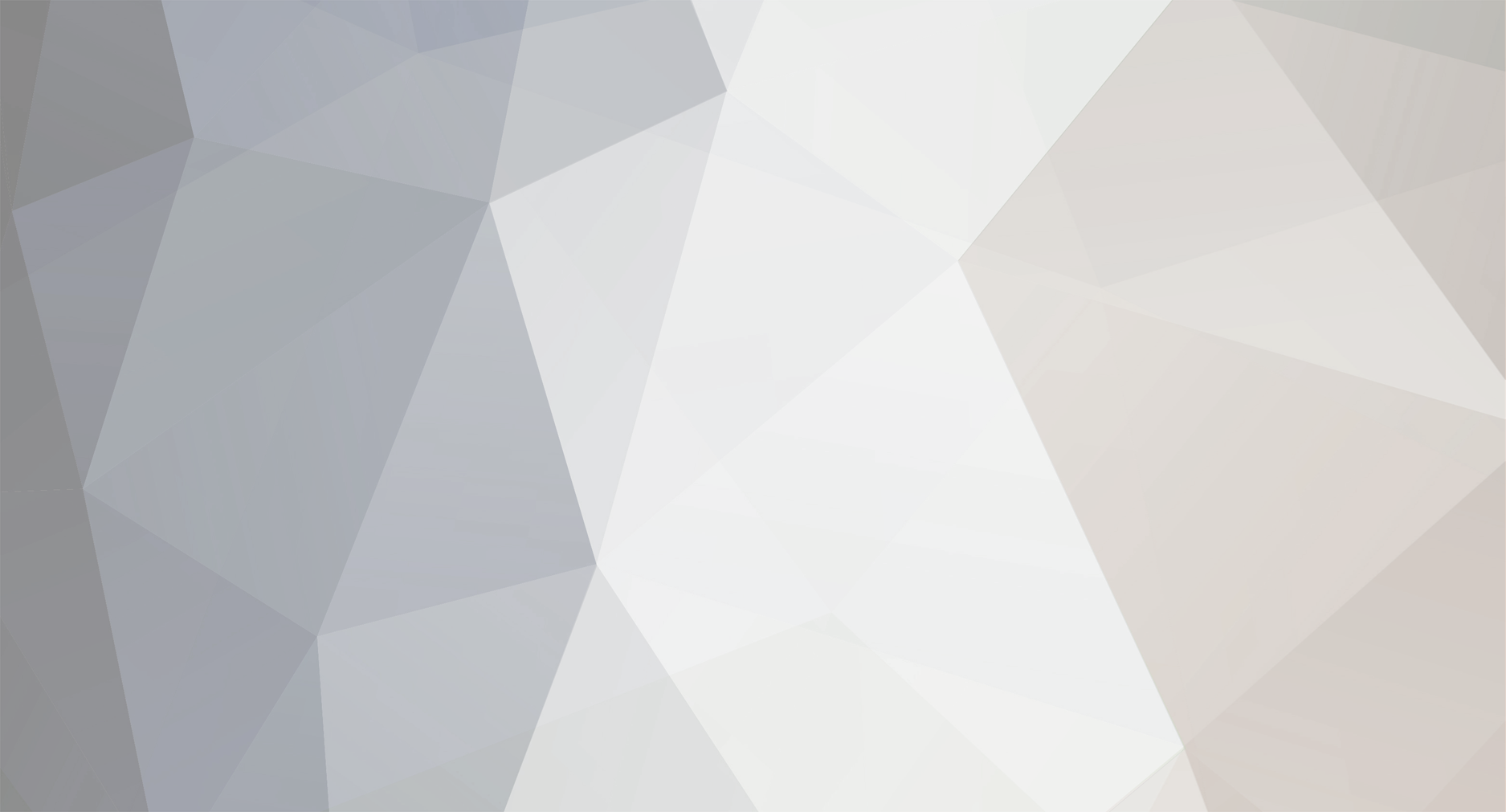
NewZed
Members-
Posts
6681 -
Joined
-
Last visited
-
Days Won
70
Content Type
Profiles
Forums
Blogs
Events
Gallery
Downloads
Store
Everything posted by NewZed
-
No (Low) Rear Brake Pressure
NewZed replied to Twisted46's topic in Brakes, Wheels, Suspension and Chassis
Start at the pedal and figure out how each piece works. You're talking about the booster but nobody uses the booster when they bleed the brakes, it doesn't matter. Nobody has the engine running. You haven't confirmed that your pedal play is correct, as described in the FSM. At this point, by your description, it sounds like the brakes work fine but the pedal throw is too long. That sounds like a simple clevis adjustment at the pedal. Study how the pedal presses on the rod that presses "through" the booster to the MC. Make sure that all of the mechanical play is set correctly. " (the pedal get firm at the bottom and does not go to the floor). The problem is still that I get a lot of travel before much happen. " -
Hmm. Seems like nobody got hurt and a poorly run business might be defunct. Anybody who works with FRP's and paints knows about flammability of the materials involved. Mixed feelings. Thanks for the link.
-
No (Low) Rear Brake Pressure
NewZed replied to Twisted46's topic in Brakes, Wheels, Suspension and Chassis
Do you have the leaky bleeders (eeewww...) on the car now? How are you using your pressure bleeder, since the speed bleeders have a check valve inside? Might be a good idea to get primitive. Reinstall the stock bleed screws, get a foot long piece of hose and a jar, and do it the old-fashioned way. -
No (Low) Rear Brake Pressure
NewZed replied to Twisted46's topic in Brakes, Wheels, Suspension and Chassis
I bleed mine using the stick between the pedal and seat. Crack the bleeder, push the pedal and jam it down with the stick, close the bleed screw, let the pedal up. Works surprisingly well. Put a tube in a jar and you can see what came out. I have speed bleeders on the back also. Still drums. -
No (Low) Rear Brake Pressure
NewZed replied to Twisted46's topic in Brakes, Wheels, Suspension and Chassis
It's a late 260Z right? Here's a 1975 NP valve drawing. What would be odd though is that, if it is gutted and all systems are on the same hydraulic line, if one wheel gets pressure they all should get pressure. You might be working on the wrong problem. Maybe it's mechanical. The beauty of the old school bleeding method is that you actually see the response at each wheel as you bleed it. Fluid squirts out, showing that some pressure is being transferred. -
No (Low) Rear Brake Pressure
NewZed replied to Twisted46's topic in Brakes, Wheels, Suspension and Chassis
Maybe try old school bleeding methods before the pressure bleeder. As Miles suggests there might be air in the MC. An air bubble might not get pushed out of the MC by a pressure bleeder if the MC is "nose up". Be the air bubble...where would you hide? -
No (Low) Rear Brake Pressure
NewZed replied to Twisted46's topic in Brakes, Wheels, Suspension and Chassis
If the rear cylinders were leaking there would be fluid. Did you see any? Sounds more like a bad MC. The front and rear systems are stacked, in series. If one seal fails the pedal will drop that distance until the second one catches. Your new MC might fix it. Here's a drawing, they're all the same. The right seal contains the fluid, the other two create pressure. You can see how you can lose one but keep pressure on the other end. -
Hey datnut, there's only one vague reference to a fire in this Hybridz thread. Not clear what fire you're talking about. Is there a link to some info?
-
Here's the Rule I was remembering. It only matters though f the guy is still in business, or cares about being on Hybridz.
-
-
Some of the new/reman ones come with the clevis. You might try your local auto parts store. I think that I just threw one in the recycle bin a couple months ago. I might have one in a parts box. What part of PNW? Close to Portland? https://www.rockauto.com/en/catalog/nissan,1976,280z,2.8l+l6,1209226,transmission-manual,clutch+master+cylinder,1996 The Tilton does not come with a clevis?
-
The leg of the T should be white with a black stripe by the diagram. The other should be yellow. The WB wire is the one that should control your charge light. Not sure what's happening when you jump it like that, it shouldn't really do anything. It might be that you're running full current through a short in the alternator. The charge light is actually a resistor that controls current flow through that circuit. Kind of sounds like you have two problems - a bad connection to the BAT terminal, and a bad alternator. Parts store alternators have been known to be bad out of the box. I'd get it tested.
-
I think that shows a high resistance in the line from the BAT terminal to the battery. That cable runs to the starter lug, then the positive cable runs up to the battery. Could just be a loose connection at the starter terminal or bad positive connection at the battery. It's a good test though, you have a problem somewhere along the way. Forgot about the black fusible link also. It could be bad or have a bad connection. It's on the way to the battery from the BAT terminal.
-
You can report them to the Better Business Bureau if they are a licensed business. Hybridz used to have some things about Vendors and how they would deal with the bad ones. But the Rules and Guidelines aren't available anymore.
-
I think that Motorsport Auto used to sell their own brand of lowering springs that were blue. Nissan/Datsun springs are black with a colored paint splotch on them. The springs aren't really difficult to change. The 240Z's have enough room to swing the strut out and take the top off, without disconnecting the control arm. Once you get started though you usually find a bunch of other stuff that needs doing.
-
Hey @RETRO-SPEC
-
Here's two thoughts - 1. Check voltage at the coil. Maybe your voltage regulator is going bad and "over-volting" things. I don't know how a tach would react to that but it's a possibility. 2. Spend $25 for a GM HEI module and wire it in quick and dirty. It might actually make things worse, sometimes they cause their own tach problems, but it might tell you something. Always good to have a backup ignition module anyway, the 40+ year old modules die on a regular basis. Two cheap checks, compared to new gauges. Good luck.
-
Does it match RPM? Could be a sign of a failing ignition module. If the flasher makes noise then it must be getting voltage. Current flow heats and cools the mechanism. Always possible that the bulbs are burned out. Also, check the grounds. Can't remember if the tach signal lights have their own ground wire from the socket or if they ground through the socket to the tach body. Who knows, poor ground might also be the problem with the tach needle. The ground circuit is often overlooked. I've also found that the bulbs and sockets can be pretty touchy. They have to be just right and are easily knocked loose. Once you get in there sometimes the problems just grow. I got the fuse cover picture from the 75 FSM. You might have a more 76 like system. 75 had a lot of firsts, and new changes. Here's 76.
-
My mistake, I was thinking clevis pin. You could cut the rod in the middle and insert a tall nut, maybe. Or put a bolt/screw through the back of the clevis and use the tall nut as an extension. Spitballing... Example - https://us.misumi-ec.com/vona2/detail/221005295770/?rid=rid3
-
You should find a shop that knows Z cars and Quaifes. The wrong shop could waste a lot of your time. There are many people out there that are happy to guess, on your time and money. The "clip" problem is pretty well known by people that have worked on the Datsun diffs. A 510 shop would probably know also.
-
That's the basic problem, I think, the groove shapes are different. Nissan changed the location of the clips around the time that they introduced the VLSD diffs. If you get a VLSD diff, like from a 90's Nissan, the clips will come out with the axle. If you have an early open or CLSD diff the clips stay inside. I think that if you get two square grooves combined you could end up with a stuck axle. Better inspect things closely. Your shop is probably use to looking at VLSD's like on the 240SX. There is a lot of confusion on the CV axles. Some places even show the 240Z's used CV axles. There's bad data out there.
-
Looks like they changed over the years. #10? Might be available from Nissan. http://www.carpartsmanual.com/datsun/Z-1969-1978/brake/brake-clutch-pedal https://www.courtesyparts.com/oem-parts/nissan-pin-clevis-46123h850a
-
Most strut/insert manufacturers recommend bump stops. Probably in the instructions of whatever you end up getting.
-
RB25 in a 1977 280Z Heater Functionality
NewZed replied to SelectSpeedShop's topic in Nissan RB Forum
Connecting direct to S might work. There is an electric connection in the switch that opens and closes that first magnet valve. It's described in the chapter. Not clear what would happen if you still have vacuum when you turn the heat to Off. I can't remember what actuates the first magnet valve. Without a vacuum bottle the valves will open and close with engine vacuum, probably, even with a check valve. Cold feet on the on-ramps.