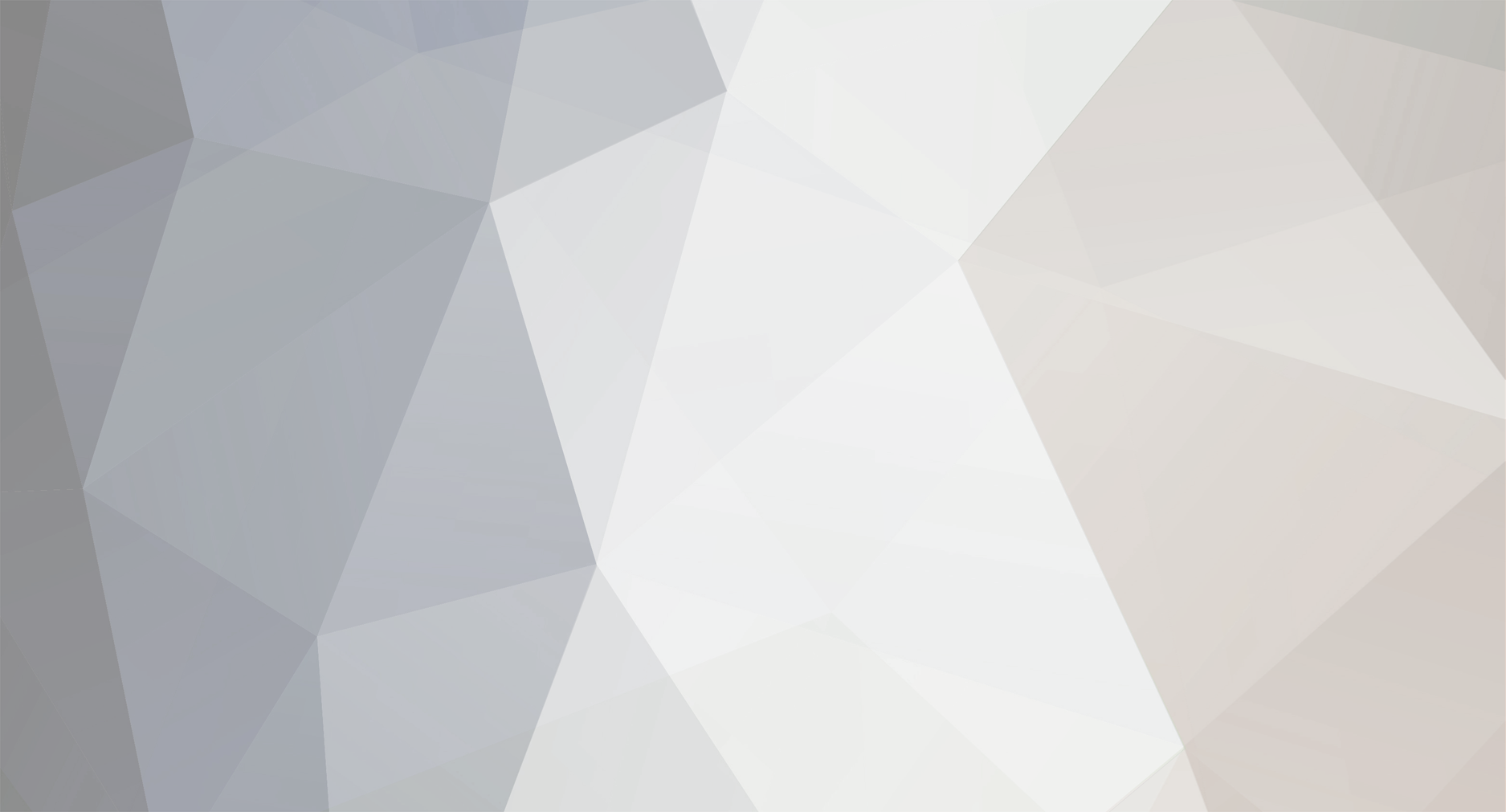
Brad-ManQ45
Members-
Posts
1775 -
Joined
-
Last visited
-
Days Won
6
Content Type
Profiles
Forums
Blogs
Events
Gallery
Downloads
Store
Everything posted by Brad-ManQ45
-
+1 for 112!
-
Warren has made the swap to a 2004R from a Grand National, having made his own pieces and bought one piece - the flexplate to converter adapter from someone else. He is selling the whole kit, but I don't know for how much, but eventually I will buy one for my car.
-
If you are actually looking for advice then here is my .02... Set up ground rules based on consideration for each other ahead of time... Ex: In return for trying to leave the toilet seat down, she agrees no hose/feminine products draped all over the bathroom. Let her know your pet peeves about your sister if she doesn't already know, and if she has brother(s) that do things that bother her, get her input on what her gripes with him/them. Figure a way to try and live together even for only a short time. It may be that something will grow out of the situation, so try being a mensch instead of a hoser with her and at least keep her as a friend. She's definitely a bit of all right looking and you definitely shouldn't even THINK about screwing up her opinion of you as a roommate/friend due to lack of consideration - think of moving out and never seeing her for the rest of your life - or even worse, having her tell stories of your peccadilloes to whoever will listen... Goop, or whatever else works well waterless with paper towels has saved my marriage - I'm 3/4 clean before seeing the sink. I also use latex or some other work gloves a lot to keep grime off the hands as much as possible - but this can be clumsy at times and there will always be grime. NOTE: Using gloves cuts down on the time you spend lazing around using a knife to clean under you fingernails - this greatly aids them in feeling okay with your being around - especially if you're not married to them. One of the things I have learned from several relationships, a marriage of 8 years and the current one at 20 is the older I have gotten the more I have thought about my actions in advance - and not just about girls. Part of this is hoping to not have to do something over again, thus saving time and energy - which I definitely have less and less of the older I get - just never thought about it when I was young (say college and a few years after), never thought I'd live to be as old as I am, and just wanted to score big at whatever I was into at the moment and to hell with the consequences. It may seem to sound like what your parents would say, know what? - you're right. That doesn't make them automatically wrong. I grew up in the 60's, was at Woodstock, rebelled at what my father said and actually was stupid enough to let him know how wrong he was about being quick to judge based on what seemed scant knowledge/observation, and he simply said that one day I will call him up and tell him he was right. I did, after I was out in the real world and learned what to look for. I am hoping that even though I'm old enough to be your grandparent you will accept this small bit of advice from a former and still bit of a rebel that has learned a lot since school - especially what is most important in life - relationships - between yourself and everyone you come in contact with. Tis type of attitude is not conducive to becoming matujre
-
Don't go back to that exhaust shop. Or any of them that recommend a Flowmaster for a turbo car either for that matter. If you need to ask why you haven't used the search feature of this forum.
-
It really depends on what cam you are running. Stock cam, put the compressor section on a stock turbo. Upgraded cam, have the stock turbine housing machined for the P trim turbine.
-
That 4th prong is for 120V and can be capped off. I wired my basement and added circuits to my garage, but paid for a permit and inspections by the county, so no insurance problems. I think it was $30 for the permit, and well worth it because the inspectors that I talked to answered questions and gave advice that was worth every penny... Nowadays, everyone is starting to like self-reliance and thrift-except for union workers and people charging 35-75 dollars an hour for easy work.
-
PM'd you.
-
Warren, I'm not about to get into a pissing match with you, I will simply make a few statements and observations, then I'm done with this thread.... That PROVEN company has not been in business as long as Turbonetics. They STILL don't have working website (ie: not a placeholder page). As far as I know, the only reason anyone here knows about the company you were using was because of one member here who sold their products, and yes, there have been failures. Turbonetics has been around a LONG time - years and years before I even bought my turbo in '94 and are still around and apparently still providing good product. We already know not to trust that company you've had to deal with. And no folks, I will not name names, but the member selling these turbos is no longer in the business. There is no way that any of the woes Warren has had are a result of anything he did wrong - you just simply don't know how much attention to detail Warren puts into anything he does. Now, I would probably entertain doing business with a company that gives discounts on Turbonetics Turbos - but only for turbos that are stock Turbonetics - not frankenturbos using some Garrett and some Turbonetics and some who knows what. Come to that - even mixing up parts from the same manufacturer for a frankenturbo such as what Warren had, if done by people with no long term reputation can lead to exactly the problems we're talking about too. If I can see the same specs in the Turbonetics catalog and on the sellers website and they state it is a Turbonetics - then as far as I'm concerned, if it isn't a real Turbonetics when it comes in it'll go back - I'm protected by laws governing false advertising ans my AMEX account reps will back me up. I don't mind saving a buck, and I'm sure due diligence of a sort was used in sourcing a supplier by the person who sold Warren his, but sometimes one simply has to pony up the proper amount of valuta to insure getting a good product. For something as expensive as a turbo, that extra 10-25 percent can be considered insurance - especially if you're talking about a daily driver. For a weekend or race car, some will go cheap but they almost always DNF eventually. I am sure there are companies out there that can put turbos together as well as Turbonetics, I can think of a few that have good reps that have been reported here. Because I have had good luck with Trubonetics (the ZXT was my daily driver at the time), I see no reason to look anywhere else. Other people have had other good experiences with other companies. There are at least two people out of our small population on this board that have had problems with the turbos from this one particular company . I am only encouraging people to do business with companies that are known to be trustworthy and not have to shell out big bucks later to save a relatively small amount on their initial purchase. I'm sure I've said more than enough, so I'm outta here...
-
Warren - don't give up on Garrett just yet. Concentrate on dealing with PROVEN companies that provide good units. Turbonetics comes to mind - I've had no problems with mine for over 40K.
-
I have an '83ZXT and I have a welder and know how to use it. I have replaced half a firewall and half an inner fender panel and part of the battery tray on mine, have yet to take out the windshield and get to the bubbling at the top edge and any rust in the windshield channels, and have a bit of rust behind the driver's rear wheel opening. That's all the rust on mine. If it were my car, I personally would look for another shell.
-
What resistance to use with low impedance injectors?
Brad-ManQ45 replied to Zmanco's topic in MegaSquirt
I may be off base here, but electrically speaking, when you are talking about using low impedance injectors, the resistors should NOT be in parallel, but in series - in parallel, you are lowering resistance even more - in series you are increasing resistance. That said - to take maximum advantage of low impedance injectors (you didn't mention what version of MS software you are running), racingmini_mtl has injector driver boards that let you run low impedance injectors and get maximum resolution from them - fine idle and better tip-in response. I bought two sets of two - one for the L28ET project and one for a V8 project. Please let us know how the EDIS works out... -
+1 on the turbine A/R. You also have no idea what trim the compressor section is, so forget it - not worth the money.
-
Upgrade a N/A to Coil Packs and Remove MAF
Brad-ManQ45 replied to Albert's topic in S130 Series - 280ZX
Please be aware that a toothed ring is not the only way to achieve CAS w/MegaSquirt. You can use the same types of magnets that Electromotive uses and mount them (epoxied) in holes drilled in the back of the dampener and fab a solid mounting bracket for a Hall sensor, which is what I will be doing. MS can be set up to utilize either VR or Hall sensors, and it's easier to use the Hall sensors - less circuitry. It is the same setup that you would use for the stock distributor, since it's optical (both Hall sensors and optical sensors output a square wave signal, versus a sine wave for the VR sensors, which require signal modification to be a square wave to work w/MS. Doing a 12-1 setup is not that difficult, but you can go 36-1 if you want - just buy more magnets. 6-1 would be the least you can get away with. More magnets = greater resolution. Either way, once you determine where the sensor is to be mounted, and where TDC is, you want the missing tooth to be ~60 degrees ahead of where the timing mark shows TDC on #1 cylinder. This eliminates a lot of hassles with the toothed ring thickness, pulley alignment and having to have the bracket go through the belts so the senso can read the teeth if mounted on the front of the pulleys... -
Has anyone gone from 60 mm TB BACK to stock?
Brad-ManQ45 replied to Zmanco's topic in Nissan L6 Forum
It's gonna be a GM 4L60E and I have a converter from PTC that is around 3K based on what I gave as parameters. Boost onset ~2800, full boost ~3500. Torque @ 3000 ~300 lb/ft. This ought to be fun - basically the same 1st gear as the T5 w/a torque converter - 2nd ought to hit HARD! -
Has anyone gone from 60 mm TB BACK to stock?
Brad-ManQ45 replied to Zmanco's topic in Nissan L6 Forum
Since I am converting my car from a T5 to automatic, I'll leave the linkage the way it is - let the torque converter work for me! -
I think that I remember only the 406 and 427 engines were cross bolted. All of the blocks were "Y" blocks w the main rails extending below the centerline of the crank for rigidity though.
-
I'm 56 and have been in and driven/rented quite a few cars as software trainer all over the US. I have 2 Z's, a '96 Lincoln Town Car and a '94 Q45a. A few years ago my wife was hit in the Q by someone and we rented a 4 cylinder Sonata. It had more leg room in the back than the Lincoln! Great mileage, just as if not more quiet perky acceleration. This was the year that C"&D ranked it over the Camry in a shootout. They have gotten nothing but better since then. Good choice!
-
Don't know about the rise in temp issue - most of it goes out the exhaust anyway, but if I were to get the tops coated, I'd make sure it is a 3 layer coating. A single layer coating, which is what most everyone not in the aviation/racing business uses will flake of fairly soon. It takes 3 layers with different expansion rates to keep the coatings on the piston. Most expansion on the top layer and work your way down the scale closer to the piston. Swain has their Gold coat that I believe is the 3 layer coating - I hope that's what you got...
-
L28ET Problems, need solutions please help!!!
Brad-ManQ45 replied to ArchetypeDatsun's topic in S130 Series - 280ZX
Did you take the stock Pop Off Valve off the intake manifold and plug the hole? If you didn't then once you build more than ~7 psi you WILL run rich. I believe you would be better off buying a MegaSquirt or other aftermarket ECU and using the settings that others have already set up for their cars (with the same basic setup ie: turbo size and injectors) as a base point. -
Hella vs Cibie vs Bosch vs AutoPAL H4 Housings
Brad-ManQ45 replied to 240Z_Master's topic in Miscellaneous Tech
I've always put Cibie's on my cars and have loved them. -
Looks like you don't have the stock fuel rail behind the bracket on the left side looking from the front. You will want to make sure you have a washer that thick if you aren't using the stock fuel rail.
-
Nigel is right - only the automatic ZXT's had oil coolers - that's because the load the tranny put on the water cooling system was too much along with the turbo to keep oil cool.
-
So, did you guys hear about the new Honda-Nissan merger?
Brad-ManQ45 replied to auxilary's topic in Non Tech Board
Having been backed into 3 times in 2 years, all by women, I am firmly convinced that putting a car in reverse disengages their brains... -
Level Ten can do whatever you want...