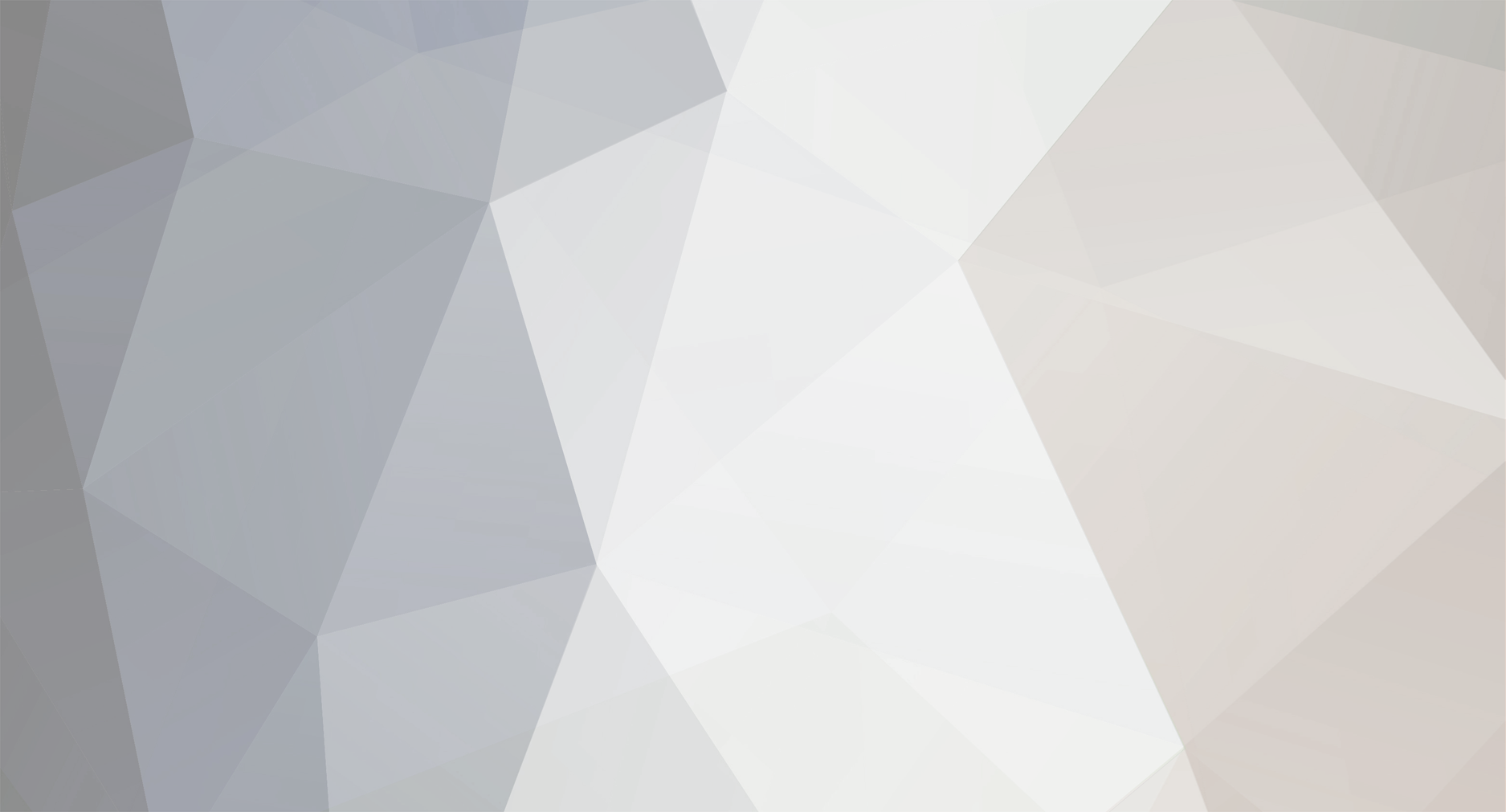
tube80z
Super Moderators-
Posts
1394 -
Joined
-
Last visited
-
Days Won
30
Content Type
Profiles
Forums
Blogs
Events
Gallery
Downloads
Store
Everything posted by tube80z
-
has anyone installed Rx7 brakes?
tube80z replied to andyhorror's topic in Brakes, Wheels, Suspension and Chassis
What I've found to work best is Neil Robert's recommendation. Find a constant corner and apply brakes medium hard. If it pushes you have too much front bias, if the rear steps out too much rear bias. If the cornering balance stays the same they you're set. Cary- 59 replies
-
I used cables and turnbuckles on my car. The top mounted with nothing more than a fender washer and a bolt. The connection was pretty much what Jon showed in his pictures. Nothing ever bent even with numerous off track excursions with wheels in the air. One nice side effect of running them is that you don't have to jack the car up as high to put wheels on. Version two for me was going to be a stop that was under the ARB arm. I saw a few older sports racers running something similar and owners said no issue running up against the limiter. The did say it was a ton easier to adjust these to keep abreast of ride height changes. Cary
-
And the Woodward spool valve has no damping built into it. So it allows for a lot of assist but you can still get good feel and treat it much more like manual steering. It's one of the few affordable solutions that lets you change t-bars in the spool valve to change the steering force curve. But to the original point I don't think there is a bolt-in solution that uses new parts anymore. All require some fab to use newer used or rebuilt parts.
-
My plan for chassis/subframe fabrication...
tube80z replied to capriottikidd's topic in Fabrication / Welding
Why are you using a 240Z? You're adding a frame that sounds more like it's built for a 3/4 ton truck. Why not go with the heavier 280 body and reinforce that. If you're using 2x2 why not thinner? I would think 0.65 would be more than enough and you can almost get two for the price of one weight wise. I'd personally have some sheet folded that mimicked the front rail to add in the back. Then up top do the same but tie into the seat mounts and tranny area boxing that in. Then complete an X rocker to rocker. Take a look at the maier reinforcement for the convertible 65 mustangs. The X will help with stiffness more than two parallel connectors. http://www.mustangdepot.com/OnLineCatalog/Suspension/images/PNMS2214B_App_650w.jpg Cary- 19 replies
-
- frame rail
- subframe
-
(and 2 more)
Tagged with:
-
Triangular front strut bar ideas
tube80z replied to Hypertek's topic in Brakes, Wheels, Suspension and Chassis
On my new race car I have implemented a triangulated double cross tube front structure. There's the normal cross bar at the front of the doors and another that would be at the base of the cowl, which I have made removable. This structure gives the tubes coming from the strut towers a place to feed load into. This ended up being a lot stiffer than just using a single cross bar on the cage and provides a solid spot for tubes coming from the strut tower. I'd think on a street car a similar idea could be used and would make the a-pillar stiffer in case of a side impact. When taking these pieces out of the car I was surprised at light it all was. -
Ken, Your wish is my command, at least for the merge. That last time, and it was a long time ago, I ran an autocross with the circle track to infield it felt like hitting a curb when going onto and off of the banking. I think you said that was the loaded side, which sounds like it's loaded up with a lot of lateral force and run across the junction it may be too much for the hub to hack. I don't know about your steel wheels but when I run my diamonds really hard I could see a wear pattern on the hub face. Do you see anything like that on yours? I'm thinking the easy solution is a 5-lug hub so there is more clamping against the wheel. If you have ARP or similar studs and upped the torque it might be harder on the hub with a flexible wheel. All conjecture but not sure how you really test this one out without a lot of fancy equipment and/or FEA on part models. Cary
-
Suspension upgrade for a RB26? S130
tube80z replied to Bandit50's topic in Brakes, Wheels, Suspension and Chassis
If you're willing to do some work you can source used motorsports bilsteins cheaply and those can be revalved. That gets you a good shock with many valving options. I have picked up various shocks in very good condition from 35 to 50 dollars. These are rod end shocks and to work you'll need to fab mounts. On the strut side there is a lot of info on this site of various options that can be done. If you can't fab or don't want to do the work then you're looking at a kit of some kind. It all boils down to how much you value your time. On the 280ZX platform the rear suspension squats very easy and the camber will go negative quickly. It gets worse if you lower the car. You'll need to raise the pickups if you lower the car to help with the squat and for a street car I'd look at a Z-bar in the rear that acts like a third spring against squat. If you do any tricks like running packers against the bumpstops you'll probably shock the tires too much on launch and lose traction. I've played with z-bars on 510s, which are very similar and was able to run a much softer rear spring but not have so much squat. For a street car I'd think this would be a good way to go. Hope this helps, Cary -
Old tires can be used to work on balancing your setup but when the grip goes the car still feels good but goes slower. If you run a data logger you should be able to compare your lateral acceleration from when it was working better. If you don't data log I would recommend adding that to the must have column of stuff. From what you're writing it's clear to me that you need to be stiffer. That will reduce rebound requirements and you'll need less bar and let you run with lower roll centers. As far as how to go faster that is all about first principles. That is what are the terms in the equations of motions and their various forms. That is mass, center of gravity height, and grip (force). One often overlooked area that pays big dividends we have talked about from time to time is friction. The more you can remove from the parts the move equals more grip. Hope that helps, Cary
-
From your picture and the following description it sounds like you want flexibility in being able to have a non-zero toe curve and the ability to tune it by using spacers on the toe-control link. The only downside I see is if you stick to something similar to the reverse a-arm design in your diagram you give up being able to also adjust anti-squat and lift. This assumes you keep the strut and don't add an upper a-arm. Is this going to be a strut or an a-arm? The other thing to check is if this design is not as stiff as using a reverse a-arm. To check that on the car you use some method of pulling the wheels together with the vertical position locked. Then repeat by pushing. Then switch to pulling/pushing the same side wheel pair. This is a poor mans K&C rig and you can see camber and toe changes from force at the contact patch. I think you could do something similar in a CAD package to at least see what the forces were in the members. If no difference that's great. If you end up putting a lot more load on a single member or joint then you might have problems. Happy to see a more technical thread in this section. Cary
-
My Dream LS7GTZ.......project underway
tube80z replied to cobramatt's topic in S30 Series - 240z, 260z, 280z
Looks really nice. Very, very jealous -
Square (all the same) or wider rear work fine. It's all in the setup if you're not matching the contact patch area to the weight distribution. Wider rear generally allows more throttle in a corner sooner and that gives a knock on effect down the next straight. It also depends a lot on the type of event you're doing. If the reaction stuff is a copy of the original IMSA items the rear was setup for 14 inch wide wheels. Cary
-
Lifting a front wheel isn't caused by the ARB. It's from being too soft in the rear or too soft all round. Personally I would look at a C6 vette for the ABS computer and tone rings. They are a generation newer than all the 240SX stuff. Teves sells a motorsport unit but it's going to run 5K or so. Bosch also has a motorsport ABS but it's probably closer to 20K installed. Cary
-
How i've always removed spindle pins
tube80z replied to motomanmike's topic in Brakes, Wheels, Suspension and Chassis
I like the air hammer for stub axles. For spindle pins a puller has worked better for me and I don't have to destroy the pin. -
Lower the rear. Your RC is too high if I understand the control arm angle. You want to lower the end that needs traction unless you're hitting the ground and upsetting the cornering balance. For the really bad bumps add packers and tune the bumpstops. If you have a lot of lock on try and winding the wheel sooner or less caster to reduce cross weight change. For a fun afternoon put the car on scales, if you have them, and raise and lower each end and turn the wheels and watch the weights change. Change caster and see the difference. On our cars we often use a lot of caster to help low speed turn in. This can cause catch and release on corner exit as you unwind the wheel. Spacers to change the track that add more scrub will make this worse. Maybe a cool winter project would be a simple subframe in the rear and new arms that allow you to raise and lower the pickup points. I have some pics if you're interested. Cary
-
I may not be following all this but if you don't have enough rear droop travel you don't want to soften the rear. You need to stiffen it up. If you lower the spring rate in the rear you'll get more suspension travel used up from weight transfer. A lot of the hillclimbers in the NW used to soften the rear of the car so they would put down the power better. I have convinced a number of them to use much stiffer rates and it works. When you start using aero you also need to run stiffer and change your driving style to accomodate. To keep the splitter down and working harder to match the rear wing you can trail brake to the middle of the corner. Then onto the gas but you need a stiff rear end to keep the car from squatting too much and upsetting the extra grip you are getting from aero. If you watch classes with wings and splitters you'll see often see this. I think you'll find that the diff will be kept loaded this way too. Cary
-
Thanks, learn something new everyday. I dug out my old nissan comp catalogs and didn't see it listed. But clearly they are now available.
-
I'm pretty sure you can't get a 4:44 in a R160. I seem to recall only the 4:38 was available that was close. Or 4:62. I had a 4:44 but it was in an R190.
-
Thanks Gary, that's awesome. Now saving pennies
-
Not sure if it would help but there's also Evan's coolant. That might help if you need a higher delta in temp across the radiator. Cary
-
2015 Dodge Challenger Hellcat. Dodge has set the standard
tube80z replied to BMAC's topic in Non Tech Board
I heard 4500 is the new 2500 -
Thanks Gary. One more question. What happens if you release the wheel in a corner? Does it straighten out like manual steering or does it slowly move back like damped hydraulic steering? Cary
-
You really want a mount over the top as the diff tries to move up under acceleration. You could still do something similar but it would be better if one piece that connected to those tubes by dropping down. It probably could be fairly simple with poly bushes around the tube. You need to be careful that you don't make one end or the other solid when mounting the diff. Cary