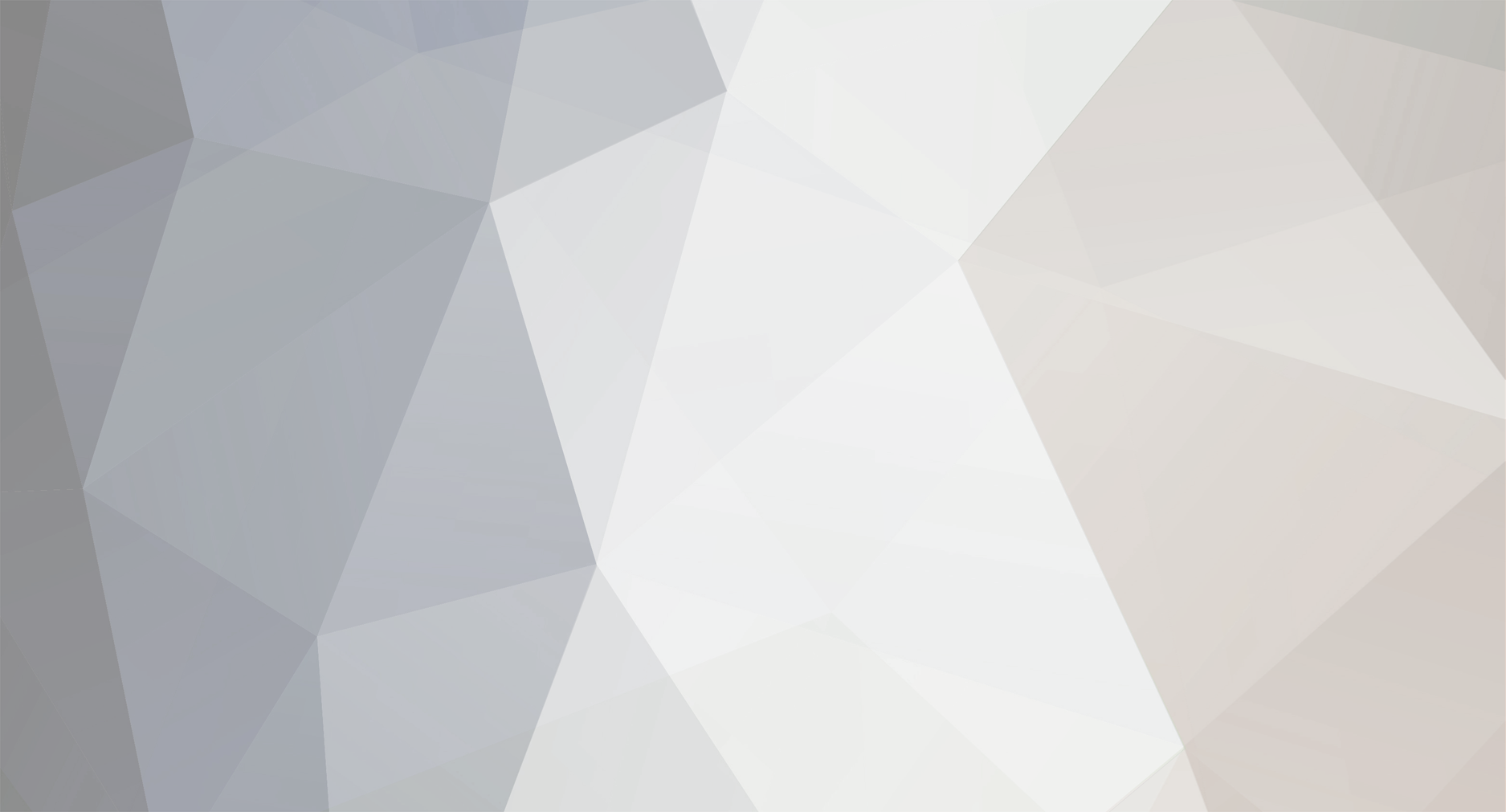
tube80z
Super Moderators-
Posts
1394 -
Joined
-
Last visited
-
Days Won
30
Content Type
Profiles
Forums
Blogs
Events
Gallery
Downloads
Store
Everything posted by tube80z
-
My Dream LS7GTZ.......project underway
tube80z replied to cobramatt's topic in S30 Series - 240z, 260z, 280z
How much weight did you drop? -
My Dream LS7GTZ.......project underway
tube80z replied to cobramatt's topic in S30 Series - 240z, 260z, 280z
Just guessing since it has a new front clip the wheels are moved forward. Easy to add fender behind them. Cary -
Seeking air compressor recommendations
tube80z replied to RebekahsZ's topic in Fabrication / Welding
A blast cabinet goes through a lot of air. I wouldn't use that as the main planning priority personally. The one thing I didn't mention is that I have a special connection that is before the main regulator (I usually run around 100 PSI in the main line), which is connected to the tank. It shuts off at 155 PSI. I use that one every now and then when I need some extra oomph. Nice option to have if you have a few tools or tanks that need the extra pressure. I have a tire tank that can hold 175 PSI if needed. I've used propane tanks converted to do this too. Cary -
Seeking air compressor recommendations
tube80z replied to RebekahsZ's topic in Fabrication / Welding
My only advice it mount the compressor up high if you can. Then you can have the floor space for something else. Mine is in a loft in my shop and out of the way. I looped my main air line and all drops come off the top. Main lines are all angled down to one corner and I have drains at all corners. I have a special filter for my plasma cutter (looks like it uses toilet paper) and a desiccant system for the main shop. Probably not as good as an air dryer but then again this is non-commercial. The compressor is an old 7.5 HP Costco 2-stage cast iron compressor. Oil is synthetic and it's been in three shops now and is about 16 years old. Having the compressor raised makes it easy to drain the tank via a remote line I have running from the bottom. I use a contactor as a remote switch to turn the compressor on and off. Nothing fancy has worked for years. My blast cabinet is the only thing that makes it run continuously. The tank size is 80 gallons. If you want more air volume you can use a propane tank I got an old 150 gallon propane tank I was going to add but decided I already had enough capacity for the moment. Hope this helps, Cary -
Sounds like a great idea. I was looking to do the same thing. Converting to servo operation and using modern controls from a 350Z. Cary
-
jmortensen's "while I'm at it" roadrace/autox project
tube80z replied to JMortensen's topic in S30 Series - 240z, 260z, 280z
Love how the camera shakes when it revs. You beat me to startup -- great job. Cary -
Interesting, I never would have thought to use pistons for an ATV/MC on a car. You can download the Penske manuals and see diagrams of each and the curves they generate, which is maybe what he did. Unless the missing bit is missing was how he figured out how many shims to stack on these to get them to work. I also thought the comment about nitrogen pressure changing the dynamic roll center was interesting. Props to being willing to do this yourself. That's a lot of work with some odd components to figure out. Not a path I would have ever taken. Cary
-
Woodward also makes some nice pieces. Often can be found on ebay from ex NASCAR at bargain prices. Or you can add in the OEM collapsible pieces somewhere in the column. Cary
-
It's not cheating when allowed in the rules But I do think there's a legal way this can be done with the spacers. If they had an angle to them you'd move the steering arm. I can find no spot in the SCCA rules that defines how the spacer must be made. You also have the steering rack bushings that can be made different thicknesses to change the position of the rack.
-
You have been given you a lot of good advice. A lot of what will make you faster depends on you and how you do things. Are you the feeling type or the analytical type. Do you need to find things out on your own or do you do well with coaching. If you know those things it can help you find the resources you need. That aside one thing that is often overlooked is a good notebook and set of notes. You should have everything in these. From car setup to all lap times and printouts from the AIM. I keep detailed notes of what the weather was and what the track and air temp was when I was running. This might seem like overkill but as you have more time later in the week you can look over your notes and think about what you did and how the car was working. Many times you may find something you didn't think about when you are pressed for time. And when at the track you have a reference you can use for what to do, which is assuming that you are making setup changes. Even things as simple as what starting tire pressures to run. And what is the best hot pressure I should be at. With the gopro you can get a cheap little program (race render) that lets you overlay data onto the video. And if you have a couple of cameras (one that can see what you do and another for where you are on the track) you can see areas from the data where you can improve. To answer your question about the investment to map the chassis for building a suspension model it probably won't make you any faster at first. But if you know what to do with the data or where to ask the right questions (wonder where that could be!?) it can help make you a lot more consistent and help you with what to do next. Each car is just different enough there's no one size fits all approach. But as Clark mentioned you want the arms close to flat or pointing down when looking at the tire just a little. And if you have actual suspension model you can see what each end of the car has for various suspension curves and map this back against track data. This would be used to try and set the cars alignment and ride height in the best spot for the track. This sometimes will make you faster but generally it makes you more consistent and leads to better tire life.
-
Which one? I think there are three now that have died around oil related issues but I may be miss counting. We also lost an engine from counterfeit lifters that came apart. All were using a 3 qt or whatever the large one is. It was plumbed in the front of the block same place my dry sump will be. It cost $6 for a straight AN port to fit the plug removed. We used the manual valve and the electric valve but not the fancy EPC valve. I'm with Mike in that if you have a couple of oil events back to back I don't know if the accumulator is going to be of much help. I also had a chat with Kevin Johnson and he was telling me one of the issues that they ran across with accumulators was what happens when you push good non-aerated oil into the oil galley when the pump is pushing oil that has a lot of trapped air. The short version is that it doesn't always go the way you think it does. Can't say for sure in the LS. Many people use these systems and they work fine. But once you get to a certain performance level they won't work. That's when you start looking at a dry sump. A long time ago I thought they were overkill for what I did. But tires have gotten much better and dabbling in aero has pushed corner limits beyond what the wet sump can handle. You can do a dry sump for about $1500 to 1800 with some ebay shopping and perhaps less if you get a good used pump and some deals. If you use a 4 stage pump you'll also get a lot of vacuum in the crankcase so if you're looking at add a vaccum pump you won't need to bother. For an autox or hillclimb car I would recommend getting a water to air heat exchanger as it will get the oil up to temp quicker. I think for street tires at a track day the scraper, pan insert, and accumulator will probably be okay. If you add aero, higher rev, and/or slicks and the cornering is getting close to 2Gs then you're playing with fire if you don't upgrade. When you get close to 10K in a rebuild and it costs $1500 for a race weekend you don't want to be dealing with oil issues. And if my engine goes in the middle of a season I don't have budget to rebuild nor the time to get it fixed quickly. Hope this helps, Cary
-
I wouldn't do it so big. I'd only do a 2x2 or 2x3 size area. I don't think any larger will buy you anything extra. You also have the door side that can be boxed from the door post to the fender liner insert. Cary
-
A couple of options I could see. One is to change the tube you currently have from the rocker to rail (TC connection). Remove this and add back in so that it forms a triangle with the cross tube you have from the rocker to the rail. Option two is to add folded sheet metal on the firewall where it bends and bring this straight down and fold back to the floor. Connect to both frame rail and rocker. Then add in the tubing. The benefit to this option is you don't have to remove the existing tube from the rocker to the rail. This will be stronger for not a lot more weight. On the side of the car (not shown) where you have the tube going up you can fill in the area where the fill panel to the fender is. This is covered back to the door post making another box. That's about it for easy. You may want to look at seeing if you can add in a crosspiece between the frame rails that would connect with this new crosspiece/torque box. With the exhaust on the side it should be opened up just behind the flywheel area. If you need some pictures let me know. And to finish use the BMW example. Your K-member could connect to the TC box and back to the rocker rails. And you can can have a skid plate that connects the crossmember/k-member, TC boxes and across the back of the engine. The more complicated mods involve taking the rails apart and adding metal/tubing inside and working that in. Hope this helps, Cary
-
Yeah, I think we all love project Blinky. I have learned a lot from those two guys even though they act like they don't know what they are doing half the time. It's definitely an act. I have been doing CAD for some time though so that's nothing new. I do think you should sue BMW for using your K-member I think adding a skid plate underneath that connects to all the points would add a good bit and it's not a bad idea to have that under the car anyway. One thing to remember when you build any prepared car, or your V8 supercar, is that you don't build that cage and bracing in the car. Those bits are built and the car is added on around it. I used to do the former and got much smarter on my new car. I have taken major sections off by removing the spot welds and then make whatever I want underneath and then add back only the bare minimum. It's also given me a lot of ideas for how to make a street Z much stiffer. But that's about the only way the welds can be done on some of those cages. The main tubes are the required thickness for safety and all the rest are as light as needed by FEA. There are a few videos on youtube that show the triple 8 cars being built and you can see that the newer cars have even more cage bracing. And the most amazing rear live axle I have ever seen. When you first look at these designs they seem silly. But the stiffer you can make the car and still make weight the better. The reason as I understand it is since the chassis is a spring it requires you to raise the rates on springs and dampers to meet the targets you want for axle stiffness. The floppier a chassis the worse this is or you need to have a completely different method for determining the chassis setups. When the V8 guys went to the new COTF it caused them a lot of headache because it isn't as stiff as the old car. A number of drivers also complained about the feel of the car as the stiffer chassis is more responsive. A lot of the rules of thumb have changed. I have heard you need 5 times the spring stiffness for the torsion, also 10, and 20. It's really related to the constant learning in racing. I think Jon has some good shots of his exhaust. That's the one area I forgot to document on Dave's car. He did a 90 at the bottom of the headers and came out though/under the lower frame rail behind the TC box. It was mostly the thin lower section but he also had to notch the main rail a little and added back in some structure. I wasn't too worried since this was also tied to the cage. From there the pipes came out and around the front of the rails and down the side of the car. How close you can go depends on the mufflers you use. There are two downsides to this mod. The noise goes up and you need to be careful when getting in/out. But working under the car is much easier. Transmission and diff swaps are a lot easier and can be done on a car when it comes in off the track if needed. Hope this helps, Cary
-
I would agree. I saw all this after I had done the Nascar style door bars on my cage. I'm pretty happy to have three tubes pressed out to the door skin and hope I never hit anything with them but in case I do there's almost 12 inches to me. I moved the seat against the tunnel and will be mounting on tubes that are connected to the cage. Perhaps the following picture of a V8 Supercar might help. There's a lot to steal from this design. They have connected the sides of the cage to the main rails and the seats float on this. This is more or less what the inside of my car is starting to look like. The key is to always make triangles. As long as you do that you add strength. The Z car is missing structure that connects the front frame rails to the rockers as well as a triangulation to the strut tower from the outer rail. This is all standard on new cars. There are a few examples I've seen that may be of help. These are both for older Mustangs but the front structure is very similar, http://www.sn65.com/fire%20&%20ice%20unibody%20reinforcement.htm and http://www.stangnet.com/mustang-forums/threads/torsional-rigidity-test-67-coupe.723029/. On the Mustangs the export brace is a large contributor to torsional strength. And it's very similar to the bracing done by BMW. So I think that would be a good. There's also a series about modifying a Mini that's really good called project Blinky. They are building it like a real unibdy using folded sheet metal and spot welds. There's a lot of ideas I got from it. You can find it here, https://www.youtube.com/user/badobsessionmsport. Hopefully the V8 supercar pictures and the export brace idea help. On my car I have a bar that goes across the front of the unibody just behind the rocker horns and will be tied into the front frame rails. I have just enough room to run this under my transmission as I have moved the exhaust to run down the side of the car. This is something I just found I could add and is not shown in the first pics I posted. I will be connecting the structure above to this. Depending on your transmission you may or may not be able to do do this. But I would think you could make something similar to the skid plate brace the BMW used connected your crossmember to TC buckets and perhaps a few more attachment points. That would serve dual purpose as a skid plate and also connect all the lower suspension points to the frame rails and rockers. So would I.
-
So thought I'd try and upload some photos of the ideas I mentioned. I'm not sure this will work so well but here goes. This past season I saw a tire come in on an older car and the driver was lucky not to have their foot broken. I got to thinking about how to stiffen all this up. I wanted all the tubes to connect so that if the wheel/tire came back at me it needed to rip apart a lot of metal, which hopefully will stop it. This also serves to work as additional triangulation to make the car stiffer. I think you have something similar to this but for adding structure to the front of the rocker to the main frame rail I was thinking along these lines. My car was modified so the cowl is now removable. This allows me to add some more triangulated structure to replace what was there. I have been researching side impact and found that there's some research around the Prodrive mini that looks interesting. I don't think you'd want to redo your door bars but they found this setup to work very well, And In reading some papers about side impact strength it seemed like adding a cross beam to the floor that connected the subframe connectors to the rockers and lower door bar would make a lot of sense. There's some data in this report, http://www.dynalook.com/8th-european-ls-dyna-conference/session-1/Session1_Paper2.pdf. If you Google body in white topology studies you can find a lot of info about strength and accident testing from the auto manufacturers. I noticed there's definitely a trend in making the floor much stronger and connecting the sides. I did find a few interesting ideas on retrofitting from some rally sites. One idea that seemed very interesting was to mount DOW IMPAX foam between the seat and the and the side of the car. For my hillclimb car I'm using left and right nets along with a normal window net. I have a basic Kirkey road race seat and I'm building my own halo wings and a basic frame to stiffen the seat. I found some research that indicated the need for special padding to keep from getting lower back injuries. You can read about it here, http://www.802solutions.com/crash-pad-products/. I don't know if you're interested but I found some ideas on how to make the car stiffer. A lot of them come from a really cool tech talk from BMW around the new M4. I couldn't believe how stiff they were able to make a street car. http://youtu.be/8CJ6IwVzV-A I have another project for making a fun to drive streetable car and this looked like a good fit. For cooling there are a couple of options to look into. Evans cooling, which is essentially a zero pressure option or if you don't like that then retrofitting to a constant pressure system. I saw these on a lot of the cars at Pikes Peak when I was there, http://www.crracing.com/cr-designed-products/pressurized-cooling-systems. Hope this helps, Cary
-
Overall I like your car a lot. I do have some ideas on how you could do some of the detail work a little better. I'm not sure you want to hear that now as you'd need to redo some of what you have done. Specifically how you are protecting your feet. That could be turned into a pickup point for the suspension. The one area where these cars cars are weak is the floor. you have an extra tube along the rock, which helps a lot. I'd personally consider running a tube across the car about midpoint in the floor to connect both side. And something similar across the back. These can then be used to solidly mount the seat to the cage. And if you desired you could add more triangulation to make the car stiffer. You have connected the the entire side of the car from rear strut to lower rocker, which is really good. A lot of builds miss this. I can't tell if you welded the rear hoop into the roof. That's a similar mod to the dimple plates. Remember to glue in the windshield if you're doing glass. It will add to the shell's stiffness. Overall I think you did a really nice job. Pikes Peak would be a great place to run, I'm totally envious. The one thing I saw when there was you need a lot more cooling that anywhere else in the world as the air is so thin. You may want to think about water cooling brakes if legal and/or a larger radiator and oil cooler. Looking forward to seeing this happen, Cary
-
Sorry to hear about your back. I have been in your shoes (major back surgery) and can offer you need to be very careful in your recovery. I have all my lumbar and S1 fused and I can tell you that you need to look at some of the newer options out there. I think a fusion is a medieval surgery and often leads to needing more of the same in the future. I wish no one the level of complications and shit I have had to deal with. I really hope plan A works for you. And if not be very careful what plan B is. As you now well know your back isn't something to mess with. Cary
-
The windage tray info can be found at the same site as the scraper. Interestingly the latest issue of Engine Masters features a 436 CI LS running one of the teflon scrapers and windage trays from crankscrapers.com. They also did some very interesting things to control oil. They completely tubed the came and added external drains back to the pan. I'm thinking that's pretty high dollar stuff but depending on what you do perhaps an option. It looks like a scraper, external drains, a good, pan, and one of Vern Schumann's oil pumps might be all that's needed. Here's a link to the modified oil pickup tube, http://schumannsdynamicperformance.carshopinc.com/product_info.php/products_id/131438/LSPSF My comment about the accumulator is not that it won't work but if the block is not setup to send oil to the mains first and you inject at low pressure it will most likely end up going to the cam and heads first and then if there's any left to the cam bearings. Where is your pressure sensor port in all this? The block I have in my shop with the big hole in the side was running an accumulator. I don't know if there's an easy way to inject oil into the lower end and block that from the top but I think that's what's really needed when the pressure drops. Perhaps this was all really bad luck but I have too much money in my motor to take things to chance. And I'm also concerned because I expect my car to corner at a much higher level than the cars that were data logged, hence the dry sump. Hope this helps, Cary
-
I ran across an interesting article on how to upgrade the stock type LS pumps. Take a look here, http://ls1tech.com/forums/generation-iv-internal-engine/1366685-schumanns-sale-lsx-oil-pumps.html. One interesting item to note is that one issue noted causing problems is the screen on the oil pickup. This should be made much larger not to cause problems. I also found the external bypass interesting. Supposedly this solves the issue of running the pump at speeds higher than 6500 RPMs. Cary
-
I'm sorta late to your party and there's a lot of anecdotal evidence for LS oil issues. I've been told by a number of people that this isn't an issue at all and I'm more or less overthinking it. I have been a part of a few tracked LS engines and seen them die. From what I can tell the LS engines have a shit oiling system compared to what Datsun originally gave the Z. The first problem is the block is not set up to oil the main bearings first. This is done for a production engine so you don't have any rattles that drive warranty claims at cold startup. If you look at the aftermarket blocks the oiling is setup with what's called mains priority. I think there may be a few simple tricks to fix this but I haven't tried them so I won't add to speculation. I was thinking you might be able to plug the upper galley and then feed it via an external source you could restrict. For the more adventurous have at it. One the oil gets to the heads it's more or less dumped back onto the cam and the crank. If you haven't drilled holes in the lifter trays those will fill with oil too. I can only imagine how frothed up the oil will be from being dumped on all the rotating parts. I saw an interesting trick I wanted to copy on my engine where a baffle above the cam that directs the oil onto the cylinder block walls. This was in one of the Engine Masters magazines and was claimed to help with HP. It seemed like this would help to keep the oil from getting air into it in the first place. I took a good look at the ideas from Ishihara and Johnson (http://www.crank-scrapers.com/Chevrolet_LS.html) and bought there teflon scraper. For a little more than the IR piece you can get there laser cut scraper that is a lot better design in my opinion. And if you're handy (who here isn't?) you can copy the windage tray. From reading a lot of various articles it sounds like the oil gets wrapped up around the crank as windage and what doesn't goes up to the heads. And if you run them hard and long enough the quality and volume of lubrication gets to the point where these engines let go. I have a mockup block from one of these episodes that has a very large hole in the side. So here's what I do know. If you log the oil pressure and you go around a left hand corner for more than 2.5 to 3 seconds and you're pulling over 1.25 Gs then you'll probably end up with zero oil pressure. You can overfill all you want and run an accumulator but it won't do a lot of good giving the oil is headed upstairs first. I also found that if you run down a long straight and jump on the brakes the pressure can drop a lot. I got to help out at a circle track event and my friends LS powered car would completely fill the right side head until it came out the top. From reading and talking to a few other people I've been told that this is partly a oil drain back issue and partly related to too much oil going to the heads. Jon and Richard already mentioned external head drains. Ideally these need to be a number 8 fitting and hose (1/2 inch). The heads are drilled and tapped in the back in the valve spring pocket area. I've uploaded a picture of this done on a SBC to give provide a better idea. We tried unhooking the PCV hose on the circle track car and hooking it to the dipstick tube. This worked much better than you'd think. Up until that point the PCV system (one of the can systems) keep filling and we'd lose over a quart in a couple of laps. I think if you run a scraper and windage tray, drill the lifter holders, and have external cylinder head drains and do the overfill trick you can probably deal with corner under 1.25 Gs. Once past the 1.25 G cornering level I think you need to look at a real dry sump. If you can do some ebay shopping you can put together a good system with a new pump for under 2K and probably closer to 1500. I did mine using a used pump for around 1250. That wasn't too much more than an accusump, windage tray/scraper, special pan, and PCV system. The trick to making the dry sump cheap on the LS is the drive system and mounts. You don't have to spend the money for the ATI damper unless you want to. And a used tank and lines can save you a ton of money. You do need to be able to clean all this stuff and fab mounts, which isn't any more difficult than putting in a motor. Hope this helps, Cary