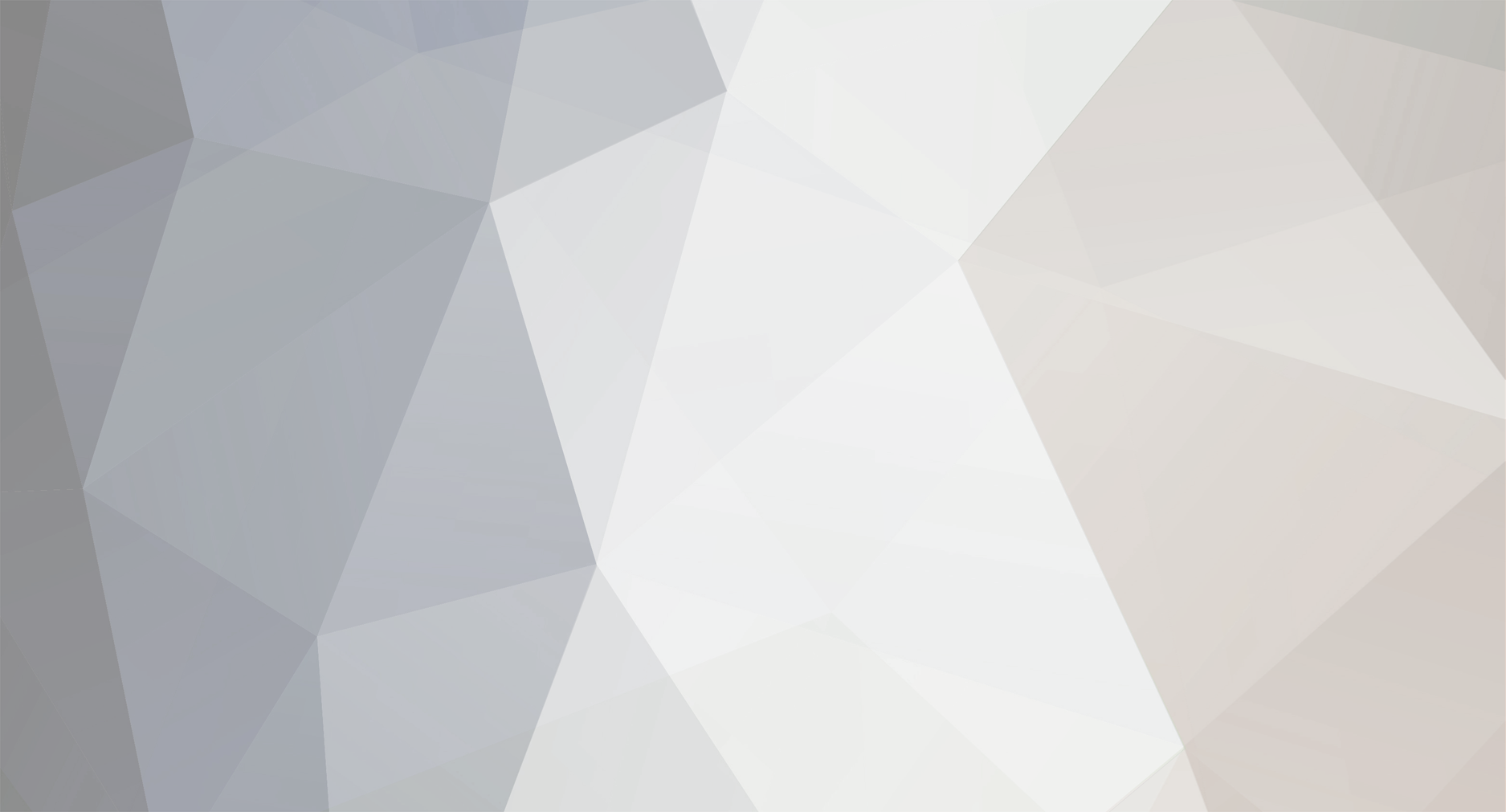
tube80z
Super Moderators-
Posts
1394 -
Joined
-
Last visited
-
Days Won
30
Content Type
Profiles
Forums
Blogs
Events
Gallery
Downloads
Store
Everything posted by tube80z
-
First impression of Formula Atlantic slicks
tube80z replied to 74_5.0L_Z's topic in Brakes, Wheels, Suspension and Chassis
That's how they are supposed to feel. If you're trying to get them to feel like hoosier radials you'll need more pressure than where they make max grip. The slicks should be about half for your suspension travel when everything is working correctly. It took me a long time to figure that out even when told it was right. Your pressures are high but not completely out of the realm of reason. A good picture head on of the front at max load will show if you need camber or air pressure. I have a favorite place where we run to get these. I can point you to some examples if that would help. If there are properly inflated more camber or more caster might be needed. I would lower the rear of the car until the spring rattles and then bump up the rate to around 550. I ran rear limiters with just a small amount of drag on a 0.40 feeler gauge. If the track was smooth I ran less and less front droop often down to 0.25 inches to control roll and make the car turn in faster. If you have big bumps you may need to limit the same as the rear. I missed the second pick of your car. It looks like it's rolling too much in that photo. I think you tried the limiters in the past but can't recall. I would do that again and see if that helps with the rolling. I'd also be very tempted to increase the springs rather than add front bar. Springs will reduce the amount of pitch and roll compared to just the bar. Your spring rates look close for the car on radials. -
First impression of Formula Atlantic slicks
tube80z replied to 74_5.0L_Z's topic in Brakes, Wheels, Suspension and Chassis
How much weight do you have on front? Any tire temps? You're pressures look too much to me for Avons. Maybe you arrived there by experiment but we're usually down in the 19 to 22 range. As far as springs go for the Avons I'd be 100 to 200 lbs/in more. You're car is around 2500 to 2600 lbs. with you in it? Cary -
First impression of Formula Atlantic slicks
tube80z replied to 74_5.0L_Z's topic in Brakes, Wheels, Suspension and Chassis
I was saying from the picture it looks like the front is compressing (Dan's pic). From your info I'd go with more rear spring to keep it from coming up. And since you don't have a rear bar perhaps a Z bar instead. Another option would be more tire pressure. Until we see pics it's shooting in the dark. And then we have that issue of you running the wrong tires that won't work on the car If I can ever get you down to Medford we'll see what it's doing and get it fixed. Cary -
I think the sharing isn't setup for public on your pics.
-
Drill out a large nut and weld that to the tube. Or buy a tube already setup with flats. Both are options. Cary
-
Interesting project. Keep up the good work. Cary
-
First impression of Formula Atlantic slicks
tube80z replied to 74_5.0L_Z's topic in Brakes, Wheels, Suspension and Chassis
Raising the rear will help it turn better and should increase rear tire temp. But at the same time it will not put power down as well. Adding spring will do both but hopefully won't hurt forward traction as much. Add Avons and this will all probably change. At least it runs and doesn't have any issues that need to be addressed outside of tires and initial setup. -
First impression of Formula Atlantic slicks
tube80z replied to 74_5.0L_Z's topic in Brakes, Wheels, Suspension and Chassis
Dan has some good information about caster above. I don't think that is the problem here but it could be adding to it. I say that because we've had two cars running the FA rears all round that were setup very close to Jon's car and neither of them lifted tires when going into tight turns under braking or in transition. After thinking about this for a while the car is rolling on a diagonal on the inside front to the opposite rear. So we're already extending the inside rear tire. If we're on the brakes then the rear will be very close to fully extended before we start cornering. Now add roll mostly from the front end dipping on one side and steering induced ride height change and it's looking closer to what is described. So how to fix. I'm thinking we need to go stiffer. As the rear tires are not up to the same temp as the fronts I'd go with more rear spring and if there's a lot of rake reduce that at the same time. If that doesn't fix it then more front bar or stiffer front springs. This will help reduce front roll, dive, and rear lift. Cary -
Nice run. What time you were hoping to get? Sorry to hear that PP is looking less likely to happen. It would be great to see it come together. Cary
-
Keep wearing out Koni struts ....
tube80z replied to heavy85's topic in Brakes, Wheels, Suspension and Chassis
It may be logger dependent too. I'm not completely sure what I was using corrected for roll, which would give higher numbers. Hopefully more data this next year to see how Hoosier and Avons compare. I created a math channel that looked at 1/4 seconds of cornering for continuous (autox) and then picked out the highest number for peak. On an EP car on GYs I would see similar numbers on a race technology DL1. But that was the best I ever saw and it could drop a lot depending on track conditions. For lateral acceleration (or longitudinal) are you thinking of comparison of cars or just as a gauge for your own car? Bob Knox recommends a 0.3 second moving average filter for acceleration data. Cary -
You can also bolt angle iron to the ST bar and run the rod end from it. Heavy85 has a nice piece he built here, http://i1150.photobucket.com/albums/o618/ls240z/Mobile%20Uploads/image_zps6017f710.jpg Cary
-
Keep wearing out Koni struts ....
tube80z replied to heavy85's topic in Brakes, Wheels, Suspension and Chassis
On slicks you should see 1.6 continuous and spikes near 1.8. Tires keep getting better and better. -
RX7 FC steering rack in S31z
tube80z replied to s30kid's topic in Brakes, Wheels, Suspension and Chassis
You need to reinforce the nut you used. A threaded bushing could have been used, which would have more weld area. And a rod end would give you much more room to raise the inner control arm if you need to. The large bearing you have looks like it would contact the top of the crossmember. Just a few things to think about. Cary -
MSD box has a tach out option. I think it's a 5 volt square wave.
-
Keep wearing out Koni struts ....
tube80z replied to heavy85's topic in Brakes, Wheels, Suspension and Chassis
My guess is the bushing that's used to guide the shock rod at the top. Those can wear and you get that rattling. If you go with the larger Bilstein size you can use a different piston (COBB) that has more tuning options. (Digressive, linear, etc.). Option 3 use the strut rod and a linear bearing as the bushing but done have any piston or oil in it. It will be a control arm so to speak. Them mount a coil over shock inside of the strut. This used to be done years ago in IMSA before you could get good struts. Then you can use much cheaper shocks compared to struts. Option 4 like Jon mentions is convert to a 2 piece strut and use 240SX struts. They have built some really nice pieces. Option 5 go to a-arms and no more struts. Obviously rules may play into this. I'm doing option 5 myself after reviewing the other alternatives. More fab but cheaper running costs when done. Cary -
Actually if you make two cuts to the centerline at angles it makes a cope. Lay a coped tube on a flat surface and you'll see. There are tables of what angles to use. The paper method is pretty cool too. Cary
-
Just underwear. That's all that's needed.
-
If you play with Kevlar you'll need carbide scissors. They will probably cut up the blanket. I really don't think you have anything to worry about. But your idea of bonding kevlar to the tunnel or the bellhousing should work. You can get a bellhousing that's rated to contain the flywheel clutch for your setup. It's very heavy. Cary
-
The QA-1s are called a slot bearing. They are a 2 piece design and not designed for the amount of vibration you'll see on the rear suspension. We used these first as they are low cost and they lasted one event and the liners pounded out. Then AM Auroras in 5/8 and they pounded out and then 3/4 X/Ms (not sure but their top lines) and they worked fine. I've done CMs on a street car and those seem to be working fine but it hasn't done a ton of mileage. It's your money but I don't think you need to spend $200 a rod end to get some that work. Hope this helps. Cary
-
Davies Craig EWP (electric water pump) on an LS2
tube80z replied to Zzeal's topic in Cooling Systems
I had one on an L6 mounted similar and never had a problem. They are really good pumps and the controller worked very well to warm the engine as well as cool. I'm thinking about adding one to my LS too. Cary -
Tube adapters can be had in any size for most thicknesses in the 0.065 to 0.120 range. I'd agree with John that 0.095 would be good here. Very successfully used on a 2600 pound car with 474 WHP and huge slicks at hillclimbs, track days, and many autocrosses. To use the tie rod end you have to build a mount that is thick enough to have the taper needed. Then the rod end is inserted into this. Take a look at BMW lower control arms inner joint to get an idea. In the case of the Z it would be a bracket bolted to the strut housing. Myself, I would opt for using rod ends. Aurora, NHBB, FAG as John mentions all make quality products. The Auroras that died were the top of their line and their engineering department was sent the rod end. All I got back as that the surface area of the ball must have have been two small for the load, which is ludicrous if you look at what's listed as acceptable loads in their catalogs. All I know is the larger size worked fine for a long time. It may seem like these are a waste of time to build but changing from polly bushings to rod ends and the extra floating link helped the car put power down better. And not just in rough areas. All I figure is that a lot of friction was reduced. It also made changing the strut out very easy. One thought on the arms I forgot to mention is that using left right in 5/8 or 3/4 threads changes the toe very quickly. It might be better to use the same handedness and 3/4 on one end and 5/8 on the other. This would allow for smaller increments of change per turn. Hope this helps, Cary
-
280z track car by Performance Motorsports Fabrication
tube80z replied to Rosco's topic in S30 Series - 240z, 260z, 280z
Flex plate is just for starter. The shiny metal bit on the flexplate is the new friction surface. They are sandwiched together with the clutch bolted to that.- 75 replies
-
- performancemotorsportsfabric
- track car
- (and 3 more)
-
I personally wouldn't use the tubing thicker than (0.95). My reasons are that I'd prefer the arm to bend rather than the frame to get bent. Same argument for CroMo tube. The 5/8 rod ends that wore out were Auroras. The liner was pounded out of the fixed end of the lower control arm. Stepping up to 3/4 ball/race cured that. For a street car it would be interesting to try and use ball joint style ends. One of the local hot rodders uses Ford tie-rod ends for all his axle linkages. He said they were cheaper than rod ends and last about 5X longer. Only downside if you need to change the mounts. Rod ends are much nicer in that regard and you don't lose any alignment when taking it apart. Hope that helps, Cary
-
'74 260Z front frame rails are TOAST...need sage advise...
tube80z replied to xringx's topic in Fabrication / Welding
If you do decide to rebuild I would look very hard to modern cars and how they have reinforced the tire well near the driver's feet. If your welding in tubing it wouldn't take a whole lot more to strengthen that area. It is one of those things you never want to find and when you have an attachment to a car it doesn't help. If you can overcome that and objectively look at what you have and different options you'll be money ahead in the long run. Good luck, Cary -
T3 plate or CrMo plate or stock TC rod modified. You should be able to get small samples if not there are online metal dealers. To fix the offset shear issue you can do double shear with a solid rod end. That was the planned next step if the single stick didn't cut it. But we never had a problem on a car that can break at 1.4gs so figured we were good.