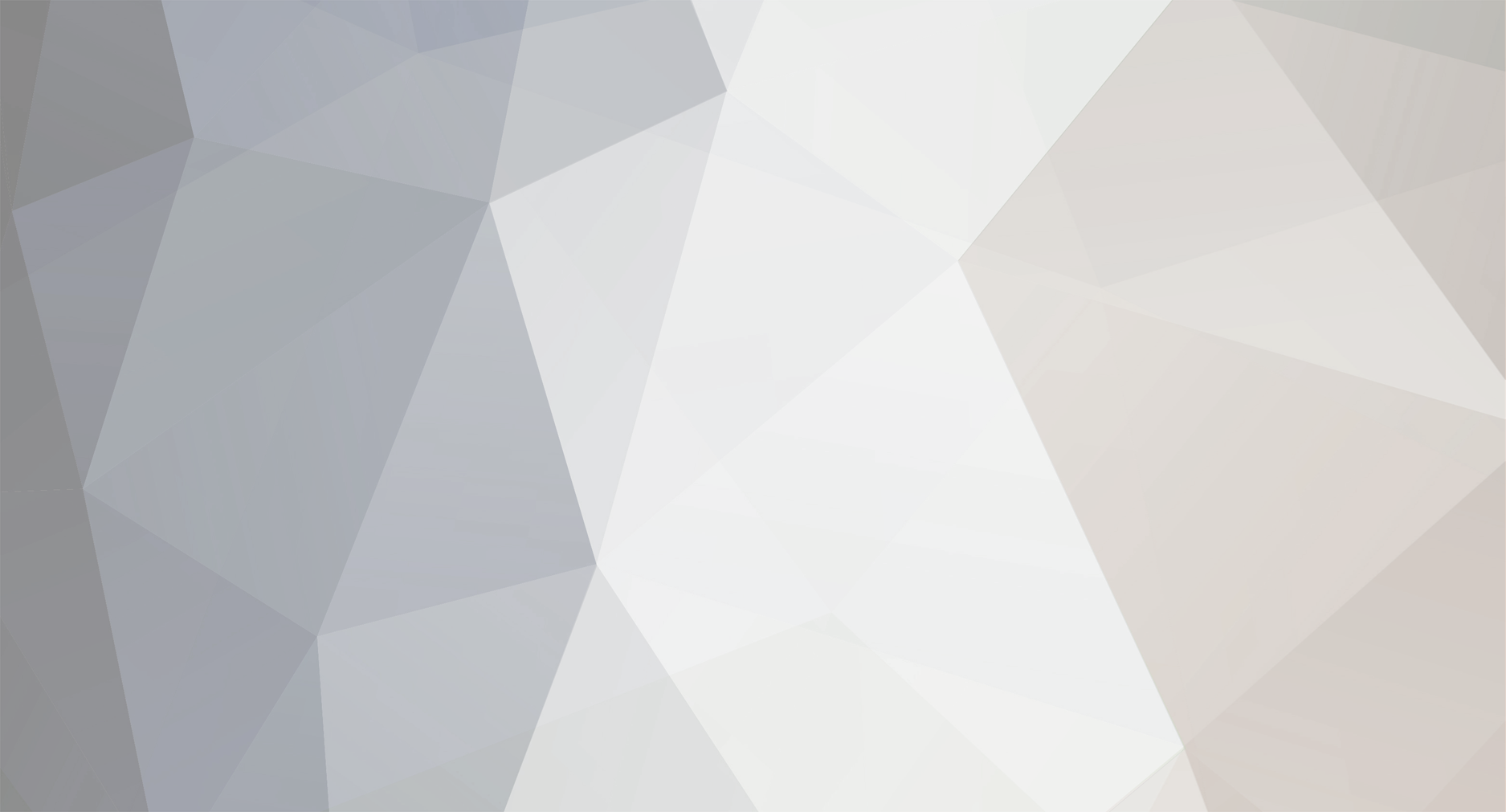
NewZed
Members-
Posts
6650 -
Joined
-
Last visited
-
Days Won
66
Content Type
Profiles
Forums
Blogs
Events
Gallery
Downloads
Store
Everything posted by NewZed
-
Fuel Pump Relay on Passenger side keeps clicking
NewZed replied to abbascamille's topic in Trouble Shooting / General Engine
Forgot to say, if you tried some things tell people what you tried. "Every possible idea" could mean one bad idea. -
Fuel Pump Relay on Passenger side keeps clicking
NewZed replied to abbascamille's topic in Trouble Shooting / General Engine
Firstly - is this a Ford? A chevy? 1985? 76? And the two facts you posted could just be a correlation, not cause and effect. Won't start. Relay clicks. Not even clear that you're sure it's the fuel pump relay. Sounds like a dead battery or bad battery connections. -
Weird no power to fuel pump 280z 76'
NewZed replied to ericp501's topic in Trouble Shooting / General Engine
Looks like there's no fuse on the power supply line to the fuel pump relay. It comes directly from the fusible links. Are there other things that don't have power also? Check your fusible links. -
Weird no power to fuel pump 280z 76'
NewZed replied to ericp501's topic in Trouble Shooting / General Engine
You had a good clue with the relay clicking when you opened the flap. Follow the power. The AFM switch must be working, that's one. The relay clicks, that's two. If the contacts in the relay are closing, power should be supplied to the pump through the relay. Get in to the wiring diagram and follow the wires back to the pump from the relay. There's a connector right next to the passenger seat that carries the power back. Since you know you have the AFM and AFM power in to the relay working, and you know the pump works, check the relay itself if the wires back look right. There's a procedure in the EF chapter. You'll need a meter. Make sure that power is being supplied to the relay to run the pump. There might be a fuse, can't remember. You can also disconnect the wires by the passenger seat and supply power there if you're careful, or check continuity back through the pump motor. Break the chain in to parts until you find the broken link. -
Weird no power to fuel pump 280z 76'
NewZed replied to ericp501's topic in Trouble Shooting / General Engine
Not really clear what you're saying. You said that you bypassed everything, so why would the AFM and relay matter? No power to what? Why would you push the flap with the key in the Start position? The flap controls it in the On position. Sounds like you've collected some information. You're just not using it right. Try putting everything back together the way it should be, disconnect the little yellow wire to the starter solenoid, then turn the key to Start. That should send power to the pump. If it doesn't spin, check for voltage at the terminals with the key turned to Start. Or put everything back together, turn the key to On, and open the AFM flap. The pump should get power. -
Any metallurgists on here? Input about breakage
NewZed replied to BluDestiny's topic in Miscellaneous Tech
I knew that somebody would bring that up. That general design is ceryainly everywhere. The location of the ARB end link seems closer to the stress point though in this case, than a comparable Z car arm. Pulling and pushing more on the arm itself than the wheel hub. The leverage factor is higher. -
LS SWAP 280Z e A few questions for the wiz's
NewZed replied to TheZkid's topic in Gen III & IV Chevy V8Z Tech Board
With wiring, if you have to ask these kinds of questions you probably shouldn't be attempting it. The Hazard switch alone foils most people. You're probably replacing the wiring because it looks bad. But it probably functions fine. I'd leave it and do the engine harness alone. That effort alone will help you decide if you want to tackle the body harness. The engine harness should feel like a piece of cake. If it doesn't, think twice about the body harness. -
Why do you want to rebuild it? The 71B's have some noises that they make normally, like the rumbling bearing with the clutch pedal up in neutral, and the worn factory parts are often as good as new replacement parts. Many people have been happy with just using a better fluid, like Redline MT90, if' ti's a synchro problem. Make sure you're rebuilding for the right reasons.
-
Any metallurgists on here? Input about breakage
NewZed replied to BluDestiny's topic in Miscellaneous Tech
Looks like a terrible design. A bolt ot threaded rod, essentially designed for tensile loads, used to handle a side load, with about 20 stress risers to choose from for a crack to start, Once the crack starts fatigue will kill it eventually. You can actually see the rusty spot where things started. -
It's not really a bypass hose. Looks like somebody removed your air regulator and the heating plate that sits underneath it and just connected the tube ends. The AAR is shown on page EF-5, 7 and 17 and other places. The proper hose routing is shown on EM-4. Attached a picture. I can't remember if that coolant flow helps avoid water pump cavitation or not. There are discussions about it out there. Replacing the AAR and plate would be a good idea, it's a convenient mechanism. Could also be that everything's there but somebody couldn't get there fat fingers in to the tiny places to fix a leak so just bypassed it.. Anyway the coolant is supposed to flow underneath the AAR.
-
240z engine compartment dimensions
NewZed replied to hutch0421's topic in S30 Series - 240z, 260z, 280z
One of those triangulated aftermarket strut tower braces might help you on the top of the firewall. TC rods might help on the front of the rail, locating it to the transverse link and bottom of the strut. http://www.racetep.com/automaker/datsun-z/z-car-front-ultimate-strut-tower-brace.html -
LS SWAP 280Z e A few questions for the wiz's
NewZed replied to TheZkid's topic in Gen III & IV Chevy V8Z Tech Board
You should ask "why?". Here's a good swap thread - http://forums.hybridz.org/topic/95965-lst56240z-project-mentor-wanted/ -
LS SWAP 280Z e A few questions for the wiz's
NewZed replied to TheZkid's topic in Gen III & IV Chevy V8Z Tech Board
Why would you remove general car function wiring to do an engine and engine management system swap? You're getting distracted. Wires provide power or control signals for functions. Focus on the functions. -
Brakes dragging after 30 minutes of driving
NewZed replied to ditto64's topic in S30 Series - 240z, 260z, 280z
Hard to tell what the timing is on your description but if "recently" means essentially right after you installed the new MC, then you probably have the rod from the booster to the MC adjusted too long. It closes the return hole for the fluid, and the fluid heats up and expands in the lines, actuating the brakes. It's actually a fairly common problem. You may not have adjusted the rod when youdid the swap but the new MC might have its seat for the rod closer than the old one. If "recently" meant months after the new MC was installed and it's been fine for many miles, then never mind the above. -
The two red things don't go together.
-
I think so. See attached. You do realize that many people never get their diffs back together noise-free? At least that's what I've seen in the various internet stories. You might be trading bearing noise for ring and pinion noise. Beware. Probably a fun project but a used factory-assembled junkyard diff is probably the most effective, inexpensive, way to solve your problem. Good luck.
-
These seem to be them - http://www.courtesyparts.com/nissan/300zx/3812006p10/1986-year/base-trim/3-0l-v6-gas-engine/universals-and-rear-axle-cat/differential-scat/?part_name=pinion-bearings
-
what diff is in my 240z? VLSD
NewZed replied to nicholas1122459's topic in S30 Series - 240z, 260z, 280z
The propeller shaft doesn't care what the ratio is. Spin and count will get you close on the ratio. Finding the stamped tooth count numbers on the ring gear will let you do some division. Are you sure that you want to start this swap? If you have a car that runs you might want to keep it that way. You're going to have a tough go, at your current question rate. -
what diff is in my 240z? VLSD
NewZed replied to nicholas1122459's topic in S30 Series - 240z, 260z, 280z
The bolt pattern looks like an R230. Here's a pretty good comparison picture from the back, Post #6. http://www.mgexp.com/phorum/read.php?40,1106874 -
This guy just keeps building his inventory of Z stuff - https://zcardepot.com/product/search?search=battery
-
Owen, maybe? http://forums.hybridz.org/topic/78000-71-240z-roller-for-sale/?do=findComment&comment=741673
-
Looks like he had work done at M and R. They might recognize it. Amateur sleuthing. http://www.mandrauto.com/
-
I dug a little deeper around the web and it looks like only the Mitsubishi version is available. Amazon only has three types. One page has answers from Precision saying Mitsu only, the other two have MITZ in the part number. Odd. Is there a Brute Force brand diff? Can't find one described anywhere.
-
Did you mean Power Brute, not Brute Force? Don't know much about the aftermarket products. Seems kind of inexpensive. They might have gone overseas with their manufacturing. If Amazon can hold inventory for them, they can't be expensive, wholesale. "Ships from and sold by Amazon.com." https://www.amazon.com/Precision-Gear-LOM83-Limited-Differential/dp/B005HJQRQK Here are some CLSD's if you do go used again. Should bolt right in with no flange swap. You could still have the CV shaft problem though. https://whiteheadperformance.com/product-category/240z-260z-280z-70-78/240z-280z-diff-differential-axles-lsd/
-
Here's an odd thought - disconnect the CV's at the diff and let the engine spin it while it's on the stands. The load will be considerably reduced but it will remove any CV-caused noise from the situation. Or remove one CV at a time and do the same to see if one side is tight. If you get both CV's removed and it's still whining, it's probably the pinion bearing. The whine seems too high frequency and too "shallow" to be the typical gear whine.