you can see it's not that much of a stretch to just replace it all. In the end you'll probably have a more reliable car and in the event something is wrong you'll know where all the skeletons are buried. If it's any consolation that's my plan on my street car project that I hope to start working on in the next year. Painless seem very proud of their products and I think you can find competitors that are less expensive and feature similar materials and workmanship. Hope this helps, Cary -
Guys let's try and keep this on topic, which was thoughts about the subframe. If you want to discuss business practices that should probably a different thread. I'm not saying you can't do this but this is the drivetrain subtopic. For what it's worth this is nothing new. I have seen/had this problem with all vendors not just Datsun specific parts. Any catalog that has the statement bolts-in is usually code words for if you can fab and have the tools to make it fit. Thanks, Cary
-
Did you weigh before the conversion?
-
You definitely need to do this or you may have issues by bending on your rack and it might feel weirdly stickly. If you corner hard you put a lot of load in via the lower control arm. Cary
-
Moving tension rod mount outboard
tube80z replied to fusion's topic in S30 Series - 240z, 260z, 280z
One thing to add is if you push the wheel forward to gain more caster then that small difference will be closer to nil. Like Jon said if you try and remove via spot welds you better have a number of cutters available. I cheated and bought and air powered spot weld remover. It wasn't cheap but oh boy does it make this easier. Cary -
I can't speak directly about the 280ZX suspension in a Z but we once used that setup in a 510 for rear disks and CVs. It wasn't a bolt in by any stretch of the imagination. I did a lot of research into trailing arms and it seemed like one of the big problems is the toe and camber curves are reversed. If the arms are close to flat in side view when the car is running then a lot of this doesn't matter. Bit if you lower the car and the arms run at any angle pointing up or down then you get a lot of toe and camber change. Any alignment change (toe or camber) will move the suspension pickup points and that changes a lot of other things. Add a lot of power and the car squats getting you into these outer extremes. To get around this we made a custom crossmember that had about half the trailing arm angle (similar to what BMW uses) and fixed the pickup points on the crossmember. All adjustment for camber and toe was on the arms. This along with mounting the crossmember higher in the car allowed it to operate in the sweet spot and worked really well on this 510. Previous attempts with the stock suspension included ever stiffer rear springs, which helped as long as the surface wasn't too bumpy. On my own 510 I tried a Z bar for a while and that really helped with squat and lift. Here's a Sierra example and you can see the fab work to reduce the trailing arm angle. If I were to do it again I would have used the rules that allowed any axle locating device to create an extra arm that would run behind the diff and connect to the trailing arm to control lateral load. Then use the outside mount on the cross member and not hook up the inner mount. You end up with the equivalent of what Subaru uses on many of their cars. Here's an example below, which is from a thread where Richard is talking about what he's going to do on his Z31.
-
Sorry no idea. I looked at the admin section and there's no mention. It's not hidden but I'll post a note in the admin section to see if anyone knows why it isn't there. Cary
-
set up wheels ( for track or general...)
tube80z replied to nzarano's topic in Brakes, Wheels, Suspension and Chassis
The strings are a box around the vehicle. You don't really need to be centered but you do need to be perpendicular to the front/rear, which often ends up referencing a body panel or a crossmember. This is a good example of the work involved, https://www.turnology.com/features/easy-accurate-inexpensive-do-it-yourself-vehicle-alignment/. It looks more complicated than it is to do. You can also do the same thing with jack stands and fishing line but that takes a little longer to get setup. There are a number of videos on youtube that show how to do it various ways. -
set up wheels ( for track or general...)
tube80z replied to nzarano's topic in Brakes, Wheels, Suspension and Chassis
The easiest alignment system I've found are strings. If you take some time and make a simple jig the is centered on the car these are easy to setup and use. If you don't need to worry about the car being squared up toe plates where you use two tape measures are also a good choice. But whatever you do will require access to the adjusters. The trickest system I ever saw was from Riley & Scott on a world challenge touring car. They had rods they screwed into receptacles on the frame. The had a laser and a target on the same end and on the opposite end you'd mount a mirror to the their setup wheels, which in this case were a special set of tires that were never used mounted on modified wheels that allow attachment of the mirror. The laser would shoot down the side of the car parallel to the frame and bounce off the mirror and back to the target. Accuracy was claimed at one tenth of a degree according to one of the mechanics I chatted with. He even let me inside the pen for a closer look. I like to go to the pro races and watch the top teams when they do boring things like basic maintenance. Setup wheels are used a lot and often while sitting on scales. You have much better access to all the adjusters and can do easier brake maintenance, ride heights, and so on. For most of us this would be a shop only item to use. -
Mine all cracked in the bend. The bolts into the body were still tight and a cursory visual inspection missed it until I pulled the diff and it was plain as day. I mostly had problems with the right side. Another SCCA EP car a friend has had similar handling issues so we looked closely and his plates had been cracked too. Same spot also on the right side.
-
Hi Luigi, it allows the strut another axis of movement that isn't putting bind on the strut insert. If you have stock rubber bushings those probably allow enough movement this doesn't matter. WHen you take apart the rear struts and try to line them back up to go on the upper mount you often see how small changes to the pickup points (toe/camber) make it really hard to get back where it needs to go. The stiffer you make the bushings (poly, rod ends, or sphericals) there's less give needed to follow the path laid out by the upper mounts. There's a lot of good info in the suspension section stickies that discusses in deeper detail. I'd recommend the brace for any V8 or higher powered street car. Years ago I was sitting in a friends V8 car and he tells me to watch the tire from the side mirror. He proceeds to power brake and I see the rear tires toe out and not a small amount. Even on a lower powered car if you corner really hard I'd expect this isn't helpful. The brace helps to reduce this.
-
What you want to do for the rear brace is triangulate the lower pickup point with the rear diff stud (orange line). Somewhere I have a picture of this but I can't find it so I used a random image that's in my downloads folder. Not my car or a friends in case you're wondering. Some company in the UK that does rebuilds. Another item to add to your list are toe-link rear arms if you don't already have them. This helps reduce side loads on the strut from alignment changes, which reduces friction. On my street car I've been looking at a bracket that bolts under the normal spindle pin location that allows a control arm using rod ends to be mounted in double shear. And that's lead to more rat holes and I think I'm leaning towards a fabricating housing that uses nothing Datsun on the outer end to keep costs down. Somewhat similar to the Apex Engineering stuff but different outer mounting and a simple bolt-on hub assembly. Other easy items to think about. 1. Droop limiters 2. Hanging ARBs from rod ends (lowers friction) On the front you can do something similar to the yellow and orange lines in the attached image that helps stiffen the suspension mounting points. Rather than bolt things to the TC cup those could be welded and the tubes could mount as plates under the mount. They would stack and be bolted in a sandwich from the bottom. There's a lot of things you could do for engine bay bracing between the strut towers. BMW touring cars had this cool tubular structure that was connected to the strut towers, frame rales, and lower crossmember. It looks like a truss in the engine bay and you could easily hang your motor from it. That would allow you to ditch the normal motor mounts. And if you pick up the bellhousing with mounts you can get rid of the transmission mount. My old race car ran solid mounted this way and it worked really well. Hope that helps, Cary
-
Time to move the radiator back to the hole you have there I'm sure you've probably already been thinking about that given some of the FB threads. Great to see all the updates. Two things I'd add in case they aren't done. Run a brace from your rear diff mount down to the transverse link, The will help flex that does lead to rear toe changes. Also make sure to inspect those two bits of medal as you have enough tire to crack them. I went through a few sets before adding the braces and never had a problem after. You also need to put bolts into the ebrake bracket that is on the strut. Those little threaded holes can lead to cracking the rear struts if you don't.
-
Actually the benefit is a lot more than you might think, at least for a racing car. I did this with an old car of mine where I set the motor back so the 1st cylinder was on the axle centerline. To do this you need to cut into the firewall. Even moving the engine back to where it almost touches will give you some benefit. It's mostly on how fast the car will change direction. At the time we had a number of cars with identical mods and suspension tuning. The engine setback car was always quicker than the others. The advantage depended on the track design so if there were more changes of direction then it was a bigger gap. The total change for my car was about a half a percent of weight shift to the rear. All the easy things were already moved towards the rear axle. Once you've move all the easy parts to the back of the car then this can be looked at. Mine was a hack job at best (finishing someone else's project). The motor mounts were done using a flat plate that bolted to the block and allowed the motor mount to be moved a couple of inches. Similar thing done on the engine crossmember mount location. Sorry, photos have long since gone for all this. You do need to be mindful of the oil pump interfering with the front ARB. If you go far enough then you have the rack/crossmember to deal with. Hope this helps, Cary
-
For panels that overlapped in my car that needed welding I've used a zinc based weld through primer. My only testing was on some metal I removed from the car, sanded down, sprayed with the weld through primer, and welded up. I left these outside for a couple of years. They had the usual surface rust but nothing major on the weld areas. This isn't much of a test but that's what I've done for overlaps. This will be for a race car that is mostly pampered and will only get wet in occasionally. What Ironhead describes seems to be how most of the OEMs do it now. You need somewhere for trapped water to go and use a lot of the new seam sealers. Ever take a new car apart and notice how much of that stuff is everywhere? OEMs aren't into spending money on things not needed so that's probably a good thing to follow. Hope this helps, Cary
-
I'd recommend more than just the hoop change. Try sitting in the car with a helmet on and you may be hitting the upper halo bars. Those need to be much closer to the roof and often require a couple of bends to make it back to the main hoop. It's your money and this is one of those items you hope to never use but when you never know when you might.
-
ANOTHER Datsun Z/LS3/T56 Swap Thread
tube80z replied to Ironhead's topic in S30 Series - 240z, 260z, 280z
You've got it. At first it was for easy on/off when loading/unloading from the trailer. But it worked well when jumpings curbs, various offs, and occasional high angle track entry. -
ANOTHER Datsun Z/LS3/T56 Swap Thread
tube80z replied to Ironhead's topic in S30 Series - 240z, 260z, 280z
I looked through my photos sure I had taken pictures of how we did this on a friends Z. Good thing we didn't bet on it because I would have lost. Every time I do this it's a little different. For just the splitter blade (flat piece, whatever we want to call it) we fabricated what was essentially a outdoor gate latch as the rear pivot and cables connected the to a frame that was mounted to the blade. This allowed you to lift up the front or side if it hit anything but still connect to provide downforce. As we had no idea if this would hold at 150 MPH the frame was very basic and light so if it folded under or came off it wouldn't hurt too much when ran over. To seal to the airdam edging material was going to be added that would mount outside of the bumper cover/airdam. At speed I figured the leakage would be minimal. My FP car had an airdam and one-piece front end (hood, fenders, grille) and separate airdam with floor (no splitter) that was reinforced with a metal frame. The front end was held down with hood pins that floated on springs so there was some movement allowed. The airdam had a frame behind it and that mounted to a tube that connected to the stock bumper bracket location. I used only the rear bolt hole and it was mounted so it would move up or down and there was a bracket that connected to where the stock hinges were that captured this tube. It was L shaped and the bottom limited the bumper bar from going down and there was an upper limiter on top that used a valve spring to keep some pressure on the tube in the downward location. I don't know if that was needed or not but I had seen a similar setup on a wrecked Ferrari challenge car. The used this for allowing splitter movement. The airdam mount was was tubing that slid over a pin and held in place by a spring clip. I had to be able to take it off to load and tie down the car. Previously it was all connected to the front and and couldn't be removed without much effort. My new car (if it's ever completed) will use a setup like almost all the current Trans-Am and GT1 cars do. That's a seperate frame that hold the splitter, airdam, radiator and front ducting that bolts up to the car. The lower connection is in a cup that allows it move forward to a degree but not rearward. So if ground a corner the body can lift up a limited amount or like loading on a trailer. Since this will replace the core support being able to remove the engine will be easier too. I don't know if the attached image will help or not. Happy to try and draw it out a little better. Cary -
When you blot up the tranny make sure to try the clutch fork with your hand. It should have a small amount of play before engaging. If you can move it a half inch or so the release bearing collar is too short. If the lever has no free play and you cannot move it then you probably have top long of a collar. I've screwed this up so many times over the years and finally came to my senses about checking up front. You can measure everything on the bench too and come to the same conclusion but I'd still try it by hand to make sure you don't have some other problem related to the fork.