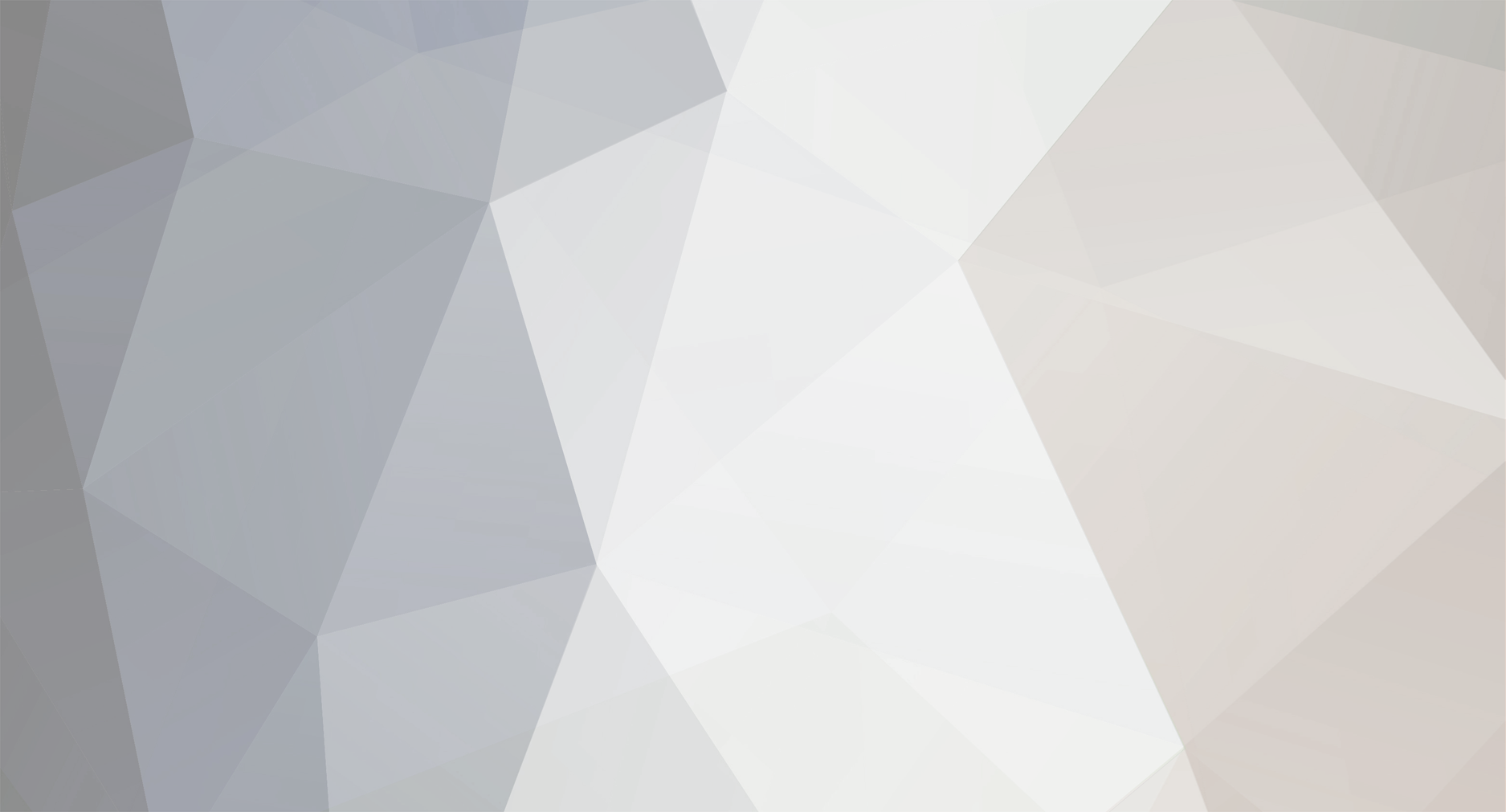
NewZed
Members-
Posts
6681 -
Joined
-
Last visited
-
Days Won
70
Content Type
Profiles
Forums
Blogs
Events
Gallery
Downloads
Store
Everything posted by NewZed
-
'78 280Z Charging Issues
NewZed replied to TheWeekendWagon's topic in Trouble Shooting / General Engine
The tach, the charge lamp, and the check relay all get power through the ignition relay. The ignition relay power comes through a fusible link. -
'78 280Z Charging Issues
NewZed replied to TheWeekendWagon's topic in Trouble Shooting / General Engine
Do you not have a hand held meter? To use for measuring voltage? When I posted the wiring diagrams I thought that you would see the circuits and check those. Didn't know you'd remove the dash to change the bulb first. Anyway, the diagram shows that power to the check relay and the charge lamp comes from a single fuse. You might check that one. 10 amps, 4th down on the left side. Edit - I see that you said the fuses look fine. But you should be using your hand held meter or test light to confirm voltage, on both sides of the fuse. If there's no voltage at the fuse, follow the circuit backward. All the way to the fusible link. The location of the relays is in the Body Electrical chapter. -
1978 280z, GM Hei Module Problem
NewZed replied to TakemuraShuu's topic in S30 Series - 240z, 260z, 280z
The diagram in the first two posts is the correct one. The pickup coil in the distributor "signals" the module to fire the coil. The ECU is not involved. Your second diagram is for the system where the ECU controls the coil. That did not come until 1981 with the 280ZX turbo engines, and the ECCS system. Yours is actually pretty simple. A few checks with a meter should find any problems. -
1978 280z, GM Hei Module Problem
NewZed replied to TakemuraShuu's topic in S30 Series - 240z, 260z, 280z
This isn't really a sign of a bad module. "complete drop in rpms when mashing on the accelerator when the engine's warm" Module problems are associated with high RPM, but "mashing" isn't necessary. It's the high RPM that overload it and cause it to fail. If you just can't get the new HEI module to work, consider disconnecting it and reconnecting the old one. -
1978 280z, GM Hei Module Problem
NewZed replied to TakemuraShuu's topic in S30 Series - 240z, 260z, 280z
Have you checked the B pin for voltage? Checked the red and green wire's resistance, through the distributor's pickup coil? Checked the resistance of the coil's primary circuit? Checked for pinched wires? Did you disconnect the old module? Just unplug it, up by the fuse box. It needs to be disconnected for the new one to work right. You have wires connected but haven't confirmed that things are correct. A picture isn't really going to help. Good luck. -
Somebody put a package together of Stagg and Vogtland a few years ago and that's why those two names are associated. There doesn't seem to be anything special about Stagg except the air of mystery because they're new to the scene. They're just inexpensive shocks. Wouldn't be a surprise if they were made in Asia for cheap, and the name is the selling point. California area code and zero information about the company, on the "official" company web site. Pretty common in today's internet connected world. They're just manufactured and imported from parts unknown. http://staggshocks.com/Stagg Contact.html And they don't warranty "excessively lowered" applications either, but don't define excessive. http://staggshocks.com/Stagg AG/Stagg Warranty.html
-
1978 280z, GM Hei Module Problem
NewZed replied to TakemuraShuu's topic in S30 Series - 240z, 260z, 280z
They're just the holes used to mount the module. Not sure, but one of them has a wider grommet. Just pick a good spot and ground both. But, word is, that if they're not grounded from the start that the module might be damaged. hopefully you won't find that to be the case. One or both definitely need to be grounded though because that's where the coil current flows, through that ground. No ground, no coil current (as opposed to voltage). No current, no spark. -
1978 280z, GM Hei Module Problem
NewZed replied to TakemuraShuu's topic in S30 Series - 240z, 260z, 280z
-
The ball valve might not last long with gasoline flowing through it instead of water. Wire nuts are always bad. Weird that somebody would remove fenders to put louvers in that spot. Looks like a Baja rig, but with potential. Can't tell if your pictures are before you got it or after. Good luck. Edit - not trying to be negative. But you have a curiosity there.
-
Assuming that the slave cylinder diameter is the same as the master diameter, which is common, it would be pounds of force on the pedal times the length of the pedal in feet. ft-lb, not ft/lbs. The hydraulics will transmit the pedal's force to the slave cylinder at a 1:1 ratio if the cylinders are the same diameter. If you want more force at the slave, you would use a smaller master cylinder, trading distance for force at the slave cylinder. Short answer - it's probably the same as it is for the L series engine.
-
Not sure what you mean by "straight line". What you're trying to do is to get the crankshaft parallel with the pinion shaft of the diff. They can be offset but have to be parallel. So when you're done the transmission could be pointing to either side or above or below the diff, but as long they're both parallel you'll be okay. Another way to define it is that both joints must have the same angle. Maybe you know it already but here's a good link. The angles are up, down, and sideways. https://www.drivelinesnw.com/part-trouble-shooting/vibration-analysis/angle-analysis/
-
'78 280Z Charging Issues
NewZed replied to TheWeekendWagon's topic in Trouble Shooting / General Engine
I was going to mention what Sam280Z said about the Charge light. But the diagram shows a parallel circuit with the check relay so that wouldn't be a problem IF the diagram is correct. Current through the check relay solenoid would supply the L circuit and the bulb circuit would not be necessary. Now that you've mentioned all of the other problems, it seems more likely that it could be the cause and the diagram is not correct. Good luck. At least you know that it's power to the L wire that is the problem. -
'78 280Z Charging Issues
NewZed replied to TheWeekendWagon's topic in Trouble Shooting / General Engine
According to one diagram that I have that is the L wire, for Lamp. It supplies power to the alternator windings. That would explain your problem. Now you just have to find out why it doesn't have power. Nissan made things complicated in 1978 with lots of extra relays and gizmos. I think that the best you can do is to follow that wire back. Looks like it gets power through a"check relay" (maybe your e-brake warning light) and also the Charge lamp. The Charge lamp in the meter should light up when the key is on. The colors aren't right in my copy of the 78 FSM but it shows the various connectors. Maybe you just lost a connection. Edit - looks like they only mislabeled the color, WB, right at the plug. It's back to "L" (blue) farther down the circuit. It does indicate a splice to a yellow wire along the way. Nissan used a crimp on to exposed wire to create branches. Likely a stressed point, susceptible to bending and fatigue. -
People say that the welding process itself will often help break a bolt loose. The heat and the current. You can spend a lot of money at a machine shop. Make sure you agree on a maximum price. Sometimes they get obsessed and will take a lot of time to get it out, all at their hourly rate.
-
'78 280Z Charging Issues
NewZed replied to TheWeekendWagon's topic in Trouble Shooting / General Engine
Get a voltmeter and measure voltage at the plug to the back of the alternator. The T plug. They should both show 12 volts with the key on. Also make sure that plug is making good contact with the pins in the alternator. I had a plug that was loose and was not making contact. Had to recrimp it with a pair if pliers. Make sure that the charge wire to the lug on the starter is intact. It's the white wire that starts at the B terminal on the back of the alternator. And check your fusible links. -
The 260Z carbs and manifolds should bolt right up to an L28. People do it all the time, especially when they have problems with EFI. Many L28's don't have the parts or holes in the head for a mechanical fuel pump though, but the 260Z has an electric pump anyway.
-
The rail and FPR don't have anything to do with the pump. Pump noise depends on how it's mounted and how powerful it is. Start your own pump thread and you can get a pretty good conversation going. This thread is Pallnet's vendor thread. Don't want to clutter it up.
-
Use the "Single Fuel Rail Fuel Injected" diagram here. Ignore the others, some aren't quite right. Leave the unused inlets on the FPR blocked. The supply is at one end of your rail and the FPR at the other. Tank-(prefilter maybe)- pump-filter-rail-FPR-tank. https://www.aeromotiveinc.com/in-line-diagrams/
-
That red loctite idea is good for a first try. High strength thread locker. Worst case the nut just comes off and you're left with more grippy threads. Probably pay about $8 for a tube of Loctite. Most of us try to go cheap with the tools at hand. And regret it.
-
I like the red loctite idea. Another option is JB Weld Steel-Stick. If you use either, stick a piece of plastic wrap over the nub, leaving the threads uncovered, so that you don't glue the nut to the head. And clean the threads of any lubricants. MEK or acetone preferred for cleaning. Filing flat is apparently personal preference, along with channel-locks vs vise-grips. Maybe based on hand strength, who knows. But if you squeeze on the threads they will deform and you'll get limited contact area. Then the pliers will probably slip. Clamp on solid steel flats and you'll get less slippage. In the end though, if you do strip threads off you'll end up filing flats. I just jumped ahead to where the neophyte will probably end up. You'll probably crush the threads, round off the end of the stub in to a cone shape, then wear it down in to a tiny useless mound. Unless you plan ahead and are very careful. Good luck.
-
A pair of vise grips might do it. File some flats on to the stub so that you can get a good grip. Position the vise grips in a good spot for grip and leverage and get them as tight as you can. If they start to slip at all when trying to turn the stub, stop. Don't destroy the stub. If you don't have the right type of vise grip take the time to go to the store and buy them. Some time and money now will save you a lot of aggravation. Preparing everything for the twist is key.
-
Where to Buy OBX diff / rear end build compatibility
NewZed replied to carbuilder723's topic in Drivetrain
This guy put a diff together working with a reputable supplier. Might cost more but probably a better product. http://forums.hybridz.org/topic/127169-mfactory-r200-helical-lsd/ -
Who rebuilt the engine? And has the 5 speed been rebuilt? Good luck.