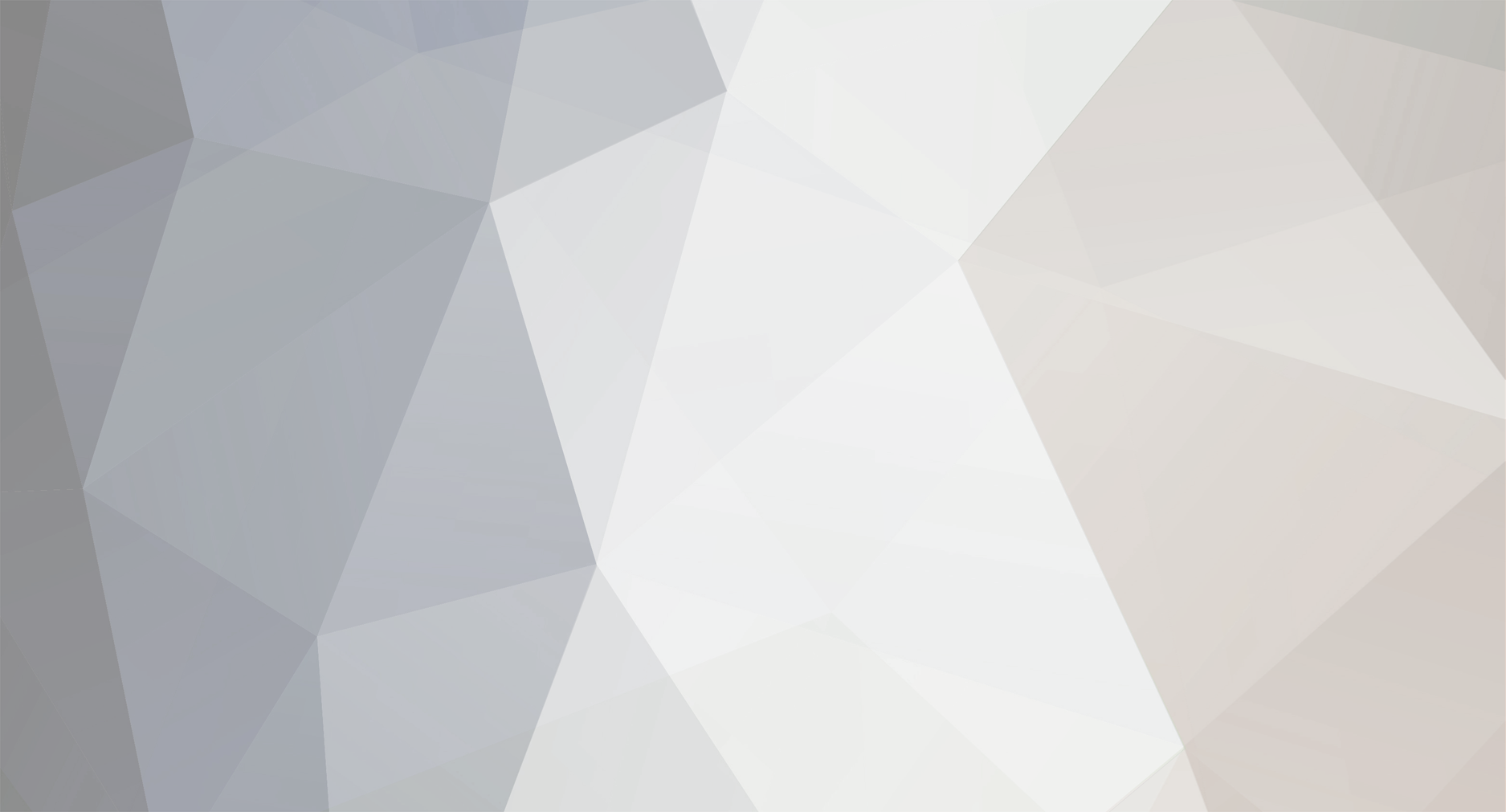
Brad-ManQ45
Members-
Posts
1775 -
Joined
-
Last visited
-
Days Won
6
Content Type
Profiles
Forums
Blogs
Events
Gallery
Downloads
Store
Everything posted by Brad-ManQ45
-
Warren is going to mount his just ahead of the cat...
-
The 280 ZXT's had 2 3/8" exhaust pipes, so you are bigger than that now. For an NA engine, I imagine 2 1/4" pipe would be about right.
-
ZXT's used vacuum pumps to insure they had vacuum to work the cruise control. Haven't heard of the pump you're tal;king about, but no reason for it not to work. Doubt you'd need it though... I'd be worried about that 8" though....
-
There are actually 2 humps in the torque curve as you are accelerating - corresponding with the efficiencies of each turbo. Think like a 2 hump camel vs a 1 hump. The 2 hump camel will have its' second hump higher in the rev range and of course will have a higher amount of torque. If racing, you'd be better off with a single curve/hump for controlability reasons. Not only that, but even the TT RX7's and Supras go to Single turbos for POWER. For street and autocross, where instant acceleration is needed, two matched smaller turbos will spool quicker and still be linear - best of both worlds, though more expensive and involved. The real reason the ttRX7 went sequential is that wankels are notoriously dismal at providing low end torque - and sequential turbos do a good job of providing that on the street, but once again, what works on the track ain't neccessarily the same...
-
What kind of cam are you running to only have 8" of vacuum at idle? Sure your timing isn't off? What shape are your valves/guides in? Inquiring minds want to know...
-
TMC has springs for around $149... Have 'em on my '75. TMC is Traction Master Corp. They have stuff for Z's, 510's and of course - Mustangs. They also have good sway bar kits...Have them too...
-
I went and found the write-up in Car & Driver - their quote (note quite verbatim perhaps but absolutely correct as far as syntax and message) - "The big weight savings is the 136 lb chassis - 1/3 less than the heavier but stonger steel chassis." Like I said earlier, I'm not sure that 70 lbs saved (I know I said 40 earlier) is worth it if it means a more flexible chassis - not only from a control standpoint, but longevity reasons. I would suspect that for those of us who would actually buy one of these cars and put it to the use intended, that we wouldn't deal much with water, so eliminate the obvious advantage of no rust that an aluminum chassis has. You are left with a chassis that is more flexible, and aluminum fatigues quicker than steel does - If both frames flexed the same amount, the aluminum would fatigue quicker. But in this case, according to C&D, the steel chassis is stiffer also, so I stand by my statement. We've heard for years that the vettes were always a little too heavy, and I think Chevrolet had a goal to get the weight to the parameter people have been bandying about for all this time. I'd rather have the additional 70 lbs in a steel frame, or apply another strategic 30 to the aluminum one with proper supports/mounts for SCCA rollbar mounting (thanks Mike for the heads up on that - hadn't heard about the issue) to make it as stiff as the production chassis (without roolbar installed). In this case I will use the analogy of cars and women (male chauvinist pig that I am) and state that in both, losing TOO much weight can be a turn off...I like to be comfortable with the way they both feel.
-
As others have stated more wordily - PCV=cleaner and longer lasting engine.
-
I had one magazine that stated that the schassis flexed a bit more than the production - maybe because of the bigger tires....
-
Actually, sequential turbo are very non-linear in their power curve, and difficult to control in racing (curves). Had a friend that has owned ttRX7's, Supras - he's got a Z06 now...
-
Mike: The only aspect of the new car I am not enamored of is the use of aluminum for the chassis - I think the ~40 lbs saved at the increase in chassis flex was a bad tradeoff....
-
Not bad at all for not even having to take it out yourself... Heck, I believe that's a good price if you had to pull it youself - am I wrong here guys?
-
I certainly don't mind your changes, my customization was of someone else's design. My garage has a lip at the entrance to keep out water, so I opted to use 10" pneumatic tires to make it easy to roll in and out for blasting purposes. Turning the car around in the garage is not an option, just rolling in and out, so I just welded more tubing onto the existing base to keep the initial height (and consequently total height) down. With 1/4" thick square tubing, I don't have to worry about things bending. by the way, here is the link that I got the plans from (minus my own updates): Rotisserie I believe this was actually copied from another site that someone had an MGB restoration project from, which had some nice pictures, but appears to be gone. The above link does have a materials list and good directions. By the way, my gallery does have a pic of my rotisserie setup...
-
When it comes to headlamps for our Z's, I will state unequivocally that Cibie E codes are simply the best - I used to sell them, Hella and SEV Marchall. Do not get taken for a ride when purchasing H4 bulbs - if they look blue or "White" (ie: not a clear glass bulb), you are losing lumens - PERIOD!
-
My notes for 83zxt to MSnS-e on v3 PCB (Hall and VB921)
Brad-ManQ45 replied to a topic in MegaSquirt
Thanks 1seymour! I will be eventually installing MS in my '83ZXT, allthough I am thinking about EDIS for ignition... Please keep us informed about your experience and especially tuning. You might want to post what other mods you have done to your ZXT... Brad -
Wilwood tandem BRAKE master cylinder in a 280Z
Brad-ManQ45 replied to a topic in Brakes, Wheels, Suspension and Chassis
Sure they're not 3/8"? -
Have to agree w/Grumpyvette here. ScottyGNZ had Hypereutectics in his GNZ and blew a head gasket without having any problems from the pistons - the key of course being to AVOID DETONATION. IMHO, you mightg as well get forged and have peace of mind/fudge factor when dynoing and tuning on the road.
-
Assuming the same amount of overall flow for TT vs single T, the biggerr turbo's diameter has to increase a pretty good amount - ~1/2 to 2/3's bigger for the same amount of flow. The increased diameter causes rotational intertia to go up not by a straight factor, but exponentially. Hugh MacInnes covers this in his book on turbocharging. Road racing a V engine, he suggests using two turbos for quicker spool. Drag engines want to keep the turbo going as fast as possible between shifts, so the use of one BIG mamma-jamma is the norm (think like the latest TT Supras going to one big one)).
-
and musicians...
-
Depends on what type of wastegate you use...
-
(Probably dumb) strut sectioning question
Brad-ManQ45 replied to scott19's topic in Brakes, Wheels, Suspension and Chassis
The purpose of sectioning the strut tube is to allow the use of a shorter strut in the tube in order to gain suspension travel lost when using shorter/stiffer springs. If you use springs that lower the car 2", then you have lost compression travel when using the stock struts - you have moved the position of the piston in the strut downward 2". Since the Z only has a limited amount of traqvel to begin with, you haqve to have really stiff springs in order not to bottom out, which compromises ride qand handling in bumpy corners. You can use a lighter spring, have more compression travel, hold larger bumps better and ride better with the sectioned struts and shorter inserts. -
I will chime in and say that for most HybridZ-ers, MIG is more forgiving and easier to learn for what we are going to be doing, sheetmetal and schassis work. If you start adding thin aluminum into the equation, then TIC starts looking good. MIG was developed for the mass production auto industry for body panels. Foir people just starting out, MIG is a great way to get into welding. I took classes, and I too bought a MM175 - this is one fine machine. I learned on LIncolns in class, but I have heard some bad stories about CS at RED that mad me pick BLUE, and I'm glad I did. I have finished my rotisserie and am awaiting time and funds for hoisting the beast up and attacking floorpans and subchassis connectors - soome warmer weather wouldn't hurt either.... I will back everyone else who has said to go with a quality product. Even professionals have a hard time with the cheap crap. For the real beginners worried about burn through on sheet metal, Harris makes a product called "Twenty Guage" that is actually .031", and is a cored wired that you use gas with. VERY difficult to burn through with it - you really have to be trying. As far as weld quality goes, MIG and TIG can meet the same standards, but it is a little harder with MIG - you simply can't see it as well because of the gun tip. I have produced some absolutely beautiful welds (mostly when practicing, of course!) - That stack of dimes can happen with MIG just as it does with TIG, but it requires a lot of experience and practice. I happen to be fortunate because Warren lives about 8 miles from me and has a TIG, we just tore out his rear suspension arms to put iin camber and toe adjusters on his 280ZXT....Possible to do without removing rear suspension member if you have a right angle dril l- heh heh!
-
I'd say that on a stocl 280ZX you're better off with the turbo in the stock location because there are hood vents to get heat out when idling. On a 1st gen, I wouldn't think there would be any difference, except for weight distribution...