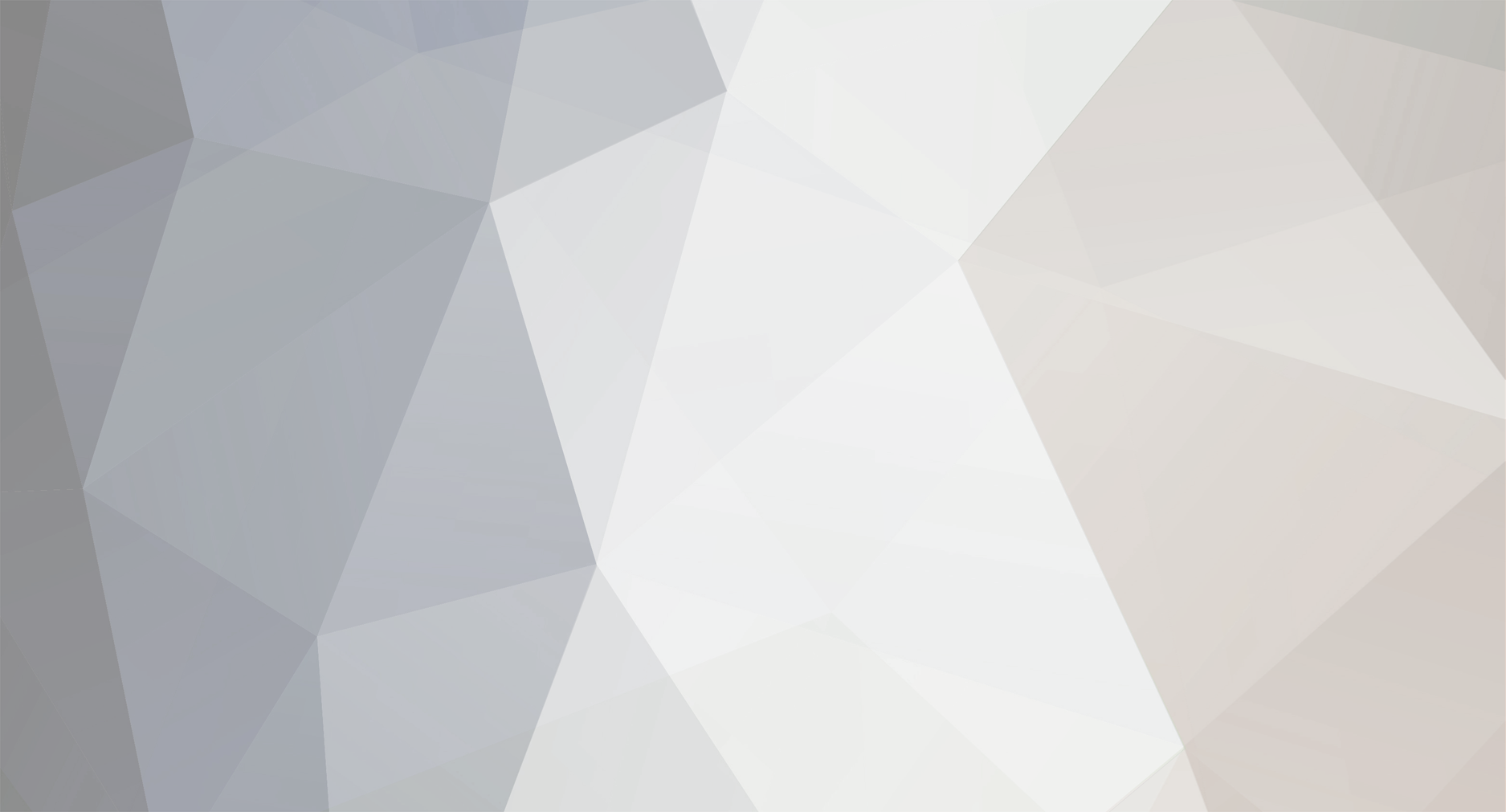
NewZed
Members-
Posts
6681 -
Joined
-
Last visited
-
Days Won
70
Content Type
Profiles
Forums
Blogs
Events
Gallery
Downloads
Store
Everything posted by NewZed
-
You're starting a shop just to focus on pre-83 L6 Datsuns? What is your area of expertise - composite molding, tooling, engine building...? Just curious. Examples of previous or current work would be interesting.
-
Don't know why your idle would drop from1200 to 500, with a click. But, people get the AC compressor power wire and the BCDD power wire mixed up quite often. They look similar. Try turning your AC on and see if the BCDD clicks. And 37 psi is too high for idle. Sounds like you don't have manifold vacuum to the FPR.
-
In your case, the 81 troubleshooting chart is only good for ideas about how things work and some cause and effect clues. 81 had a separate Turbo Supplement that describes the three plug ECCS. The main 1981 FSM is for the 35 pin style ECU. The concepts are the same though. Sensors provide information that the ECU or ECCS computers use to determine fuel enrichment. Pretty sure that after the whole ECCS analyzer section in the EF&EC chapter there is some basic multimeter testing that you can do. You just have to work through the whole chapter. Take notes on where the good stuff is.
-
I opened up the 81 FSM, but it looks like Nissan changed things in 1982, to focus on the ECCS analyzer. Probably worthwhile to look at the 81 just to get some ideas. Nissan tried to make things easier but just made them more complicated instead.
-
Good luck. There's a third of a page dedicated to "Poor gas mileage". EF&EC 18.
-
You're probably seeing something else. Sounds like you just have a plain old externally regulated alternator, on an old 1975 280Z, with a bunch of old corroded connections drawing enough current at idle to put your headlights on battery power. Revving the engine provides enough current to charge the battery and run the headlights. A PO decided to replace one of the fusible links with a fuse in the past. Not uncommon. I plugged your part number in to Google and it comes up as an externally regulated alternator. You can move on to cleaning electrcial connections and fixing other worn-out stuff.
-
The engine wouldn't even run in the last post in your link, now you're driving it. Open the ZX FSM that fits the year of your engine and go through the troubleshooting in the EF&EC chapter. Check the CHTS circuit first.
-
I'm going to guess that your dad has big feet. Check where they've been.
-
Many of the mid-90's Nissans, like the Pathfinder, used a 3 wire power tranistor that looks like it would work. Ground, ECU Pin1 and coil primary circuit. Same basic design as the ZX turbo systems. The wrecking yards are full of them, or about $60 to 120 at RockAuto.com Attached a drawing from the 95 Pathfinder FSM, Page EF & EC 235.
-
Seems like there are three topics in play, and all blended together. Contoured counter weights for improved oil windage purposes (knife-edging), lightweight crankshafts (a side-effect of kinfe-edging), and harmonic dampers (got thrown in from the side from Porsche and VW land, although it should be considered when crank shaft weight modifcation is done, re the BJH white paper [which is well worth reading]). The original question was a little bit vague, and referred to the effects of losing crankshaft inertia (motorcycle-like response) unless he was implying that oil film drag was slowing the engine's ability to rev quickly. Seems like the purpose of knife-edging has been mis-defined a little bit and thrown the thread off-topic. From my limited understanding of all of these things.
-
Umm... I get 86mm = 3.385". Maybe your 3.25 is a typo for 3.35? Your gaps match 3.35". The factory range is in the back of the 81 FSM. Looks like your top ring is good and the second ring too loose. Are all of the second rings the same? You have six of each right? 76 (N42 block) and 81 (F54 block) are both L28's with the same bore and stroke. Pistons are different. The last few pages of the Engie Mechanical chapter has all of the spec. with ranges tabulated. Good luck. Looks like fun even witth the problems.
-
I checked my "How to Modify..." book by Honsowetz and he says .017" (.43mm) top, and .014" (.36mm) second. But Monroe and Honsowetz worked together, I believe. It was written in a different style though so it doesn't look like a cut and paste. I'm just repeating what I read. The 1976 specs. at the end of the Engine Mechanical chapter says: Ring gap Top .23 to .38mm Second .15 to .30 Oil .15 to .30 Honsowetz and Monroe recommend looser than factory spec. You have a dilemma. Edit - I see that the 1981 spec. is a little bit different, but not much. What is the diameter of the bore (after honing)? Weird though, that someone would ship rings with different gaps. Maybe they're reboxed returns. Aggravating to get bad parts that you can't evn modify to work.
-
Monroe's "How to Rebuild..." book says top ring should be "OK" at .3 - .43mm for an 88.9mm bore, recommends a target of .36 mm.. Second rings should be .05mm less since they run cooler. Page 121. BUT - then he says to follow the ring manufacturer's recommendations. So if you have a brand name (ITM) maybe you can find a spec. for mm gap / mm bore.
-
The quality of the clutch kit will depend on how well they copied someone else's design. XTD is Aimco, which looks like a typical off-shore copycat company. Here's an interesting couple of links. It doesn't look like they manufacture anything in the states. The contact e-mail address is a yahoo.com address. Just shining some light for those who want to know where these great deals come from. http://www.xtdclutch.com/cms.php?id_cms=4 http://www.ripoffreport.com/r/aimco-clutch-company-ebay-id-aimcoclutch/los-angeles-california-60007/aimco-clutch-company-ebay-id-aimcoclutch-jim-kun-song-xtd-racing-clutches-sells-automot-378941 EBay is a crap-shoot. Hope for sevens...
-
Forgot to say that once the engine warms up the temp. switch is out of play. So if keeping the engine running when it's warmed up is the problem, that won't fx it. All the switch does is cause your timing to advance about six degrees when the engine is cold. If you add some detail to "stay running" someone might have some ideas.
-
People have made the switch linked to below work. I don't think that the original is available anymore. http://www.thezstore.com/page/TZS/PROD/11-3122 But all it does is activate the second pickup coil in the distributor when the engine is cold to advance the timing. Either for emissions or just a more convenient idle, its purpose is not clear. Described in the Engine Electrical chapter, Ignition Circuit section, of the FSM. If it's not there, you just don't get the cold temp. timing advance. www.xenons30.com/reference You'll barely notice a change if you fix it (the idle will be higher for longer when cold), but if you do, an alternative fix is to run a very small metal screw in to the wire stub in the center of the broken one. Put a tiny ring on the end of your wire with the bullet connector.
-
Thanks for the link. That should help the OP out if he reads through it. The semantics problem is general to dampers around the auto world, I think, as you noted in in the link, since it's often referred to as a "balancer". The idea of "damping" energy is uncommon and misunderstood, and harmonics hard to understand, so we end up with dampners and moistening devices. Not claiming to feel super comfortable talking about harmonics myelf, to be clear. As far as harmonics and the L6, I wonder if the Porsches and VW's the OP refers to are 4 cylinder engines. Different harmonics maybe?
-
The balance and harmonics concepts might be getting interchanged here. Seems like everyone in this thread supports having a damper. Where's the link to the thread about dampers where it's said you don't need one? Only TEP and you seem to be saying that.
-
Found on Google. For discussion, don't know anything about its performance. http://www.ebay.com/itm/Z-Car-Lightweight-Single-Groove-Aluminum-Crank-Pulley-/310246632272 and http://www.racetep.com/nissan.html I thought the damper was for harmonics damping, not balancing. (Edit - semantics, maybe..) Edit #2 - I can't find a sign on the interweb that anyone has ever actually bought and used one of TEP's damperless pulleys.
-
You forgot to sign it. Where can we get prints?
-
bled the system 5 times.
NewZed replied to RangerWill's topic in Brakes, Wheels, Suspension and Chassis
You bled your brakes and "now" the pedal goes to the floor because you have a rotor that was turned off-perpendicular? If your brakes worked before, and you didn't just have your rotors turned then you probably don't have the exact same problem. The black in the brake fluid is probably worn out seal material. When you bled the brakes you probably pushed the MC piston down in to a rusty zone and finished off the seal. Try blocking the ports at the MC like RangerWill did and see if you can build pressure. If not, the MC needs work. -
Too wordy. Try to simplify.
-
Syncro difference btw closer ratio and wider ratio FS5W71B
NewZed replied to tamo3's topic in Drivetrain
I actually thought it would be more than 5/16", between 1 and 2 inches (recalled from one of Xnke's previous threads, I think). And I think that measuring to the end of the output shaft might be more important, although the dust shield matters too. Have you compared bellhousings (front cases)? I'm not familiar with the CA20 engine (Leon's link), it may not have the same tilt/angle and bolt pattern as the L engine. You might be in to a bellhousing swap, with machining and/or bearing swaps required. Whatever it is you're working with doesn't seem to be a common transmission used for the Z's. -
There are actually two - one written in 1975 and one in 1980. The other one is at the S130 xenon site. Called Fuel Injection Guide or Book. Non-denominational. Best to use the FSM and the guides together. The guides have better drawings and diagrams, but the FSM is more model specific, for relays, part locations, etc.
-
It's called the "transverse link" in the FSM, instead of LCA.