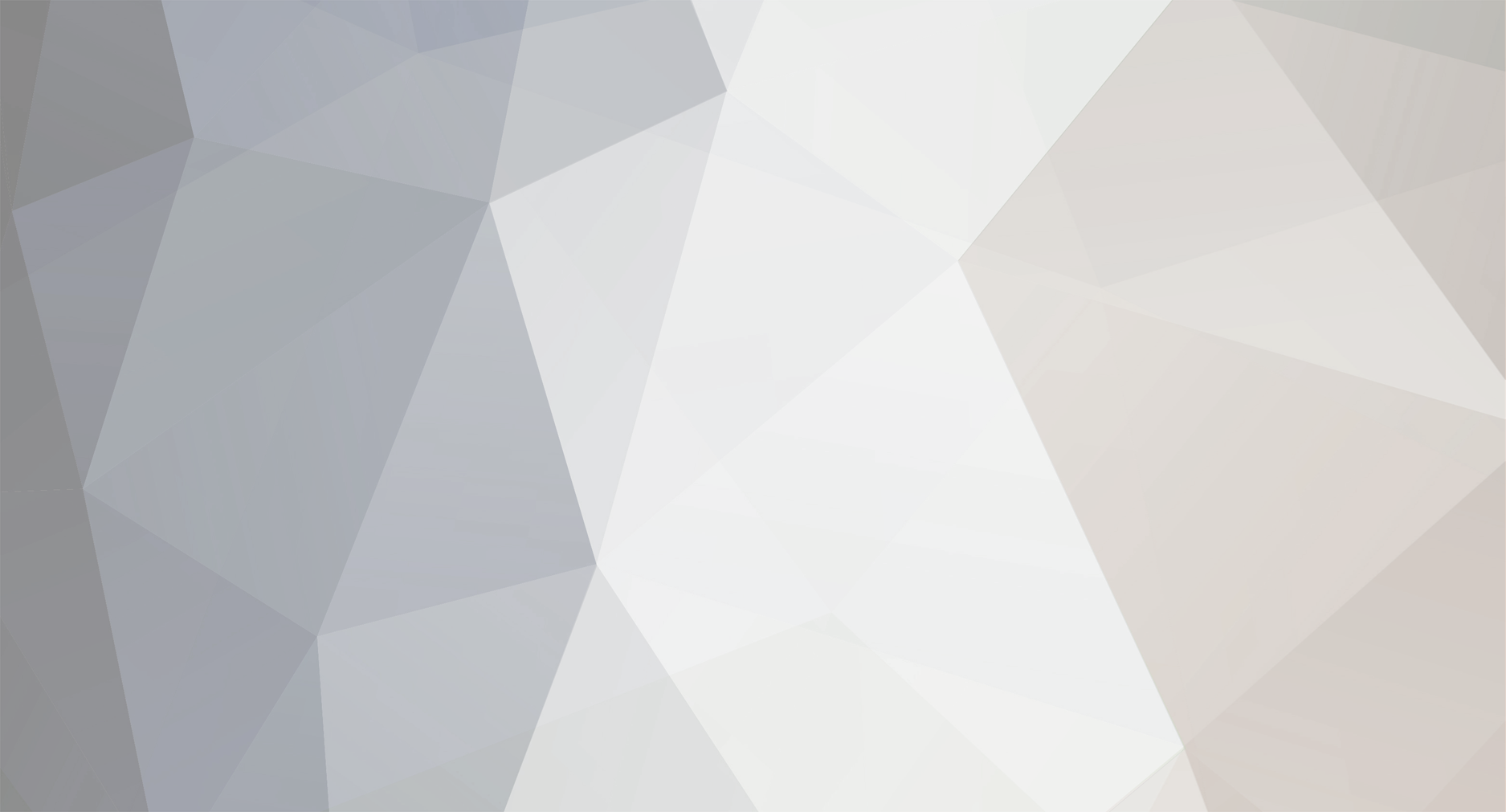
tube80z
Super Moderators-
Posts
1387 -
Joined
-
Last visited
-
Days Won
25
Content Type
Profiles
Forums
Blogs
Events
Gallery
Downloads
Store
Everything posted by tube80z
-
Not that I have any real experience, but with IRS you could do a number of things you can't with a live axle. Assymetric camber, toe, etc. And you could experiment with packers to adjust when the bump stops are engaged as well as ride height to try and even the weight distribution at the rear. In some ways you're wanting just the opposite of what road racers do. If your car has an automatic have someone power brake it while you watch the rear wheels. You may get quite and education from this and decide that toe can help to fix this (or look at heims or much stiffer bushings). Cary
-
I have his video and brought it up when I took the Motec seminar with Claude Rouelle. He spends a lot of time discussing suspension kinematics. What I got out of that class was the classical approach to thinking about RCs in general isn't really very good and we don't really have decent tools to work with them. What I mean by that is most software doesn't really roll the car realistically and how the points move (RC, IC, etc.) isn't real and tire and component deflections can cause large changes. You can analyze geometry and some decent cars show a lot of RC movement, which many books tell you is bad. But when you use the force based approach you will find that this isn't the case. Claude went on to say that movement isn't so bad as velocity. That's one item that really needs to be watched. I don't know if you get racetech magazine or not but they had a really good three part article on force based RCs from Andy Thorby. Like anything the more you know the more complex it gets but his explanations were very good and he provided a few tools to help. In the motec seminar Claude goes over pitch centers and how they work, which is exactly what you're seeing here. If you get a chance his class is really a good one to take and will shine a bright light down the mineshaft. Cary
-
Now if you're gonna tell stories let's get them straight. I cam up to drive as Mike was using my R200 diff from my race car. It just so happens you can't share a car in Woodburn, or maybe any drag strip since that was the and only time I've ever been on a drag strip. And Michael didn't break a halfshaft, he dropped my R200 onto the ground when the rear diff strap pulled apart. I remember everyone giving me crap the Michael broke my diff Then we got to push the car out into the parking lot, remove the numbers, and call tripple A. Then the tow truck driver managed to ding the car up on the way home, and Michael was less than amused. I think Paul's car was about the fastest car there other than a couple of real drag cars (supercharged rotary truck, something else, and a fool on a snowmobile). Yep, small world. There are also a number of stories related to the Medford track, Kelvin's garage, and a number of areas in between but those have been sworn to secrecy. Cary
-
Independent vs. Live Axle rear suspension
tube80z replied to RacerX's topic in Brakes, Wheels, Suspension and Chassis
In Medford an ex-Griggs Mustang took TTOD when the Datsun guys didn't show up this year. Other than that I've seem a demon fast Toyota Starlet, a killer B210 (actually was a GT-5 car), another that had an L20B, and a few older RX-7s that all at one time or another took TTOD. So it can be done but it's not something typically seen. I think you'll see more fast live axle cars at higher speed events. Autox generally seems to favor smaller cars and the deck is stacked. Oh, I did forget some FWD cars that have live rear axles. Do those count? Cary -
Independent vs. Live Axle rear suspension
tube80z replied to RacerX's topic in Brakes, Wheels, Suspension and Chassis
I'd be careful on that one. What you'll find is that you can quickly screw things up with antisquat and too much will make a car that puts power down well when going straight but oversteers when you press the throttle in a corner. The same is true of antidive and too much of that will make a car have terminal understeer. The big one that you missed for an advantage is the a live axle is simple to setup. There are many pitfalls to be avoided with IRS and a poorly setup IRS will generally not functional as well. Cary -
Not to get too far off topic here, but I believe the current theory is his tires lost heat behind a safety car and more importantly ride height. When he came to the next high speed corner the car bottomed and he lost control. I think the answer to why carbon wheels are not allowed in F1 has to do with rules. Last time I checked metal was required. I wouldn't use these on a street car of mine. Maybe a racer but I'd agree with the concern over bumps/potholes shattering them. Cary
-
rear poly bushings on outboard end of CA
tube80z replied to blueovalz's topic in Brakes, Wheels, Suspension and Chassis
These are generally thick enough for that not to be too big an issue. And on my balance bar sleave I used a hone to fix it. In the past I've used some pieces of aluminum round stock I have to control the warping. I don't know if any of this helps or not. Cary -
rear poly bushings on outboard end of CA
tube80z replied to blueovalz's topic in Brakes, Wheels, Suspension and Chassis
Why would you turn it? Why not alter the front crossmember the bolt-on rear pieces to deal with the larger diameter? I think I'd be inclined to weld the collar to them anyway. That would seem a lot cheaper when you don't have access to a lathe. Good find BTW, I knew I saw them but I wasn't having luck without their catalog. My next trick would be to find these in my shop ... Cary -
rear poly bushings on outboard end of CA
tube80z replied to blueovalz's topic in Brakes, Wheels, Suspension and Chassis
What I'm trying to find on their stupid site is a adapter for building your own lower control arm. It uses a spherical bearing with snap rings to hold it in. You weld these onto a tube and then you can make your own LCA. I even have a few of them but I can't seem to find them to measure them up. Argh, I'll keep looking. Cary -
rear poly bushings on outboard end of CA
tube80z replied to blueovalz's topic in Brakes, Wheels, Suspension and Chassis
No, I was thinking it might be possible to use a spherical bearing holder in place of the stock rubber busing. And the stock arm would fit into this. I don't know if the sizes would work or not. Just a rough idea of a possible way this would work with little to no machining. Cary -
rear poly bushings on outboard end of CA
tube80z replied to blueovalz's topic in Brakes, Wheels, Suspension and Chassis
I don't know the OD of the pieces but I've seen a machined sleave from stock car products that you might be able to use. If it really is one inch then you might not need any machining. Cary -
Cross Member Bump Steer Mod
tube80z replied to Twoeightnine's topic in Brakes, Wheels, Suspension and Chassis
Sure, attached is a diagram. I won't have a real pic until mine comes back. Credit has to go to Brabham. The design comes from the manual for the BT-18. The other cool thing I need to build is flag alignment system. Cary -
Cross Member Bump Steer Mod
tube80z replied to Twoeightnine's topic in Brakes, Wheels, Suspension and Chassis
Jon, that's a really slow way to measure bumpsteer. It's much better to use a simple system of a heavy weight at the bottom, two cheap heims, and a simple fabricated H. The bottom legs of the H are hooked to the weight. You put a toe plate on the wheel and move it up and down the amount needed (I used spacers under the wheel to make this go quicker. No dial indicators are used, you simply eyeball the gap front and back. Make a change and repeat. If you're really anal and want to meausre it you can use feeler guages. Not only is this cheap but you can do a corner in about a quarter of the time. Cary -
No, the issue isn't the pin (bolt), it's really what's the best way to resist bending at this point. Few people will ever see this as an issue unless they use the car rally hard on a track. A better way to resist bending is to use a solid rod end and a wider spacing for the mount. Just adding a lower dog leg to the standard clevice will generally keep the bending from happenning. You don't want to put a heim in this location as it will allow an addition degree of freedom. Once you overcome the forces putting tension on these parts from car weight you will get a wheelbase/caster change. In practice this is seen as severe wheel hop under braking. Double lower balljoints can be done but you have be careful how things align. Cary
-
Front Suspension Swap question
tube80z replied to Careless's topic in Brakes, Wheels, Suspension and Chassis
I went and looked at the pics. One thing you need to be aware of doing this conversion is that you're steering geometry is going to have issues. Look at the angle when the steering arm is in rear steer mode and then look at the angle it is on front steer mode. It looks to me like you now have an anti-ackerman mod. Are you doing this to get a two piece strut or better brake options? From a geometry standpoint I don't see this as an upgrade over the Z strut, unless I'm missing something. I'm very curious though. Cary -
It would be better for anyone making these to stop using a clevice. It's far easier to bend where the clevice is than if you use a solid rod end and a double shear mount. My old race car used arms like these and I could bend the dog legs from time to time (braking and jumping FIA curbing). A double shear mount with the clevice stopped this but then I have an extra piece that's a waste. I'd be careful to think about using flat steel for the LCA. With sway bar loads you've introduced an undamped spring. Is it an issue? I don't know. Cary
-
Q about control arm design (non Z related)
tube80z replied to J__'s topic in Brakes, Wheels, Suspension and Chassis
There's a lot of good advice above. It's really hard to give any specifics for an open ended question, with little info on how the car will be used. A few things to think about. Most of the software out there doesn't calculate the RC correctly. When you enter numbers for roll it simply moves the car on the centerline and calculates how the RC moves. There's a good reason for this but it can lead to misleading results. RCs move in three dimensions and most of the software doesn't take that into account. And none of the packages that I've seen (cheap ones anyway) allow for compliance in the bushings or the linkage. If you do come up with a design it might be interesting to see what happens on the computer if you move things around an eigth of an inch or so. Sometimes the results are interesting and will lead you to make parts much stiffer in some dimensions. The best advice I could give is don't get to wrapped around a particular RC height or trying to control its movement too precisely. As stated above try and determine what the tires need from a camber point of view and use that to let things fall where they may. It may make more sense to look at changes to the slope of the curves that are generated. In my very limited experience keeping this more or less constant has made my car a little easier to drive. In general a above ground RCs will have car that reacts quicker and heats the tires more from the lateral scrub. You will have a net lift when you corner with a suspension like this. An underground RC will make a car react slower, which sometimes can be good, put less heat into the tires, and will lower the ride height as it corners. I'd try and keep my RC in an envelope that doesn't move more than 20% of the track width, doesn't cross the ground or a wheel during any high force manuvers. Some argue this is BS but again in my limited experience this has helped some stabilit problems I had. It would be best to create a design that allows you to at least change RC height as this is a key tuning tool. Hope that helps, Cary -
rear poly bushings on outboard end of CA
tube80z replied to blueovalz's topic in Brakes, Wheels, Suspension and Chassis
Unibits are great for this kind of thing, even the cheap HF versions. Although Costcos cut much better. Cary -
any pic of "slotting the strut tower"
tube80z replied to Rebird's topic in Brakes, Wheels, Suspension and Chassis
We autoxed for years that way with no issue using the isolator on top. I even drove my 510 that way for 5 years. Cary -
rear poly bushings on outboard end of CA
tube80z replied to blueovalz's topic in Brakes, Wheels, Suspension and Chassis
Yes, if the ball pops out you may lose containment. Most sanctioning bodies require safety washers for single shear mounting. I figure it's cheap insurance you hope to never need. Cary -
rear poly bushings on outboard end of CA
tube80z replied to blueovalz's topic in Brakes, Wheels, Suspension and Chassis
The only thing I could think of might be to use spacers to change the side to side track width either to tune balance, square the car up, or get the strut tube fore/aft angle equal. I guess it depends on how precise you want to be on setup. I would recommend a safety washer on the outside of the heims. Cary -
PICS: Custom rollcage fabrication/install
tube80z replied to mull's topic in Brakes, Wheels, Suspension and Chassis
Looks very similar to what I did on my tube car. I have a book from Japan that is a history of racing Zs. I'm pretty sure I have some of these pictures. I can't read any of it but it's fun to look at what they've done. Cary -
Typically rebound forces are higher than compression forces on the shock shaft. Welding a gap is a really great way to make a weak joint. If you have a gap use tubing on the outside to bridge and weld this up. That's the correct way to do this. Cary