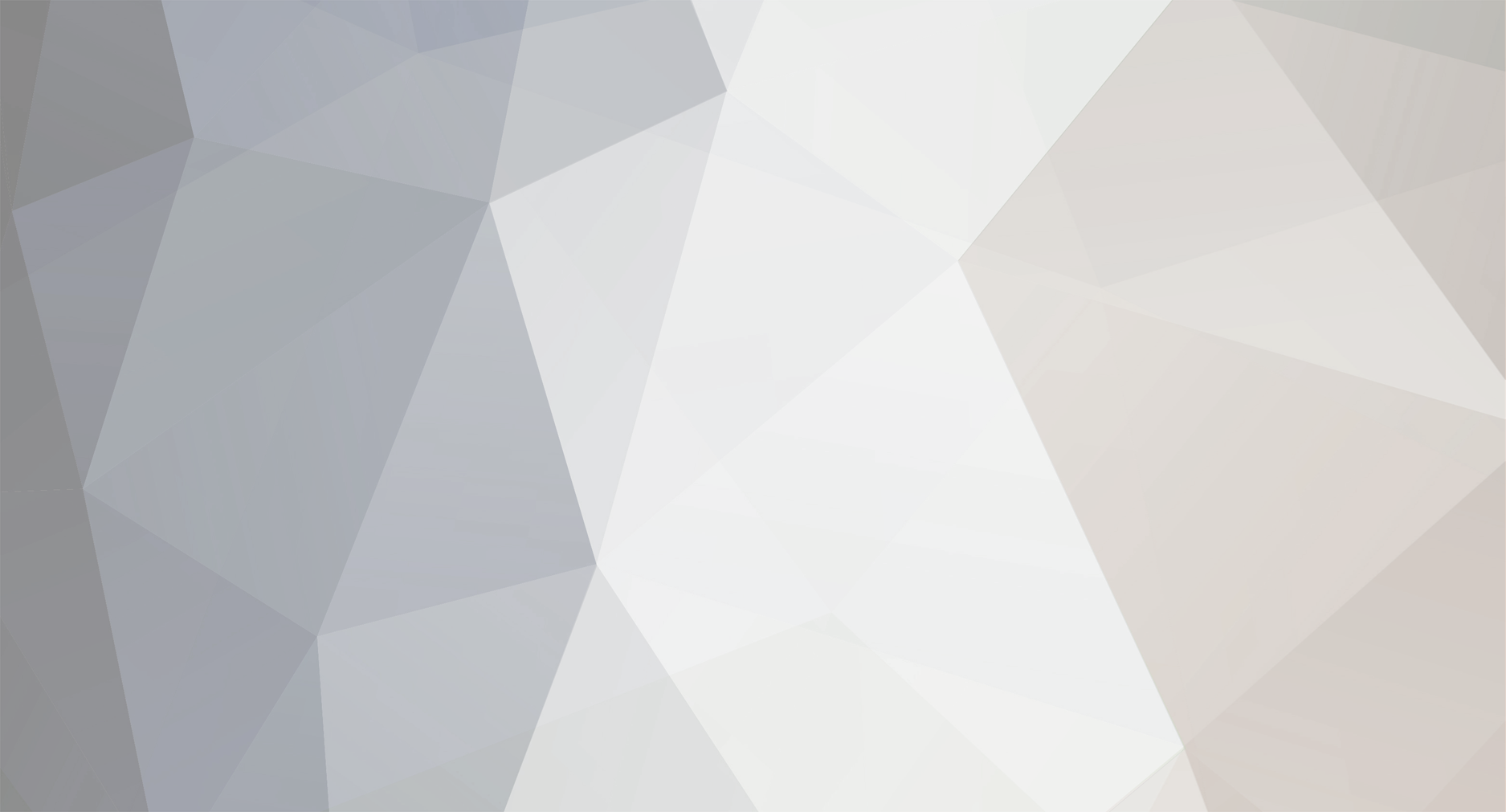
NewZed
Members-
Posts
6680 -
Joined
-
Last visited
-
Days Won
70
Content Type
Profiles
Forums
Blogs
Events
Gallery
Downloads
Store
Everything posted by NewZed
-
This comes up all the time and I just realized that I have the pieces in the garage to take the critical measurement. Assuming that the slave cylinder is the same distance from the back of the block and the flywheel thicknesses are the same, and the clutch forks are the same, then the distance from the bottom of the pressure plate to the surface that fork sits on is the distance that needs to be within a certain range. The pressure plate and the collar are the two things that vary over all of the combinations. So here's a few pictures of a pressure plate with a long collar, a combination that I used to have on my car. The pressure plate is the one I used, the collar is not, bit it's identical to the one that was used with that PP. The distance is 90 mm, or 3.5 inches, from the surface of the flywheel to the surface the clutch fork rides on. If I was starting from scratch with unknown parts, that's the distance I would shoot for. Edit - the caliper measurement looks off in the picture due to camera angle.
-
Thanks. Interesting. That's a tight fit.
-
The "How to Modify" book says to never get less than .050" clearance between piston and head, .055" in a race engine. .030" is asking for problems isn't it?
-
Here's a link that shows the hole with the adjustment screw. The screw is kind of deep inside, with a big slot, hard to reach depending on the orientation of the AFM. Often they're factory sealed with hard clear plastic that you'll need to break loose, sometimes just a rubber plug. Keep track of how many turns you use in case you want to go back. Don't get carried away with all of the other advice in the link if you're just trying to lean out your idle. The first color picture - idle "flow" adjuster. Out is leaner, it lets more air past the AFM vane. http://atlanticz.ca/zclub/techtips/afm/index.html Edit - it's possible that the turbo AFM doesn't have this, I haven't actually worked with a turbo AFM.
-
The hold at 2,500 is just a second chance to pass if you fail initially. They don't measure. So the AFM idle air screw leaning should get you there, assuming you don't have any missing from bad plugs, wires, etc. I'm surprised they tested without the converter, unless they were just giving you some numbers to work with. The door jam tag tells if your supposed to have one and I don't think that they'll pass you without it.
-
Turn the AFM idle air screw out as far as you can before getting a lean miss, then turn it back in a half turn. I don't know what tests they run for an 82 but they only test idle for 1976.
-
Possible vapor lock issue? (Carb'd 240z)
NewZed replied to BrandenZ's topic in S30 Series - 240z, 260z, 280z
Isn't this why Nissan added the electric pump? -
Call Jok and ask him if tuned it to pass DEQ.
-
I get it, I've done the same thing. Gear oil smells better than used motor oil. Uuhhmm... Another spot that might leak due to seeing a high oil level would be the front cover bolt holes. The holes are tapped through to the inside of the cover and can pass fluid along the threads. The top ones, that might only see a splash or two due to braking and turning over time, might be seeing a steady oil supply now. The FSM recommends sealing the threads upon assembly but I'll bet that a lot of people don't. The right oil level might get you back to normal, but it might take a little while for everything to drain out. Another spot, but which would probably leak all of the time (one of mine did), is the clutch pivot ball bolt. It's also tapped through the cover.
-
I'm not familiar with the Solex carburetor at all but most carbs have a throttle plate to control air flow. Your description shows that you are basically using the choke plate to control air flow. It sounds like your throttle plate(s) is(are) stuck or adjusted too far open. Timing at "full retard" doesn't mean much either. Meaning no vacuum advance or distributor twisted as far back as possible? To control idle speed? That's not the right way to do it. An actual static timing number is what you need. Just an observation of carb and engine basics from an EFI guy...
-
Pretty sure that the "proper level" is up to the bottom of the fill hole with the car level. You could just remove the fill plug, level the car, let the excess drain out, and put the plug back in. Then see if it still leaks. How do you know where the fluid is coming from if the transmission is mounted to the engine? How can you see the hole that you described?
-
Wet plugs would mean "flooded", but the reason why isn't clear. Dry the plugs, crank the motor a few turns with the plugs out while you check for spark (watch out for gas and fumes in the area of the spark), check your inlet and outlet lines to the rail to make sure you're not over-pressurizing. The hose connected directly to the top of filter goes directly to the fuel rail, not the regulator. If you have spark and everything looks right, it should go.
-
Did you reverse the inlet and outlet hoses to the rail? That will give full pump pressure to the rail, the regulator won't regulate. Could be 90 psi if you have an after market pump. Are the plugs wet? Or you just knocked a wire loose. Check for spark?
-
Here is a great thread to read to get the basics down of how the L-Jet fuel injection system works and how it's affected by common modifications. Worth reading before you spend too much money or get too carried away, and for any future problems you might run in to. It should give you some ideas and help you avoid the more common mistakes. Good luck with the new car. http://forums.hybridz.org/index.php/topic/95316-braaps-l6-efi-induction-advice-and-tips/
-
These are pretty common (both). Fuel pressure should never get down to 15 psi. Apparently, there is a screen or wire sock around the outlet tube from the tank. Many stories on the forums about flakes of rust or "stuff" floating on to the mesh and clogging it, then floating free after the engine dies. The fuel tank has a drain plug. You might consider disconnecting the hose to the fuel filter, running it in to a gas can or three, and hot wiring your pump (disconnect the starter and hold the key or run a jumper directly the the pump) while you monitor fuel pressure as the pump drains the tank. Then shake the car around to stir up the residue and remove the drain plug. You'll get a look at what happens to fuel pressure over many gallons of fuel, and you'll see what's sloshing around in the tank at the end.
-
If there are three wires then you probably have one with dual pickups. You only need one pickup (two wires)for the GM HEI module. It's probably a rebuild, that's why the wires are blue. Take a look right at the pickup coil in the distributor and you'll probably see a green and a red spliced in to the blue wires. The GM HEI module used with a variable reluctor distributor isn't really written up well anywhere that I've seen. In short, on the HEI module, B connects to switched battery voltage (coil positive is a convenient source), C to coil negative, G to the green wire from the distributor pickup coil, and W to the red wire from the pickup coil. Make sure that the module mounting points (holes) are electrically grounded, since that is part of the module's control circuitry. Edit - here's a popular link specific to the 240Z - http://www.sonic.net/~kyle/ztech.html
-
Did you take the rubber boot off to see if it's leaking? The boot can fill up with fluid without external leaks. I've opened a new slave cylinder and found honing grit inside. Best to open it up and flush it out before installing.
-
There's a couple of 77 280Zs in the PicknPulls in your area. Might be worth a look.
-
Backwards I was. So, there are advantages to avoiding the shims. Your 2.3 camshaft degree estimate (4.6 crank degrees) suggests that the #2 hole would give 0.6 crank degrees retarded with the .080" missing. Seems within the bounds of the range suggested by the FSM's before and after pictures. Also, since the notch is relative to the cam, you could pre-assemble and check the notch position per the FSM procedure to see if it's right.
-
According to the FSM, the four degrees described per cam shaft sprocket adjustment hole, is in crankshaft degrees. #2 is four degrees, #3 is eight. The sprocket has 40 teeth, so 1/40 is .025 or 2.5% of one camshaft rotation, 5% of one crankshaft rotation since the crank moves at double camshaft speed. .05 times 360 = 18 degrees. Or 1/40*720. So you can have 4 or 8 degrees of advance with the stock chain/camshaft configuration or retard the timing one tooth and use the adjustment holes to move forward to get 18-8 (the #3 hole) for 10 degrees advance, or 18-4 (the 2 hole) for 12 degrees. 4, 8, 10, 12. Weird how that worked out so evenly. Sticking with the stock chain and sprocket configuration and using the #2 hole seems like the most likely option, if you can avoid the chain slack issue, and are on a budget. BUT, isn't rocker arm angle and wear patterns the other problem with the milled head? The other, maybe the main, reason for the shims?
-
One tooth divided by the total number of teeth times 720? Just a quick guess...
-
Isn't that a typical lug nut size?
-
240z alternator and battery wiring
NewZed replied to infiltrate2000's topic in S30 Series - 240z, 260z, 280z
These links might help you. If you're having a problem, describe it with details of smoke and sparks, and you'll get some good replies. http://atlanticz.ca/zclub/techtips/electrical.htm www.xenons30.com/reference -
Pretty sure that there's a diagram in the electrical section of the FSM. If no one comes through with the easy answer.