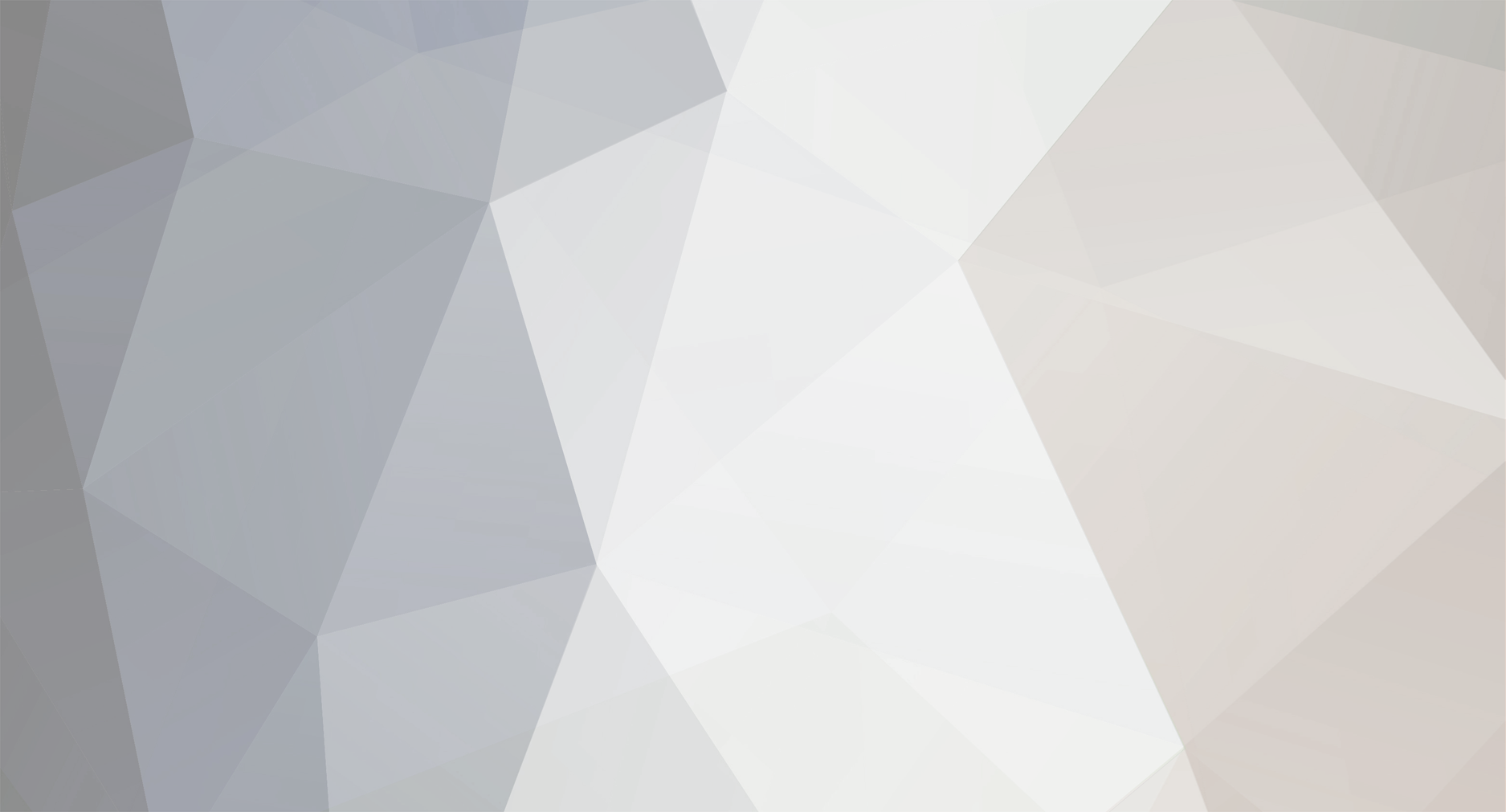
ctc
Members-
Posts
275 -
Joined
-
Last visited
-
Days Won
3
Content Type
Profiles
Forums
Blogs
Events
Gallery
Downloads
Store
Everything posted by ctc
-
77 280z cannot start, injectors not functioning?
ctc replied to ISPKI's topic in Ignition and Electrical
That double relay was problematic for me. I had two of them go bad very quickly. Bosch l-jetronic used a similar double relay, but much better sealed. Sounds like you are making progress. If you get voltage to the ECM and still no spark, I would go find a known good ECM. -
77 280z cannot start, injectors not functioning?
ctc replied to ISPKI's topic in Ignition and Electrical
The ECU needs power when cranking or the injectors will not fire. I don't have my FSM at work, but pin 4 should have battery (+12V) while cranking. Use the FSM page I referenced above to verify the pins. Also double check the injectors are powered when the engine is cranking. The way the key works is to disconnect the run position and power everything from the start (crank) posisition. So, If you only checked for power to the injectors and ECU while the key is one, they might not be recieving power when the engine is being cranked. I would focus on getting the ECU power when the engine is cranking. A check you can do, is to jumper the starter solenoid while the key is in the on position. This will cause the starter to engage without having the key in the start position. If the ECU is functioning correctly the engine will start. Resistance between the ECU plug and injector plug should be really low. It would show infinite ohms if there was a open. Just wanted to make sure you did not have a break in the wire between the injector and the plug. -
77 280z cannot start, injectors not functioning?
ctc replied to ISPKI's topic in Ignition and Electrical
First post, strong spark. No injector firing. -
77 280z cannot start, injectors not functioning?
ctc replied to ISPKI's topic in Ignition and Electrical
So another thing to check, with ECU plug disconnected, Key on, Pins 10 should have 12V. With the key in the start (cranking) pin 4 should have +12V. Also double check that 72 has ground as well. It is the double relay ground, but since the injectors have 12V, it should be ok. I am using the diagram on EF-25 of the FSM to trace the supply voltage and grounds to the ECU. -
77 280z cannot start, injectors not functioning?
ctc replied to ISPKI's topic in Ignition and Electrical
So what was the measured ohms between the ecu plug and the injector plugs (pins 15,33,32,14,30,31)? What pins are missing? Can you post a pic of the ecu pins? Do all the grounds show continuity now? -
77 280z cannot start, injectors not functioning?
ctc replied to ISPKI's topic in Ignition and Electrical
The ECU "supplies" the ground signal by completing the circuit to ground. Your wires should show continuity, and check the ohms, between the injector negative and the ECU plug. -
77 280z cannot start, injectors not functioning?
ctc replied to ISPKI's topic in Ignition and Electrical
Dome light should work. If you want to be picky, I think around 2 or 3 watts is what you want. You can ohm out the injector and build to get in the ball park. -
77 280z cannot start, injectors not functioning?
ctc replied to ISPKI's topic in Ignition and Electrical
So the last thing I would do before the new ECU is to install a test light in place of one of the injectors. The fancy word is NOID light, but any low wattage 12 volt non-led bulb will work. Wire it so you can connect it to the two pins of the injector plug. It should flash when the engine is cranked if the injector is receiving a signal. Or you can buy one, google OTC 7188 Bosch PFI Noid Lite -
+1 This was the point I was trying to get across. Head work on stock bottom end, then see what you need.
-
I guess my opinion, having done the stroker route, is that the extra work and cost for custom rod/piston and crank combinations will not gain you anything on the street over stock rods and crank with custom pistons. Based on the Oz calculator; Stock L28, 88mm pistions comes out 2.883L and 1.648 rod to stroke From above 2.949L and 1.772 rod to stroke. I just can't see where from a drivability/performance stand point you will feel the 0.066L of displacement and 0.124 increase in rod to stroke ratio. If this were a track car, sure every thing you can do for a couple extra hp, great. I just don't get it for a steet engine other to be able to say you did. Now $$$ in head and cam work plus dyno tuning to dial it in. That wound be money better spent than crank and rod work. Edit: if others can post quantitative evidence that given the same level of build and proper combination of compatable parts, that a 3.0L stroker has significantly more torque than a L28 given head and cam work dialed in for each engine. I will humbally change my opinion, but I haven't seen the evidence yet.
-
Having built a stroker NA motor and spending some coin to do it, I will never do it again. The time and money spent trying to get that last HP would have been better spent on gas driving the car. My biggest issue, besides trying to sort bull from bologna, was the set up time required to finish the build. Multiple iterations of build up, measure, tear down, fly cut valves, assemble, measure again, tear down, clearance block for rod bolts.....etc. For a street car, not intending to maximize hp for a given set of rules, my advise is to bend the rules. Money in EMS or carb tuning, proper cooling mods, head work with a cam designed for it, blue printing the engine, stock or near stock (forged) bottom end, oil cooler, etc. will be money better spent. Read up on all the finer details of a stoker build and ask if it is worth it to you for the few extra hp it will bring. On the seat of your pants dyno, 50hp won't matter one way or the other. Also, consider your driving style. My engine had 50mm Mikunis, light flywheel, lumpy high lift cam, basically a full race prep. Idle was 1200rpm, you either dumped the clutch at every light or stalled it, trying to even cruise to the burger joint became a pain. Looked into EFI to see if I could tame it some and still keep the fun, ended up going L28ET. For me, after dropping a bunch of money, doing that again just seemed foolish. Couple tweaks here and there and I am back to the same power level, but much better on the street. I know you don't want turbo, but my point is that a 200hp NA engine can sometimes be more fun than 300hp, at least on a daily basis.
-
77 280z cannot start, injectors not functioning?
ctc replied to ISPKI's topic in Ignition and Electrical
If you take an ejector plug off, with the key on, do you have +12v on one pin and continuity to ground on the other? -
Spray bar in a spacer behind the throttle body. Think of the kind you bolt between a carb and intake on a v8. Could be really clean install if you plumb the lines under the manifold or tuck them up by the thermostat. Or you might be able to put it where the cold start valve went. My 2 cents. And as an aerodynamist, putting it at the end of the manifold will not lead to even cylinder distribution.
-
Keep in mind that Rock Auto is just a middle man. While I agree it is their problem to use quality suppliers, ultimately Aisin is responsible for incorrectly labling and not remanufacturing the part correctly. The fault is with Aisin quality control for incorrectly marking the part. Rock Auto is only at fault for buying parts from a company that mislables them. I think it is reasonable for Rock Auto to offer a refund to you and then contact Aisin about the quality issue. Welcome to the age of internet buying vs. your local counterman. I would also bet the part they inspected, looked at photos?, had the correct impeller. Oh, the irony of it!
-
I thought this also once, but it is incorrect. Stock NA cams offer a power increase over the stock turbo cam while still playing reasonably well with stock engine management. If you have the ability to tune, get a cam matched to your application. If it is all you have on hand, run it. Just don't expect huge power.
-
I think the old time expertise is still for sale today. A few shops come to mind. I think the problem is everyone wants something for free. That it should be given to them.
-
L28et Swap Cold Air intake placement with large FMIC
ctc replied to halokilller's topic in Nissan L6 Forum
So what you are saying is there is no reason to have a cold air intake if you have an efficient enough intercooler? Yes I am just trying to understand how a cold air inlet doesn't lower the temps out of the intercooler. It does, but I was addressing Tony's point that your intercooler was sized poorly. If it were properly sized, you would not have seen the change in after cooler temps when you moved your air intake to another location. So can we see some examples of this in a calculation or formula? Go look at an good intercooler site, they have sizing equations posted or call them direct. I will leave the math as and exercise for the student and those interested. To Kash, as an ME, I think you would like people to be more precise in their understanding of thermodynamics, especially those that do share the foundational knowledge we acquired in school. Generalizations belong on other sites, not this one. Rules of thumb, depend on the thumb. To simply state "cooler air in equals cooler air out" neglects the cooling medium being used. In some instances, I bet I could get an intercooler to heat the air from the turbo further. Based on your knowledge base, I am supprise your first post didn't recommend properly sizing the intercooler first, then getting colder air into it (both inlet and cooling air). TO THE OP's ORIGINAL QUESTIONS; Will the fmic make the cold air vs hot air intake negligible? Yes, if adequately sized. Where do you guys mount your intakes to make them breathe cold air? Outside the engine bay or boxed to shield the intake from engine bay heat with a fresh air supply. -
Then do and post pics!
-
L28et Swap Cold Air intake placement with large FMIC
ctc replied to halokilller's topic in Nissan L6 Forum
Wow that is an over simplification. Did you put and engineering or thermodynamic thought into that statement. You totally missed Tony's point. A properly sized intercooller will extract enough heat to get the charge air down to almost ambient or even sub ambient, depending on the cooling medium chosen, regardless of inlet temperature. The key ratio is the cooling medium temperatre to the charge air inlet temperature for a given intercooler design. In the case of the above FMIC example, with proper sizing, it will remove the heat added to the ambeint air from not only the turbo, but any additional heat introduced by the engine bay. Being simplistic, an intercooler by definition takes the intake air at an elevated temperature and extracts as much heat as the cooling medium and thermal losses allow. -
San Diego SCCA region links posted above. Stock cranks and rods, massaged, ignition and fuel control. Interesting comments on valve train geometry. Kind of sounds like the advice every one in the know on here gives. Taken to another level of course.
-
Or you could try talking to those people who, were/are Electamotive. It's not like they are all dead or anything. The 80's wasn't that long ago!
-
I ran mine for two years without filters, driving it two or three times a week. If you keep up on your maintenance, wiping them down frequently and plan for a rebuild at shorter intervals, you can run without filters. Don't drive on dirt roads or in the rain. After two years, there was starting to be visible build up in the throats. You just have to careful and think about where you drive.
-
Behold post #9 from a quick google search http://forums.hybridz.org/topic/33724-ls1-project/ Also try dallas ls1 swap site:hybridz.org in google
-
I know of two 5.6 Titan swaps, one into an S130, that are documented here. One was complete and one wasn't. Based on the part availability comment, you should stick to engines that are domestically available. That would rule out all the RB's. Do some searching and PM people who have done the RB swaps, ask them how it's been driving the car after the RB is installed and what issues they have had. IMHO a RB swap is more of a prestige, keep the heritage kind of swap because of the cost and parts sourcing issues involved. Some will say you can do an RB swap cheap and easy, but I would converse with those who have pulled it off well (there are a few examples on this site) to find out the real story. I think most will agree a well executed RB swap will take a great deal of thought and bucks. Again my opinion only, but I think there are a few issues with the RB swaps that get glossed over in the sparkle of the that first youtube engine start up video. Two of the top of my head are transmission choices and how hard the RB was flogged before you got it. The LS1/2 swaps are well documented and would initially be your best choice if you are set on an engine swap. Part availability is not an issue and great domestic aftermarket support. Do not fail to consider all the other body modification that may be required (engine cross members, fire wall, trans tunnel) that may or may not be required based on the swap you choose. Also consider the rest of the drivetrain and things like guages, cooling and interfacing with the vehicle wiring. My real suggestion to you is not to read opinions but talk with those who have completed the swaps and have driving cars. Then decide on what direction you want to go.
-
I should have searched first... From a Tony D post on Zcar "The function is close, but not quite. It's a pressure relief valve that allows a bypass from the lower portion of the thermostat (back of the head) to the pump inlet when the engine is brought up to higher rpms before the engine thermostat is open. When the heater is on, or if the thermostat is open, the valve will never pop open. It is a pump cavitation relieve device. This works in conjunction with the internal bypass on the right front of the block to the water pump inlet, and the 8mm line from the lower thermostat housing through the throttle body and to the water pump inlet. Those two lines are more than enough bypass to let the engine recirculate internally at fast idle and idle to warm the engine and get the thermostat open. The thermostat is also spring loaded to open under higher pressures---but this will be higher than cavitation point when cold, so on the later cars they added that valve. It is not necessary if you are letting your car warm up before running the rpms over 3000. Do that, and you will never notice anything. If you insist on cranking the car up stone cold -40F, then jumping onto the highway at 80mph within 2 minutes (like I could do if it got to -40 here...) then this pop valve opening would likely keep you from cavitation on the water pump and housing, along with some overheating issues as a result of the errosion from same. If you leave your heater valve cracked about 1/4, it flows similarly. Knowing these tricks, you can function just fine without it. It's a nice 'idiot proof' device for the car, and god knows we need that with the group here... but a little intelligence in warmup or heater valve position and you will never notice it. Don't tell me nobody here has ever noticed if they turn their heater to full "HOT" and left the fan "OFF" that the car will almost overheat? It warms up WAY faster like that! Why? 15mm of full open hose recirculating from the hottest back of the engine right to the water pump inlet. It can be so efficient the engine temperature can spike before hot water is circulating enough around the thermostat to open it! (especially if someone removed thermostatic control heat to the TB and or Manifold and didn't restore a proper bypass line to the bottom of the thermostat housing...) Those lines are like Emissions Devices: Just take em off, the only reason they were there is because some guy's cousin had a factory making the parts and that's the way Japs design cars..." http://www.zcar.com/forum/10-70-83-tech-discussion-forum/301526-what-tee-fitting-thermostat-inside-heater-hose-return-path-used.html